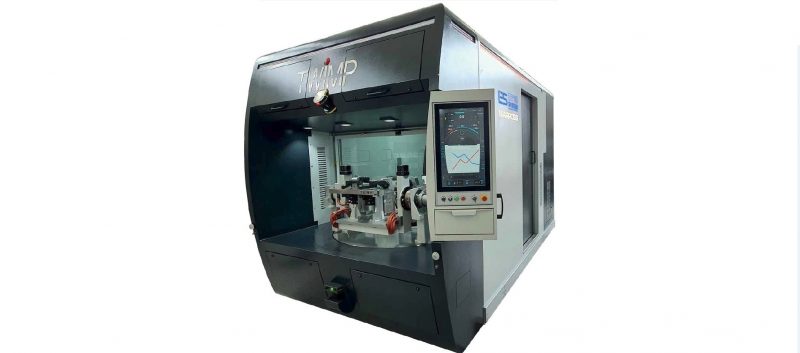
Twimp è una soluzione modulare progettata da Elettrosystem per l’esecuzione di processi laser di vario genere tra cui i principali sono taglio e saldatura attraverso una sorgente laser. Di recente l’azienda astigiana ha sviluppato un progetto nel quale Twimp viene utilizzata per saldare tra loro materiali diversi senza apporto di materiale.
di Davide Davò
Svolgere una costante attività di ricerca e sviluppo è uno dei pilastri su cui si deve basare la filosofia di qualsiasi azienda che intenda affrontare con successo il settore delle lavorazioni meccaniche. Attraverso tale attività infatti le imprese sono in grado di migliorare la propria produzione dal punto di vista della qualità del pezzo finito, della produttività, della riduzione degli scarti e del contenimento dei costi di processo. Ogni tecnologia infatti, per quanto evoluta possa rivelarsi, deve comunque rappresentare un investimento sostenibile per l’azienda non solo al momento dell’acquisto ma anche in fase di utilizzo. In quest’ottica, la costante evoluzione delle sorgenti laser fibra ne ha abbassato i costi e ampliato la possibilità di utilizzo, contribuendo così alla sua diffusione in svariate tipologie di applicazione. Ne è un esempio l’operazione di saldatura, ambito nel quale il laser fibra si sta dimostrando una valida alternativa alle tecnologie tradizionali. Lo dimostra una recente applicazione sviluppata da Elettrosystem, realtà appartenente al gruppo Marposs, che assecondando la richiesta di un cliente ha realizzato un progetto per la saldatura di alberi per pompe dell’acqua utilizzando appunto una sorgente laser fibra.
Una nuova sfida
«Elettrosystem è un’azienda fortemente votata all’innovazione: studiamo soluzioni sempre nuove seguendo strategie interne oppure rispondendo a specifiche esigenze provenienti dal mercato», ha esordito Anisa Kapxhiu, Application Manager di Elettrosystem. «Con questo spirito, quando un cliente ci ha chiesto di valutare la possibilità di realizzare alberi per pompe saldando tra loro barre di differenti materiali e diametri adottando una soluzione differente dalla saldatura TIG o da quella per frizione, abbiamo immediatamente accettato tale sfida per la quale non sono presenti in letteratura dati relativi a un processo di saldatura laser senza apporto di materiale su elementi pieni. Nel caso specifico, l’obiettivo principale era quello di identificare una tecnologia che avesse un impatto economico complessivo sulla produzione più basso rispetto a quello della soluzione utilizzata dal cliente al momento dell’avvio del progetto. Al contempo, la nostra proposta avrebbe dovuto garantire lo stesso livello di performance in termini di qualità e resistenza meccanica della saldatura. Infine, doveva mantenere inalterato il processo a monte e a valle della fase di saldatura, evitando l’introduzione di fasi di preparazione del componente o di altre operazioni».
La situazione di partenza studiata da Elettrosystem vedeva una barra in C40 di diametro 60 mm e lunga circa 300 mm, saldata a una barra in acciaio inox del diametro di 40 mm e lunga 300 mm tramite processo di Friction Stir Welding. Si trattava di un processo che richiedeva la fusione di circa 30 mm di materiale per eseguire una corretta saldatura, e di conseguenza un notevole consumo di materia prima che contribuiva all’incremento dei costi di produzione. Anche la valutazione relativa all’utilizzo della saldatura TIG, che insieme alla saldatura per frizione rappresenta una delle principali tecnologie adottate per la produzione di pompe dell’acqua, evidenziava costi legati non solo al materiale d’apporto in sé, ma anche al suo stoccaggio e alla sua gestione in produzione.
Con queste premesse, la possibilità di impiegare un sistema laser senza apporto di materiale si è dimostrata da subito vantaggiosa sul piano dell’impatto economico.
Aspirare i fumi
«Concluse queste prime valutazioni, ci siamo dedicati allo studio degli aspetti chiave del processo – ha proseguito Kapxhiu – e anzitutto abbiamo valutato le condizioni nelle quali i componenti giungono alla postazione di saldatura, notando una importante quantità di olio di lavorazione presente sulla superficie dei pezzi. Questi lubrificanti indispensabili per le operazioni di asportazione di truciolo rappresentano invece una criticità durante la saldatura. Se surriscaldati dal laser infatti generano fumi nocivi per l’operatore, mentre le particelle di olio che vengono inglobate nel cordone di saldatura generano dei difetti interni che compromettono la qualità e la resistenza meccanica della saldatura stessa. Abbiamo quindi deciso di adottare un sistema di aspirazione dei fumi che è stato agganciato alla testa laser per essere portato il più vicino possibile al punto di saldatura, aspirando in modo efficiente sia i fumi sia le particelle che potrebbero entrare nel bagno di fusione».
Sempre parlando di condizioni iniziali dei semilavorati, Elettrosystem ha valutato la qualità del taglio eseguito sugli spezzoni di barra per portarli alla misura desiderata. Le barre infatti vengono tagliate meccanicamente tramite un disco, e la superficie così lavorata presenta tolleranze non ottimali per un processo di saldatura. Di conseguenza, al momento dell’accoppiamento delle superfici si evidenziano alcune zone di vuoto. Motivo per cui è stata adottata una testa laser wobbling in grado di movimentare il fascio laser senza spostare fisicamente l’intera testa. Grazie a questa soluzione si riesce a portare a fusione una quantità di materiale tale da riempire il gap tra le superfici, ma evitando sprechi del materiale stesso poiché l’area interessata dalla fusione è minima.
L’angolo giusto
Grande attenzione è stata dedicata anche alla posizione che deve raggiungere il polso del robot sul quale è montata la testa di saldatura. La condizione ideale per una saldatura laser senza apporto di materiale vede il fascio incidere perpendicolarmente sulla superficie da lavorare. In questo caso però viene di fatto richiesta la realizzazione di un giunto a T su un profilo circolare, e di conseguenza diventa impossibile operare con un angolo di 90°. Elettrosystem ha superato questa criticità adottando due mandrini orizzontali come sistema di bloccaggio pezzo, che tengono in posizione i due spezzoni di barra e li mettono in rotazione in modo da permettere alla testa di saldare senza doversi muovere nello spazio. Inoltre è stato studiato un angolo della testa ottimale per realizzare un cordone di saldatura la cui posizione della zona fusa non risulti essere troppo orientata verso l’uno o l’altro spezzone di barra.
«Il quarto aspetto tenuto in considerazione è stato l’individuazione dei corretti parametri di lavoro della sorgente – ha precisato Kapxhiu – e per la saldatura di questi alberi possiamo utilizzare sorgenti da 8 o 10 kW che abbiano un BPP (Beam Production Parameter) basso, ovvero capaci concentrare un’alta densità di energia nel core del fascio. Considerando la necessità di fondere due materiali differenti, con proprietà e punto di fusione diversi, abbiamo dovuto studiare con attenzione una serie di parametri che ci hanno permesso di raggiungere una corretta temperatura del bagno di fusione per operare in modo uniforme sulle due barre. Questo ci ha permesso di ottenere una saldatura conforme alle specifiche richieste dal cliente in termini di resistenza meccanica a trazione, compressione e flessione, di profondità del cordone, di inclinazione del cordone e di assenza di difetti, il tutto abbattendo i costi di produzione».
Condividi l'articolo
Scegli su quale Social Network vuoi condividere