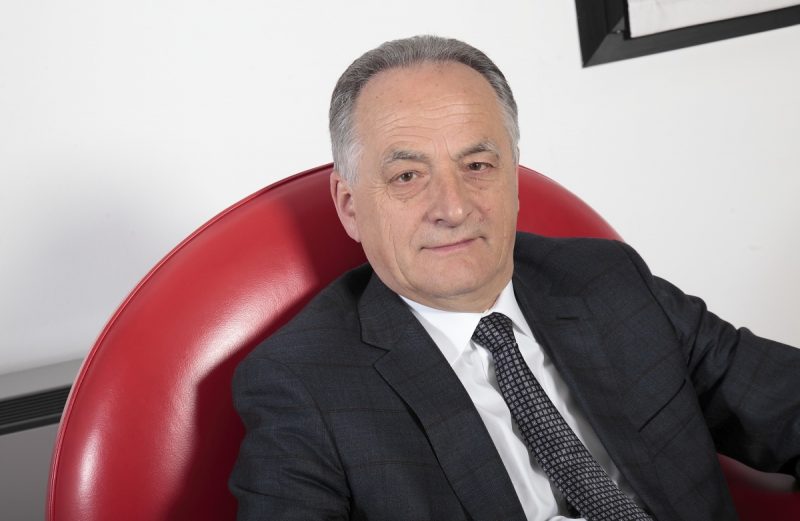
Classe 1952, Gianlugi Viscardi è perito meccanico. Nel 1982 fonda, insieme ai fratelli, la Cosberg SpA (di cui è CEO), azienda che produce macchine speciali e sistemi per l’assemblaggio, con impiego delle più innovative tecnologie nell’ambito della meccatronica, robotica e sistemi di visione. Attivamente impegnato nel mondo associazionistico ricopre importanti ruoli in Confindustria (è membro della Squadra di Presidenza di Piccola Industria Nazionale con focus sull’Innovazione), presidente del DIH (Digital Innovation Hub) Lombardia, presidente del Consorzio Intellimech e dal 2020 è a capo del Coordinamento nazionale della rete dei DIH di Confindustria. È inoltre vice presidente e membro del Comitato Tecnico Scientifico del Cluster Tecnologico Nazionale Fabbrica Intelligente, dopo avere ricoperto il ruolo di presidente per due mandati (2015-2019). Lo scorso 31 maggio 2021, su proposta del ministro dello Sviluppo Economico, Giancarlo Giorgetti, è stato nominato Cavaliere del Lavoro dal presidente della Repubblica, Sergio Mattarella.
di Edoardo Oldrati e Raffaella Quadri
La pandemia ha pesantemente segnato tutto il 2020 e il manifatturiero italiano oggi si trova ad affrontare le difficoltà della ripartenza. Qual è la prima sfida da superare e cosa possono fare governo e istituzioni per aiutare le aziende a ripartire?
La pandemia ha sicuramente segnato negativamente il 2020 ma ha evidenziato anche alcune opportunità, tra cui la necessità di affrontare un percorso di trasformazione digitale strutturato che ridisegni l’intero processo produttivo. La crisi ha accelerato l’affermazione delle tecnologie digitali come leva per rendere le imprese competitive e resilienti. Le realtà che avevano già iniziato il percorso di digitalizzazione, dotandosi di soluzioni digitali e di una struttura organizzativa adeguata a supportarle, hanno potuto rispondere meglio allo shock pandemico. In questo contesto la sfida più importante è supportare le PMI. Il Governo deve operare in questa direzione, potenziando anche gli strumenti finanziari per migliorare la competitività delle imprese sui mercati. Governo e istituzioni non devono mai lasciare sola alcuna organizzazione né alcun imprenditore, supportando la loro ripartenza e crescita. La digitalizzazione porta all’azienda un valore intangibile ma reale, che andrà poi riconosciuto nella valutazione dell’impresa anche a livello di patrimonializzazione.
Il DIH Lombardia ha come obiettivo “rafforzare il livello di conoscenza e di consapevolezza delle imprese rispetto alle opportunità offerte dalla trasformazione digitale”. Qual è ora il livello di conoscenza delle aziende lombarde su questi temi e quali le priorità che muovono l’azione del DIH Lombardia?
Già nel primo Piano Industria 4.0 ne erano stati indicati i tre pilastri: realizzare i DIH (Digital Innovation Hub), potenziare i Cluster e costituire i Competence Center. Confindustria ha fatto un grande lavoro per supportare le aziende in particolare creando una rete di DIH che sono, a tutti gli effetti, la “porta di accesso” delle imprese al mondo di Industria 4.0.
Il DIH Lombardia rappresenta il “medico di base” per le aziende: attraverso figure di manager professionisti fornisce un servizio di assessment di maturità digitale, che identifica lo stato dell’impresa e ne evidenzia le principali criticità. Tramite l’analisi dei trend del settore in cui la stessa opera e sulla base delle criticità emerse genera poi una roadmap di implementazione, fornendo un possibile percorso di trasformazione digitale. Inoltre si è sviluppato un modello di mappatura della filiera che è di uso comune fra i DIH delle diverse regioni e alcuni progetti di filiera – con a capofiliera Ansaldo, ABB e Leonardo – hanno già enfatizzato la forza della rete. Il ruolo del capofiliera è trainante per le PMI e permette all’intera filiera di crescere condividendo benefici comuni, sfruttando sinergie e cooperando in modo integrato. La forza del DIH Lombardia è quindi sia di offrire un livello qualificato di servizi, avvalendosi di un network di attori dell’innovazione nazionali ed europei, sia di lavorare in rete con gli altri DIH di Confindustria. Tramite lo strumento “Test Industria 4.0” sono stati realizzati circa 1.800 assessment di maturità digitale, di cui più di 400 dal DIH Lombardia.
Ne emerge una buona consapevolezza delle tematiche di Industria 4.0, ma con la necessità di fare progettualità. Con il piano Industria 4.0 le aziende hanno investito prevalentemente in Produzione, Qualità e R&S e sui sistemi ritenuti maggiormente appropriati, mentre resta molto da fare in ambiti quali gestione della domanda, approccio al mercato, servitizzazione di servizi ecc. Ora anche l’Europa sta lavorando alla costituzione degli EDIH (European Digital Innovation Hub), che saranno finanziati mediamente con 2 milioni di euro l’anno in compartecipazione tra Europa e Stato membro. L’Italia avrà diritto ad avere tra 12 e 23 EDIH.
Da anni, lei è impegnato nel CFI (Cluster Fabbrica Intelligente): come valuta questa esperienza?
Da ormai 8 anni collaboro proficuamente insieme al CFI, di cui come sapete sono stato anche presidente. In quegli anni la figura dei Cluster – a oggi in Italia sono in totale 12 – era nata da poco e grande parte del nostro lavoro è stato creare una community che raccogliesse gli stakeholder attivi nell’ambito del manifatturiero avanzato cioè imprese, territori, università, centri di ricerca e associazioni per lavorare insieme al futuro sostenibile del manifatturiero italiano. Con il MiSE abbiamo proposto il progetto dei Lighthouse Plant, che stiamo portando avanti con successo anche oggi; sono già 5 i progetti finalizzati. Grazie alla “Roadmap per la ricerca e l’innovazione”, redatta nel 2015, abbiamo individuato i macroscenari di sviluppo – Linee di intervento – all’interno dei quali programmare specifiche attività di ricerca e innovazione per i prossimi anni. L’aggiornamento della Roadmap 2015 è in corso di finalizzazione con il supporto di 60 esperti organizzati in 7 gruppi tematici tecnico-scientifici. Recentemente, proprio nell’ambito di CFI, è stato elaborato il documento “Produrre un Paese resiliente” che, sulla scorta della situazione creata dalla pandemia, definisce alcune possibili azioni da intraprendere per rendere le imprese e il Paese più pronti, resilienti e proattivi. È importante fare sistema, o meglio “ecosistema” volto all’innovazione. E i cluster ne sono attori primari.
Nel DESI (Indice di Digitalizzazione dell’Economia e della Società) della Commissione Europea per il 2019, l’Italia si colloca al 26° posto fra i 27 stati membri dell’UE nella categoria “Capitale Umano”. Sono le competenze, il freno allo sviluppo digitale della nostra industria? Come è possibile risolvere questa criticità?
Certamente bisogna fare ancora molto. Credo che i più grandi ostacoli siano due: la cultura aziendale deve orientarsi verso un futuro sempre più digitale, con una ricaduta sulle competenze presenti nell’organizzazione, e le aziende devono ricevere un supporto reale sul mercato. Spesso l’investimento in innovazione e tecnologie digitali è visto come non cruciale e troppo complesso da gestire, ma occorre comprendere l’importanza di sfruttare e anticipare questi cambiamenti. Allo stesso modo, bisogna evidenziare l’importanza della componente umana: non basta acquistare le tecnologie, bisogna investire nel personale e, in particolare, nei giovani, che dobbiamo considerare come una “tecnologia abilitante”.
Per quanto riguarda il mercato, spesso le imprese ricevono moltissime offerte di tecnologie, ma vanno supportate per fare combaciare fabbisogno e offerta. Alcune organizzazioni, in particolare PMI, non sempre comprendono quale sia il loro fabbisogno digitale e, per questo, è necessario orientarle verso soluzioni e approcci che creino realmente valore in un percorso di trasformazione, coerente con l’ecosistema di innovazione digitale costituito da DIH, Competence Center e Cluster tecnologici.
Il Piano Transizione 4.0 dovrà agire in uno scenario molto diverso da quello in cui è stato previsto: servono modifiche o correzioni per renderlo efficace?
Lo scenario è senza dubbio diverso e quest’ultimo anno ha colpito duramente la nostra economia e frenato gli investimenti delle imprese. Il Piano Transizione 4.0 però è completo e affronta tutti gli aspetti e gli interventi necessari alla trasformazione digitale. Inoltre, con la legge di bilancio 2021 è stato ulteriormente potenziato e ha molti punti di forza. In particolare è stata assicurata la continuità delle misure anche al 2022 con una premialità per il 2021; sono state rafforzate le aliquote dei crediti d’imposta per i beni strumentali materiali e immateriali – ordinari e 4.0 – e la R&S; sono stati ridottii tempi di compensazione del credito beni strumentali da 5 a 3 anni e il credito è fruibile già a partire dall’anno di entrata in funzione del bene; è stato ulteriormente rafforzato il credito d’imposta per la formazione 4.0, consentendo l’inclusione nella base di calcolo anche delle spese relative all’erogazione della formazione. Il piano potrebbe poi essere ulteriormente rafforzato con l’introduzione di una misura che consenta la cedibilità del credito d’imposta e lo sconto in fattura e con il rafforzamento ulteriore delle aliquote dei diversi crediti d’imposta, come previsto in un emendamento governativo alla legge di bilancio 2021 non ancora depositato e che dovrebbe essere recuperato in un prossimo provvedimento legislativo. La fase di ripartenza dell’economia italiana non può prescindere dalla ripresa degli investimenti delle imprese. Questa è la sfida del Paese e il Piano Transizione 4.0 rappresenta un asse portante del PNRR (Piano Nazionale di Ripresa e Resilienza).
Dopo anni dalla loro ideazione finalmente gli 8 Competence Center hanno iniziato le attività aprendo le loro strutture e lanciando programmi e finanziamenti. come valuta queste realtà?
I Competence Center, centri di eccellenza nazionali ad alta specializzazione che fanno parte dell’ecosistema digitale, sono realtà molto importanti perché permettono alle aziende di “scaricare a terra” i progetti. Successivamente alla realizzazione della roadmap da parte dei DIH e all’analisi interna aziendale sulle priorità le imprese possono orientarsi verso i Competence Center, che sono partner strutturati nell’implementazione del percorso di trasformazione digitale.
Per tante aziende del manifatturiero l’innovazione arriva dai propri fornitori. Quale ruolo dovrà avere la supply chain nell’evoluzione del nostro manifatturiero?
La trasformazione digitale sta portando benefici alle aziende anche relativamente all’integrazione la propria supply chain. È importante aprirsi alla collaborazione con altri partner, anche con modelli di open innovation. Avere processi digitalizzati e integrati permette di scambiare e condividere informazioni in tempi brevissimi o addirittura in tempo reale. In questo contesto, un ruolo molto importante è giocato dai grandi player che devono trainare le PMI all’interno del processo di trasformazione digitale, creando un ecosistema in cui nessuno resta indietro. Ignorare l’importanza delle PMI sarebbe un errore molto grave. Le filiere stanno diventando sempre più strategiche. Dobbiamo chiederci però se saremo capaci di affiancare alle imprese tradizionali realtà che potranno competere in nuovi ambiti di filiera, coinvolgendo anche i fornitori di tecnologie avanzate come accade altrove in Europa.
Come imprenditore, anche lei sta affrontando la grande sfida della digitalizzazione. A che punto è Cosberg in questo percorso? Vi potete considerare una fabbrica intelligente?
Da ormai 40 anni progettiamo e costruiamo impianti customizzati per l’automazione dei processi di assemblaggio, “abiti su misura” integrati con tecnologie avanzate. I valori della nostra azienda sono il know how e il “sapere fare” del nostro capitale umano, e i giovani sono la nostra vera “tecnologia abilitante”. È poi fondamentale capire ciò che ci chiede il mercato, anticipandone le esigenze. La parola chiave è adattarsi e per farlo è necessario avere fabbriche sempre più flessibili e riconfigurabili. Stiamo tornando all’era della personalizzazione. Le aziende vincenti sono quelle capaci di personalizzare e di farlo in tempi rapidi. Devono però essere riadattabili e pronte a rispondere al mercato. Questa è per me una fabbrica intelligente e questo è il futuro del manifatturiero. L’Italia è il Paese che può realizzare tutto ciò, perché ha le piccole imprese, l’inventiva e le maestranze. Per noi la digitalizzazione è uno strumento di innovazione per incrementare l’efficienza di processi e impianti, e per procedere in modo oggettivo nell’analisi di processi o risultati. Prima progettiamo e testiamo i processi, poi li digitalizziamo. Prioritaria è la gestione dei dati, che rappresentano il patrimonio informativo di un’azienda e di un processo decisionale efficace e strutturato. Avere sistemi in cui storicizzare i dati, condividerli, integrarli e renderli accessibili alle diverse aree aziendali permette di ottenere numerosi vantaggi. Registrare i dati permette poi di analizzarli, individuando i trend e comprendendo il mercato. Infine, la condivisione e l’integrazione della conoscenza porta alla riduzione dei tempi e all’eliminazione di sprechi e attività non a valore aggiunto. Stiamo predisponendo un sistema integrato di gestione della conoscenza, dalla codifica all’archiviazione – idee, prototipi, progetti – e di interazione con i clienti da remoto. Inoltre stiamo utilizzando le tecnologie di Industria 4.0 per il monitoraggio e il collaudo, anche da remoto, degli impianti. Non so se ci possiamo definire una Fabbrica Intelligente, di sicuro abbiamo tracciato una strada chiara verso la crescita digitale e del valore della nostra azienda. Del resto innovare significa proprio portare valore e farlo con velocità, sempre in funzione di ciò che chiede il mercato. E fare innovazione digitale significa partire dalle nuove tecnologie per ripensare e semplificare il processo produttivo, ridisegnare i modelli di business, in una logica di apertura al cambiamento.
Condividi l'articolo
Scegli su quale Social Network vuoi condividere