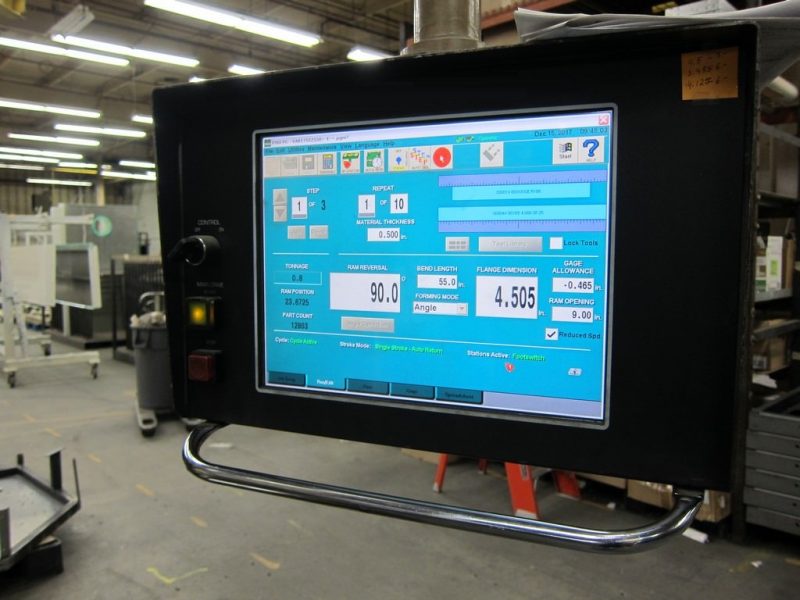
Personalizzazione, rendimento energetico, facile Integrazione nel processo produttivo. Questi i principali temi che guidano l’innovazione tecnologica nel settore delle presse.
di Davide Davò
Quello che stiamo attraversando è un periodo decisamente positivo per il settore della lavorazione della lamiera sotto molteplici aspetti: c’è un importante ritorno agli investimenti, le macchine diventano sempre più efficienti e performanti grazie all’introduzione di una serie di tecnologie che le rendono ancora più performanti e affidabili, e il cambiamento che l’Industria 4.0 sta portando con sé spinge verso l’adozione di nuovi strumenti da integrare tanto nel sistema produttivo in generale quanto a bordo macchina. Per capire in che direzione si stanno muovendo i costruttori di presse in termini di sviluppo tecnologico dei prodotti e di soluzioni in chiave 4.0, la rivista TecnoLamiera ha realizzato quest’inchiesta raccogliendo le voci di alcuni dei principali attori di questo settore.
Visione d’insieme
A rompere il ghiaccio è Lorenzo Galli di I.M.V. Presse, che sottolinea l’importanza di non focalizzarsi su un singolo elemento cercando piuttosto di avere una visione d’insieme del progetto in costruzione. «I.M.V. Presse articola la ricerca e il progresso tecnologico delle proprie macchine verso diversi ambiti. Non sono solamente un certo tipo di cinematismo o l’applicazione di tecnologia specifica a incrementare la qualità e le prestazioni delle nostre presse, bensì la visione d’insieme. Per fare la differenza si lavora con un continuo sviluppo sui propri cinematismi e sulle caratteristiche strutturali, e allo stesso tempo si stringono rapporti sempre più stretti con i fornitori per applicare al meglio le continue novità e il progresso della componentistica e degli accessori, che se ben integrati e sfruttati al meglio generano prestazioni, affidabilità e semplicità d’uso: gli aspetti più richiesti dal mondo produttivo odierno».
L’importanza di curare tutti gli aspetti della progettazione e la loro corretta interazione viene ribadita da Andrea Nava di F.lli Nava. «Da sempre i punti di forza delle nostre presse oleodinamiche si distribuiscono su più piani: per iniziare dai fondamentali, la parte strutturale con un dimensionamento conservativo che assicuri la massima rigidezza sotto carico e il modo ottimale di funzionamento degli stampi, per la qualità dei pezzi stampati e la migliore durata delle attrezzature. La parte di azionamento oleodinamico è segnatamente un altro dei punti di forza delle nostre presse, particolarmente curata e realizzata con know how interno, per investire sulla qualità e lo sviluppo costante del prodotto e di soluzioni sempre innovative. Così come la parte elettrica e software, per scelta sviluppata con competenze interne all’azienda per avere un controllo ottimale dello sviluppo delle presse di nostra produzione. Con un’attenzione così focalizzata sulla progettazione e sulla ricerca costante di nuovi sviluppi è possibile per noi soddisfare e a volte anche anticipare le esigenze dei clienti utilizzatori, mantenendo così una posizione di primo piano nel panorama dei costruttori di presse».
Sulla stessa linea anche Michele Muffato di Muffato Presse, che sottolinea la necessità di studiare con attenzione ogni aspetto delle macchine, software compreso. «Nello sviluppo dedichiamo grande attenzione alla trasformazione del moto rotativo in alternato, dall’albero eccentrico al martello, attraverso l’esclusiva tecnologia a pattino che riduce le spinte di secondo ordine caratteristiche delle bielle, offrendo una grande superficie di contatto sempre perfettamente parallela al piano di lavoro e alla mazza. Una serie di soluzioni tecnologiche e strutturali consente il sollevamento della parte superiore del corpo attraverso cilindri idraulici ad alta pressione, così da provvedere allo sbloccaggio di emergenza o alla normale manutenzione dello stampo senza perdere la posizione di lavoro garantita da una battuta meccanica regolabile in modo centesimale. L’intera struttura, gli accessori e i carter sono stati costruiti oltre che per garantire alta qualità delle lavorazioni e durata nel tempo, anche per consentire agli operatori di lavorare in modo rapido e agevole sui quattro lati della pressa tenendo anche conto dei basilari principi di ergonomia umana. Il software che gestisce l’intera macchina raccoglie ed elabora le informazioni che arrivano da ogni tipo di sensore presente: velocità, corsa mazza, potenza assorbita, tonnellaggio utilizzato, temperature, intasamento filtri. Lo stesso software è inoltre in grado di gestire la teleassistenza, l’invio di messaggi ordinari, di avaria, di manutenzione programmata, preventiva e salvare la memoria di setting desiderati dagli operatori».
Efficienza energetica
Quando tutti i sistemi funzionano e interagiscono nel modo corretto, ne beneficiano tanto le prestazioni quanto l’efficienza dell’impianto. Proprio l’efficienza, e in particolare l’aspetto del consumo energetico, viene messa al centro dell’attenzione da Valerio Ferraro di Omera. «Nei processi di stampaggio dove sono richiesti carichi elevati l‘energia utilizzata è molta, pertanto l’impatto ambientale è diventato un argomento importante. Cogliendo questa esigenza, la gamma di presse idrauliche e meccaniche Omera è stata sviluppata con una tecnologia capace di adattarsi al processo riducendo l’assorbimento energetico. Relativamente agli aspetti strutturali, le macchine puntano sulla rigidità, caratteristica fondamentale per l’ottenimento di prodotti di qualità. Per l’affidabilità della struttura abbiamo introdotto il trattamento delle strutture saldate (After Welding Treatment) in alternativa alla distensione termica (Stress Released). L’analisi è stata condotta con il Dipartimento di Ingegneria di Padova con incrementi dei coefficienti di sicurezza nelle saldature del 30%. Anche nell’analisi della deformazione elastica, grazie agli elementi finiti, abbiamo sviluppato routine di calcolo basate su tecniche di Design Of Experiment (DOE) valutando oggettivamente tutti i parametri di progetto».
In linea con la necessità crescente di massimizzare l’efficienza energetica è anche Stefano Rivellini di NRCM. «NRCM è un’azienda relativamente giovane nel panorama nazionale e internazionale per la produzione di presse oleodinamiche in diversi settori merceologici quali lamiera, SMC, PTFE e ceramica. Produciamo presse speciali con tonnellaggio fino a 50.000 kN, studiate per soddisfare le specifiche richieste del cliente; al suo interno operano tecnici qualificati con oltre 40 anni di esperienza nel settore. NRCM è fortemente motivata nella ricerca di nuove applicazioni, in particolare sta seguendo un programma di Energy Saving studiando e realizzando delle servopresse con sistemi idraulici ad alta efficienza energetica che permettono all’utilizzatore finale, nel suo ciclo produttivo, di abbattere il consumo energetico dal 25 al 50% rispetto a un sistema oleodinamico tradizionale e consente inoltre un notevole abbattimento del rumore, ottenendo accelerazioni e velocità migliori. Il sistema Energy Saving elimina quasi completamente il surriscaldamento dell’olio idraulico e quindi riduce il deterioramento dello stesso, oltre a risparmiare l’energia per l’abbattimento del calore».
Evoluzione delle servopresse
Carlo Ridolfi di Cavenaghi & Ridolfi prosegue sulla linea dell’efficienza energetica. «Costruire presse oleodinamiche dal 1922 significa attenzione alle specifiche esigenze del cliente e per questo essere sempre all’avanguardia nelle tecnologie di produzione e di controllo. La nostra attenzione è sempre più focalizzata al risparmio energetico, ai sistemi fluidici di controllo di ultima generazione, alla flessibilità e alla manutenzione predittiva. Siamo in una fase avanzata di progettazione di presse alternative alle presse oleodinamiche tradizionali. Parliamo di servopresse idrauliche attualmente realizzate fino a 6.300 kN e servopresse elettriche attualmente realizzabili in taglie medio-piccole, ma di cui prevediamo un futuro applicativo sempre più esteso grazie all’elevato risparmio energetico e al minimo impatto ambientale, permettendo di ridurre i costi operativi e le emissioni di anidride carbonica globale in conformità alle normative (direttiva CE N 640/2009)».
Il crescente interesse del mercato nei confronti delle servopresse è confermato dalle parole di Yarno Riva di Zani. «Il principale punto di forza della nostra azienda è senz’altro il know how organizzativo e progettuale. Zani infatti è in grado di rispondere con dinamismo e adattabilità alle nuove esigenze di mercato, e seguendo le richieste e le esigenze dei nostri clienti abbiamo sviluppato nuove soluzioni sia a livello del cinematismo che delle verifiche strutturali oltre che a tutta la parte di supervisione e controllo pressa. Tra le nostre famiglie di prodotto la pressa servo, la quale offre la più ampia flessibilità possibile unitamente a performance produttive di alto livello, è quella che in questi anni si sta maggiormente evolvendo. Nuove taglie di motori sempre più potenti sono ora disponibili in concomitanza con la parte di gestione e calcolo delle curve di moto che ottimizza al meglio i valori impostabili liberamente dal cliente. A livello software abbiamo sviluppato controlli dedicati con ulteriore sensoristica a bordo per verificare qualsiasi anomalia a livello di coppie trasmissibili e carichi sbilanciati. Infine le dimensioni delle macchine prodotte stanno aumentando sempre di più, infatti lo scorso anno abbiamo completato l’avviamento della pressa più grande mai prodotta nella storia di Zani: una 3.200 t servo con un piano da ben 7 m».
Maggior vantaggio competitivo
Altra voce a sottolineare il trend di mercato legato alla tecnologia servo è quella di Michele Archenti di Aida. «Dal punto di vista tecnologico, il fiore all’occhiello di AIDA è certamente la padronanza della tecnologia servo. Grazie all’esperienza accumulata e al continuo sviluppo interno del proprio pacchetto servo, dalla concezione alla produzione e alla programmazione, mantiene una posizione di primo piano nel comparto delle presse. Aida è stata tra le prime aziende a riconoscere e sfruttare le potenzialità della tecnologia servo applicata alle presse, sviluppando e producendo i propri servomotori e vendendo oltre 1200 unità dalla fine dagli anni 90. Le presse Aida DSF (Direct Servo Former) rappresentano un innovativo sistema per lo stampaggio della lamiera e attirano sempre più clienti italiani che mirano a incrementare la loro produttività e il proprio vantaggio competitivo. A questo punto di forza tecnologico si somma lo standard qualitativo dei prodotti Aida, le cui presse sono progettate e sviluppate interamente all’interno dell’azienda al fine di garantire il rispetto di stringenti livelli qualitativi, sia di prodotto che di processo, lungo l’intero ciclo produttivo. Fiore all’occhiello di ogni stabilimento Aida nel mondo il reparto di carpenteria dello stabilimento di Pavone Mella, dotato delle ultime tecnologie nel campo della saldatura, realizza testate, slitte, basamenti e cinematismi e può vantare una capacità produttiva di oltre 240 t al mese».
La crescente attenzione del settore nei confronti delle servopresse è ribadita da Giacomo Pavesi di Balconi. «Balconi ha sviluppato soluzioni estremamente personalizzate e tecnologiche per rispondere alle specifiche richieste dei clienti. Oltre al tradizionale sistema “Plunger” per la guida di precisione della slitta sono state introdotte guide slitta di tipo idrostatico, senza contatto fisico tra le parti in scorrimento. La servopressa si è imposta in tutte quelle soluzioni dove la flessibilità è la condizione principale richiesta dal cliente. Particolare attenzione è stata riservata all’implementazione di soluzioni tecnologiche atte a non generare fluttuazioni sulla rete elettrica del cliente, garantendo inoltre consumi elettrici uguali o inferiori a quelli delle corrispettive presse meccaniche tradizionali. Nell’ambito delle presse ad alta velocità stiamo sviluppando soluzioni specifiche per la tranciatura di lamierino magnetico con spessore di 0,20 mm. Infine abbiamo realizzato presse orizzontali per l’estrusione a freddo dell’allumino fino a 20.000 kN, dedicate alla produzione di componenti per l’automotive».
Ampia offerta
Antonio Dentis di Galdabini focalizza l’attenzione sulla disponibilità a portafoglio di un’ampia gamma di soluzioni per accontentare clienti con esigenze applicative molto diverse tra loro. «La Galdabini, grazie a una presenza sul proprio mercato di riferimento ormai “secolare” (127 anni), è nota e apprezzata per la velocità e la precisione delle proprie presse idrauliche. La qualità realizzativa è testimoniata dalla lunghissima vita operativa di macchine spesso maltrattate e con minima manutenzione, ma anche dalle numerose applicazioni speciali che hanno rappresentato una continua crescita dell’azienda e un punto di riferimento per i propri clienti. A oggi la Galdabini è in grado di offrire macchine e impianti in un range da 70 a 1500 t e in settori che spaziano dall’aerospaziale all’automotive, dal cookware ai serbatoi in pressione, dal medicale al petrolchimico. Punti di forza restano la qualità realizzativa, il software di controllo e la ricerca di soluzioni sempre più efficaci per elevate produttività».
Anche Mauro Buriola di SanGiacomo Presse punta i riflettori sulla necessità di proporre soluzioni per i più svariati settori applicativi. «Al giorno d’oggi le aziende performanti sanno bene quali sono i loro punti di forza e i loro range d’azione. Le produzioni sono sempre più spinte, per cui la distanza tra la necessità di nuovi impianti produttivi e la loro messa in marcia ha margini molto ridotti. Viene quindi meno da parte dei clienti la possibilità di adattare le loro esigenze alle caratteristiche standard delle presse, passando così ai costruttori il compito di adeguare i propri prodotti alle richieste del mercato. Oggi SanGiacomo è un’azienda che realizza ogni anno diverse centinaia di presse meccaniche a collo di cigno da 10 a 450 t e presse a doppio montante da 50 a 500 t che soddisfano le esigenze più disparate dei clienti. Le presse Sangiacomo spaziano dalla pressa base con un interessante rapporto qualità-prezzo, proponendo poi varie versioni cinematiche, soluzioni e opzioni tecnologiche elettroniche/meccaniche dedicate ai vari settori produttivi, per finire con integrazioni software sempre più avanzate».
Massima personalizzazione
Puntare sulla forte personalizzazione del prodotto è un concetto ribadito da Pietro Maffi di AEM3, che ha fatto proprio di questo aspetto il cuore della propria filosofia aziendale. «Il punto di forza generico che caratterizza le nostre presse è che vengono costruite come da esigenze del cliente, al quale offriamo la possibilità di richiedere specifici valori di dimensioni, tonnellaggio, velocità, oltre alla scelta della tipologia di asservimenti da integrare. Al fianco della personalizzazione, altro aspetto caratteristico dei nostri impianti è la loro affidabilità, che possiamo abbinare a prodotti progettati su misura grazie alle profonde competenze che abbiamo maturato in questo campo. Il nostro approccio al cliente è quello di metterlo nelle condizioni di trovare sempre la soluzione più adatta alle proprie esigenze applicative».
La possibilità di fornire soluzioni su misura altamente performanti passa anche attraverso la stretta partnership con fornitori di primissimo livello, come evidenziato da Luca Gelli di Gigant Industries. «Il settore dello stampaggio, e più in generale quello della lavorazione della lamiera, sta sperimentando un periodo di forte innovazione grazie soprattutto alla spinta degli incentivi Industria 4.0. È importante che i produttori di presse rimangano al passo con l’evoluzione e le esigenze di mercato. Gigant Industries, dal canto suo, vanta un’esperienza di più di sessant’anni nel mondo dello stampaggio, e questo le garantisce un’ottima conoscenza delle proprie macchine e delle loro performance. All’esperienza si unisce la continua ricerca con partecipazione a progetti di ricerca con partner industriali e universitari a livello nazionale ed europeo. Il frutto di questa esperienza è bivalente: da un lato le macchine altamente customizzabili sulle esigenze del cliente, dall’altro come costruttore Gigant Industries può suggerire soluzioni non note e innovative ai suoi clienti che rendano più efficiente e sicura la produzione. La forte relazione con partner tecnologici (per esempio stampisti o produttori di automazione) permette un arricchimento esponenziale delle competenze di processo. La conoscenza della propria tecnologia non è più sufficiente in un mercato ipercompetitivo come quello di oggi: il costruttore deve essere un vero consulente per il proprio cliente».
Filosofia 4.0
L’intervento di Luca Gelli ci permette di introdurre l’argomento Industria 4.0, che porta con sé una serie di riflessioni legate all’approccio alla produzione e a quali strategie adottare per migliorare l’efficienza complessiva dell’intero sistema produttivo. Antonio Dentis offre la visione di Galdabini in merito a questo tema. «Industria 4.0 significa potere disporre di uno stabilimento produttivo completamente integrato, nel quale tutti gli impianti comunicano e scambiano dati in tempo reale. Negli ultimi anni Galdabini ha operato un cambiamento importante che le ha permesso di proporsi sul mercato come fornitore capace di fornire soluzioni complesse e di processo. La macchina rimane il nostro core business, ma ci siamo strutturati per rispondere al meglio alle richieste di clienti che sempre più ci chiedono un sistema produttivo e non un singolo macchinario. Abbiamo migliorato le nostre proposte tecniche per raggiungere un livello di eccellenza, identificando mercati e applicazioni dove le proposte altamente tecnologiche risultano vincenti. Oggi siamo in grado di sederci di fronte a un cliente e affrontare la sfida della fornitura di un sistema produttivo complesso operando su più fronti: performance del prodotto finito, layout, gestione della commessa sul piano del project management e dell’engineering. Un’evoluzione che ci ha permesso di ottenere da subito ottimi risultati e presentarci preparati all’arrivo della quarta rivoluzione industriale, con capacità di gestire nel modo ottimale l’integrazione di differenti tecnologie. Un nuovo modo di porci nei confronti del cliente, in alcuni casi addirittura incentivo per le aziende che si sono rivolte a noi nella ricerca di una soluzione più complessa e completa, performante e soprattutto allo stato dell’arte dal punto di vista tecnologico».
All’interno di questo quadro si percepisce anche il nuovo ruolo della pressa, che da elemento a sé stante diventa sempre più parte del sistema come spiegato da Luca Gelli di Gigant Industries. «La quarta rivoluzione industriale ha cambiato il modo di pensare alle singole macchine e al loro impiego. Gigant ha oltrepassato il suo modo di pensare alla pressa come ‘macchina indipendente’ e iniziato a progettarla come un vero e proprio centro di lavoro. Difatti, i clienti di oggi hanno esigenze che puntano al prodotto nella sua globalità e non alla singola lavorazione. Per questo motivo, l’ingegneria di robot e sistemi di interfaccia macchine stanno crescendo esponenzialmente per garantire una comunicazione snella e una condivisione dei dati di produzione in tempo reale. La soluzione adottata da Gigant per rispondere a questa esigenza si chiama ‘ConnectPro’, ovvero una utility software che connette la pressa a un personal computer per scambiare i dati di produzione tramite un runtime Siemens: in questo modo più macchine possono comunicare tra loro registrandosi con un indirizzo IP e sfruttando la connessione LAN. È impressionante e un tema attuale riflettere su come questo cambiamento stia influendo positivamente su tutta la filiera di lavorazione della lamiera. Come produttrice di presse idrauliche Gigant è entusiasta di questa nuova possibilità di integrazione con altre macchine, e si impegna a mantenersi costantemente al passo con l’evoluzione e le esigenze del mercato».
Nuovi strumenti
Giacomo Pavesi di Balconi introduce il tema della manutenzione preventiva, operazione facilitata dall’introduzione dei nuovi strumenti digitali. «Da anni Balconi ha sviluppato interfacce operatore intuitive che, oltre alla gestione completa della pressa e delle ricette stampo, guidano l’operatore anche nelle operazioni di manutenzione preventiva con l’aiuto di messaggi di avviso, foto per l’identificazione dei componenti, disegni e schemi. Nei controlli di ultima generazione il cliente può collegare la pressa alla propria rete aziendale e ottenere tutti i dati riguardanti la produttività della macchina, compresi i tempi di arresto e le relative causali. Al posto delle password di accesso per i differenti livelli operativi (operatore, manutentore, amministratore) si possono utilizzare delle chiavette elettroniche personalizzate. In aggiunta alla teleassistenza standard con alcuni clienti abbiamo sviluppato anche un sistema che, mediante l’ausilio di occhiali specifici indossati, permette di vedere e ascoltare quello che vede e dice la persona sul posto dalla nostra sede e di poterla così meglio guidare alla risoluzione del problema».
Michele Archenti di Aida sposta l’attenzione sui temi del cloud e del Machine Learning. «Nell’ottica di soddisfare le sempre più emergenti richieste d’integrazione e connessione dei macchinari il Gruppo Aida ha già implementato soluzioni utilizzando partner e protocolli come OPC-UA. La novità più importante a cui stiamo lavorando è l’archiviazione dei dati su cloud e l’utilizzo di algoritmi di ML (Machine Learning) per l’interpretazione degli stessi in modo da fornire ai vari livelli aziendali informazioni che prima erano difficilmente reperibili se non tramite un grosso dispendio di risorse. I clienti potranno scegliere tra produzione, manutenzione e management in base alle esigenze. Il sistema IIoT di AIDA potrà essere incluso sia sui nuovi ordinativi sia su macchine già esistenti. Le presse AIDA dotate di tale sistema potranno essere integrate nella fabbrica cliente ed elaborare informazioni sullo stato della produzione e della manutenzione».
Competenze digitali
Rendere totale l’integrazione dei sistemi per un più efficiente scambio dei dati è una delle priorità anche per Valerio Ferraro di Omera. «Omera si pone come uno dei punti di riferimento a livello internazionale nella produzione di linee “chiavi in mano” grazie all’esperienza e alla competenza maturate nella gestione di tutti i principali campi che identificano la meccatronica. A richiesta, le macchine di ultima generazione possono essere controllate da un software collegabile a un supervisore esterno attraverso il protocollo TCP/IP. Relativamente all’interconnessione in rete, il CNC mette a disposizione servizi che permettono ai sistemi informatici/logistici di fabbrica di interagire con le macchine; grazie alla connessione di rete è possibile prelevare un file CSV dal disco fisso della macchina con i dati di produzione; attraverso il teleservice garantiamo la telediagnosi in remoto. I sensori installati monitorano le condizioni di lavoro e l’andamento dei parametri di processo. Il software gestisce le derive del sistema e gli allarmi. La gestione adattativa di alcuni parametri avviene grazie al controllo in anello chiuso di coppia, posizione e velocità».
Secondo Yarno Riva di Zani una delle chiavi del successo è la flessibilità dell’offerta supportata dalle competenze informatiche dell’azienda. «La nostra risposta in tema 4.0 ancora una volta è la flessibilità abbinata al know how interno. Abbiamo la possibilità di personalizzare qualsiasi tipo di richiesta inerente la gestione e l’invio da e verso la macchina di più variabili. Ogni cliente ha una propria gestione della rete aziendale e l’integrazione dei nostri macchinari con la loro rete richiede continue modifiche e adattamenti tra un progetto e l’altro. È fondamentale avere al proprio interno le competenze e le persone per affrontare tutto ciò. Per questo motivo alcuni clienti collaborano con consulenti esterni con i quali ci confrontiamo e cooperiamo per quanto riguarda la connessione tra i vari macchinari, mentre altri clienti invece si affidano completamente a noi e alle proposte che prepariamo di volta in volta a hoc in funzione delle specifiche esigenze».
Integrazione totale
Interconnessione è il tema chiave di Industria 4.0 ripreso anche da Carlo Ridolfi di Cavenaghi & Ridolfi. «La quarta rivoluzione industriale ci ha trovato preparati in quanto l’attuale filosofia era ed è insita nel dna aziendale. Partendo dalla gestione i4.0 della nostra unità produttiva estendiamo questa esperienza ai clienti delle nostre presse e impianti. L’interconnessione tra le macchine, le unità produttive e la rete gestionale aziendale consente un accurato controllo del processo produttivo, ottimizzandone le fasi e controllandone i costi. Tutta l’azienda può avere a disposizione dati che, condivisi, consentono di ottimizzare la gestione integrata del processo produttivo».
Una filosofia condivisa anche da Mauro Buriola di Sangiacomo Presse. «Dalle collo di cigno alle doppio montante, oramai tutte le presse Sangiacomo possono essere integrate alle reti aziendali con molteplici possibilità di interscambio di informazioni, programmazioni della produzione da remoto e monitoraggio della produttività. Tutti requisiti richiesti da questa rivoluzione chiamata Industria 4.0».
A ribadire il concetto è Michele Muffato di Muffato Presse, che accenna anche all’importanza della sicurezza dei dati. «Software, HMI e PLC di gestione delle nostre macchine consentono il più totale controllo, condivisione e connettività. Sono possibili collegamenti tra i vari asservimenti che lavorano nella linea con la macchina, nel caso anche questi ne siano predisposti. Sono possibili collegamenti con vari reparti dell’azienda stessa con sistemi CRM, con analisi della manutenzione, predisposti per l’invio di allert sia con destinatari interni che esterni all’azienda stessa. I nostri software gestiscono connessioni su rete Wi-Fi, rete cablata o GSM worldwide, per garantire connettività e rispetto della privacy e massima tutela dei server aziendali del cliente».
A queste voci si aggiunge quella di Andrea Nava di F.lli Nava, che sottolinea l’importanza dell’attribuire un valore aggiunto ai dati rielaborati. «Le nostre macchine sono predisposte come standard per l’interfacciamento funzionale e delle sicurezze con automazioni del cliente; del resto, in ottica Industria 4.0 viene richiesto dalla clientela più consapevole delle potenzialità dell’informatica accoppiata al mondo dell’automazione e delle presse un macchinario non solo performante, affidabile come fruibilità costante nel tempo e sicuro ai massimi livelli ma anche in grado di dialogare con il mondo IT informatico, per riverberare una preziosa mole di dati di utilizzo dell’impianto in produzione. Questo ha valenza su più piani, sia diagnostico/predittivo per la manutenzione sia per una gestione ottimale delle commesse produttive elaborate potendo analizzare i dati di performance reali incrociandoli con quelli previsionali. A tale proposito abbiamo soluzioni, in funzione delle esigenze del cliente, articolate su più livelli: dall’apertura dei dati della pressa per l’uso IT del cliente fino a un sistema di raccolta/analisi dei dati già completo fornito da noi in cui fare convergere la performance di più nostre macchine installate nel reparto produttivo del cliente».
Affrontare il cambiamento
Offrire una soluzione su misura per il cliente è ancora una volta la principale missione di AEM3, come spiegato da Piero Maffi. «Siamo perfettamente consapevoli che ogni cliente ha un’esigenza differente dagli altri. Per questo proponiamo presse personalizzate con soluzioni in linea con i temi di Industria 4.0. Abbiamo infatti un pacchetto applicativo che il cliente può decidere di acquistare per integrare la pressa all’interno del sistema produttivo, collegandola alla rete informatica con l’obiettivo di gestire/memorizzare i dati di lavorazione relativi a ogni pezzo prodotto. Ancora una volta il dialogo diretto con l’utilizzatore finale è per noi un aspetto chiave, per metterlo nelle condizioni di produrre con la massima qualità ed efficienza».
Tra le richieste di personalizzazione degli impianti in ottica di integrazione di tecnologie, Stefano Rivellini di NRCM sottolinea la crescente domanda di connessione con sistemi di automazione. «Con l’avvento di Industry 4.0 NRCM si è fatta trovare pronta, da anni utilizza sistemi avanzati di gestione delle presse che, connessi a robot e automatismi, consentono di colloquiare tra di loro e inviare ad altri sistemi i dati di processo con grafici in tempo reale. In questo modo l’utilizzatore finale ha una maggiore flessibilità della pressa per la produzione anche di piccoli lotti, riducendo il tempo di setup e di conseguenza riducendo le possibilità di errore da parte dell’operatore. Altro aspetto molto importante è l’aumento della velocità della gestione della commessa, in quanto i dati produttivi vengono interscambiati direttamente tra pressa e pc per la gestione del magazzino e l’analisi della produzione, riducendo notevolmente la percentuale di scarto. Il sistema di gestione NRCM consente a un’azienda di aumentare la propria competitività sul mercato riducendo i tempi di produzione, i tempi di gestione e di aumentare la qualità del prodotto, quindi riducendo i costi finali». Gli strumenti introdotti con la filosofia 4.0 sono il mezzo per portare a termine un cambiamento molto importante.
Lorenzo Galli di I.M.V. Presse spiega come, in molti casi, oltre a fornire le tecnologie sia anche necessario accompagnare i clienti in questa delicata fase di passaggio. «La richiesta principale degli utilizzatori è quella di aumentare la produttività e l’efficienza degli impianti di stampaggio. Parlo di impianti e non solo di presse proprio perché per raggiungere determinati risultati occorre analizzare in modo globale il processo, dalla svolgitura del coil o dal carico del quadrotto fino all’uscita del pezzo finito, considerando anche la logistica intorno a esso come il carico coil, il cambio stampi e lo scarico degli sfridi. Ciascuna macchina e ciascun componente dell’impianto presentano potenziali e criticità, aspetti che se non approfonditi possono determinare perdite d’efficienza dell’impianto intero. Pertanto la ricerca innovativa di I.M.V. Presse non è solamente nel migliorare le prestazioni delle proprie presse, ma anche il corretto allestimento dell’intero impianto, curato e ottimizzato in ogni suo aspetto. Spesso la difficoltà commerciale è quella di portare il cliente ad approfondire questi aspetti invece di concentrarsi solamente su uno di essi, pensando così di ottenere esclusivamente da questo efficienza e prestazione».
Condividi l'articolo
Scegli su quale Social Network vuoi condividere