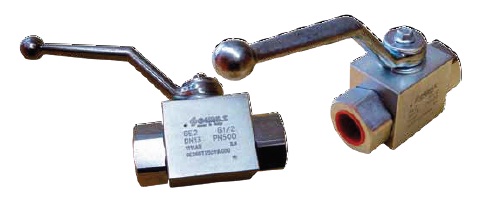
Avvalersi dei giusti mezzi consente di ottenere notevoli risultati: Gemels ha puntato sulla tecnologia Gildemeister per scendere con i costi mantenendo alta la qualità.
Internazionalizzazione, dimensioni aziendali ridotte, concorrenza spietata: sfogliando un giornale, guardando la TV o partecipando a un convegno se ne sentono di ogni genere: nonostante tutto, sono molte le realtà italiane che riescono a competere contemporaneamente sul fronte dei prezzi e della qualità.
Gemels è una azienda a conduzione familiare nata circa quarant’anni fa su intuizione di Angelo Facchinetti: inizialmente attivi come tornitori per conto terzi, ben presto si focalizzano su un proprio prodotto, una valvola per il settore oleodinamico che viene installata ancora oggi sui rimorchi per camion Iveco, Volvo e Mercedes. «Oggi siamo io, mio fratello e mia sorella a proseguire l’attività – conferma Giovanni Facchinetti, figlio del fondatore –, in qualità rispettivamente di responsabili tecnico, commerciale e amministrativa. Siamo cresciuti fino a circa trenta persone, e di conseguenza dal giorno di apertura a oggi sono cambiate molte cose: ai tre torni inizialmente presenti in officina abbiamo affiancato via via altri modelli, alcuni li abbiamo aggiornati e, a fronte della nuova produzione di valvole, abbiamo acquisito anche delle fresatrici e un transfer. Rimanere tecnologicamente aggiornati è sempre stata una costante per noi, che ci ha dato la possibilità di vincere le sfide degli ultimi anni».
Il lavoro non manca in Gemels, ma non è semplice ottenerlo e, soprattutto, mantenerlo. «È il 1994 l’anno che fa da “spartiacque” tra l’attività di terzista e quello di costruttore di valvole – prosegue Facchinetti –. Al primo modello se ne sono affiancati altri, aumentando così la gamma e la tipologia per proporci anche nei settori petrolchimico e oil&gas. Nel frattempo hanno cominciato ad affacciarsi anche altri produttori, in particolare asiatici, che hanno scosso il mercato con prezzi estremamente aggressivi, costringendoci a ripensare i processi produttivi per tornare competitivi». La qualità non era certo paragonabile, ma il mercato accetta di buon grado un livellamento dei prezzi verso il basso, ovviamente mantenendo inalterate le caratteristiche tecnologiche dei prodotti. «Ci siamo trovati nella condizione di dover competere sul fronte dei prezzi e, nel contempo, a mantenere inalterata la qualità. Non solo: la nostra produzione si divide tra diverse macchine, dai torni al transfer, in funzione dei lotti e della richiesta del mercato. Ultimamente, però, ci siamo trovati nella condizione di dover fare un ulteriore passo in avanti: se fino a qualche anno fa un buon prodotto era sufficiente, oggi non possiamo rischiare di vederci rimandato indietro un intero lotto a causa di un singolo pezzo con una bava su un filetto. Questo ha imposto un ulteriore innalzamento della qualità complessiva, che doveva necessariamente andare di pari passo con un prezzo sempre aggressivo e con la massima flessibilità in officina. Paradossalmente, negli anni ‘90 i componenti cadevano in una semplice cassetta di raccolta e, nonostante qualche ammaccatura estetica, venivano accettati senza problemi dal mercato. Oggi questo genere di imperfezione non è accettato, quindi abbiamo equipaggiato le macchine con appositi braccetti o scivoli che guidano il pezzo e lo depositano delicatamente dove necessario, come un contenitore o una lavatrice industriale posta in linea, nella quale viene eliminata ogni traccia di lubrorefrigerante».
Prezzo “cinese”, qualità italiana e flessibilità in officina non sono facili da coniugare, se non con le giuste macchine. La cadenza di un transfer è un dato di fatto, ma con i torni Gildemeister sono riusciti a ottenere una produttività di poco inferiore con una qualità nettamente superiore. Una caratteristica di estrema importanza per Gemels è infatti la ripetibilità: molte macchine sono in grado di raggiungere determinate prestazioni, ma quante possono mantenerle costantemente, pezzo dopo pezzo, dopo mesi o anni di utilizzo? «Avevamo già in officina un tornio Sprint 42 linear della Gildemeister, del quale apprezziamo ancora oggi le qualità, ma abbiamo fatto un ulteriore passo avanti con il tornio automatico Cnc multislitta MSL 42 – spiega Facchinetti –. Per noi è la macchina ideale per diversi motivi: innanzitutto ha un rapporto qualità/prezzo molto favorevole, inoltre il suo costo orario ridotto ben si coniuga con la produzione a volte discontinua delle nostre valvole. Nel 1994 i raccordi richiedevano un tempo ciclo di circa 85 secondi, mentre oggi tecnicamente siamo scesi fino a 45. Un buon compromesso, che prevede ad esempio la ripresa dei filetti per togliere le eventuali bave, ci ha portati a 50 secondi di tempo ciclo. In questo modo abbiamo praticamente dimezzato i tempi, aumentando la finitura e riducendo i costi complessivi».
Condividi l'articolo
Scegli su quale Social Network vuoi condividere