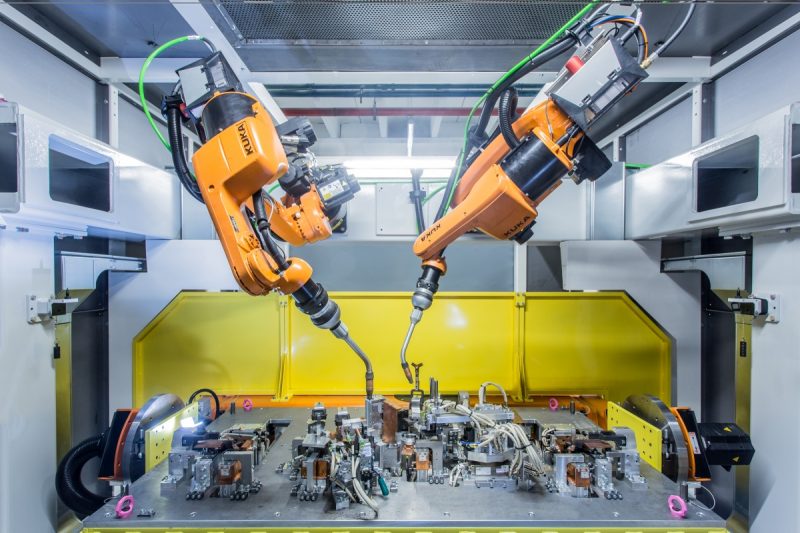
Il Competence Center di Kuka dedicato alla saldatura offre soluzioni per settori esigenti come l’automotive. Qui robot e tecnologia ricoprono un ruolo di rilievo, ma la vera “marcia in più” è il know-how interno.
di Andrea Pagani
A Grugliasco, alle porte di Torino, è operativo un team di esperti che si occupano di saldatura robotizzata. Si tratta del Competence Center ArcLas (dedicato nello specifico alla saldatura ad arco e a punti) di Kuka. Qui circa 30 tra tecnici, disegnatori e project manager sviluppano concept, studi preliminari e analisi di processo dedicati in particolare a uno dei settori più esigenti: l’automotive.
Specializzati per l’automotive
«Quello della saldatura non è un gruppo nato da poco», spiega il responsabile del Competence Center, Osvaldo Casetta. «Risale infatti al 2000 ed è cresciuto insieme alle richieste del settore fino a raggiungere le attuali dimensioni. Siamo nati genericamente come sezione dedicata ai “sistemi di saldatura” e soltanto di recente siamo diventati quello che oggi è conosciuto come Business Unit ArcLas, cioè arc welding & laser. Il nostro mercato di sbocco principale è l’automotive: realizziamo infatti impianti robotizzati che lavorano ovunque ci sia la necessità di eseguire una giunzione come saldature spot o ad arco, ma anche clinciatura, rivettatura o graffatura, per produrre molte delle parti che compongono una automobile, come cofano, longherone, portellone, tetto e telaio».
Tra i propri clienti, la business unit dedicata alla saldatura annovera gruppi come FCA, BMW, Mercedes, Renault e molti dei loro Tier1. In termini geografici è soprattutto l’Europa a usufruirne, con interessanti eccezioni in Nord Africa, Sud America e nell’Est Europa. Si tratta di un mercato molto competitivo, la “guerra dei prezzi” su determinate fasce (tipicamente le piattaforme A, B e C) è serrata e tiene conto di ogni euro speso. Inoltre, le auto restano ormai in produzione per un periodo limitato di tempo poiché vengono sostituite con nuovi modelli o aggiornate con dei restyling; questo comporta una riduzione delle tempistiche utili per il RoI (Ritorno dell’Investimento) delle linee produttive, un fattore che va tenuto in forte considerazione quando si progetta un impianto.
Tra tecnologia e costo per pezzo
Nel corso degli anni c’è stata una significativa evoluzione tecnologica che ha imposto un rapido adeguamento a tutta la filiera. Da un certo punto di vista, il mero costo di acquisto di un impianto è diventato di secondaria importanza. Non che si tratti di un argomento irrilevante (chi lavora nel settore dell’auto sa bene che non è così), ma è strettamente collegato a temi quali produttività ed economicità di processo, qualità, ripetibilità e, naturalmente, a un costo per pezzo ben definito.
Si tratta, nel caso di quest’ultimo punto, di un fattore cruciale. L’attività legata alla produzione di impianti per saldatura di Kuka non compete sul fronte economico con altri produttori a livello di costo di acquisto, ma pone obiettivi specifici di costo per pezzo. Il mercato automotive è particolarmente sensibile a questi temi e valuta con attenzione il TCO (Total Cost of Ownership). Ed è qui che i tecnici Kuka possono mettere in campo le proprie competenze al fine di segnalare le migliori soluzioni in funzione delle esigenze dei clienti.
«I clienti non sono tutti uguali», specifica Casetta. «Alcuni sono molto organizzati e ci contattano avendo già una idea ben chiara di ciò che vogliono e di come lo vogliono, talvolta persino ipotizzando l’attrezzatura che si occuperà della giunzione. In questo caso la nostra forza risiede nel trovare una soluzione che rientri in questi “paletti” imposti da un ciclo produttivo già impostato. Altre case automobilistiche ci lasciano più spazio: le tipologie di giunzioni sono specificate, ma il tutto è a un livello progettuale più acerbo e abbiamo più margine nel proporre le nostre soluzioni. Altri ancora, tipicamente i Tier1, ci chiedono come produrre un determinato quantitativo di pezzi/ora restando entro un certo costo per pezzo e affidandoci la matematica del componente. In ogni caso, a noi spetta l’onere di stabilire come procedere proponendo il tutto al committente finale. Abbiamo poi una serie di aziende di nostra fiducia che si occupano fisicamente della costruzione dell’impianto e della programmazione del software di gestione, tutto naturalmente sotto la nostra supervisione».
La forza delle competenze
Come accennato, le soluzioni proposte dal Competence Center vengono scelte per la loro capacità di rispondere a precise esigenze. «Veniamo scelti per il know-how che abbiamo accumulato nel corso degli anni, per le competenze tecnologiche e per i risultati che possiamo garantire», prosegue Casetta. «I paesi a basso costo della manodopera sono concorrenti insidiosi, ma hanno una sola carta da giocare: il prezzo di acquisto. Nonostante i nostri costi non siano ovviamente i più bassi sul mercato, riusciamo comunque ad avere un vantaggio competitivo grazie all’automatizzazione dei processi e al relativo know-how». Questo know-how che non è fermo, ma che si arricchisce di anno in anno con nuove tecnologie e idee al fine di tenere il passo con le richieste del mercato. «Sta cambiando il modo di produrre le auto. Le vetture ibride hanno una struttura più complessa: per fare un esempio, mentre sui veicoli tradizionali un particolare rinforzo della fiancata è presente solo sul lato del tappo del serbatoio, nei modelli ibridi plug-in è presente anche sull’altro lato per sostenere la presa per la ricarica. Le batterie, dal peso non trascurabile, hanno imposto inoltre delle modifiche nella parte bassa dell’autotelaio, dove ci sono più staffe da saldare, rendendo il ciclo produttivo più lungo e complesso».
A proposito di pesi, tutti sanno che non vanno d’accordo con i consumi. E se ancora non è stato trovato un modo per alleggerire le batterie, c’è un altro modo per togliere peso dalla struttura: utilizzare leghe leggere in alluminio. «Per ridurre le emissioni si utilizzano sempre più le leghe di alluminio su porte, cofano e portellone. Non sono però facili da saldare come l’acciaio, rendendo più complesso il nostro lavoro. In Kuka abbiamo brevettato la tecnologia RoboSpin, nata per velocizzare la dinamica dei robot ma dimostratasi vincente anche per saldare l’alluminio. Con RoboSpin, durante la saldatura spot si tende a mantenere in rotazione gli elettrodi attorno al proprio asse per evitare l’incollaggio degli stessi sul foglio di lamiera. Si rompe così lo strato di ossido di alluminio che si forma e si aumenta la superficie di contatto. Come ultimo vantaggio, non certo secondario, si incrementa la durata degli elettrodi e si allungano gli intervalli di ravvivatura».
Mantenendo in movimento praticamente tutti gli assi del robot, anche durante la saldatura, RoboSpin elimina la necessità di frenare e accelerare ogni volta che si effettua una giunzione. Rispetto a 10 anni fa le pinze per la saldatura sono più pesanti perché più robuste e perché le forze necessarie per saldare l’alluminio sono superiori (se bastano 300 o 400 kg per l’acciaio altoresistenziale, con l’alluminio si sale fino a 800 kg).
I numeri di vendita delle auto elettriche, infine, sono sotto gli occhi di tutti. «Se ne vendono poche decine di migliaia all’anno in tutto il mondo, un numero che rende poco sostenibile la produzione in serie come la concepiamo oggi», conclude Casetta. «A maggior ragione, quindi, i costruttori hanno vincoli progettuali, tecnici e costruttivi molto impegnativi che vengono condivisi con chi, come noi, deve fornire un impianto che sia in grado di lavorare in modo affidabile, in condizioni tecnologiche difficili e mantenendo i costi sotto stretto controllo. Solo se possiedi il giusto know-how puoi rispondere a simili richieste».
Condividi l'articolo
Scegli su quale Social Network vuoi condividere