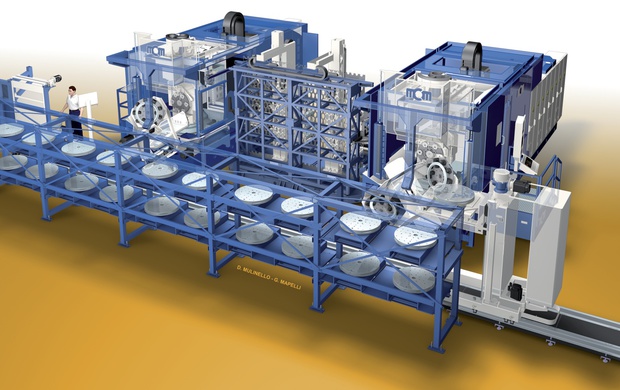
Il nuovo modello i.Tank 1300/1600 con mandrino di tornitura e fresatura in orizzontale di MCM riscrive il concetto multitasking e rende le operazioni di setup, tornitura, fresatura e rettifica più sicure, veloci e affidabili.
Il settore aeronautico è tra i più esigenti in termini di complessità tecnologica nella lavorazione dei pezzi. Per questo motivo è indispensabile utilizzare macchine e impianti in grado di offrire il massimo da ogni punto di vista: precisione, produttività, flessibilità operativa, affidabilità.
Da questo punto di vista, MCM vanta un curriculum di assoluta eccellenza: fondata nel 1978, l’azienda piacentina è stata un precursore nello sviluppo della fabbrica automatizzata sviluppando nel corso degli anni macchine e software pensati proprio per soddisfare queste necessità.
MCM è presente nel settore aerospace fin dagli anni ‘90: oggi l’azienda è considerata la scelta primaria dai principali costruttori e contoterzisti per la produzione sia di parti strutturali di estrema precisione, sia di componenti soggetti a estremo affaticamento, come le parti motore fisse e rotanti e altre parti strategiche dei velivoli.
Nel 2005 MCM realizza la prima macchina multitasking ad asse orizzontale con il modello Clock 1200; tale concetto viene poi esteso come gamma dimensionale alla famiglia i.Tank. Questa vera e propria rivoluzione si rivela vincente per la lavorazione di pezzi con un diametro massimo di 1.100 mm.
L’interesse del gruppo SAFRAN per nuovi metodi multi-processo in automazione si concretizza prima con la fornitura di un FMS di quattro macchine a Messier Bugatti Dowty, sede di Molsheim (Francia), per l’industrializzazione del gruppo “ruota-freno” della gamma A320-A380 Airbus (si veda la Macchina del Mese di settembre 2013). Oggi con Snecma sede di Le Creusot (Francia), SAFRAN consolida il rapporto con MCM attraverso la fornitura di nuove linee produttive complete, chiavi in mano, per la produzione di “dischi”; inizierà così la produzione di parti rotanti del nuovo motore aeronautico “Leap” con un innovativo processo adatto a componenti estremamente sofisticati e una nuova generazione di macchine marcate MCM.
La prima parte dell’impianto è composta da due centri di lavoro i.Tank 1300 Multitasking di fresatura e tornitura ad asse orizzontale, dotati di mandrino di tornitura su quinto asse e di una serie di opzioni che ne personalizzano ulteriormente la configurazione e le prestazioni.
Nata per l’aeronautico
L’applicazione in Snecma Le Creusot è il frutto di una collaborazione continua con il gruppo SAFRAN iniziata da oltre 15 anni con il gruppo Hispano. Le applicazioni sviluppate in co-engineering per assicurare soluzioni ad hoc, precise e sofisticate sono in grado di assicurare le specifiche di accettazione e la capacità di operare su più turni senza presidio, così da ridurre sia i costi di gestione del processo produttivo, sia i tempi di produzione e assicurare un processo sicuro.
Con questo inizio di fornitura della prima FMS dedicata alla lavorazione di componenti per il nuovo motore Leap, MCM concretizza un nuovo traguardo nel campo della lavorazione di pezzi estremamente innovativi prodotti con tecnologia multitasking.
Diverse aziende del prestigioso gruppo francese sono già da tempo clienti utilizzatori dei prodotti MCM.
Processo sicuro
Il concetto di lavorazione multitasking ad asse orizzontale comporta infatti benefici evidenti: innanzitutto la forza di gravità stessa contribuisce a un più semplice smaltimento dei trucioli, che altrimenti rischierebbero di venire rimacinati (con pessime conseguenze sulla finitura superficiale del componente e sulla durata del tagliente dell’utensile).
Le difficoltà tecniche insite in questa soluzione sono diverse, ma in MCM hanno saputo risolverle in maniera vincente. Lo scambiatore di pallet, ad esempio, deve gestire un pezzo fino a 800 kg di peso e un diametro di 1.100 mm.
Rigidità, velocità e precisione sono altre caratteristiche di i.Tank, che basa il proprio successo sulla modularità del progetto: la flessibilità della proposta è data dall’ampia scelta in termini di corse, pallet, tavole, teste, azionamenti e dalla vasta gamma di elettromandrini, capaci di assicurare coppie estreme e alte velocità, il tutto massimizzato dalla solidità della struttura, che consente di ottenere simili performance anche in presenza di asportazioni considerevoli e su materiali particolarmente tenaci.
La gamma di centri di lavoro MCM vanta prestazioni ideali per la produzione di particolari in titanio, inconel e super-leghe, destinati non solo al mondo aerospace, ma ovunque siano richieste lavorazioni precise e complesse: automotive, energetico, movimento terra e meccanica generale.
Struttura e assi
La struttura di i.Tank 1600, realizzata in acciaio elettrosaldato, permette un maggiore controllo della rigidezza, sostenendo la grande dinamicità della macchina. Caratteristica peculiare è la slitta asse X a elevata inclinazione, che irrigidisce fortemente il gruppo montante-carro apportando benefici prestazionali.
L’area di lavoro è stata dimensionata per lavorare intere famiglie di pezzi: le corse raggiungono i 1.600×1.010×1.400 mm rispettivamente sugli assi X, Y e Z.
Le due serie di guide sulle quali scorre l’asse X offrono un appoggio solido e stabile, all’interno del quale ricade il baricentro in Y e Z dell’intera parte in movimento. In questo modo la stabilità della macchina è sempre assicurata, anche in occasione della massima accelerazione e degli avanzamenti rapidi 50 m/min.
La precisione è garantita non solo dalla intrinseca rigidezza della struttura, ma dal processo produttivo della stessa attraverso una serie di lavorazioni, distensioni e una severa serie di collaudi durante le varie fasi produttive.
Particolare attenzione e cura è dedicata alla fase nanometrica di raschiettatura, che rende la struttura un vero e proprio strumento di precisione.
L’attenta progettazione termosimmetria della struttura, la climatizzazione di tutte le parti calde, abbinata alla sapiente applicazione dei sistemi di misura, ne permettono l’utilizzo preciso anche in presenza di transitori termici.
L’area di lavoro
La famiglia i.Tank può essere equipaggiata con diverse tipologie di mandrini in funzione delle coppie e del numero di giri richiesti.
Il cambio pallet avviene tramite uno speciale scambiatore che, attraverso una rotazione a 45°, è in grado di predisporre il pallet in modo che il pezzo entri in area di lavoro nella corretta posizione per la lavorazione, che avverrà appunto con asse di rotazione orizzontale.
Il nuovo impianto di tornitura/fresatura ha richiesto l’impiego di un elettromandrino Capto C8 da 8.000 giri/min, capace di erogare una potenza di 60 kW e una coppia di 487 Nm.
La tavola girevole (asse B) a 3.600.000 posizioni ha un sistema di trasmissione tradizionale con vite a corona e una velocità di rotazione di 20 giri/min.
Il gruppo divisore (asse C), fissato alla tavola girevole, monta un motore torque e garantisce una velocità di rotazione che arriva ai 30 giri/min in fresatura e fino a 1.200 giri/min in tornitura.
Il magazzino utensili dispone di 600 posti ed è di tipo condiviso tra le due macchine: un sistema di scambio rapido degli utensili permette di ridurre al minimo il tempo di cambio, evitando nel contempo l’inutile duplicazione di utensili (spesso speciali e molto costosi) su macchine distinte.
In fase di tornitura, un particolare sistema di bloccaggio si occupa dell’indexaggio del mandrino in posizione fissa: sarà quindi il gruppo divisore a girare, diventando così un vero e proprio mandrino di tornitura erogando una potenza massima di 77 kW e una coppia massima di 2.600 Nm.
Il divisore dispone di un sistema di stabilizzazione e bilanciatura statica-dinamica, porta un pallet tondo diametro 800 mm e permette un ingombro di rotazione nell’area di lavoro (attrezzatura + pezzo) pari a 1.100 mm (diametro) e 500 mm (altezza), con un peso caricabile su pallet di 800 kg.
Un sistema integrato di controllo equilibratura pezzo garantisce la perfetta operazione di centraggio dello stesso, e assicura la perfetta operazione di fissaggio dello stesso fatto dall’operatore.
L’automazione
Il primo step del nuovo impianto FMS per il gruppo aerospaziale francese si compone di due centri di lavoro identici con magazzini pallet e utensili in condivisione: il risultato è una soluzione altamente produttiva, senza che sia necessario duplicare tutte le risorse e i relativi sistemi di gestione.
Il magazzino utensili è di tipo mirror condiviso tra due macchine, ciascuna delle quali è dotata del proprio modulo a rastrelliera verticale a 199 posti; un modulo supplementare aumenta la flessibilità e la capacità totale fino 597 utensili circa (configurazione prevista per ogni coppia di macchine).
Il sistema di pallettizzazione lineare è composto da 32 posti di stoccaggio disposti su due livelli e altrettanti pallet, per dare all’impianto l’autonomia necessaria per gestire pezzi e attrezzi diversi.
La gestione dei singoli pallet sulle due macchine avviene attraverso navetta su rotaie.
Il posto operatore per il carico e lo scarico dei pezzi è motorizzato per la rotazione e la traslazione ed è dotato di un cuscinetto di precisione che, insieme a un sofisticato sistema, assicura il corretto centraggio del pezzo. Questa postazione è accessoriata inoltre di un avvitatore elettrico dedicato al preciso fissaggio dei pezzi, operazione gestita da apposito software.
Ogni dettaglio dell’impianto, dagli utensili agli accessori, è gestito da funzioni speciali e da software dedicati. Il tutto è supervisionato dal sistema di controllo denominato jFMX, creato e sviluppato nel corso di oltre venticinque anni dalla divisione Software e Architetture informatiche di MCM.
Il supervisore assicura il coordinamento e la gestione in tempo reale di tutte le risorse d’impianto. jFMX, strutturato su più livelli, è pensato proprio per gestire l’enorme mole di variabili che la flessibilità comporta e per facilitarne l’integrazione all’interno del sistema informativo aziendale. In questo modo la flessibilità e l’ottimizzazione dell’autonomia produttiva sono rese effettivamente disponibili.
Power Skiving
Il vantaggio di lavorare in orizzontale rende il processo stabile e sicuro anche in condizioni di estrema precarietà, lavorazione di acciai ad alta resistenza, realizzazione di cave interne per distributori o cave di o-ring.
L’elevata stabilità di processo, abbinata alle alte velocita (1.200 giri/min con pallet diametro 700 mm), precisione e prestazione dinamiche estreme, hanno permesso l’adozione di nuove tecnologie, come la lavorazione di ingranaggi ad alta velocità.
La tecnologia di Power Skiving permette la fresatura di ingranaggi interni ed esterni di diverse dimensioni con una stessa fresa progettata per un modulo specifico.
Con il metodo Power Skiving il taglio dell’ingranaggio è continua e la coppia pezzo-utensile ruota ad alta velocità. L’utensile avanza in modo uniforme nel senso dell’asse della dentatura e genera il profilo dei denti in modo graduale lungo tutta la fascia dell’ingranaggio, sia questi esterno o interno.
Si tratta di una tecnologia altamente produttiva e flessibile che oggi si può impiegare sui centri di lavoro di ultima generazione capaci di sincronizzare opportunamente il mandrino di fresatura con la tavola portapezzo di tornitura, che deve ruotare a un elevato numero di giri.
Questo permette la lavorazione di dentature su pezzi complessi senza il cambio macchina e senza riposizionamenti, garantendo un’elevata precisione di realizzazione.
Per applicazioni di modulo 4 – dentatura interna – la velocità di rotazione dell’utensile può arrivare anche a 2.300 giri/min e 800 giri/min del pezzo.
Condividi l'articolo
Scegli su quale Social Network vuoi condividere