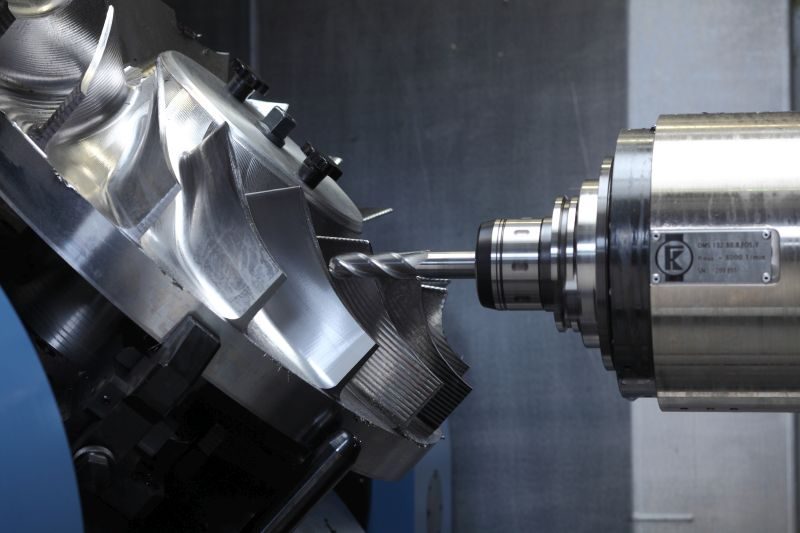
L’esperienza di Mandelli Sistemi nella lavorazione di leghe tenaci, un esempio di come anche in mercati particolari una buona programmazione e gestione delle risorse aiutino ad andare ben al di là della semplice produzione
Ancor più che in altri mercati, l’aerospace costringe le aziende a scelte precise in ogni aspetto della loro programmazione. Per approfondire alcuni dettagli abbiamo incontrato Marco Colombi, responsabile commerciale di Mandelli Sistemi.
La situazione attuale
Mandelli Sistemi tradizionalmente produce centri di lavoro per materiali tenaci, centri di lavoro caratterizzati da una grande rigidezza e capacità di asportazione e dal mantenere la precisione nel tempo, caratteristiche che ben si sposano con le attuali tendenze in campo aeronautico. Già nel DNA Mandelli c’è la lavorazione di leghe tenaci, inoltre tutte le ricerche di mercato danno per almeno vent’anni l’aerospace in crescita, sia per il rimpiazzo della flotta in servizio sia per l’incremento delle flotte e il numero degli aerei: da qui al 2035 la Boeing prevede 38 mila nuovi aerei, l’Airbus 32.500, con stime addirittura in crescita.
Nel frattempo sono cambiati i materiali: un aereo progettato negli anni Ottanta-Novanta aveva fino al 70% di alluminio rispetto ai moderni Airbus 350 e Boeing 787 che arrivano al 50% di composito e il 17% di titanio, quest’ultimo in particolare per le applicazioni strutturali, e le superleghe a base nichel o cobalto per le applicazioni motoristiche.
Oltretutto questo sviluppo nei materiali ha un impatto anche nei costi e sulla riduzione delle emissioni di CO2, quindi va valutato anche in ottica “green”: la direzione è quella di utilizzare materiali sempre più sofisticati, con rapporto tra resistenza e massa sempre più efficace. Su questa base, Mandelli ha focalizzato le proprie risorse progettuali per soluzioni che rendessero la linea Spark (che lavora con efficacia anche alluminio e materiali tradizionali come acciai e ghise) ancor più performante anche nella lavorazione di titanio e superleghe.
Gli sviluppi recenti
Le innovazioni realizzate dalla Mandelli negli ultimi anni si possono sostanzialmente dividere in due ambiti: di natura strutturale e dedicate alla motoristica.
«Il primo – spiega Colombi – consiste soprattutto nelle lavorazioni di componenti per carrelli d’atterraggio (main cylinder, brake rod, torsion link per citarne alcuni), componenti di comando per le ali come flap e slat tracks ed elementi di connessione tra motori e ali come pylons ed engine mounts. Qui domina il titanio e di solito i grezzi sono dei forgiati con sovrametalli molto importanti: la cosa più efficace è aumentare il volume di truciolo che la macchina è in grado di generare su questi materiali, obiettivo per ottenere il quale abbiamo lavorato in tre direzioni».
«Una è migliorare ulteriormente la rigidezza della macchina – prosegue Colombi – e per questo abbiamo sviluppato nuovi mandrini con attacco HSK125 che raggiungono i 1200 Nm di coppia in continuo. Il secondo aspetto, altrettanto importante, è stato trovare soluzioni per ridurre le vibrazioni indotte dalle lavorazioni. Sia su assi rotanti che sugli assi lineari adottiamo soluzioni basate su sensori che, in presenza di vibrazioni, introducono una azione dissipatoria che tende a smorzarle. Dalle prove che abbiamo realizzato (in una tipica sgrossatura con fresa a riccio di diametro 80 mm, con e senza questi dispositivi), la differenza è una riduzione del 75% di vibrazioni rilevate sul naso mandrino: quindi se il pezzo è sufficientemente solido si può “spingere” di più, altrimenti la riduzione delle vibrazioni ha effetto positivo sulla vita utensile e, in ultima istanza, anche dei componenti stessi della macchina che risultano meno sollecitati. Il terzo aspetto è quello di pressione e portata del refrigerante: spesso per queste applicazioni di tipo strutturale si lavora all’interno di tasche (le geometrie del settore aeronautico prevedono tasche con nervature anche piuttosto profonde) e per favorire l’evacuazione del truciolo si arriva a un apporto di refrigerante di 150 l/min attraverso l’utensile e pressioni fino a 100 bar».
Aumenta l’efficienza
Tutti i pezzi aeronautici hanno geometrie complesse e richiedono lavorazioni a 5 assi: «Tipicamente si lavora a 3 assi in sgrossatura, poi occorre eseguire una semifinitura per portarsi con un sovrametallo costante e si termina con la finitura vera e propria», spiega Colombi. «Quando devo lavorare una superficie inclinata, di solito si lavora con gli assi bloccati e la si terrazza, si fa una passata in semifinitura che raccoglie le terrazze e porta un sovrametallo di cinque decimi; infine con la finitura si ottiene la quota desiderata. Chiaramente se c’è la possibilità di eseguire la sgrossatura a 5 assi per portarsi in una condizione di sovrametallo costante senza ulteriori interventi di semifinitura si risparmia un’operazione e, quindi, tempo. Nel nostro caso si ottengono sgrossatura e semifinitura in una sola fase, senza generare terrazze. Alla Bi-MU esporremo una testa con coppia di 12 mila Nm sull’asse rotante, che permette di lavorare in sgrossatura a 5 assi in continuo anche con utensili lunghi, facendo comunque asportazioni pesanti e questo di fatto elimina una fase di lavorazione e permette di garantire maggiore efficienza e di sfruttare al massimo le caratteristiche del mandrino».
Aumentando le prestazioni degli assi e del mandrino si aumenta il costo dell’investimento iniziale, ma alla fine il costo orario della macchina si ripaga grazie alla maggiore efficienza: questo ha un impatto anche organizzativo nelle aziende, spesso strutturate tradizionalmente con macchine heavy duty – a volte un po’ vecchie – per le sgrossature e mezzi produttivi moderni per le finiture, il che comporta reparti dedicati e semilavorati in giro per l’azienda, mentre la possibilità di fare sgrossatura e finitura su uno stesso mezzo produttivo permette di ottimizzare il flusso del materiale diminuendo le quantità di grezzi immobilizzati o semilavorati in azienda e, in definitiva, una semplificazione della gestione e una maggior profittabilità per il cliente finale nell’ottica di organizzazioni orientate al Lean Manufacturing.
«Spesso con l’acquisto di nuovi macchinari e una collaborazione fra chi è proprietario della tecnologia e chi conosce bene caratteristiche e prestazioni della macchina si riescono a ottenere grossi passi in avanti», racconta Colombi. «Ad esempio, in occasione di un grosso progetto in Polonia abbiamo affrontato dei particolari di carrelli di atterraggio di un aereo Boeing che prevedevano 30 fasi di lavorazione prima e dopo il trattamento termico: grazie anche al contributo di Mandelli, abbiamo ridotto le fasi di lavorazione a 12».
Personalizzazioni ad hoc
Ai costruttori di aerei, che spesso si limitano ad assemblare sottogruppi forniti da società terze, si affiancano i Tier 1 (costruttori e assemblatori di particolari importanti come i motori), Tier 2 (costruttori e assemblatori di sottoinsiemi meno importanti) e Tier 3 (in genere terzisti che eseguono semplicemente lavorazioni meccaniche): per questo, a seconda dell’interlocutore al quale si rivolge, Mandelli Sistemi deve fornire una soluzione specifica. In effetti la “macchina a catalogo” per un costruttore come Mandelli, che tende più a cucire la soluzione addosso al cliente, non esiste.
«Capitano di frequente applicazioni speciali e personalizzazioni abbastanza impegnative», aggiunge Colombi. «Di recente ne sono state vendute un paio nel nord Europa, un’applicazione dedicata all’aero-engine e un centro di lavoro molto speciale a 7 assi, comprese 2 tavole con divisore e un terzo pallet standard per l’esecuzione di fasi preparatorie, quindi una macchina estremamente dedicata».
Gestione della produzione
Abbiamo citato la Lean Manufacturing, sinonimo di efficienza produttiva: oltre che nelle principali aziende aeronautiche, questo metodo organizzativo è stato adottato anche da Mandelli. Nata nel settore automotive, dove le operazioni in serie (montaggi di gruppi, teste e tavole in cicli standard) erano la regola, ormai da decenni la metodologia Lean è stata estesa nella sua evoluzione più allargata a tutti processi aziendali e ad altri settori. In Mandelli questo ha avuto ricadute molto importanti, «soprattutto la riduzione dei costi di garanzia che, nel giro di un paio d’anni, sono scesi del 40%», racconta Colombi. «Lavoriamo secondo metodologie Lean su più livelli dell’officina, ogni mese affrontiamo un problema specifico con un full immersion di tutti gli enti coinvolti per risolvere la problematica nel migliore dei modi (Kaizen event). Tutti i processi aziendali sono mappati e valutati con KPI (Key Performance Index) e implementati con metodologie 5S. Per chi produce impianti speciali la filosofia Lean è molto importante: se il tempo di consegna di una macchina standard si conosce sulla base dell’esperienza, per quelle speciali è più difficile garantire tempi di produzione che nascondono molte incognite. Da noi di solito le consegne sono entro i 12 mesi, perché viene fatto un buon lavoro in fase di prevendita, cercando di prevedere tutte le complessità prima della trattativa finale in modo da avere dei termini di consegna ragionevoli e rispettati. Le riunioni e le continue verifiche che impone la Lean sull’evoluzione dei progetti permettono di identificare le criticità e di intervenire rapidamente: anche nella gestione dei fornitori, un controllo puntuale dello stato di avanzamento delle attività sia interne che esterne permette di raggiungere risultati lusinghieri».
Condividi l'articolo
Scegli su quale Social Network vuoi condividere