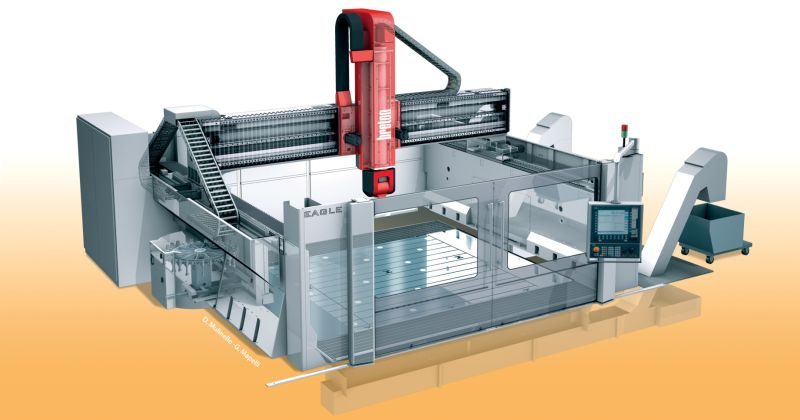
Ad alta velocità, sviluppato per rispondere alle esigenze delle officine che affrontano materiali quali resine, compositi, alluminio e carbonio, il tutto garantendo precisione dimensionale
Nella propria storia di costruttore di macchine utensili, Breton si è sempre distinta per la cura e la qualità nella progettazione e produzione di soluzioni per l’asportazione di truciolo metallico. L’alta precisione, unita a potenze e coppie adeguate per lavorare i nuovi materiali, è stata uno dei cavalli di battaglia dell’azienda di Castello di Godego (TV) per soddisfare le necessità di settori quali l’aerospace, l’automotive e quello degli stampi.
Per ottenere i migliori risultati ha progettato modelli come i centri di lavoro Matrix, usati anche per gestire materiali più leggeri (alluminio, resine e compositi), dove sono comunque richieste precisioni piuttosto spinte e performance di asportazione di buon livello.
Matrix è però un modello che può risultare in alcuni casi sovradimensionato in termini di potenze e precisioni rispetto alle reali necessità di questi settori e, come sappiamo, gli utilizzatori tendono a preferire soluzioni perfettamente aderenti alle proprie necessità.
Il mercato molto spesso offre soluzioni meno performanti e con precisioni volumetriche inadeguate. Eagle è la soluzione Breton per queste aspettative.
Un nuovo settore applicativo
Breton ha deciso di realizzare un prodotto che non fosse in diretta concorrenza con altri costruttori, né ovviamente con alcune delle macchine che già stava realizzando, bensì inserendosi in una nicchia che necessita di buona precisione senza richiedere grandi investimenti.
Non tutti i clienti possono infatti permettersi (o ne hanno la necessità) una macchina che presenti potenze o precisioni estremamente elevate: per questo si è resa sempre più evidente la necessità di offrire un prodotto che andasse incontro a questa esigenza, tipica di chi si occupa della costruzione di stampi su alluminio o di modelleria su resina, carbonio o compositi, il tutto con una precisione non spinta ma comunque superiore a quella ottenibile con macchine di fascia bassa.
Eagle è quindi un centro di lavoro ad alta velocità a 5 assi per la fresatura, la foratura e la rifilatura di componenti di medie e grandi dimensioni realizzati in composito, strutture sandwich, leghe leggere, resine e materiali plastici, il tutto con una buona precisione dimensionale.
Si tratta di una macchina concettualmente più semplice ed economica di una Matrix, ma nello stesso tempo capace di garantire una precisione superiore a quanto disponibile nel settore della lavorazione dei materiali leggeri.
Eagle nasce sulla base della filosofia produttiva che da sempre contraddistingue le macchine Breton: mandrino verticale, viti a ricircolo di sfere di alta qualità, motorizzazione degli assi con recupero dei giochi per assicurare le precisioni volute, strutture termosimmetriche, testa a forcella simmetrica, elettromandrini raffreddati ad alte prestazioni.
Dal punto di vista economico, Eagle richiede un investimento decisamente inferiore rispetto all’acquisto di una Matrix (circa il 30% in meno, variabile a seconda della configurazione). Questo valore è considerevole su una singola macchina, ma spesso gli utilizzatori necessitano di più centri di lavoro dedicati a queste operazioni: dunque la convenienza economica diventa ancora più evidente.
Costruzione modulare
Eagle porta con sé la logica costruttiva degli altri modelli Breton: si tratta infatti di una macchina gantry su spalle alte, con asse verticale bilanciato e che usa teste a struttura simmetrica in modo che le dilatazioni termiche siano sempre regolari. Non tutte le officine sono dotate di impianti di climatizzazione, e il design termosimmetrico consente di ridurre le deformazioni strutturali e di renderle facilmente correggibili via software. Naturalmente i punti nei quali viene generato il calore (come la testa, l’asse A e l’elettromandrino) sono raffreddati attraverso l’impiego di un apposito chiller, al fine di ridurre il passaggio del calore ad altri punti della struttura.
Come buona parte delle macchine prodotte da Breton, anche Eagle presenta un’elevata modularità di progetto.
È realizzata interamente in acciaio elettrosaldato ed è dimensionata tramite analisi agli elementi finiti per ridurre le vibrazioni e limitare le torsioni; questa scelta consente di venire incontro alla richiesta di modularità dimensionale imposta dagli utilizzatori della macchina, permettendo a Breton di personalizzare facilmente il prodotto standard per soddisfare le richieste del mercato.
La macchina è azionata tramite motori brushless; la trave per lo spostamento del gantry è di tipo a cremagliera con due motori e relativi pignoni con recupero dei giochi che, grazie alla modularità della soluzione a cremagliera, assicura corse da 2 m in su. In Y, a seconda del modello scelto, si parte da 2,5 m di corsa per salire fino a 5 m. La corsa dell’asse Z, infine, è pari a 1 m per il modello più compatto e arriva a 2,5 m per quello più grande.
La struttura snella consente inoltre di raggiungere velocità e accelerazioni significative: 70 m/min in X e Y, 50 m/min in Z (tutti gli assi lineari sono dotati di encoder) con accelerazioni fino a 4 m/s2, 12 giri/min sull’asse A e 19 sull’asse C.
Gli elettromandrini sono in parte ereditati dalla Matrix, mentre altri sono sviluppati appositamente per rispondere alle necessità specifiche degli utenti di questa tipologia di macchina. Il modello entry level, di costruzione Breton, offre una coppia di 52 Nm, 16.000 giri/min, 25 kW di potenza ed è lubrificato a grasso: si tratta di una scelta dettata proprio dal tipico ambito applicativo, ovvero l’aerospace, dove è tassativamente vietata la perdita di lubrificante su particolari in composito o carbonio.
In alternativa, sono disponibili altri mandrini sviluppati in codesign con i partner di Breton che offrono fino a 40 kW e la lubrificazione aria/olio.
La testa di lavorazione è stata sviluppata affinché garantisse le precisioni e le prestazioni richieste da questa tipologia di settori applicativi: una soluzione compatta ad azionamento meccanico per permettere di ottenere le prestazioni volute senza impiegare i direct drive – più costosi – e con pivot ridotti in modo da poter penetrare meglio all’interno dei pezzi e poter effettuare tutte le operazioni richieste. È un blocco in fusione di ghisa, una soluzione efficiente per lo smorzamento delle vibrazioni direttamente dove queste si generano, è dotata di freni di stazionamento per lavorare in 3+2 ad assi bloccati e assicurare la massima rigidezza anche con asportazioni impegnative.
La macchina ha ottenuto un riscontro positivo dalle modellerie che realizzano stampi rotazionali, che tipicamente eseguono forti asportazioni su alluminio. Medesimo discorso per le modellerie che realizzano particolari in scala in Ureol, prodotti in resina e altri componenti per la prototipazione.
Potenza e controllo
Un dettaglio legato alla lavorazione dei materiali compositi è la presenza, talvolta, di inserti filettati da forare o piccole lamine in titanio all’interno della struttura: altre soluzioni sul mercato non sono in grado di affrontare queste lavorazioni che, quindi, vengono effettuate manualmente da un operatore, con i problemi legati alla precisione e alla produttività che ciò comporta. Al contrario, Eagle permette di affrontare anche quei pezzi che includono composito, alluminio e inserti vari, completando l’operazione direttamente in macchina.
Nel settore dell’aerospace civile, Eagle si rivela ideale per tutto il macchinato in alluminio strutturale, le strutture di arredamento, i pannelli con struttura a nido d’ape, le fibre aramidiche, l’alluminio e i compositi che vanno forati e svasati.
Ovviamente Eagle è in grado di lavorare anche i materiali più tenaci, tenendo conto del fatto che le sue prestazioni saranno inferiori rispetto a quelle ottenibili ad esempio con una Matrix. La scelta sarà dettata quindi sulla base della predominanza delle lavorazioni da effettuare e dei materiali da affrontare.
Gli accessori
Oltre agli optional più tradizionali, come telecamere di controllo dell’area di lavoro e magazzini utensili di diverse capacità, Breton ha pensato a una serie di accessori dedicati agli ambiti applicativi specifici ai quali Eagle è destinata.
Per la lavorazione dei compositi, è stata ideata una testina di taglio a ultrasuoni che può essere gestita come un comune utensile (infatti viene alloggiata nel magazzino) che evita di strappare o scheggiare il pezzo.
Sempre per i compositi e i particolari in carbonio è stata creata una testina di controllo svasatura gestita in automatico attraverso semplici maschere nel controllo numerico, che consente di effettuare la verifica della reale posizione del foro sul pezzo prima di effettuare la svasatura: questa procedura si rivela indispensabile ad esempio con i portelloni in carbonio degli aerei perché la geometria dello stampato in carbonio difficilmente combacia esattamente con il modello Cad. Il sistema effettua quindi un controllo per stabilire la reale posizione dei fori sul pezzo (tramite tastatore fisico o laser) in tre punti per stabilirne le esatte coordinate prima di fare la svasatura. Rispetto a un ciclo di tastatura si riducono notevolmente i tempi e, quindi, i costi.
I controlli numerici installabili sulla Eagle sono i modelli Siemens 840D sl e Heidenhain 640 iTNC, entrambi in versione full optional per quanto riguarda la dotazione software. Su richiesta dei clienti, inoltre, è possibile sviluppare applicazioni, cicli e interfacce specifiche che “girano” sul controllo numerico per migliorare l’utilizzo della macchina.
È previsto infine un accessorio con un 6° asse orizzontale di posizionamento, per effettuare quelle lavorazioni di rivoluzione che richiedono un posizionamento particolare dei pezzi e un’accessibilità totale in ogni condizioni.
Sicura e produttiva
Potendo lavorare sia a secco che con lubrorefrigerante, sarà l’utilizzatore a scegliere sulla base dell’impiego che ne farà: Breton ha previsto l’impiego di nastri evacuatori, sistemi di aspirazione o entrambi. In presenza di materiali accoppiati, dove è necessario effettuare fresature sul carbonio e successivamente filettature sugli inserti in alluminio, si potranno gestire le polveri di carbonio con il sistema di aspirazione e i trucioli in alluminio con i nastri evacuatori.
L’impegno di Breton nel soddisfare la normativa Atex è massimo: quando si parla di sicurezza, in particolare con impianti industriali, nessuno vuole incorrere in problemi o “sorprese”.
La macchina è perciò completamente chiusa con soffietti a cielo per evitare la dispersione di polveri all’interno degli ambienti di lavoro e presenta sistemi di aspirazione a bordo tavola e sul naso mandrino.
In fase di lavorazione di grafite, la cui polvere è estremamente aggressiva sia sulle parti meccaniche, sia su quelle elettriche, Breton offre cabine IP65 per i quadri elettrici o, in alternativa, posizionati a opportuna distanza dal punto in cui le polveri vengono generate.
Condividi l'articolo
Scegli su quale Social Network vuoi condividere