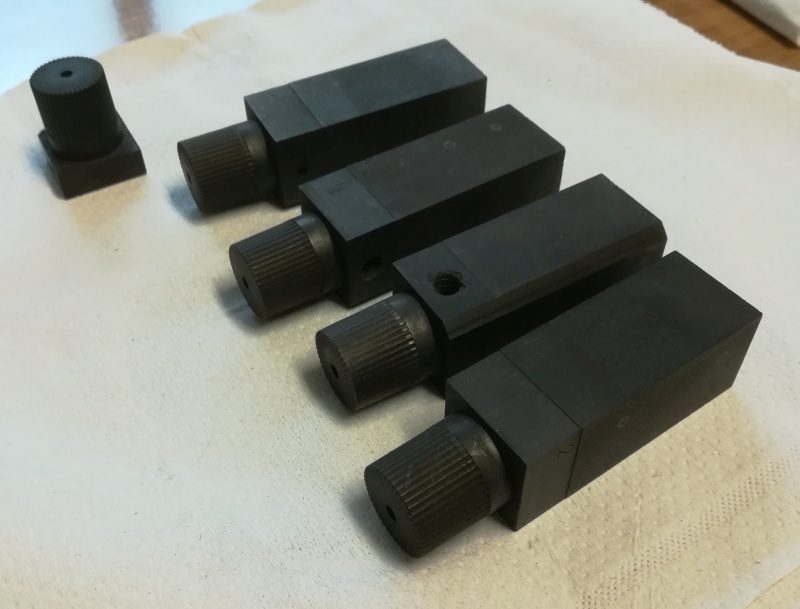
Con gli elettrodi in grafite forniti da Tokai Carbon O.M.A. ha migliorato l’efficienza nella produzione di uno stampo tramite elettroerosione
Per capire quando è utile usare elettrodi in grafite, abbiamo intervistato un costruttore di stampi per la formazione termoplastica che ha scelto questa soluzione per un suo prodotto. O.M.A. è un punto di riferimento per il mercato del packaging alimentare, dei prodotti monouso, del campo automobilistico, medicale e dell’imballaggio in generale.
Passione, sacrifici, volontà e capacità d’investire in tecnologie all’avanguardia; organizzazione e competenza maturata nel comparto manifatturiero al fine di rispondere alle esigenze sempre più complesse di una clientela alla ricerca di veri e propri partner per la fornitura di soluzioni e servizi molto performanti: ecco la ricetta del successo di O.M.A., che da oltre quarant’anni progetta e realizza stampi per materie plastiche e lavorazioni meccaniche.
Specialisti dell’elettroerosione
Presente sul mercato dal 1975 l’azienda di Vermezzo (MI), con i circa 15 dipendenti suddivisi tra i reparti di progettazione, programmazione della produzione e lavorazione meccanica, è in grado di realizzare manufatti attraverso un processo completo che va dall’analisi delle specifiche alla progettazione computerizzata fino alla consegna del prodotto finito e della relativa campionatura al cliente. Quest’ultimo viene seguito e consigliato in ogni momento da personale altamente qualificato, capace di gestire tutte le fasi di progettazione ed esecuzione dello stampo in modo preciso e affidabile. Il processo di produzione prende il via all’interno dell’Ufficio tecnico dove, al ricevimento delle matematiche da parte dei clienti, il personale tecnico sviluppa lo stampo con avanzati software CAD-CAM 3D, rendendo disponibili i disegni esecutivi nella rete informatica aziendale per il personale presente all’interno dell’officina che si occupa della realizzazione pratica del manufatto. Un ampio parco macchine composto da centri di lavoro a controllo numerico, macchine per l’elettroerosione sia a tuffo che a filo, rettifiche e torni consente agli operatori di rispondere alle necessità anche molto complesse di un mercato sempre più esigente. «Un mercato che vuole prodotti in tempi brevi e dai costi concorrenziali, ponendoci quotidiane sfide da affrontare e vincere per rimanere competitivi, considerando anche e soprattutto i tempi di realizzazione dello stampo, passati da novanta a una quarantina di giorni – ha affermato Valentino Simondi, titolare di O.M.A. – Questo ci ha imposto un deciso cambio di passo nell’intero processo produttivo, dunque le macchine di cui disponiamo sono sempre più performanti per fare fronte a queste nuove esigenze realizzative.
Il grado di finitura dei particolari richiesto dall’industria sta via via raggiungendo livelli qualitativi un tempo impensabili, così che anche le fasi di assemblaggio hanno dovuto subire un’accelerazione. Proprio nell’ottica di potere ottenere un margine molto elevato di qualità dei manufatti, O.M.A. aveva bisogno di potere disporre di utensili speciali da utilizzare per compiere lavorazioni piuttosto delicate e importanti. «Infatti, in linea generale costruiamo noi gli elettrodi per l’elettroerosione, in rame o grafite, ma quando dobbiamo eseguire operazioni come per esempio la creazione di nervature sottili con pareti molto profonde, geometrie piccole e dettagliate o di grosse dimensioni abbiamo bisogno di elettrodi in grafite pronti da utilizzare, per potere ottenere un migliore risultato e una migliore finitura dello stampo – ha proseguito – Dopo una valutazione di quanto il mercato ci poteva offrire, dunque, la nostra attenzione s’è rivolta verso Tokai Carbon, azienda giapponese e realtà mondiale centenaria nella produzione di materiali ceramici avanzati per applicazioni industriali, tra i quali in evidenza la grafite isotropica per EDM, che ci ha affiancato da ormai quasi 20 anni guidandoci nella scelta dei prodotti più adatti alle nostre esigenze realizzative».
Pioniera sin dal 1918, leader anche nella produzione di grafite isotropica e grafite estrusa per applicazioni industriali, resistenze in carburo di silicio, glassy carbon, CFC (Tokarec), prodotti friction per macchine movimento terra e pastiglie freno, carbon black per la produzione di pneumatici e gomme speciali, elettrodi per acciaieria, nitruro di silicio ceramico e resistori ceramici, la società giapponese dà sempre al più alto livello tecnologico dei propri prodotti, i quali sono distribuiti nel nostro Paese da Tokai Carbon Italia Srl, filiale italiana aperta nel 1994, al 100% di proprietà del Gruppo nipponico, capace di assicurare un supporto tecnico altamente qualificato ai propri clienti e un servizio logistico snello e veloce grazie alla sede con magazzino a Trezzano Rosa, in provincia di Milano.
Performance al top
Gli elettrodi prodotti da Tokai Carbon e forniti alla Società O.M.A. sono realizzati in grafite isotropica. Detto materiale viene utilizzato nel comparto industriale dalla metà degli anni 60. In quel tempo l’EDM rappresentava per la grafite un’applicazione di nicchia e il rame dominava il mercato di riferimento. Solamente gli elettrodi di grandi volumi e pertanto di elevato peso venivano realizzati in grafite: densità grafite 1,8 g/cm3 contro gli 8,9 del rame.
Le grafiti disponibili a quei tempi, pur non essendo raffinate come lo sono oggi, soddisfacevano la richiesta prestazionale attesa. Comunque già si intravedeva quali fossero quelle buone proprietà fisiche del materiale grafite, motivazioni che hanno spinto i produttori come Tokai Carbon ad aumentare il livello qualitativo dei prodotti per EDM, e i produttori di macchine per EDM a realizzare meccanica sempre più adatte alle prestazioni date dagli elettrodi in grafite, portando così il comune pensiero che con la grafite si realizzano elettrodi anche di piccole dimensioni e per rugosità superficiali che furono tipiche solo dell’elettrodo in rame. L’aspetto interessante che ha spinto l’utilizzo di questo materiale all’interno del processo produttivo di O.M.A. deriva dal fatto che gli elettrodi in grafite consentono l’ottenimento di risultati avanzati in tempi molto più brevi rispetto al rame.
Entrando di più nel dettaglio della tecnologia, le grafiti vengono classificate secondo la granulometria: quelle con un valore elevato, dai 13 ai 10 micron, sono per lo più usate in sgrossatura; le grafiti che vanno dai 9 ai 6 micron sono per la finitura dove è richiesto un basso consumo dell’elettrodo e alta definizione, mentre le grafiti sotto i 5 micron sono utilizzate per un alto grado di finitura superficiale e basso consumo degli spigoli. La resistività (cioè il valore della resistenza al passaggio della corrente) della grafite è inversamente proporzionale alla granulometria, ovvero più è grande la granulometria meno è resistiva la grafite, ed è per questo che le grafiti di sgrossatura hanno una granulometria elevata: in questa fase di processo elettroerosivo è necessario utilizzare una quantità maggiore di corrente, e un prodotto meno resistivo ha un rendimento maggiore.
Questa è una classificazione indicativa di utilizzo dei vari gradi di grafite, ma la realtà ci insegna che le condizioni di lavoro e di scelta del grado appropriato di grafite variano a seconda delle dimensioni dell’elettrodo e alla sua morfologia. Per dare un’indicazione del livello di lavorazione cui sono soggetti gli stampi dell’azienda di Vermezzo, possiamo dire che si arriva a utilizzare anche elettrodi in grafite HK3 con granulometria di 2 micron per potere soddisfare le condizioni di lavoro e le specifiche richieste dai clienti.
Elettrodi in grafite Tokai Carbon
«La scelta di Tokai Carbon per questo tipo superiore di grafite è stata operata dall’Ufficio tecnico con a capo Luca Facchetti, ricercando il giusto bilanciamento tra le prestazioni durante il processo elettroerosivo (velocità di erosione, consumo dell’elettrodo, rugosità superficiale) e le proprietà meccaniche del prodotto, al fine di prevenire eventuali rotture durante la fresatura. La qualità HK3 di Tokai Carbon permette il passaggio di corrente necessario alla strategia di lavorazione e grazie a superiori proprietà meccaniche ha favorito le operazioni di costruzione dell’elettrodo durante le fasi di fresatura nella definizione della geometria – ha aggiunto Simondi – La collaborazione con la Tokai Carbon Italia Srl, filiale italiana della società nipponica, non si limita al solo servizio di fornitura del materiale ma anche alla condivisione delle metodologie di processo più adatte. Infatti, la tipologia di commesse che riceviamo rende i processi anche molto differenti tra loro, richiedendo così un confronto di idee per la loro ottimizzazione per mantenere alto il livello qualitativo, nello spirito che contraddistingue la nostra azienda da oltre quattro decenni».
Tokai si offre da sempre come partner delle aziende clienti per convogliare verso la migliore scelta del grado e per condividere quali sono i reali vantaggi ottenibili mediante il suo utilizzo nei processi di produzione: fresatura e processo erosivo. «Grazie alle soluzioni produttive e ai servizi forniti da Tokai Carbon stiamo lavorando molto bene nell’evadere molteplici commesse anche molto impegnative – ha voluto aggiungere Simondi- Guardando al futuro, abbiamo in programma importanti investimenti in nuovi impianti ad alta tecnologia per potere essere ancora più competitivi in un mercato molto complesso e articolato, che richiede aggiornamenti continui di mezzi e personale al fine di riuscire a soddisfare tutte le richieste produttive del comparto manifatturiero».
Condividi l'articolo
Scegli su quale Social Network vuoi condividere