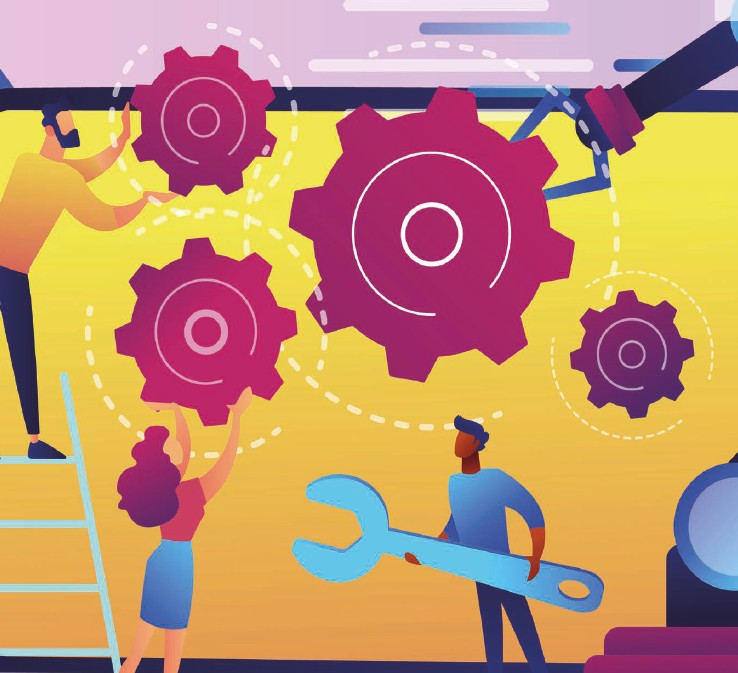
Incontriamo i principali costruttori di robotica collaborativa per capire tendenze e caratteristiche di questa tecnologia sempre più richiesta nel comparto della meccanica.
di Edoardo Oldrati
Dalle piccole officine alle grandi realtà produttive, fino ai contoterzisti evoluti e alle realtà specializzate in specifiche nicchie produttive. Tutte le realtà che compongono lo sfaccettato mondo delle lavorazioni meccaniche stanno guardando con grande interesse all’implementazione di cobot o, per dirla in modo maggiormente corretto, all’applicazione collaborativa di robot. Le ragioni di questo grande interesse, che è già anche un trend di mercato rilevante e che sembra destinato a crescere ancora di più nel futuro prossimo, sono molte e coinvolgono tematiche commerciali, ergonomiche e gestionali. Per meglio capire questo trend tecnologico e i suoi sviluppi per il mondo della meccanica, abbiamo realizzato un’inchiesta tra i principali costruttori di robot collaborativi, raccogliendo opinioni e analisi di operatori ed esperti.
Cosa piace dei cobot
Gualtiero Seva, end-users sales executive di Fanuc Italia, sottolinea come la prospettiva vada allargata, non limitandosi a robot ma guardando all’intera attività che viene automatizzata. «Dal nostro punto di vista occorre innanzitutto parlare non di “robotica collaborativa” ma di “automazione collaborativa”. In questo momento tutti identificano la sicurezza intrinseca del robot con la collaborazione con un operatore. Usando invece il termine “automazione collaborativa” vogliamo includere ovviamente i robot ma anche l’utensile, il polso, tutte le attrezzature complementari e, soprattutto, l’attività da automatizzare. È molto diverso, infatti, parlare di un robot che “intrinsecamente non danneggia l’operatore” da un’attività realizzata in “collaborazione tra un operatore e un robot”. Anche se si utilizza il robot più sicuro al mondo ma con un utensile che può creare un danno all’utente, oppure se si vuole realizzareuna operazione completamente automatica, allora il robot collaborativo non è la soluzione giusta. Fatta questa premessa, le richieste di automazioni veramente collaborative sono ancora poche, e sono di assemblaggi/montaggi di componenti meccanici, asservimento di macchine operatrici, presentazione di parti all’operatore al momento esatto dell’utilizzo, ispezione con sistemi di visione contemporanea al montaggio».
Per Valerio D’Angelo, business development specialist in ABB, l’applicazione collaborativa nel settore delle macchine di lavorazione meccanica richiede soprattutto semplicità di programmazione, flessibilità, elevati standard di sicurezza verso gli operatori, basso impatto a livello di ingombro macchina, elevata produttività. «In questo contesto il robot è per la maggior parte utilizzato per asservire una macchina a controllo numerico nella fase di caricamento e scaricamento. La declinazione collaborativa di queste necessità si traduce nell’adozione di soluzioni robotizzate che permettono all’operatore di intervenire se necessario in modo semplice all’interno dell’area di lavoro. Per realizzare ciò in ABB utilizziamo un sistema denominato SafeMove2 in grado di rilevare in maniera sicura la presenza dell’operatore e di rallentare temporaneamente il robot. Il fatto di utilizzare un robot industriale, per esempio IRB1200, ci permette di mantenere una produttività elevata grazie alla velocità fino a 8 m/s. L’offerta ABB che chiamiamo Collaborative Machine Tending oltre al robot prevede componenti modulari di facile installazione di fronte alle macchine e personalizzabili con infeeder, sistemi di visione e alimentatori vari, HMI di controllo e gestione delle ricette con lo scopo di ridurre al minimo il tempo di messa in servizio».
Marco Filippis, product manager robot South EMEA di Mitsubishi Electric, pone l’enfasi sul contributo che la robotica collaborativa può dare in ottica di riorganizzazione della produzione. «Un aspetto rilevante per gli utilizzatori di robot collaborativi – precisa Filippis – è rappresentato dalla loro facilità di utilizzo in fase di start up e di cambio formato. La sfida per i produttori di robot è quindi legata al fornire una soluzione che garantisca la convivenza con l’essere umano ma allo stesso tempo che metta a disposizione un ambiente software il più possibile snello e semplice. Naturalmente il concetto stesso di robotica collaborativa non può incontrare la totalità delle richieste applicative delle aziende della meccanica, in quanto molto spesso ci si scontra con la produttività richiesta. È dunque fondamentale scegliere il robot da impiegare in funzione della tipologia di applicazione per evitare grossolani errori in termini di resa. L’approccio di Mitsubishi Electric in tal senso prevede una varietà di soluzioni diverse con differenti livelli di collaborazione con l’operatore, per garantire la soluzione ottima in base ai dati progettuali».
Le opportunità per le aziende
«La robotica collaborativa – conferma Giulio Scifo, sales specialist di Comau – ha portato numerose opportunità di impiego all’interno delle aziende della meccanica. Gli aspetti più intriganti della soluzione collaborativa risiedono nella facilità d’installazione dei robot collaborativi, con un notevole risparmio di spazio all’interno delle fabbriche; nella loro semplicità d’uso e programmazione, con la creazione di programmi automatici da personale non esperto di robotica; nella maggiore rapidità di avvio dell’isola robotizzata, con la possibilità di un time-to-market più veloce che in passato. In tema di applicazioni collaborative, le più diffuse in ambito meccanico riguardano l’assemblaggio di componenti, l’asservimento di macchinari per il carico/scarico dei pezzi, il confezionamento dei pezzi a fine linea. L’uso di robot collaborativi consente un’integrazione completa con l’attività manuale degli operatori, anche grazie all’impiego di dispositivi quali laser scanner o barriere ottiche, che permettono di agire in completa sicurezza e nel rispetto delle norme. Questa collaborazione o cooperazione tra uomo e macchina consente all’operatore di dedicarsi a compiti di supervisione dei processi e di controllo qualità, demandando al braccio robotico l’attività di manipolazione o asservimento a basso valore aggiunto».
Per Fausto Chiri, direttore commerciale Yaskawa Italia, la robotica collaborativa presenta diversi aspetti interessanti per le aziende della meccanica. «In particolare, a differenza dei robot tradizionali, i robot collaborativi – essendo pensati per applicazioni caratterizzate da esigenze di bassi payload ma elevata precisione – hanno dimensioni minori rispetto ai robot tradizionali, assi più sottili e motori ridotti: di conseguenza sono meno ingombranti e permettono di risparmiare spazio. Inoltre, i cobot possono essere installati e spostati molto facilmente tramite piattaforme mobili, per operare in diverse stazioni di lavoro. Per garantire la sicurezza nel lavoro in compresenza con l’uomo, i cobot si muovono a una minor velocità, ma questo non va a incidere sulla produttività grazie alle peculiarità che ne permettono un impiego più flessibile all’interno dei sistemi produttivi. Allo stesso obiettivo contribuisce il fatto che, a differenza dei robot tradizionali, i robot collaborativi non sono specializzati in un’unica attività, in quanto gli utensili montati sull’ultima flangia possono essere sostituiti spesso e rapidamente. Un aspetto non meno importante da considerare riguarda il piano di investimento di Industria 4.0 di cui la robotica rappresenta uno dei pilastri riconosciuti».
Alessio Cocchi, country manager Italia di Universal Robots, parte nella sua analisi dalle applicazioni più richieste dal mondo della meccanica. «Asservimento macchine, manipolazione in generale, assemblaggio e controllo qualità. Sono una serie di applicazioni che, a ben vedere, coprono tutte le fasi del processo produttivo, dalla lavorazione iniziale al controllo qualità. Il cobot può essere un ottimo alleato per ciascuna di queste fasi per alcuni semplici motivi che rendono molto apprezzata la robotica collaborativa dal settore della meccanica. Innanzitutto, i cobot UR presentano un’estrema facilità d’uso e una grande riconfigurabilità, ovvero sono flessibili sia in termini applicativi sia in termini operativi. Inoltre, possono operare in spazi compatti o molto aperti quali sono il bordo macchina o il banco di lavoro, cosa che garantisce il mantenimento del layout produttivo senza doverlo modificare».
Per Inga Akulauskaite di Kuka Roboter Italia i robot collaborativi, capaci di operare al fianco dei lavoratori supportandone l’attività, accrescendone l’efficacia e operando azioni difficili se non impossibili per un essere umano, sono ormai una presenza sempre più consolidata nelle linee di produzione delle fabbriche moderne. «L’adattabilità alle sollecitazioni esterne – evidenzia Akulauskaite – consente al robot di compensare eventuali imprecisioni delle attrezzature che interagiscono col robot stesso. Nel caso del nostro robot collaborativo LBR iiwa notiamo un trend rivolto verso le applicazioni di assemblaggio, manipolazione e testing. La capacità di lavorare a stretto contatto con l’uomo è la prima caratteristica che viene in mente pensando ai cobot, ma sono altrettanto essenziali la sensibilità, la flessibilità e la capacità di apprendimento. Robot collaborativi sono presenti nei diversi settori a partire dal consumer goods all’automotive, aeronautico e anche medicale. L’implementazione di nuove soluzioni di automazione robotizzata richiede di ottimizzare gli spazi di lavoro, e quindi operatore e robot si trovano a lavorare a fianco l’uno dell’altro in totale collaborazione. Il robot tende a diventare la terza mano dell’operatore umano, quindi a dare il supporto all’operatore umano nell’esecuzione di attività difficili sul piano ergonomico, alle volte impossibili per una persona; ecco il contributo più importante che un robot collaborativo può fornire assieme ai dati. Tutto ciò, agendo e collaborando con una gestualità naturale e massimi livelli di sicurezza. Si tratta di robot che saranno sempre più sensibili, accurati e intuitivi, ma che non potranno mai sostituirsi alla razionalità umana, anche in presenza di una intelligenza artificiale sempre più sviluppata a capace di analizzare dati provenienti da ogni singolo passaggio produttivo».
Importante ricordare anche i servizi richiesti ai fornitori di soluzioni collaborative e che, come sottolinea Gualtiero Seva di Fanuc, non si limitano alla semplice fornitura di tecnologia. «Tra le richieste che riceviamo più di frequente – conferma Seva – troviamo l’attività di consulenza e di proposta sulla soluzione collaborativa, la rapidità di installazione, una programmazione facilitata. In subordine ci viene chiesta la velocità di esecuzione dei movimenti quando l’operatore non è presente. Inutile poi citare le richieste sull’affidabilità della soluzione e sulla facilità di manutenzione, che sono da sempre caratteristiche native del prodotto Fanuc».
Una vasta gamma di soluzioni
L’obiettivo di questa inchiesta non era solo quello di definire le tendenze in corso, ma costruire anche una panoramica sulle varie soluzioni proposte per la robotica collaborativa. Partiamo da Kuka che propone il robot LBR iiwa, una soluzione con i 7 assi che si ispira al braccio umano e può essere movimentato e controllato sia in modalità compliance che in modalità positioning. «Tutto ciò – spiega Inga Akulauskaite di Kuka Roboter Italia – in combinazione con i sensori integrati conferisce al robot la capacità di avere la sensibilità programmabile. La presenza dei sensori di coppia integrati su tutti gli assi e l’efficientissima funzione di rilevamento delle collisioni rendono LBR iiwa una soluzione ideale per delicati processi di assemblaggio con l’uso di tools. Grazie al peso ridotto, i 7 assi e il design smussato lo rendono una soluzione ideale per spazi di lavoro ridotti e permette una facile integrazione nei sistemi di produzione già esistenti. I robot leggeri e collaborativi sono quindi l’elemento di contatto tra l’universo delle macchine e quello umano, grazie a cedevolezza e sensoristica che garantiscono un ambiente sicuro, senza rischi di collisione ma con una continua produzione di dati da analizzare. Il KMR iiwa è la versione mobile e fa parte di una gamma che spazia da robot leggeri che si possono spostare manualmente, fino a sistemi che agiscono in modo indipendente nello spazio come il KMR iiwa che dialoga con l’intera smart factory, permettendo non solo lo svolgimento delle operazioni richieste, ma anche l’ampliamento dell’orizzonte operativo dei robot fissi e in generale la riconfigurazione dello spazio di fabbrica in base alle esigenze produttive o di logistica».
Alessio Cocchi ci presenta invece la proposta di Universal Robots, unica a proporre una vera piattaforma tecnologica di robotica collaborativa. «Al centro della piattaforma – spiega Cocchi, country manager Italia di Universal Robots – ci sono ovviamente i cobot dotati di 17 funzioni di sicurezza, un sensore di forza/coppia al polso e caratterizzati dall’ormai proverbiale semplicità di installazione e utilizzo e dall’incredibile flessibilità applicativa e operativa che, a tutti gli effetti, definisce lo standard dei cobot e di cosa questi siano veramente: utensili intelligenti a disposizione di tutte le imprese di ogni dimensione e non macchine che, semplicemente, operano in sicurezza. Sopra le “fondamenta tecnologiche” ci sono gli altri elementi che danno vita alla piattaforma a cominciare da Universal Robots+, lo store digitale di prodotti hardware e software sviluppati da terze parti e certificati da UR che si integrano plug&play con i cobot. Una miniera di gripper, sistemi di visione, altri utensili, software pronti per personalizzare le applicazioni e renderle sempre più collaborative. Accanto all’UR+ trova spazio Universal Robots Academy, ovvero la piattaforma di e-learning gratuita attraverso la quale chiunque può imparare nozioni base e di livello intermedio per la programmazione e la gestione dei cobot. Un’opportunità straordinaria per tutti, dagli studenti agli integratori, per misurare sia le caratteristiche dei cobot sia quanto sia semplice, ma potente, utilizzarli. A completare la piattaforma ci sono l’Application Builder, un “simulatore” software per gestire le applicazioni con i cobot e una ricca dotazione di webinar per rendere immediato l’uso dei nostri robot. La piattaforma che mettiamo in campo è senza dubbio unica nel suo genere, giunge a compimento a 10 anni dalla vendita del nostro primo cobot ed è il segno della nostra leadership di mercato che, nei numeri, ci sta portando molto velocemente verso il tetto dei 30 mila cobot venduti».
A fianco dell’operatore
All’interno del catalogo Yaskawa, Fausto Chiri ha voluto presentarci invece il robot Motoman HC10. «Motoman HC10 – spiega il direttore commerciale di Yaskawa Italia – rappresenta una nuova generazione di robotica capace, accessibile, versatile, facile da usare e costruita con la forza industriale per la quale Yaskawa è conosciuta. Progettato per lavorare fianco a fianco con gli operatori umani all’interno di un unico spazio di lavoro condiviso, Motoman HC10 costituisce un passo importante verso quello che l’azienda definisce come “umanotronica”, ovvero un miglioramento dell’interazione uomo/macchina focalizzato sul fattore umano. La facilità di utilizzo contraddistingue inoltre il cobot HC10: il linguaggio di programmazione Inform, inclusa la funzione EasyTeach, consente infatti di gestire facilmente il braccio per definire il percorso e i waypoint che si desidera fare seguire al robot. Questa modalità è chiamata Lead-through-Jogging, o Hand Guiding. HC10 può anche essere programmato tramite il metodo tradizionale utilizzando il Teach Pendant che, con un peso di soli 730 g, è il dispositivo di programmazio ne più leggero della categoria ed è in grado di mostrare le posizioni del robot in 3D tramite un display. Dotato di 6 assi, ha uno sbraccio di 1200 mm e una capacità di carico utile di 10 kg: queste caratteristiche gli permettono di lavorare con gli operatori in un’ampia gamma di applicazioni. Inoltre, Motoman HC10 può essere utilizzato come un robot ibrido sia in modalità collaborativa sia come un vero e proprio robot industriale. Pertanto, se non è necessario un contatto diretto con l’operatore, il robot può funzionare a piena velocità. Un ulteriore punto di forza della serie è il controllo YRC1000 che, molto compatto, permette un utilizzo ottimale dello spazio ed è progettato per impostare nuovi standard elevati per l’accelerazione e la velocità del robot. In alternativa, il cobot di Yaskawa può essere gestito con il nuovo controllo ultracompatto YRC1000 micro con alimentazione civile. Un altro aspetto che contraddistingue il robot collaborativo e in generale tutti i prodotti di Yaskawa è senza dubbio prevela rete di assistenza pre e post vendita: l’azienda infatti supporta l’intero ciclo di vita dei prodotti con servizi di assistenza in linea con tutti i tipi di esigenze e in tutto il globo».
Fulcro della proposta collaborativa di Comau è il robot denominato AURA (Advanced Use Robotic Arm), che si distingue dagli altri robot collaborativi presenti sul mercato per la sua capacità di movimentare oggetti molto pesanti, fino a un massimo di 170 kg di portata utile. «Questo elemento – spiega Giulio Scifo, sales specialist di Comau – è distintivo sul mercato in quanto la gamma dei robot collaborativi si posiziona tradizionalmente in un quadrante definito da una bassa portata utile, di solito fino a 10 kg con qualche eccezione, e da un’area di lavoro contenuta. Rispetto a questo quadro, Comau ha deciso di posizionarsi in un ambito totalmente differente, dove all’alto payload corrisponde un campo di lavoro fino a 2,8 m di sbraccio. L’AURA 170-2.8, il primo modello oggi disponibile sul mercato, risulta quindi essere l’unica soluzione collaborativa disponibile per lavori con pesi elevati in spazi significativamente grandi. Ecco perché trova principalmente impiego in settori industriali quali l’automotive, la meccanica pesante o l’aeronautico, dove gli oggetti da manipolare hanno peso e dimensione rilevanti, come motori, batterie, parti di carrozzeria o di aeroplani. La tecnologia che sta alla base di tale prodotto è molto avanzata, in quanto le questioni di sicurezza legate a un robot di taglia così grande sono numerose e di non facile risoluzione. Per tale motivo Comau preve de non soltanto la fornitura di un robot collaborativo stand-alone ma è in grado di rendere anche il gripper collaborativo l’intera cella robotizzata nel suo complesso, grazie a un mix di dispositivi quali laser scanner o barriere ottiche. Una supervisione completa dell’intera isola di lavoro, dove il robot AURA può interagire con l’operatore e con altre tecnologie come gli AGV o robot di tipo tradizionale, eliminando i compiti più gravosi e fungendo come un intelligente azze proratore di peso. Nel prossimo futuro Comau prevede inoltre di ampliare la gamma collaborativa con prodotti impiegabili in settori e applicazioni diverse, per rispondere alla crescente domanda di soluzioni sempre più easy to use, digital e smart, come da filosofia dell’azienda».
Diversi approcci alla collaborazione
Per coprire tutte le esigenze applicative, Mitsubishi Electric ha strategicamente definito tre differenti approcci alla collaborazione tra robot e uomo. «In particolare – conferma Marco Filippis, product manager robot South EMEA di Mitsubishi Electric – il primo approccio prevede l’utilizzo di funzionalità di safety avanzate su robot industriali standard MELFA mediante l’impiego della centralina di sicurezza MELFA Safe Plus. Grazie a tale opzione è possibile creare delle aree collaborative e quindi lavorare occasionalmente a ripari aperti in completa sicurezza, mantenendo di fatto inalterato il livello di produttività della linea. Il secondo approccio prevede l’utilizzo di una cover sensoriale (Airskin – safety touch cover) su robot standard che rende il robot cooperativo, ovvero in grado di lavorare senza barriere e di fermare la movimentazione in sicurezza con un semplice tocco. L’ultimo e più innovativo approccio riguarda l’introduzione del robot collaborativo MELCoR che consente una completa collaborazione con l’essere umano, sottolineando le caratteristiche principali che portano i maggiori vantaggi all’utente, ovvero rapidità di start-up, semplicità di programmazione e apprendimento delle traiettorie».
L’approccio di ABB è invece quello di proporre due tipologie di robot per applicazioni collaborative in funzione principalmente del tipo di interazione uomo-macchina e in funzione dei compiti da assolvere. «Il robot a 2 bracci Yumi – interviene Valerio D’Angelo, business development specialist in ABB – nasce per applicazioni in cui occorre manipolare componenti di piccole dimensioni, con elevata precisione e velocità paragonabile a quella di un operatore. Novità del 2019 è l’arrivo di YuMi a braccio singolo che, potendo essere posizionato anche a muro oppure a soffitto, dà un ulteriore grado di flessibilità all’isola robotizzata. Questa famiglia di robot si coniuga molto bene in ambiti in cui l’operatore e il robot lavorano gomito a gomito in continuo. Per le applicazioni in cui si prevedono manipolazioni di oggetti più grandi, invece, ABB propone robot dai 5 kg in su di portata in grado di collaborare, come si è detto in precedenza, utilizzando il SafeMove2. Per entrambe le famiglie di collaborativi fondamentale resta la necessità di facile programmazione che si può ottenere utilizzando RobotStudio, il software su pc in grado di simulare in 3D i movimenti del robot e quindi di programmarlo fuori linea, mentre quello reale resta operativo. Flessibilità si coniuga anche con la capacità del robot di adattare i propri programmi in funzione delle variazioni del contesto e questo lo si può ottenere per esempio con una gamma di sistemi di visione integrata».
Conclude questo nostro tour nella robotica e nell’automazione collaborativa la soluzione proposta da Fanuc che ci viene presentata da Gualtiero Seva, end-users sales executive di Fanuc Italia. «Nella proposta collaborativa, essendo partita dai prodotti esistenti nella sua gamma di robot industriali gialli, Fanuc ha potuto rapidamente presentare una gamma di cobot per tutte le esigenze di carico al polso (da 4 a 35 kg) arrivando al robot collaborativo con maggior capacità al polso del mercato, mantenendo al tempo stesso la proverbiale affidabilità del robot stesso e tutta la gamma di funzionalità software disponibile sui robot standard. Inoltre, con l’opzione “Hand Guidance”, abbiamo fornito all’utilizzatore una facile programmazione del robot, pur mantenendo lo standard di programmazione Fanuc per gli operatori più esperti».
Condividi l'articolo
Scegli su quale Social Network vuoi condividere