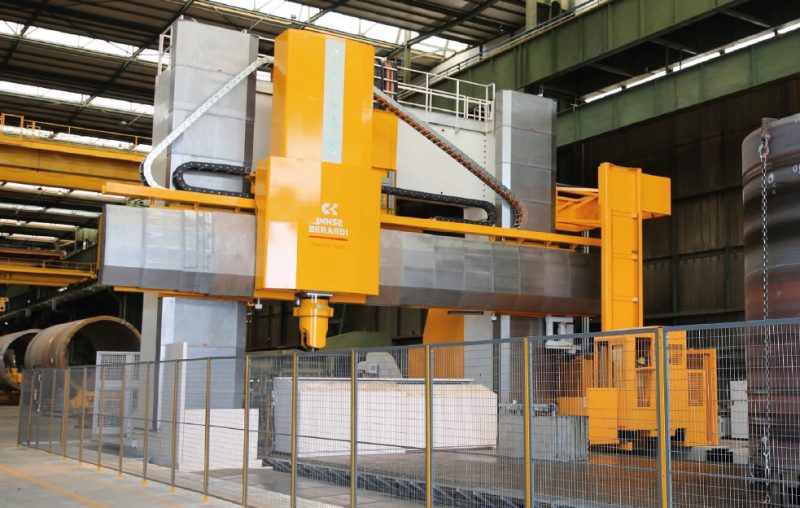
Alti livelli di precisione, produttività e flessibilità sono i vantaggi ottenuti da Walter Tosto con l’acquisto del centro di lavoro a portale mobile Atlas Hydro di Innse-Berardi. Installato presso la Belleli di Mantova, il centro è destinato alla produzione di componenti critici per il nucleare.
di Ernesto Imperio ed Ezio Zibetti
Grazie alla consolidata esperienza nella progettazione e produzione di componenti critici per l’industria di processo, in particolare chimica, petrolchimica, oil & gas ed energia, Walter Tosto è riconosciuta in tutto il mondo come eccellenza tecnologica nella realizzazione di apparecchi in pressione di altissima qualità. L’azienda abruzzese è a capo dell’omonimo Gruppo e svolge le sue attività produttive in sei stabilimenti ubicati a Chieti, presso un workshop all’interno del porto di Ortona con sbocco diretto sulle vie del mare, uno stabilimento con sede a Bucarest, Walter Tosto WTB, e un ulteriore insediamento a Oltenita (WTO) in Romania con accesso diretto al fiume Danubio. Dal 2016 appartiene al Gruppo la società mantovana Belleli, specializzata nella progettazione e realizzazione di apparecchiature di processo nei settori oil & gas, generazione termica e nucleare con la fornitura di reattori/recipienti in pressione sino al peso di 1800 t. Un’operazione lungimirante che non solo ha riportato un’eccellenza italiana nuovamente in mano a imprenditori nazionali dopo un decennio vissuto sotto il controllo della società americana Exterran, ma ha consentito al Gruppo di dare continuità alla sua strategia di espansione. Walter Tosto, la consorella Belleli Energy CPE e Walter Tosto WTB, condividono la stessa filosofia aziendale di sviluppo socialmente sostenibile basata su qualità, miglioramento continuo, trasparenza e flessibilità; uno sviluppo che affonda le sue radici nella forte volontà di investimento, sia nell’aggiornamento tecnologico degli impianti sia nel capitale umano, con l’inserimento di molti giovani e la creazione di una Academy per formarli esaltandone le eccellenze. «L’elemento chiave del nostro successo – esordisce Luca Tosto, amministratore delegato della Walter Tosto SpA e presidente di Belleli – è la capacità di investire in tecnologie d’avanguardia per modernizzare con continuità la fabbrica e, di conseguenza, per garantirci massima competitività sui mercati. Operiamo nel settore dell’energia, con particolare riferimento agli ambiti oil & gas e nucleare sia convenzionale che scientifico; da un punto di vista geografico operiamo in tutti i mercati del mondo direttamente o, più spesso, come sottocontraenti di aziende che esportano fuori Europa. Le nostre commesse di lavoro riguardano soltanto gli item critici degli impianti la cui criticità fa riferimento a dimensione, volume, peso e metallurgia dei componenti che realizziamo; per loro forniamo anche l’ingegneria di dettaglio e, in molti casi, anche l’ingegneria termica e di processo. Il 70% del nostro monte ore per la fabbricazione è sulla saldatura, dove vantiamo tecnologie di processo d’avanguardia e lunga esperienza nella lavorazione di materiali difficili da saldare, come per esempio il cromomolibdeno-vanadio, tipico dei recipienti sottoposti ad altissime pressioni e temperature di esercizio. Con gli ultimi investimenti che abbiamo fatto in macchine utensili avanzate, tra le quali il centro di lavoro verticale a portale mobile Atlas Hydro della bresciana Innse-Berardi, le ore di lavorazioni meccaniche stanno aumentando e ci stanno consentendo di entrare in progetti di big science o in quelli a elevata complessità meccanica».
Walter Tosto sceglie l’innovazione di Innse-Berardi
In tale scenario, il più recente investimento è stato deciso nel 2017 con l’acquisizione di un grande centro di lavoro a portale mobile a 5 assi, a elevate prestazioni, progettato e realizzato da Innse-Berardi; installato nello stabilimento mantovano di Belleli, il centro di lavoro è stato destinato principalmente alla lavorazione di componenti critici del progetto ITER, il più importante progetto a livello mondiale per lo sviluppo della fusione nucleare a freddo come fonte attuabile e sostenibile di energia. «La lunga esperienza sulla tecnologia idrostatica, la capacità di offrire soluzioni personalizzate avanzate e una macchina completamente digitalizzata con algoritmi di proprietà per la manutenzione predittiva – ha sottolineato poi Luca Tosto, in quanto presidente di Belleli – rappresentano il mix vincente che ci ha portato a selezionare Innse-Berardi per concretizzare la nostra partecipazione al progetto ITER». La fornitura di questo avanzato impianto di fresatura rappresenta per la società bresciana il coronamento di un significativo impegno progettuale che ha portato a soddisfare puntualmente tutte le sfidanti richieste del cliente, sia in termini di prestazioni che in termini di tempistiche per l’avvio in produzione. Innse-Berardi, dal 1999 appartenente alla divisione Machine Tools del Gruppo Camozzi, rappresenta una delle principali realtà industriali, a livello internazionale, nel settore della progettazione e costruzione di macchine utensili e vanta una storia di oltre 120 anni. La mission della divisione Camozzi Machine Tools è rivolta alla progettazione e alla produzione di macchine utensili di grandi dimensioni, sviluppate con l’obiettivo di fornire soluzioni specifiche per massimizzare l’investimento dei clienti in termini di prestazioni e di efficienza produttiva. In particolare, l’offerta di Innse-Berardi si compone di centri di lavoro orizzontali e verticali ad alta velocità, fresatrici orizzontali e verticali di medio-grandi dimensioni, macchine speciali destinate a specifiche applicazioni, macchine customizzate sulla base delle esigenze produttive del cliente. Si tratta di soluzioni avanzate che trovano applicazione in tutti quei settori dove si richiedono lavorazioni ad alto valore aggiunto come, per esempio, quello dell’energia, dell’aeronautico/aerospaziale, del siderurgico, del navale, delle lavorazioni meccaniche pesanti e, al tempo stesso, di precisione. Il prezioso bagaglio di esperienze maturato da Innse-Berardi nel corso degli anni, continuamente valorizzato dalla costante attenzione verso l’innovazione tecnologica e verso la fornitura di soluzioni tailor made, è stato un fattore determinante per la scelta dell’azienda bresciana da parte di Walter Tosto.
Dalle esigenze alla soluzione
«Il progetto ITER – spiega Tosto – costituisce la più rilevante collaborazione internazionale nel campo dell’energia che coinvolge il 50% della popolazione mondiale e copre l’80% del PIL globale. In qualità di membro del Consorzio AMW, a cui appartengono anche Ansaldo e Mangiarotti, il Gruppo Walter Tosto è stato incaricato della fornitura di cinque settori della Vacuum Vessel, il cuore della macchina Tokamak. Per la lavorazione di tali componenti in acciaio inossidabile ad alto contenuto di boro, elemento utilizzato per assorbire i neutroni veloci emessi dal plasma durante le reazioni di fusione, sono richieste macchine a elevata rigidità e con un’elevata affidabilità di prestazioni in termini di precisione e di produttività. Per rispondere a queste esigenze abbiamo ritenuto che Innse-Berardi fosse l’interlocutore giusto; il centro di lavoro verticale a portale mobile Atlas Hydro, opportunamente configurato, ci è sembrato adeguato alle nostre esigenze: una macchina tecnologicamente avanzata che mette a frutto la grande esperienza maturata dall’azienda nella lavorazione di acciai inossidabili ad alto contenuto di boro. Tale lavorazione, per conseguire elevati volumi produttivi, richiede particolari attenzioni progettuali e costruttive. Avevamo bisogno anzitutto della certezza della precisione di lavorazione e di una determinata dimensione di macchina per realizzare i componenti del reattore nucleare. La flessibilità intrinseca della Atlas Hydro, inoltre, ci ha consentito di ottenere dalla Innse-Berardi alcune modifiche e migliorie sulla macchina, ottimizzando così alcuni processi di lavorazioni».
Atlas Hydro, tecnologia al top
Con una luce tra i montanti di 7200 mm e una distanza massima tra naso mandrino e piano di lavoro di oltre 6600 mm, la macchina è in grado di lavorare tutta la gamma dei pezzi di grandi dimensioni prodotti nello stabilimento Belleli. «Nella fattispecie – spiega Stefano Lodolo, direttore commerciale di Innse-Berardi e di Camozzi Manufacturing – la soluzione presenta una struttura di macchina sovradimensionata in acciaio elettrosaldato calcolata attraverso metodi di analisi degli elementi finiti, per garantire la massima stabilità e rigidità d’insieme. Data la grande dimensione delle masse in movimento, per conseguire il massimo smorzamento delle vibrazioni, grande durata nel tempo, minima manutenzione e, dunque, minori costi di esercizio, gli assi lineari e il RAM sono a sostentamento idrostatico. La macchina è stata anche corredata di una testa universale a 5 assi per potere lavorare pezzi molto complessi, spesso ricavati dal pieno. Un capiente magazzino automatico con teste accessorie e un magazzino utensili a catena di grande capacità danno alla macchina una grande flessibilità di utilizzo sia per applicazioni con grandi asportazioni di truciolo che per lavorazioni dove è richiesta una grande precisione». Il movimento di tutti gli assi lineari è realizzato con sistemi precaricati; per gli assi X e Y viene utilizzato un sistema a doppio pignone e cremagliera con recupero elettronico del gioco. «Con lo stesso principio, anche gli assi polari della testa universale a 5 assi – evidenzia Lodolo – utilizzano un sistema a pignone multiplo su ruota dentata per ottenere massima rigidità e alta dinamica di movimento in assenza di giochi. La soluzione adottata, con recupero del gioco elettronico, garantisce un precarico costante del sistema senza necessità di messe a punto periodiche e con minima necessità di manutenzione».
«Inoltre – interviene Tosto – questo centro di lavoro è stato concepito per poter integrare una tavola di tornitura di 6 metri con una portata di 250 t: è facile comprendere che con tale configurazione la nostra Atlas Hydro raggiunge massimi livelli di flessibilità: aspetto estremamente importante per noi che costruiamo pezzi singoli».
Vantaggi della soluzione Innse-Berardi
Il centro di lavoro a portale mobile, ora in piena produzione, offre significativi vantaggi: in primis l’alta produttività grazie all’elevato tasso di asportazione truciolo e al livello di automazione implementato sulla macchina. Il cambio utensili e cambio teste accessorie automatico, l’uso di sonde elettroniche per misurare i pezzi, la possibilità di controllare la lavorazione in remoto con l’uso di telecamere infatti riducono i tempi morti e garantiscono la massima produttività della macchina. «Non meno significativi – aggiunge Tosto – sono i vantaggi derivanti dalle soluzioni tecniche adottate: tolleranze ristrette mantenute nel tempo, vita utile dell’utensile ottimizzata a parità di costanza di proprietà meccanica del componente da lavorare, consumo energetico ottimizzato grazie al costante monitoraggio delle utenze, sistema di evacuazione trucioli ottimizzato per una facile pulizia della zona di lavoro e cabina operatore mobile per permettere un controllo ravvicinato delle lavorazioni eseguite garantendo la massima sicurezza degli operatori».
«La macchina – interviene Lodolo – è dotata di controllo numerico Siemens 840D sl di ultima generazione ed è inoltre completamente digitalizzata per andare incontro alle esigenze dell’Industria 4.0, per massimizzare il fattore di utilizzo della macchina. La stessa, infatti, integra il sistema IBRM (Innse-Berardi Remote Maintenance), la piattaforma digitale dotata di algoritmi brevettati dalla nostra società in collaborazione con Camozzi Digital, che permette una reale manutenzione predittiva e un continuo monitoraggio dei parametri vitali della macchina. Oltre a un continuo controllo in tempo reale di una serie di parametri di funzionamento della macchina la piattaforma IBRM, che lavora in cloud, consente la diagnosi automatica sullo stato di salute dei suoi componenti critici. Questo avviene mediante un monitoraggio continuo delle condizioni di lavoro e dei parametri di processo mediante sensori installati sulla macchina. Nel momento in cui sono superate le soglie limite di alcune grandezze fisiche stabilite dagli algoritmi, si genera automaticamente un segnale di allerta per potere intervenire sulla macchina in modo immediato o programmato/predittivo».
«Siamo particolarmente soddisfatti dell’investimento – conclude Tosto – perché stiamo registrando performance di macchina molto alte. E poi si tratta di un costruttore italiano: è bravo, rapido nella realizzazione della macchina e con la voglia di sperimentare insieme a noi alcune soluzioni innovative».
Condividi l'articolo
Scegli su quale Social Network vuoi condividere