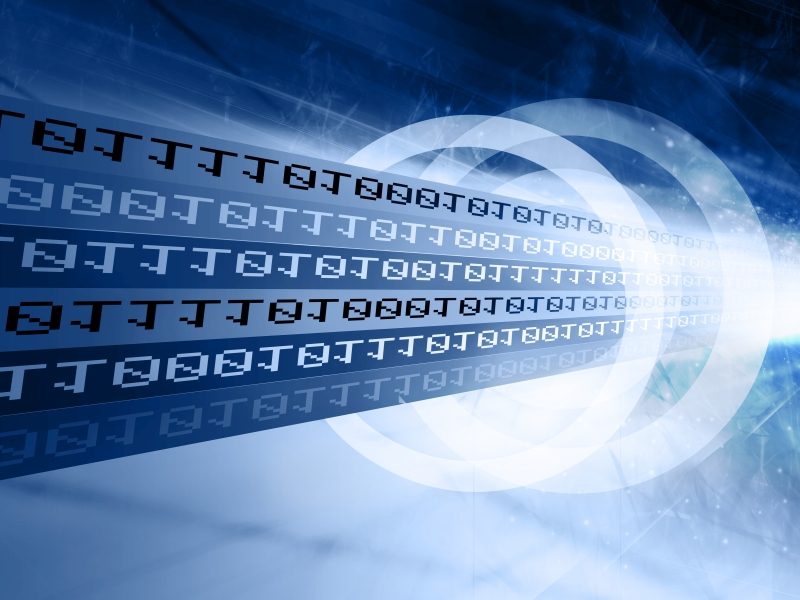
Le tendenze di mercato, le evoluzioni tecnologiche in corso e le esigenze dei clienti, sia utilizzatori sia costruttori di macchine, nelle parole dei costruttori di controlli numerici attivi sul mercato italiano
Per andare in profondità e conoscere l’umore di un settore industriale non c’è scelta migliore che sentire direttamente gli operatori. Visto che parliamo di macchine utensili e di meccanica, uno dei comparti che ha molto da dire e rappresenta una vera e propria cartina al tornasole è quello dei controlli numerici. Dalla sua nascita a oggi il controllo numerico si è evoluto, diventando sempre più una macchina nella macchina acquisendo un ruolo di primo piano nelle prestazioni di una macchina utensile. Nel tempo, il mondo del controllo numerico si è costituito con una serie di grandi aziende presenti in tutto il mondo e società più piccole ma specializzate. In particolare, in Italia la presenza di queste due tipologie di costruttori di controlli numerici è molto forte. Tecnologie Meccaniche li ha incontrati per conoscerne le opinioni sul mercato del CNC in Italia e sull’evoluzione tecnologica. Vediamo insieme quali spunti sono emersi.
Mercato: la ripresa c’è!
La EMO di Milano si è da poco conclusa, offrendo una fotografia del mercato che sta tendendo con chiarezza verso il positivo. Tale valutazione è condivisa anche dai costruttori di controlli numerici. Il primo a esprimerlo ai microfoni di Tecnologie Meccaniche (i numeri di Tecnologie Meccaniche sono leggibili online previa registrazione gratuita ) è Paolo Francese, di Mitsubishi Electric. «Il mercato della macchina utensile è in forte ripresa, come dimostrano i recenti dati e il grande successo dell’ultima edizione di EMO 2015. La produzione per il mercato interno sta finalmente tornando a crescere e gli imprenditori stanno lentamente aumentando il volume degli investimenti. Le aziende escono da un periodo difficile molto ben strutturate, forti e competitive nei confronti della concorrenza. La crisi ha avuto l’effetto di aumentare ancora di più l’eccellenza e l’innovazione introdotta dai costruttori italiani per diversificare la produzione e fare fronte alle sempre più esigenti richieste del mercato. La tendenza è quella di costruire macchine estremamente versatili, in grado di produrre pezzi molto diversi e di passare rapidamente da una produzione all’altra. Questo crea sempre maggiori opportunità per il CNC Mitsubishi Electric che, grazie alla sua flessibilità e alle notevoli possibilità di customizzazione, ben si adatta alle macchine speciali, ove sono richieste lavorazioni non convenzionali e personalizzazioni più spinte per potersi adattare a queste nuove tipologie di macchine utensili». Segnali positivi sono rilevati anche da Andrea Bianchi, di Heidenhain. «Leggiamo cifre con segno positivo e molte officine ci riferiscono di avere ripreso la produzione a pieno ritmo, con commesse interessanti tanto come livello tecnico che in termini economici. Dal nostro osservatorio rileviamo che questa fotografia è veritiera ma purtroppo parziale; infatti, constatiamo come il risveglio sia concentrato in certe aree geografiche o settori e non ancora generalizzato. Ovviamente, questo contesto per chi come Heidenhain fornisce tecnologia e innovazione è ricco di potenzialità. I rilancio del mercato interno passerà attraverso l’ammodernamento delle strutture produttive: si opterà per macchine più performanti, idonee all’attività non presidiata e in grado di operare come sistemi aperti. In questa scelta un elemento determinante sarà rappresentato dal CNC, sempre più elemento chiave della catena di processo. Il controllo numerico per lavorazioni combinate TNC 640 Heidenhain è già ampiamente attrezzato per sostenere questo importante ruolo elaborando i dati, dialogando con la rete e adattandosi alle diverse esigenze delle aziende moderne». Giancarlo Merlini, di Fanuc, evidenzia come tutto il continente europeo, Italia compresa, stia dando ottimi segnali di ripresa. «L’attuale andamento del mercato delle macchine utensili rispecchia abbastanza l’andamento dell’economia mondiale che vede l’area euro in leggera ripresa, mentre aree come Asia e Stati Uniti confermano il trend positivo sebbene, in alcuni casi come la Cina, al di sotto degli scorsi anni. In questa situazione, destinata a perdurare anche nel prossimo anno, colgono le migliori opportunità quei costruttori che hanno saputo affrontare la sfida dei mercati globali e che in alcuni casi arrivano a esportare più del 70% della loro produzione; ovviamente in questo contesto soffrono in maniera particolare quei costruttori che hanno nel mercato interno, in ripresa ma ancora debole, l’unico sbocco commerciale». Dopo un 2014 soddisfacente il trend del 2015 di Fagor Automation, come sottolinea Diego Perego, segue i buoni risultati dell’anno precedente. «Vediamo un incremento delle macchine d’importazione, particolarmente dai mercati asiatici, e la tenuta dell’export dei nostri costruttori. Per quanto riguarda il mercato interno le agevolazioni fiscali del primo semestre 2015 hanno dato impulso al rinnovo dei macchinari, specialmente di piccole/medie dimensioni, a scapito del mondo retrofit. Va però detto che molto c’è ancora da fare, visto che la quantità di macchinari obsoleti attualmente utilizzati dal settore produttivo e manifatturiero italiano è ancora importante. Un fattore determinante al fine di tale scelta (rinnovo di macchinari) è sicuramente il tempo di consegna, dove i grandi dealer che operano sul nostro mercato riescono a soddisfare in maniera molto celere questa esigenza della clientela finale. Per il futuro vediamo un mercato abbastanza stabile, senza particolari scossoni né verso l’alto né verso il basso. Per quanto riguarda le opportunità riteniamo che l’unicità del nostro prodotto dove fattori come velocità, potenza e semplicità sono alla base del successo di Fagor, sarà sempre più un fattore determinante per l’utente finale al fine di scegliere il CNC in maniera oculata e proficua per lui. L’attività di Fagor, oltre a concentrarsi in maniera sempre più decisa nella ricerca e sviluppo, è volta a pubblicizzare agli interlocutori del settore (cliente finale, OEM, dealer, retrofit) quanto di buono svolto finora non solo nel mondo tornio e rettifica, settori di lungo corso, ma particolarmente nel settore fresatura/ alesatura grazie agli ottimi risultati ottenuti dopo l’apertura del centro tecnologico di Ivrea. Per il futuro vediamo quindi opportunità ad ampio raggio che siamo certi di cogliere». Positive anche le valutazioni di Marco Battistotti, della Num. «Dal nostro punto di vista, possiamo confermare che il mercato nei primi tre trimestri del 2015 ha fornito segnali di risveglio, riscontrando un’entrata ordini superiore rispetto allo stesso periodo dello scorso anno. Un dato rilevante, alcuni nostri clienti hanno notato qualche segnale di risveglio sul mercato interno. Siamo costruttori di soluzioni CNC da più di cinquant’anni e offriamo un sistema capace di adattarsi a pressoché tutte le tipologie di macchine di produzione, siamo sicuramente interessati alle nicchie di mercato ma non vogliamo disperdere le nostre energie, buttandoci in mercati troppo differenti da quelli di riferimento». Paolo Trezzi, di Siemens, sottolineando la ripresa del mercato evidenzia che le aziende stanno puntando su innovazione e qualità. «Non possiamo che confermare i primi segnali di ripresa, ma la strada da percorrere per tornare ai livelli dello scorso decennio è ancora lunga e in salita. L’allargamento della platea delle imprese intenzionate ad assumere, l’incremento delle assunzioni dirette e soprattutto il più consistente investimento in profili professionali di livello elevato fanno capire che una parte della nostra industria sta scommettendo sul suo futuro. E lo fa puntando sull’innovazione e sulla qualità, investendo su quelle figure qualificate che possano fare la differenza in un mercato sempre più competitivo e allargato. La nuova legge Sabatini ha senza dubbio aiutato le aziende italiane ed è auspicabile che il provvedimento diventi strutturale, assicurando alle aziende utilizzatrici il giusto incentivo per gli investimenti a elevata tecnologia come le macchine a controllo numerico con o senza robot. Le imprese industriali si trovano ad affrontare profondi cambiamenti nel mondo della produzione per rimanere concorrenziali con il mercato globale. La digitalizzazione offre nuove opportunità per rendere più intelligenti, cioè più efficienti, prodotti e soluzioni». Oggi Fidia, forte di oltre 40 anni di innovazione tecnologica nel settore dei controlli, si trova in una posizione particolare in quanto la produzione di CNC è destinata sia alle macchine di proprio marchio che a quelle di altri costruttori mondiali, come sottolinea Claudio Castagno. «Nell’insieme abbiamo constatato una decisa ripresa della domanda, che fa seguito all’andamento molto positivo concretizzatosi nel 2014 con il fatturato record dell’azienda. Il primo semestre 2015 ha confermato questa tendenza con una redistribuzione della domanda che, a fronte di una flessione della Cina, è stata ampiamente compensata dalle commesse di Germania, Nord America e anche del mercato domestico. In linea di massima, l’anno in corso si presenta con ottime aspettative su tutti i mercati e tale da prevedere ancora un certo incremento sul già ottimo 2014. Per quanto riguarda il mercato italiano, le opportunità sono legate sia al settore automotive sia a quello aeronautico. La necessità di rinnovare un parco macchine piuttosto datato è una delle principali molle della ripresa degli investimenti anche nel settore retrofit, mercato non secondario per i nostri prodotti CN. Quando un cliente deve fare fronte all’aumento di commesse, ma non è ancora in condizione di investire in nuovi macchinari, ha bisogno di una soluzione immediata che apporti un reale beneficio al parco macchine esistente, aumentandone la produttività e l’efficienza. Per i CN di propria marca, Fidia da sempre offre soluzioni di ammodernamento in kit che, senza costosi interventi di ricablaggio e lunghi fermi macchina, permettono ai clienti di sfruttare in modo più intensivo il proprio parco macchine. La versione software V5 con nuovi algoritmi di Look Ahead Dinamica consente di migliorare in modo evidente non solo le prestazioni di macchine nuove, ma di garantire risultati sorprendenti in termini di qualità superficiali e abbattimento dei tempi di lavoro del 30% con punte fino al 50% su particolari lavorazioni a 5 assi, anche su macchine già installate. Per ottenere questi vantaggi su una macchina acquistata in origine con un CN di altra marca, Fidia propone l’applicazione personalizzata dei modelli C19, C20 e C40, mantenendo gli azionamenti originali o fornendo azionamenti digitali Fidia XPower. L’offerta è comprensiva di mano d’opera qualificata, certificazioni, aggiornamento schemi elettrici, garanzia e test di lavorazione prima e dopo l’applicazione per certificare i miglioramenti ottenuti. L’aggiornamento dei CNC installati è quindi un altro degli argomenti vincenti in questa fase di ripresa del mercato. A fronte di un costo contenuto il risultato è immediato e il cliente può subito apprezzare il nuovo livello tecnologico raggiunto da Fidia». Interviene nella discussione Giovanni Apolloni, di Osai, sostenendo anch’esso l’attuale positività del mercato. «Ci sono segnali interessanti nel mercato dei CNC che potrebbero portare a un aumento dei volumi delle macchine utensili prodotte in Italia. In particolare, il rallentamento della Cina e l’apprezzamento del dollaro potrebbero favorire l’export delle macchine utensili sia in USA sia in mercati dell’Europa Centrale e Medio Oriente. Dal punto di vista della vendita dei CNC al di fuori dell’Italia, Osai è convinta che gli USA possano rappresentare di nuovo un mercato in cui si potrebbe avere una crescita significativa». L’importanza dell’esportazione viene evidenziata da Giorgio Rossi, di ECS. «Effettivamente sembra che il mercato stia dando segnali di risveglio, non tanto per quanto riguarda ECS sul mercato italiano ma in modo particolare nel mercato estero, USA e Cina. In Italia qualcosa si sta muovendo, ma è sempre molto traballante: per questo anche ECS come altri costruttori sta puntando al mercato estero, con grandi fatiche nel mettere a disposizione risorse umane ed economiche, ma con ottimi risultati. Ritengo che il futuro sia rivolgersi sempre più a mercati esteri senza comunque tralasciare il “piccolo orticello” domestico». Concludiamo il giro di opinioni con Francesco Dreoni, di D.Electron. «Il settore delle macchine utensili è vasto e molto differenziato, e ogni sua specializzazione può manifestare dinamiche di mercato indipendenti. Ciò che D.Electron vede dal suo punto di osservazione è che il mercato delle macchine utensili sta dando, nel suo insieme, segnali di miglioramento. Osserviamo, per esempio, che per i costruttori di dimensioni maggiori per i quali l’esportazione è una componente fondamentale del proprio mercato il deprezzamento dell’euro sul mercato internazionale è certamente un vantaggio, ma si nota un significativo miglioramento anche del mercato interno italiano, che riesce a dare prospettive anche ai costruttori di dimensioni più piccole. In Italia notiamo, per esempio, un rientro di produzioni a elevato valore aggiunto quali la produzione di stampi di qualità, la meccanica di precisione o il settore degli accessori moda, che trascinano la richiesta di macchine utensili adatte alle esigenze dei clienti. Un fattore importante, che stiamo notando, è che i costruttori di macchinari in settori limitrofi alle macchine per asportazione truciolo ad alte prestazioni, quali per esempi i settori per lavorazione di lapidei o il settore della modelleria, hanno la necessità tecnica di fare crescere le prestazioni dei propri macchinari per potere restare competitivi sul mercato. Per questi motivi, crediamo che nel breve o medio periodo ci sarà un leggero aumento dei numeri complessivi di CNC venduti in Italia, ma un sensibile aumento del valore aggiunto del singolo CNC. Per quanto riguarda D.Electron, vediamo questa prospettiva come una buona opportunità di crescita, in quanto la vicinanza che possiamo offrire ai costruttori e la possibilità di specializzare e arricchire il nostro CNC in base alle richieste dei nostri clienti rappresenta un valore aggiunto su cui basare i nostri prodotti».
Tecnologia: sempre più innovazione
Come si è notato, il mercato è in ripresa. Ciò porta le aziende a investire e l’innovazione tecnologica diventa quindi un fattore discriminante. Il mercato infatti chiede sempre più innovazione, come sottolinea Andrea Bianchi della Heidenhain. «Gli OEM ci chiedono di essere promotori di innovazione, sviluppatori di tecnologia in grado di anticipare le esigenze del mercato e partner di progetti lungimiranti. Tutto questo è congeniale a Heidenhain, che da sempre è un pioniere in ambito tecnico. I finali, invece, cercano in Heidenhain anche il consulente che li affianchi nel loro operato per studiare insieme le soluzioni più adatte all’officina. Anche questo è nel dna di Heidenhain, che ha fatto dell’attenzione al cliente uno dei suoi punti di forza. I nostri clienti sanno di potere contare sull’elevata qualità e sulla comprovata affidabilità dei nostri prodotti e su un servizio pre e post vendita puntuale e professionale in linea con gli standard stabiliti dalla Casa madre. Tanto gli OEM quanto i finali chiedono che la nostra tecnologia di controllo supporti l’operatore con funzioni software all’avanguardia, che contribuiscano a rendere il più possibile efficace e sicuro il processo di lavorazione. Tra queste è da annoverare AFC (Adaptive Feed Control) che garantisce ridotti tempi di lavorazione, minore carico per la macchina e nel complesso maggiore sicurezza di processo. Inoltre, Heidenhain continua a puntare sul tema “accuratezza”: grazie all’impiego di sistemi di misura lineari e angolari che funzionano in Closed Loop è possibile eliminare completamente errori determinati da condizioni termiche differenti e ottenere elevata precisione dei componenti realizzati persino in condizioni di impiego variabili». Giancarlo Merlini, di Fanuc, evidenzia come i costruttori di macchine utensili italiani puntino sempre più sulla complessità delle macchine e sulla customizzazione e quindi anche il CNC deve rispondere a questa tendenza. «In Italia il mercato dei CNC si è sensibilmente modificato negli ultimi anni, dovendo seguire le esigenze dei costruttori la cui produzione si è evoluta verso macchine sempre più complesse, flessibili e performanti. Tale tendenza sarà sicuramente confermata nel breve e medio periodo, in quanto per vincere le sfide in un panorama internazionale i costruttori italiani dovranno sempre più “customizzare” le loro macchine in funzione di una clientela sempre più esigente. Il rischio principale è che i costruttori italiani non riescano a generare quella massa critica di produzione che permetta loro di abbattere i costi ed essere competitivi. L’inventiva e la capacità dei costruttori italiani di assecondare le richieste degli utilizzatori più esigenti rappresentano sicuramente qualità che li contraddistinguono nel panorama dei costruttori di macchine utensili mondiali e che li mette in grado di cogliere le opportunità più importanti e con il più alto valore aggiunto. Gli utilizzatori dei CNC richiedono prodotti sempre più potenti e flessibili, facili da programmare e in grado di effettuare operazioni combinate di tornitura/ fresatura, funzionalità 5-assi eccetera. I CNC Fanuc della serie 30i-B sono in grado di soddisfare appieno anche le esigenze di lavorazione più complesse, integrando altresì funzioni per la sicurezza dell’operatore come la Dual check Safety (DCS) e per la prevenzione delle collisioni macchina come la Built-in 3-D Interference Check Function. Lo sforzo di Fanuc è volto allo sviluppo di prodotti che consentano all’utilizzatore di sfruttare al meglio tutte le funzionalità a disposizione nel modo più facile e immediato. La strategia tecnologica di Fanuc è di essere “Technology driven”, che in pratica si traduce nel fatto che Fanuc concentra notevoli investimenti in ricerca e sviluppo nelle tecnologie più avanzate che ritiene più adatte a essere implementate sulle macchine utensili». Sulla stessa lunghezza d’onda Paolo Francese, della Mitsubishi Electric. «La macchina utensile deve oggi essere in grado di coprire svariate necessità produttive in modo efficiente, rapido e affidabile. Di contro, macchine sempre più complesse e performanti richiedono una sempre maggiore semplicità d’utilizzo e un’interfaccia chiara e intuitiva. Mitsubishi Electric risponde a queste e altre crescenti richieste con una nuova generazione di CNC, l’ottava serie prodotta nello stabilimento giapponese di Nagoya. La nuova generazione garantisce maggiore produttività, grazie anche a una CPU superveloce realizzata da Mitsubishi Electric specificamente per il CNC. È stata inoltre migliorata l’affidabilità diminuendo i componenti e aumentando la resistenza ambientale degli stessi. A tutto questo si abbina un avanzamento significativo dell’usabilità grazie a schermi touch (anch’essi prodotti da Mitsubishi Electric) e a semplici e intuitive pagine video facilmente personalizzabili e modificabili secondo le esigenze o le preferenze del costruttore o dell’utilizzatore. Queste e altre soluzioni tecnologiche di Mitsubishi Electric permettono di realizzare macchine finora impensabili, per meglio adattarsi alle nuove necessità e ai rapidi cambiamenti tecnologici degli ultimi anni». Anche Claudio Castagno, di Fidia, conferma che «il costruttore di macchine deve sostanzialmente interpretare le esigenze dell’utilizzatore finale e poi riuscire a esaudirle offrendo, se possibile e se l’utilizzatore non ha già indicato una preferenza, il CNC che meglio soddisfa tali requisiti. Quindi, l’esigenza dell’utilizzatore e quella del costruttore possono anche divergere nella ricerca della soluzione quando il costo diventa un argomento determinante (per esempio sulle macchine più piccole), o quando l’esigenza dell’utilizzatore è di livello medio/basso (lavorazioni generiche o con poco valore aggiunto). Fidia si rivolge agli utilizzatori più esigenti e più attenti alla valutazione complessiva del CNC, che non è soltanto l’apparecchiatura in sé. Fidia opera in stretta collaborazione con utilizzatori, costruttori, enti di ricerca per elaborare e proporre nuove soluzioni nell’ambito delle lavorazioni per asportazione. La recente realizzazione della funzione Look-Ahead V5 (LA V5) è un esempio di sviluppo destinato ad avere un impatto diretto sull’utilizzatore finale. Altrettanto vale per il software Fidia ViMill® dedicato alla sicurezza operativa a bordo macchina per la prevenzione di urti e collisioni: un sistema esclusivo, indispensabile per salvaguardare la macchina e il pezzo in lavorazione. Senza dimenticare il dispositivo HMS (brevettato) per la calibrazione di teste e tavole, uno strumento che si sta rivelando indispensabile per potere garantire le precisioni richieste dai committenti. Per Fidia, quindi, è di estrema importanza il contatto diretto con l’utilizzatore finale al fine di interpretarne al meglio le esigenze. Un gruppo di persone con forti motivazioni, elevata professionalità e grande predisposizione all’attività diretta sul campo costituisce uno degli elementi fondamentali del modo di operare di Fidia». Paolo Trezzi, di Siemens, intervenendo nella discussione evidenzia che «ciò che noi viviamo attualmente è un’integrazione sempre più importante dei processi di sviluppo dei prodotti e i processi produttivi attraverso innovativi sistemi software e hardware potenti. Contestualmente si fondono i mondi produttivi virtuali e reali. Ciò rappresenta un momento centrale sulla via di una nuova era industriale. Già ora i costruttori di macchine utensili e le aziende manifatturiere possono sfruttare le opportunità offerte dalla digitalizzazione, migliorando notevolmente la propria competitività attraverso prodotti e soluzioni integrate. Del resto, oggi devono introdurre sul mercato prodotti sempre più complessi, nell’ambito di cicli di innovazione sempre più brevi. Tutto ciò comporta anche la necessità di gestire volumi sempre più consistenti di dati. Inoltre, le aspettative in termini di produttività sono cresciute enormemente dato che i clienti, che devono confrontarsi con mercati assai volatili, puntano sempre più su una produzione di serie personalizzata piuttosto che su prodotti di massa indistinti. E, naturalmente, in un mercato competitivo gioca un ruolo importante anche un utilizzo consapevole di energia e risorse. La digitalizzazione della produzione ridurrà i tempi di introduzione dei prodotti sul mercato, aumenterà la flessibilità e migliorerà l’efficienza. La Suite Software di Siemens, Digital Enterprise, soddisfa quasi tutti i requisiti di tutta la catena di creazione del valore, dal design ed engineering del prodotto alla produzione fino al servizio di assistenza. Con la digitalizzazione si realizza un progressivo concatenamento di processi e applicazioni tra mondo virtuale e reale, sia a livello orizzontale che verticale. Le aziende di produzione di grandi dimensioni e orientate al processo tendono a collegare in rete ogni loro infrastruttura produttiva. Con Sinumerik Integrate for Production, offriamo a queste aziende soluzioni per interconnettere le macchine e collegarle ai sistemi IT di livello superiore. Per favorire l’integrazione orizzontale fra diverse macchine utensili in un determinato ambiente di produzione, Sinumerik Integrate for Production permette di condividere in rete le risorse, gestendo i dati di produzione a livello centrale. Il software gira direttamente sul CNC, registra sia i dati relativi ai programmi e agli utensili utilizzati sia i valori di efficienza operativa OEE, mettendoli a disposizione per successive analisi e ottimizzazioni. Le nuove funzioni si possono installare facilmente su un server. Oltre all’interconnessione via rete delle macchine utensili anche l’integrazione verticale, ovvero il collegamento verso sistemi di livello superiore, riveste un’importanza altrettanto fondamentale. Sinumerik Integrate for Production si può integrare facilmente e rapidamente in sistemi di livello superiore come Teamcenter. Ciò permette di rendere fruibili a livello d’impresa i dati relativi agli ordini e di sapere in quale sede di produzione dell’azienda devono essere prodotti determinati ordini. Inoltre, è possibile tenere sotto controllo e coordinare in modo efficiente le scorte di materiale, i processi logistici e la disponibilità degli utensili. Nell’innovazione tecnologica siamo all’avanguardia. E con Sinumerik 840D sl disponiamo anche del giusto sistema CNC. Molto importante per Siemens è anche la produzione additiva, oggi in rapida crescita. Sinumerik 840D sl offre ai produttori meccanici un sistema di controllo efficiente, con il quale possono realizzare macchine utensili per processi produttivi additivi, mentre NX Hybrid Additive Manufacturing offre un ambiente per la programmazione delle varie fasi di produzione, compresa la simulazione delle operazioni di apporto e asporto del materiale. A livello internazionale, Siemens è l’unico fornitore di soluzioni hardware e software integrate, che rappresentano il presupposto per un’efficiente produzione di pezzi con tecnologie additive e sottrattive. Siemens offre al mondo della fabbrica digitale soluzioni continue, dalla macchina utensile fino al livello di guida aziendale». Come costruttore di sistemi a controllo numerico NUM nota, come afferma Marco Battistotti, che ogni settore ha delle sue specificità. «In alcuni settori gli interlocutori principali sono gli utilizzatori finali, in altri settori i costruttori di macchine. Alcuni esempi, nel settore della rettifica degli utensili dove Num ha una esperienza quasi trentennale e propone un’offerta completa che va dal CAD/CAD NUMroto fino al servomotore, gli interlocutori principali sono gli utilizzatori, grosse multinazionali che mirano a una maggiore produttività, affidabilità, semplicità d’uso della macchina e integrazione della macchina stessa nel sistema ERP aziendale (Industry 4.0, MTconnect, OPC server UA). Inoltre NUMroto, sotto la spinta degli utilizzatori, evolve continuamente integrando funzionalità che permettono di rettificare e manutenere punte e frese con geometrie sempre più complesse, come per esempio quelle multielicoidali utilizzate in ambito aeronautico per la lavorazione di leghe speciali e materiali compositi. Questo continuo sviluppo, trascinato dagli utilizzatori, ha reso NUMroto una delle soluzioni/sistemi complete migliori e più versatili sul mercato. In molti altri settori, invece, l’interlocutore principale è il costruttore che mira a costruire macchine sempre più precise, versatili, complesse, competitive e sicure. Num sviluppa i propri prodotti per andare incontro a tutte queste esigenze. Macchine più precise grazie alla funzione HSC (High Speed Cutting) che permette di eliminare l’errore di inseguimento, grazie all’interpolazione eseguita con risoluzione sub-nanometrica, le funzioni VEComp (Volumetric Error Compensation) permettono di aumentare la precisione volumetrica del TCP (Tool Center Point); inoltre, azionamenti estremamente performanti con interpolazione eseguita a 100 microsecondi e tempi di campionamenti che arrivano 25 microsecondi completano il sistema. Con il sistema CNC Flexium+, il costruttore di macchine ha la possibilità di interagire in real time sia con il controllo numerico (Dynamic Operators) sia con l’azionamento (Drive Embedded Macro) per creare funzionalità uniche e proprietarie, l’interfaccia uomo-macchina (HMI) è liberamente personalizzabile con varie tecnologie, e inoltre per la completa integrazione della macchina nel sistema di gestione aziendale grazie a OPC-UA server e/o MTConnect® il CNC è in grado di interagire con i più comuni sistemi ERP/PLM. La complessità delle macchine continua ad aumentare? il sistema CNC Flexium+ è quindi l’alleato ideale; Flexium+ può gestire fino a oltre 40 processi in parallelo e 200 assi/ mandrini; tali processi possono essere sia di tornitura che di fresatura, possiede un unico PLC che supervisiona l’intero sistema, l’ambiente di sviluppo è integrato, moderno e dotato dei più moderni sistemi di ottimizzazione (analisi frequenziale, ballbar, PLC state analyser eccetera). Precisione, flessibilità, complessità sono spesso sinonimo di costoso. Il sistema Flexium+ è scalabile, può essere adattato ai bisogni del cliente per raggiungere il migliore compromesso prezzo/prestazioni. Azionamenti biasse molto compatti ed efficienti permettono di realizzare armadi più piccoli e più economici, i motori a cavo singolo eliminano completamente il cavo encoder con ovvi benefici di costi/complessità. La sicurezza funzionale è ormai comunemente utilizzata dai costruttori di macchine, e Flexium+ integra tutte le funzioni necessarie per la gestione della logica di sicurezza (NUMSafe PLC) e di tutti i monitoraggi sicuri del moto (SOS, SS1, SS2, SLS, SLP, STO, SDM). Un unico sistema di sviluppo permette di programmare e debugare il safe PLC, il PLC “standard”, di configurare il controllo numerico, di parametrizzare gli azionamenti e ottimizzare l’intero sistema». Dal punto di osservazione di D.Electron, come afferma Francesco Dreoni, le richieste specifiche da parte dei costruttori di macchine possono essere brevemente riassunte come grande flessibilità di impianto e grande semplicità. «La grande flessibilità è necessaria per fare fronte a macchine combinate o a elevate prestazioni, che possano eseguire più tipologie di lavorazioni con un solo piazzamento, mentre la grande semplicità di installazione, di eventuale riconfigurazione e manutenzione è una necessità che nasce proprio dalla maggiore complessità delle macchine e degli impianti. In quest’ottica, poter offrire un sistema di CNC e drives digitali integrato è fondamentale, perché solo così è possibile garantire l’affidabilità del sistema, da intendersi sia come affidabilità dell’hardware sia come affidabilità del software che lo completa. Da questo punto di vista D.Electron punta sia al miglioramento continuo del proprio sistema di drives digitali integrato col CNC ma soprattutto punta anche alla semplicità di gestione dell’impianto e alla semplificazione della messa in servizio. In quest’ottica, per esempio, D.Electron ha sviluppato sistemi di autotaratura degli azionamenti e sistemi di autoconfigurazione dell’hardware che permettono all’unità centrale del CNC di configurare e aggiornare il software delle periferiche, senza che sia necessaria alcuna programmazione diretta. La richiesta di semplicità riguarda anche gli utilizzatori finali, per i quali il tempo di apprendimento per l’uso e la programmazione della macchina è un costo che è necessario minimizzare: per questo motivo stiamo puntando a sistemi di programmazione e simulazione semplici e interattivi, che minimizzino sia il tempo a bordo macchina sia il tempo necessario all’apprendimento. Ne è un esempio il volantino palmare touch screen di D.Electron, che dà all’operatore una semplicità di manovra nelle operazioni di centraggio a bordo macchina difficilmente ottenibile con altri strumenti. Per quanto riguarda le richieste tecnologiche più innovative, legate alle lavorazioni da effettuare, le richieste dei costruttori e degli utilizzatori finali sono spesso sovrapposte e non facilmente distinguibili. Ciò che riscontriamo è la richiesta di macchine sempre più intelligenti. La tecnologia di alta velocità e lavorazioni 5 assi, che richiede un miglioramento e una dedizione continui, si è infatti diffusa su una grande quantità di macchine ed è difficile considerarla una frontiera dell’innovazione. Esiste invece una spinta all’evoluzione verso macchine che si adattano automaticamente alle condizioni tramite variazioni adattative dei parametri tecnologici della macchina in funzione delle condizioni dinamiche di lavoro. Questo settore di sviluppo è decisamente vasto e riguarda molti aspetti: algoritmi automatici per l’adattamento delle condizioni di taglio in funzione dello sforzo mandrino, algoritmi per lo smorzamento attivo del chatter, ovvero delle vibrazioni di macchina introdotte dal processo di taglio, sistemi di autotaratura e autoadattamento delle maglie di regolazione, sistemi di monitoraggio e minimizzazione del consumo energetico della macchina… tutte queste innovazioni rendono sempre più integrati il CNC e la macchina utensile, con l’obiettivo di rendere le macchine sempre meno dipendenti da tecnici esperti di installazione o da operatori di macchina esperti e sempre più macchine intelligenti in grado di modificare il proprio comportamento in funzione delle condizioni di lavoro». Per Giovanni Apolloni, della Osai, il cliente richiede al CNC maggiore semplificazione. «Il mercato cui si rivolge Osai è essenzialmente quello dei costruttori di macchine utensili in tutto il mondo. Stiamo assistendo non più a una richiesta di aumento di prestazioni, anche perché ormai i CNC moderni dispongono delle tecnologie più avanzate, bensì a una richiesta di semplificazione sia dell’uso del CNC stesso sia soprattutto dell’applicazione. I nostri clienti non hanno più molto tempo a disposizione da dedicare allo sviluppo del PLC integrato e alle personalizzazioni dell’interfaccia uomo-macchina e preferiscono avere sistemi precablati e configurabili, dedicando quindi un tempo minimo alla messa in servizio». Secondo Giorgio Rossi, di ECS, la maggiore richiesta dei costruttori di macchine è nelle personalizzazioni. «Per quanto riguarda il costruttore questo chiede sempre più spesso la possibilità di personalizzare a suo piacimento l’interfaccia del CNC: questo con CNC ECS è possibile in modo semplicissimo, grazie a un software chiamato RB900 sviluppato interamente da ECS e messo a disposizione dei suoi clienti gratuitamente. Inoltre, monitor sempre più grandi: infatti, in EMO abbiamo presentato il nuovo CNC 901S con nuovo hardware monitor 19 pollici e nuova interfaccia, questa completamente sviluppata con il sistema RB900. Per quanto riguarda gli utilizzatori, oltre a fornire loro oggetti sempre più performanti e sempre più affidabili, cerchiamo di fornire loro una interfaccia sempre più semplice nell’utilizzo, per rendere l’operatore della macchina sempre più autonomo nel programmare pezzi a bordo macchina e non solo un operatore che è in grado di premere un pulsante di Start». Concludiamo con le valutazioni di Diego Perego, della Fagor Automation. «Fagor Automation è da sempre un marchio conosciuto e apprezzato, in Italia e nel mondo, soprattutto nel settore della tornitura. A partire dal 2011 è stato intrapreso un progetto di sviluppo di prodotto e prestazioni focalizzato al mercato della fresatura; per l’implementazione di questo “progetto Fresa” è stato aperto, proprio in Italia a Ivrea (TO), un Centro Tecnologico di Ricerca e Sviluppo con gli obiettivi di raccogliere e rielaborare la domanda di nuove prestazioni che nascono dalla clientela, sviluppare in modo autonomo una parte di queste prestazioni (tutte quelle più direttamente legate al settore fresatura) e coordinare gli sviluppi con la casa madre spagnola per quel che riguarda le prestazioni più generiche. Enfatizzando una tendenza che già prima era utilizzata da Fagor, lo sviluppo di nuove prestazioni risponde proprio alle esigenze che ci arrivano da un lato dal costruttore di macchine, e dall’altro dal cliente finale. Iniziando dal cliente finale, abbiamo osservato che le prestazioni richieste sono orientate a una programmazione sempre più semplice ma al tempo stesso potente. Nella tecnologia di fresatura si presentano spesso situazioni in cui la programmazione diventa il terreno in cui si può guadagnare un vantaggio tecnologico importante. Per questo motivo, nei nuovi CNC serie 8065/8060 è stato inventato e implementato il linguaggio di programmazione ProGTL3. Si tratta di un’evoluzione ampliata e arricchita del linguaggio geometrico GTL di Olivetti CNC e Proget2 utilizzato in passato sui CNC Selca. Questo linguaggio permette di descrivere dei profili anche complessi, a bordo macchina, senza l’ausilio di calcolatrice o trigonometria, ma semplicemente utilizzando gli strumenti del disegno tecnico con 5 semplici codici G (G810, G811, G813, G820, G821) e visualizzando in contemporanea il profilo generato mentre lo si sta editando. Ma anche il costruttore di macchine è per Fagor un importantissimo interlocutore. Le sue esigenze sono quelle di realizzare macchine sempre più evolute, con prestazioni sempre più spinte e possibilmente in tempi più rapidi. In questo campo, l’ultima novità sono i cicli di autocalibrazione delle cinematiche di teste e tavole. Si tratta di cicli completamente automatici che, su macchine a 4 o 5 assi, effettuano una serie di misure muovendo gli assi di testa o tavola per rilevare una serie di punti con un tastatore di misura; i punti sono poi elaborati dal CNC, che calcola i valori della cinematica (lunghezze e disassamenti) utilizzando metodi statistici che permettono poi la lavorazione con la funzione RTCP con errori ridotti al minimo. Per il costruttore si tratta di un doppio vantaggio: la rilevazione è molto veloce (pochi minuti, rispetto ad alcune ore necessarie con metodi tradizionali), e una precisione di calibrazione assicurata (nessun rischio di errore umano). Riassumendo, quindi, Fagor Automation sia in Italia sia nel mondo sta puntando molto sul settore della fresatura, con una crescita di prodotto che colloca i suoi CNC tra le scelte obbligate per clienti e costruttori attenti alle prestazioni, alla programmazione, alla facilità di utilizzo, alla velocità e alla precisione di lavorazione».
Condividi l'articolo
Scegli su quale Social Network vuoi condividere