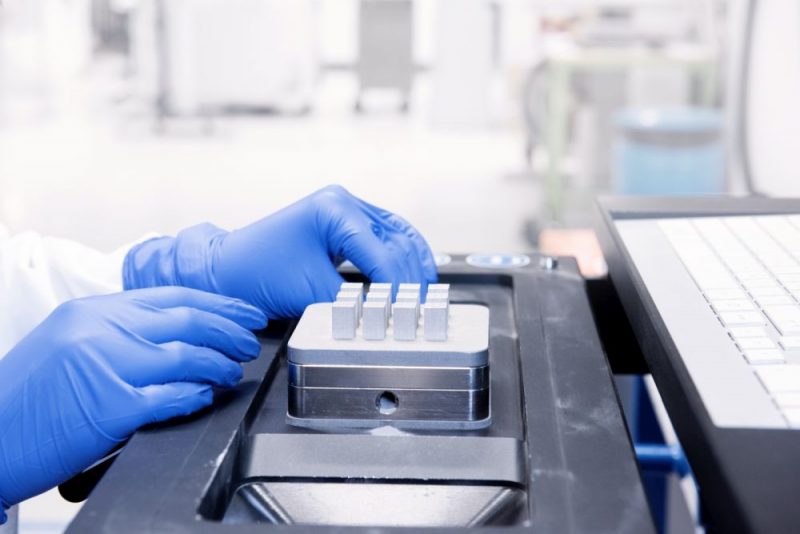
Sandvik Additive Manufacturing per i materiali, Beamit e Zare per prototipazione e stampa, Pres-X per trattamenti termici e post-processing: insieme rappresentano un gruppo all’avanguardia nel mondo della produzione additiva.
Ormai da diversi anni, le tecnologie additive stanno rivoluzionando il modo di pensare e di produrre gli oggetti. Consentono infatti di realizzare geometrie che fino a non molto tempo fa erano considerate impossibili, utilizzano materiali difficili da lavorare con tecnologie tradizionali e sono accessibili anche a realtà medio-piccole grazie ai tanti service nati per soddisfare la nuova domanda. In questo settore in forte fermento si muovono alcune realtà di grandi dimensioni, molte piccole imprese e una serie di attività che stanno mettendo a fattor comune le proprie competenze al fine di offrire una proposta completa e di qualità.
Tecnologie additive, specialisti nella materia prima
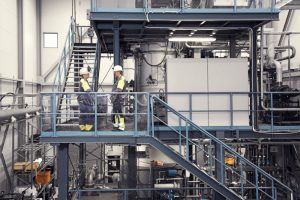
All’interno del gruppo svedese Sandvik AB, la divisione Sandvik Additive Manufacturing è il centro d’eccellenza per l’AM. La vasta esperienza accumulata nel mondo dei materiali ha portato l’azienda a concentrarsi sulla produzione di polveri metalliche, la materia prima per la tecnologia additiva maggiormente diffusa: quella a letto di polvere (powder bed fusion). Sandvik Additive Manufacturing, sotto il marchio di Sandvik Osprey, vanta infatti più di 45 anni di esperienza nella produzione di polvere metallica tramite gas atomizzazione su due stabilimenti produttivi, uno a Neath (Regno Unito) e uno a Sandviken (Svezia), aventi operative 11 torri di atomizzazione con la possibilità e l’esperienza nella produzione di più di 2 mila diverse leghe. Più di recente, a novembre 2019 è stato inaugurato un innovativo impianto di produzione di tipo VIGA (Vacuum melting Inert Gas Atomization) per polveri in lega di titanio, il cui processo produttivo ha ricevuto la certificazione di qualità in ambito aeronautico AS9100D. A settembre 2019, ha poi ottenuto anche la certificazione medicale ISO 13485:2016. I settori aeronautico e medicale sono infatti quelli in cui le leghe di titanio e la tecnologia additiva sono sempre più diffusi. Le leghe attualmente in produzione sono il Ti6Al4V grado 5 e il Ti6Al4V grado 23, con la volontà di svilupparne di nuove. Le proprietà delle polveri metalliche utilizzate influenzano direttamente l’affidabilità delle prestazioni del processo di AM, nonché la qualità e le prestazioni del prodotto finito.
Per questo Sandvik Additive Manufacturing ha ottenuto la certificazione ISO 13485:2016 per il settore medicale. «Nella produzione additiva metalli è essenziale utilizzare polveri di alta qualità con una qualità costante, adattate ai diversi processi di produzione», spiega Keith Murray, VP ed Head of Global Sales di Sandvik Additive Manufacturing. «La nostra esperienza pluridecennale nell’atomizzazione di polveri metalliche fini ci consente di fornire titanio della massima purezza alle industrie mediche e aerospaziali».
Additive Manufacturing, la nascita di un Gruppo coeso
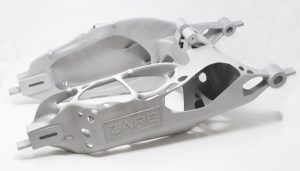
In Italia esistono numerose realtà di medie dimensioni che stanno ottenendo significativi risultati nella produzione additiva in metallo di componenti complessi. È il caso di Beamit, azienda nostrana con sede a Fornovo (PR), che a luglio 2019 ha visto l’ingresso con una quota significativa proprio da parte del gruppo Sandvik. È l’inizio di un trend che prosegue ancora oggi. Già, perché Beamit a sua volta a inizio 2020 s’integra con Pres-X, start-up innovativa specializzata in trattamenti termici e finiture superficiali, e ad agosto 2020 acquisisce Zare, dando così vita al più grande partner globale nella catena del valore del settore.
«Il settore dell’AM si sta sviluppando rapidamente e vi è la necessità di trovare partner con le competenze e le risorse necessarie per aiutare i clienti a sviluppare e lanciare i propri programmi AM», conferma Kristian Egeberg, presidente di Sandvik Additive Manufacturing. «Insieme, Sandvik e il gruppo Beamit sono in grado di fornire ai clienti l’opportunità di accedere a competenze legate all’intera filiera».
Il gruppo Beamit diventa così un’organizzazione con oltre 100 dipendenti, attività distribuite su 5 impianti e 4 uffici commerciali in Francia, Germania, Regno Unito e Giappone. «Ho avuto l’opportunità di incontrare persone speciali e imprenditori coraggiosi, come Sauro Zanichelli e Andrea Pasquali», ha dichiarato Mauro Antolotti, presidente di Beamit. «Questa organizzazione estesa è stata creata per servire e supportare i nostri clienti comuni con una gamma di servizi a 360 gradi, nonché una maggior capacità di investimento e solidità finanziaria, al fine di diventare ancora più solidi per affrontare ulteriori sfide del mercato, garantendo al contempo l’affidabilità totale per i clienti attuali e quelli futuri in questo viaggio che intraprendiamo insieme».
Qual è oggi l’attività del gruppo Beamit? Trattandosi di un ecosistema-hub nel mondo delle competenze, dei processi e delle tecnologie per l’AM, l’azienda è oggi in grado di offrire una gamma completa di materiali, soluzioni e certificazioni per l’aeronautica, l’aerospace e la difesa, l’energia, il motorsport, l’oil&gas e i trasporti.
Produzione additiva, un’offerta completa
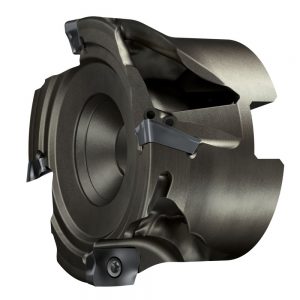
Il gruppo Beamit, il cui focus principale è la produzione di componenti metallici mediante tecnologie a letto di polvere (Powder Bed Fusion) in cui vengono utilizzate sorgenti energetiche quali Laser o Electron Beam per fondere selettivamente strati di polvere metallica, ha a disposizione anche diverse tecnologie che permettono la realizzazione di componenti in materiali polimerici e ceramici.
Un reparto SLS (Selective Laser Sintering) che utilizza laser ad alta potenza per fondere, strato su strato, il materiale in forma di polvere atomizzata in modo da creare prototipi e parti funzionali.
Un reparto FDM (Fused Deposition Modeling) che, strato dopo strato, permette di estrudere da un ugello riscaldato il materiale plastico in bobina, garantendo così innumerevoli possibilità di modellazione.
Un reparto HP Multi Jet Fusion, che sfrutta una tecnologia che ha portato nel settore dell’AM un deciso aumento della produttività: si presenta come un impianto produttivo ideale per la realizzazione di piccole produzioni in serie.
Un reparto PolyJet, tecnologia che permette di costruire modelli con superfici lisce e dettagli accurati in diverse materie plastiche e in gomme di durezza differente. Le stampanti che sfruttano la tecnologia PolyJet si basano su un procedimento simile alla stampa a getto d’inchiostro; in questo caso vengono depositati su un vassoio dei fotopolimeri liquidi che poi si solidificano dando forma all’oggetto.
Un impianto per la produzione di componenti ceramici tramite la tecnologia NPJ (Nano Particle Jetting) sviluppata dalla XJET e che offre velocità di stampa, accuratezza dimensionale ed elevata precisione nei dettagli grazie all’utilizzo di polvere ceramica nanometrica.
Soluzioni per l’intera filiera additiva
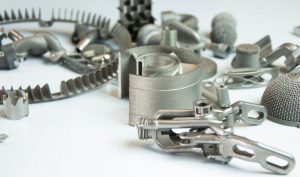
La crescita dell’AM all’inizio ha coinvolto il solo processo di produzione additiva, ma ben presto si è reso evidente come le attività a monte (come la progettazione) e a valle rivestano la stessa importanza nel giungere al risultato finale.
I trattamenti termici, per esempio, sono di fondamentale importanza per i componenti metallici prodotti con queste tecnologie. Permettono infatti di eliminare le tensioni residue nel materiale; tensioni dovute alla natura stessa della tecnologia additiva e che consentono di evitare deformazioni dei particolari una volta rimossi dalla piattaforma. Inoltre, occorre sottolineare che a seconda del trattamento termico eseguito si possono ottenere diverse proprietà meccaniche, cambiando drasticamente il campo di utilizzo di un determinato componente.
Beamit utilizza forni in aria con tempra in acqua per le leghe di alluminio, mentre per le leghe di titanio, base nichel e acciai inossidabili forni sottovuoto con tempra in argon. Per ottenere risultati ottimali e costanti è di fondamentale importanza controllare ogni singolo parametro del processo additivo: Beamit e Zare operano con i più alti standard qualitativi, entrambe le aziende del Gruppo sono certificate ISO 9001 ed EN 9100:2016, fondamentale per lavorare nell’industria aeronautica. Inoltre, lo stabilimento di Zare è certificato IATF 16489, rispondendo così agli standard qualitativi dell’industria automobilistica, mentre i processi speciali di Beamit, il reparto trattamenti termici e il laboratorio metallografico sono accreditati NADCAP (National Aerospace & Defense Contractors Accreditation Program), a garanzia dell’applicazione rigorosa di norme di processo univoche per la soddisfazione dei requisiti tecnici più stringenti nell’industria aerospaziale.
Grande attenzione al post-processing
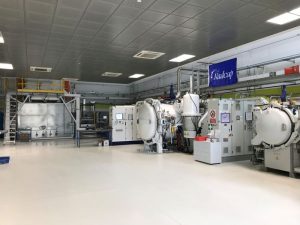
Pres-X vanta la migliore tecnologia per il post-processing dei componenti realizzati tramite manifattura additiva. Dispone infatti di un impianto per pressatura isostatica a caldo (HIP, Hot Isostatic Pressure) con possibilità di tempra in argon veloce. La pressatura isostatica a caldo, o trattamento termico ad alta pressione, consente ai materiali utilizzati di avere maggiore resistenza, e di conseguenza durevolezza, rispetto ai materiali tradizionali.
Il trattamento termico ad alta pressione (HPHT) ottimizza le proprietà meccaniche con l’eliminazione dei difetti dovuti alla fase di stampa, come le caratteristiche porosità, e accorpa due fasi di ciclo molto energivore in una singola fase, con conseguente riduzione del 50% delle tempistiche e del 40% dei consumi.
Grande attenzione anche alla qualità delle finiture superficiali: gli oggetti stampati in 3D devono avere un’estetica e una funzionalità eccellenti, mentre spesso il risultato della stampa presenta finiture ruvide e rugose. Per questo Pres-X sfrutta un processo brevettato che impiega la nuova tecnologia DryLite, un brevetto industriale al momento in sviluppo e di cui proprio Pres-X è il primo utente in Italia. L’azienda propone inoltre servizi di pulizia di componenti complessi sfruttando l’intelligenza artificiale con metodi a basso consumo energetico ed eliminando completamente residui di polvere non fusa. Pulendo la polvere residua, riducendo la rugosità ed eliminando i difetti della stampa durante il trattamento termico si amplia significativamente il campo di utilizzo della stampa 3D, abbattendo costi e tempi di produzione, migliorandone la qualità e aumentandone le prestazioni.
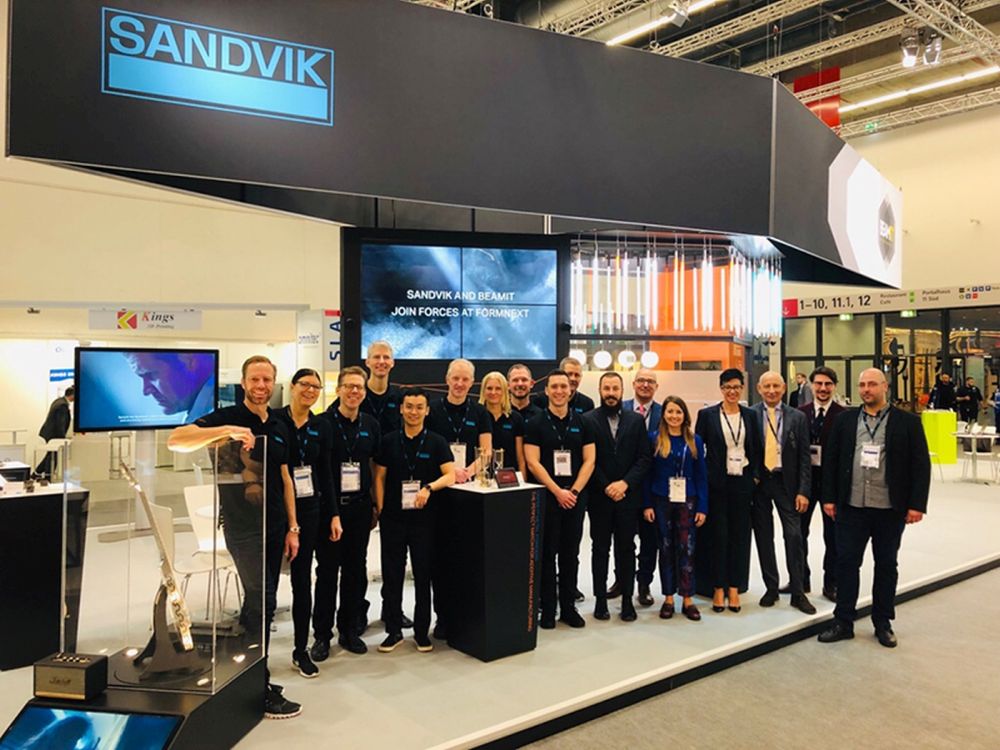
Condividi l'articolo
Scegli su quale Social Network vuoi condividere