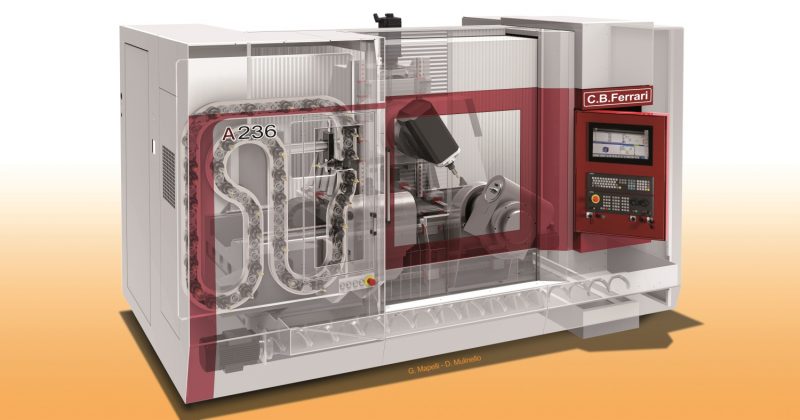
Con il nuovo centro di lavoro A236 di C.B. Ferrari si fa un deciso passo verso le soluzioni ad alta produttività, senza però dimenticare la flessibilità operativa tipica del multitasking e la precisione data dalla struttura termosimmetrica. La macchina prende ciò che di buono è stato fatto con altri modelli, ma con un approccio più votato alla produttività.
di Andrea Pagani
I moderni centri di lavoro multitasking, in grado di affrontare indifferentemente operazioni di fresatura e tornitura, assicurano diversi vantaggi pratici per l’utilizzatore. Innanzitutto evitano di dover utilizzare due macchine differenti, riducendo in tal modo costi di acquisto e operativi e il relativo ingombro in officina. Migliorano inoltre la precisione (lo spostamento di un pezzo da una macchina all’altra introduce un errore che, per quanto ridotto, va considerato) e le tempistiche di lavorazione. Tutte queste considerazioni sono alla base dello sviluppo della nuova A236 della C.B. Ferrari di Mornago (VA), un centro di lavoro che prende ciò che di buono è stato fatto sulle macchine del costruttore di Mornago (VA), ma che dà anche un taglio con il passato sfruttando un approccio più votato alla produttività.
Completamente riprogettato
Per come è stato pensato, A236 è un centro di lavoro multifunzione che assicura sia una elevata precisione e flessibilità, sia una notevole produttività. Nato per lavorare pale di turbine di dimensioni medio-piccole, può realizzare anche giranti (impeller), rotori (blisk), particolari per il settore medicale, dell’orologeria, camme e corpi utensili speciali. In altre parole, dà il meglio di sé in presenza di particolari precisi e complessi. La struttura robusta consente alla A236 di affrontare indifferentemente acciaio, titanio e superleghe (tutti materiali tipicamente impiegati nelle applicazioni citate). Il movimento dell’asse Y, che si occupa dell’avanzamento del mandrino, non è costituito da un braccio che scorre sul montante ma è il montante stesso a muoversi. Il vantaggio di questa scelta è che non ci sarà una variazione nello sbraccio e quindi nella caduta del mandrino: è un valore noto e fisso, che viene compensato già in fase di costruzione della macchina. Sul basamento scorre longitudinalmente il carrello portamontante (asse X); sul carrello portamontante si muove come detto il montante (asse Y) che, grazie alla struttura simmetrica, ospita il supporto della testa e ne consente il movimento verticale (asse Z). Gli assi X, Y e Z, che scorrono su due guide lineari a ricircolo di rulli ad altissima precisione, vengono mossi da motori tradizionali: il campo di lavoro compatto, unito a una maggiore semplificazione e affidabilità, rende questa soluzione preferibile rispetto ai motori lineari. Per quanto riguarda gli assi rotativi, invece, vengono utilizzati motori torque: l’assenza di motori tradizionali e delle relative catene cinematiche, insieme all’impiego di encoder assoluti, assicura la massima precisione e dinamicità.
Soluzioni per la produttività
Per essere definita produttiva una macchina non deve essere semplicemente veloce in ciò che esegue; deve anche assicurare la massima affidabilità di processo e impiantistica. Per l’affidabilità di processo i progettisti di C.B. Ferrari hanno pensato a tanti piccoli (ma importanti) dettagli. Come la gestione dei trucioli, che vede l’impiego di scivoli in acciaio inox e la totale “pulizia” da tubi, gradini o altri elementi che possono intralciare il corretto flusso dei trucioli nel convogliatore. Per l’affidabilità occorre scegliere la componentistica più adatta e posizionarla opportunamente. Come il magazzino utensili, collocato al di fuori dal campo di lavoro e quindi insensibile a trucioli, liquidi e così via. Lo stesso vale per gli strumenti di misura e taratura degli utensili, posti in un punto che non risente dello stillicidio tipico del truciolo prodotto durante le lavorazioni meccaniche. La macchina è pensata per lavorare sia da barra (il caricatore è in grado di gestire barre tonde, quadrate, rettangolari ed esagonali con diametro da 8 a 76 mm e lunghezza fino a 1500 mm), sia con sistema di cambio pallet automatico rispettivamente sui lati sinistro e destro. Ciò significa che la parte frontale risulterà sempre libera e accessibile, dando così la possibilità a un operatore di controllare il ciclo di lavoro e, all’occorrenza, di provvedere al caricamento di un pezzo grezzo o di uno spezzone di barra in manuale.
Il cuore della macchina
Le macchine multitasking devono essere in grado di eseguire operazioni di fresatura e tornitura, ovviamente con una particolare predisposizione per l’una o per l’altra. A236 è un centro di lavoro, ma include due divisori che ne estendono le capacità di asportazione rendendolo al tempo stesso produttivo e flessibile. Innanzitutto, in base alla configurazione scelta, A236 può gestire 6 o 7 assi in simultanea: utile per lavorare anche le forme più complesse per affrontare ogni tipo di geometria. Dei due divisori, quello a sinistra presenta un asse fisso (A2), mentre quello a destra ha due assi (A1 e B1). È dunque ottimo per la lavorazione di pale per turbine, come da tradizione C.B. Ferrari, ma può affrontare anche giranti e rotori direttamente sul divisore di destra grazie alla presenza dell’asse mobile (U). In modalità “da barra”, il sistema di caricamento automatico spinge la barra nel divisore sinistro in base alla lunghezza del pezzo, dopo di che viene bloccata e lavorata di tornitura e fresatura. In seguito il divisore di destra afferra il pezzo, che viene separato dalla barra, e il mandrino ne completa la lavorazione prima di procedere con lo scarico. Un tema importante quando si parla di tornitura su macchine di fresatura sono le forze scaricate sul mandrino: per evitare che le forze di taglio gravino sui cuscinetti e su altri componenti delicati, in fase di tornitura il mandrino viene bloccato tramite dentatura Hirth, consentendo così di effettuare anche asportazioni importanti.
Il campo di lavoro
La testa continua (asse B2) consente l’inclinazione dell’asse del mandrino. L’asse verticale è dotato di un sistema di bilanciamento idraulico che ne compensa il peso, ottenendo così un notevole miglioramento in termini di sensibilità e di precisione di posizionamento dell’asse Z. Il volume di lavoro della macchina è tale da potere accogliere pezzi di diverse dimensioni in base alla loro conformazione e al relativo utilizzo dei divisori. In configurazione con divisore fisso a un asse sul lato sinistro e un divisore mobile a 2 assi sul lato destro (B1 = 0°), è possibile fissare il grezzo sul solo divisore sul lato destro per lavorare un cilindro in acciaio con diametro di 300 mm, lunghezza di 250 mm e massa di 140 kg. Utilizzando contemporaneamente i due divisori, invece, può essere lavorato un cilindro in acciaio con diametro di 300 mm, lunghezza massima di 500 mm e peso di 300 kg. In configurazione attrezzata con divisore mobile a due assi sul lato destro con B1 = 90°, la macchina può accettare un cilindro in acciaio con diametro di 400 mm, altezza di 150 mm e massa di 150 kg, oppure un cubo in acciaio con lato di 280 mm e massa di 170 kg.
Il sistema di comando
La A236 può essere fornita con differenti controlli numerici. Il modello Heidenhain TNC640 è in grado di controllare fino a 24 assi (di cui 4 mandrini) e offre uno schermo touch da 19” con, in opzione, il controllo adattivo dell’avanzamento (AFC), la soppressione attiva delle vibrazioni (ACC), il sistema KinematicsOpt per il mantenimento delle geometrie degli assi in ogni condizione operativa e così via. Siemens 840D SL, invece, è in grado di controllare fino a 93 assi/mandrini; offre anch’esso uno schermo touch screen da 19” e le opzioni per la compensazione termica dei sistemi di misura, la compensazione volumetrica e altro ancora. Infine, l’ultimo nato in casa Siemens: Sinumerik ONE. Questo controllo numerico, presentato nel 2019 in occasione della EMO di Hannover (e festeggiato per i suoi 60 anni alla recente 32. Bi-MU 2020 di Milano), è di tipo nativo digitale: garantisce infatti rapide innovazioni grazie alla perfetta interazione tra mondo reale e virtuale grazie al concetto di gemello digitale, attraverso il quale è possibile simulare con un altissimo grado di rispondenza ogni dettaglio della macchina e delle relative lavorazioni. Molte le nuove funzioni software implementate, come Top Speed per un aumento significativo della velocità di lavorazione degli stampi, Intelligent Load Control (ILC) per adattare automaticamente i parametri dinamici e di controllo sull’asse, Integrated safety functions per operatore e macchina e così via. Tramite il software Create MyVirtual Machine si può sviluppare e testare il “gemello digitale” della macchina utensile in termini di CNC, PLC, HMI senza necessità di alcun hardware. È possibile collaudare il modello e verificarlo prima ancora di avere realizzato la macchina. In questo modo si può abbreviare significativamente il tempo di messa in servizio della macchina reale configurando il sistema e usando il modello virtuale anche per tutte le attivita di service della macchina stessa. I vantaggi si estendono anche all’utilizzatore, che puo sfruttare la medesima tecnologia per simulare processi e cicli di lavoro prima di trasferirli in macchina. C.B. Ferrari ha realizzato il gemello digitale della A236, in grado di adattarlo alle esigenze dell’utilizzatore. Indipendentemente dalla scelta del controllo numerico, la A236 nasce per trarre il massimo beneficio dalle tecnologie connesse in ottica Industria 4.0 all’interno di un ambiente industriale automatizzato e interconnesso.
Una testa, molteplici opzioni
Il centro di lavoro A236 e dotato di una testa continua con motore torque (asse B2) in grado di effettuare una rotazione di ±120° attorno all’asse mandrino. La velocita di rotazione in rapido e di 60 giri/min e assicura una coppia di lavoro di 740 Nm (1320 Nm in rapido). All’interno della testa possono essere alloggiati diversi tipi di elettromandrini a cartuccia, a partire da quello da 30 kW, 24.000 giri/min e 48 Nm di coppia salendo a quello da 42 kW, 20.000 giri/min e 67 Nm di coppia. Per lavorazioni meccaniche che richiedono coppie elevate, nello stesso housing dell’elettromandrino da 30 e 42 kW puo essere installato un modello da 50 kW con attacco HSK-A63 (o HSK-T63 per gli utensili di tornitura), 16.000 giri/min e 90 Nm di coppia.
Accessori indispensabili
La A236 e dotata di un magazzino utensili ad asse orizzontale che puo essere configurato con 40, 60 o 80 posti. Essendo posizionato sul lato sinistro della macchina, e progettato per lasciare lo spazio opportuno per consentire il passaggio delle barre. Il cambio dell’utensile avviene con testa ruotata di +90° (asse mandrino orizzontale) in 2,2 s, mentre in prossimita dello scambiatore e posizionato un misuratore laser che effettua la misurazione e il controllo presenza utensile. Sulla A236 i trucioli e il fluido lubrorefrigerante vengono raccolti in una vasca e convogliati tramite una coclea in un trasportatore di trucioli. Lo scarico dei trucioli avviene sul lato posteriore della macchina per consentire l’impiego del caricatore automatico di barre e del sistema di scarico automatico dei pezzi. In presenza di materiali particolari come alluminio, titanio e loro leghe e possibile avere dei trasportatori di trucioli speciali in cui il fluido lubrorefrigerante viene aspirato dalla pompa in un apposito pannello lamellare (prefiltro) con grado di filtrazione di 600 μm. In questo modo il fluido viene trasferito gia prefiltrato all’impianto di refrigerazione utensile, che a sua volta e dotato di un filtro con grado di filtrazione pari a 10 μm.
Raffigurazione “esplosa” della macchina in alto: disegnata da Domenico Mulinello e Giovanni Mapelli
Condividi l'articolo
Scegli su quale Social Network vuoi condividere