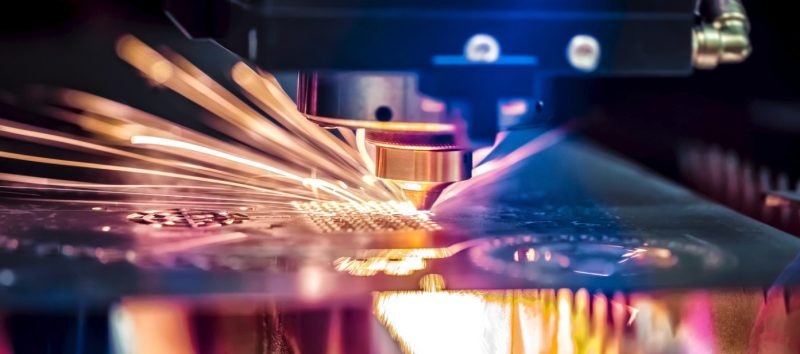
Come stanno cambiando le esigenze tecnologiche legate alle operazioni di taglio laser? E in che modo il distanziamento sociale imposto dalla pandemia ha inciso sulle attività di service? TecnoLamiera lo ha chiesto ad alcune delle principali aziende fornitrici di macchine e sorgenti per il taglio laser.
di Davide Davò
Quando si parla di tecnologie in rapida evoluzione, non si può prescindere dal citare macchine e sorgenti laser. Aumento di potenza, controllo del fascio e incremento dell’efficienza sono solo alcune delle direzioni di sviluppo di questi sistemi di produzione, con i fornitori di tali tecnologie che in tempi recenti hanno anche implementato soluzioni per migliorare il supporto al cliente eseguito da remoto causa pandemia. Per capire meglio in che modo sta cambiando il settore del taglio laser, TecnoLamiera ha interpellato alcuni dei principali fornitori di macchine e sorgenti laser per applicazioni nel mondo della lamiera.
La tecnologia laser per il taglio della lamiera è in continua evoluzione, e negli ultimi anni si sono alternate diverse direzioni di sviluppo. Attualmente qual è la principale richiesta da parte del mercato e quali saranno a vostro parere le richieste future?
Pierluigi Vaghini – Amada
«Amada storicamente dedica grande attenzione al controllo del fascio, come dimostrano anche le tecnologie di cui sono dotate le sorgenti che equipaggiano le nostre macchine. In particolare tramite la tecnologia Ensis offriamo la possibilità di modificare il mode del fascio laser in base allo spessore del materiale da lavorare, garantendo prestazioni di altissimo livello e utilizzando un’unica lente di taglio su tutti i materiali e spessori. Il Ventis, con la tecnologia LBC (Locus Beam Control), permette invece di controllare il movimento del raggio laser per ottenere una massima efficienza produttiva in base al tipo di materiale da lavorare e allo spessore. Sempre l’efficienza, ma stavolta in termini di consumo energetico, rappresenta il secondo aspetto chiave nelle strategie di sviluppo delle sorgenti Amada, e non a caso possiamo vantare uno dei livelli di efficacia più elevati sul mercato. La potenza, o per essere più precisi l’aumento delle potenze richieste, rappresenta la terza direzione di sviluppo delle nostre soluzioni. Premettendo che il nostro approccio è di dialogare con il cliente per capire quale sia la potenza di cui realmente necessita per la propria attività, negli anni abbiamo strutturato la nostra offerta partendo dal mono-modulo da 3 kW, a cui si sono poi aggiunte le sorgenti da 6 kW, 9 kW e di recente da 12 kW».
Silvia Bragagnolo – Asaf
«Negli ultimi anni, il marchio Baykal che noi distribuiamo in esclusiva su tutto il territorio italiano ha investito cospicue risorse sulla tecnologia laser fibra. Questo ha permesso alla casa madre di potere sviluppare una serie di prodotti molto flessibili e particolarmente facili da configurare. Per quanto riguarda il mercato italiano, notiamo una sempre maggiore consapevolezza da parte della clientela circa l’importanza dell’utilizzo di componentistica prodotta da primarie case costruttrici, per una maggiore garanzia di assistenza e disponibilità di ricambistica. Possiamo inoltre affermare che la nostra clientela mira a prestazioni costanti nel tempo, più che alla ricerca di caratteristiche estreme che in molti casi non vengono pienamente sfruttate. La maggioranza delle richieste che riceviamo sono sui formati 3015 e 4020. Per quanto riguarda invece la potenza, la domanda si stabilizza sui 4-6 kW, per arrivare in alcuni casi al 10-12 kW. Grazie alla sempre maggiore efficienza e affidabilità dei sistemi laser fibra, alla drastica riduzione dei prezzi di acquisto, nonché alla loro facilità di manutenzione e di gestione rispetto alla tecnologia CO2, queste macchine stanno avendo una diffusione ormai capillare. Crediamo quindi che il futuro delle macchine a taglio laser fibra sarà certamente brillante e prospero di innovazioni tecnologiche».
Elena Farina – Comaf
«Il laser è ormai diventata una macchina essenziale per la maggior parte delle aziende che lavorano la lamiera, e gli incentivi legati alla 4.0 hanno spinto molti clienti all’acquisto. L’aumento della richiesta ha comportato anche una diversificazione notevole delle esigenze dei diversi clienti: non solo maggiori potenze in alcuni casi, ma anche migliore rapporto qualità/prezzo, compattezza del design, impianti speciali, dimensioni notevoli (Ermaksan da noi distribuito sul territorio italiano ha già prodotto laser con lunghezza 9, 12 e 18 m), e opzioni quali taglio tubi. Il mercato si è quindi allargato ma in diverse direzioni, a volte anche opposte, in quanto il range di clientela è attualmente molto più vasto. Non dimentichiamo che su grossi spessori anche il taglio plasma con nuova componentistica Hypertherm ha avuto un grande progresso tecnologico in termini di qualità di taglio, sovrapponendosi in alcuni casi ai laser di alta potenza. Probabilmente le future richieste saranno ancora molto variegate per qualche anno, visto anche l’evolversi delle nuove tecnologie del taglio laser fibra, per poi stabilizzarsi su laser comunque di qualità ma non dai costi elevati, con potenze nella maggior parte dei casi “tradizionali” ma soprattutto con garanzia di efficienza e di supporto tecnico».
Federico Campana – Cy-Laser
«Stiamo assistendo a una richiesta sempre maggiore di alte potenze. Si sono dunque aperti spiragli là dove il laser non era contemplato. Le alte potenze, in particolare quelle che sfruttano come gas di assistenza l’azoto, sono adatte al taglio di medi/alti spessori e consentono di aumentare la prestazione oraria e la produttività. Quello che prima veniva tagliato al plasma oggi può essere tagliato al laser, con tutti i vantaggi che quest’ultimo offre: precisione, velocità ed economicità. Sappiamo bene che il plasma, malgrado abbia un costo inferiore rispetto al laser, nasconde l’insidia dei costi alti dei consumabili. Nel caso del laser, invece, i costi dei consumabili sono inferiori a fronte di una durata maggiore. Per soddisfare i clienti e garantire costi di esercizio bassi, Cy-Laser ha introdotto la testa di taglio EVO V HP, specifica per le alte potenze e installabile sui formati dal 3000 x 1500 mm al 13.000 x 3000 mm a testa Bevel. Per il controllo del fascio, gli optional di processo Vega e Vortex garantiscono una migliore qualità del taglio permettendo di modulare la frequenza grazie alla gestione del flusso del gas e di programmare la dimensione dello spot senza variare le ottiche».
Christian Mora – Fanuc Italia
«Fanuc da sempre soddisfa le esigenze di lavorazione degli utilizzatori di macchine a taglio laser continuando a investire nella ricerca di prodotti sempre più semplici da programmare con livelli di performance elevate. Il mercato richiede potenze sempre più importanti. Per questo motivo, Fanuc ha potenziato la linea di laser in fibra ottica attuale (1000-6000 W) con la nuova sorgente FF12000i-B da 12 kW, ponendo un occhio di riguardo al risparmio energetico e aumentando l’efficienza di tutta la linea. La gamma laser fibra è affiancata dalla tradizionalmente affidabile gamma CO2 da 1000 a 6000 W, ancora oggi a disposizione per le applicazioni che lo richiedono. Il mercato, inoltre, ricerca soluzioni di automazione dei processi che siano facili, flessibili e integrate. Fanuc ha sempre investito nella proposta di soluzioni complete e integrate, anticipando quelle che sono le richieste di mercato attuali e sfruttando il vantaggio di produrre internamente tutti i componenti e le soluzioni di automazione e potere offrire quindi un’automazione precisa e seamless. Per la gestione di macchine taglio tradizionali a 4 e 5 assi è disponibile un’unica soluzione laser-controllo numerico e, per le applicazioni di automazione pura, viene proposta una soluzione laser-robot per il taglio e per la saldatura. Nell’ottica di sviluppare soluzioni aperte che semplificano la quotidianità degli addetti ai lavori, Fanuc ha introdotto di recente i controlli numerici 0i-LF Plus e 30i-LB Plus con interfaccia iHMI dedicata alla gestione delle sorgenti laser (anche non Fanuc), oltre che della macchina stessa».
Keiji Kaneda – Fujikura European Engineering Centre di Brescia
«In questo ultimo anno in particolare, la competizione tra i principali produttori mondiali di macchine di taglio laser a fibra si è focalizzata maggiormente sull’utilizzo di sorgenti a fibra di elevata potenza, anziché sull’efficientamento evolutivo del processo di taglio. Dal nostro European Engineering Centre di Fujikura abbiamo supportato i nostri clienti in entrambi i percorsi, anche se la nostra tradizione di produzione e spinta innovativa ci ha visti particolarmente impegnati a favore dell’ottimizzazione di processo, dove intravediamo i principali sviluppi futuri. In risposta alle richieste del mercato, abbiamo anche introdotto in anteprima mondiale presso alcuni clienti corporate il nostro nuovo BPC (Beam Profiling Control), ovvero il controllo indipendente di potenza e modulazione tra ring e centre nella fibra emissiva. Ultimamente stiamo svolgendo numerose attività di qualificazione in EMEA nell’industry del taglio sfruttando le capacità distintive delle nostre sorgenti di gestire i fenomeni non lineari e di mitigare il fenomeno della back-reflection che si verifica nell’interazione del laser con materiali riflettenti. Queste caratteristiche ci consentono di ottimizzare i tempi di piercing (sfondamento di taglio) oppure di ridurre il fabbisogno di potenza massima coinvolta nel processo. In entrambi i casi i risultati perseguiti consentono un trasferimento di valore e vantaggio competitivo sia verso il costruttore di macchine che verso l’utilizzatore finale».
Alberto Cavallini – IPG Photonics
«A giudicare dalle richieste dei nostri clienti, il mercato ha imboccato con decisione la strada della maggiore potenza, che significa una maggiore produttività senza aumentare il costo del personale e mantenendo quasi invariato quello degli impianti. La maggiore potenza si traduce anche in una maggiore qualità delle superfici di taglio, aspetto a cui i clienti sono sempre più attenti. Anche l’opzione HPP (High Peak Power) di IPG va nella direzione del miglioramento della qualità di taglio e della diminuzione dei costi poiché la possibilità di eseguire il preforo a una potenza doppia rispetto alla potenza nominale della sorgente si traduce in una diminuzione della superficie coinvolta e dei tempi di esecuzione. In un contesto generale in cui tutta l’industria punta all’efficienza e alla razionalizzazione, i produttori di macchine di taglio non sono da meno: è per questo che IPG ha aumentato l’efficienza delle proprie sorgenti da un minimo del 35% fino a oltre il 50% della serie ECO. Poiché le sorgenti laser a fibra sono dispositivi puramente optoelettronici è logico pensare che in futuro i clienti si aspettino le tendenze tipiche di questo settore: una costante diminuzione dei costi degli impianti e un aumento dell’affidabilità e delle prestazioni».
Alessandro Primerano – Messer Griesheim Saldatura
«Il mercato in questo momento vive di continui ribaltamenti di fronti dovuti ad agenti interni ed esterni. Dal punto di vista esterno, il Covid-19 ha modificato il modo di lavorare e la visione del futuro, gli incentivi legati a Industria 4.0 e Sabatini spingono agli investimenti, mentre il continuo rialzo delle materie prime li frenano. Difficile in questo momento per un imprenditore decidere il da farsi. Dal punto di vista interno, ovvero quello che riguarda lo stato dell’arte dell’intera filiera laser, sono tante le variabili e le nuove correnti di pensiero. Tipicamente il costruttore di sorgenti e di teste di taglio spinge per le soluzioni proprietarie per mantenere le posizioni acquisite, mentre i vari assemblatori cercano di trarre da queste soluzioni impianti sempre più estremi. Ecco a cosa mi riferivo: a correnti di pensiero piuttosto che a soluzioni tecniche. Il cliente dovrebbe focalizzare la scelta sulle proprie necessità e tipi di materiali, sulla affidabilità e sul post vendita. L’impianto laser deve produrre e lavorare più ore possibili. Per quanto ci riguarda, Messer Cutting Systems realizza solo impianti di grosse dimensioni con testa dritta o Bevel 5 assi con automazioni per grandi formati. Nell’ultimo periodo abbiamo avuto molte richieste per il montaggio di teste di foratura con cambio utensili integrato per fornire piastre maschiate e forate».
Marco Montani – Optoprim
«La tecnologia laser si sta affermando nel settore taglio lamiera sempre di più grazie ai vantaggi che sin da subito la stessa ha portato: migliore qualità del taglio, maggior velocità, aumento della wall-plug efficency, assenza quasi totale dei consumabili, flessibilità sulle geometrie da eseguire e molto altro. Sicuramente negli ultimi anni ci sono state diverse direzioni di sviluppo per potere rispondere alle richieste del mercato. In primis si è vista un’escalation di potenza notevole per potere arrivare a tagliare spessori sempre maggiori o per aumentare considerevolmente la produttività delle macchine. Si è dato grande sviluppo alle tecnologie laser che intrinsecamente risultano più efficienti, quali i laser in fibra che possono raggiungere anche un’efficienza pari al 40%. Un altro aspetto cui è stata data importanza sono gli accessori, come per esempio uno studio approfondito sulla fluidodinamica degli ugelli atto a ridurre sensibilmente il consumo dei gas di processo. I produttori di sorgenti laser hanno inoltre lavorato per fornire ai produttori di macchine delle sorgenti che possono essere utilizzate in modo flessibile. Sicuramente la novità più rilevante è stata la possibilità di controllare la forma e la dimensione del fascio di uscita del laser. L’ormai noto beam shaping infatti permette, a parità di potenza, di tagliare spessori maggiori e di ottenere qualità di taglio migliori. Una macchina equipaggiata con questa nuova tecnologia è in grado di tagliare da spessori sottili a spessori più elevati a parità di set-up».
Giulio Amore – Prima Power
«Conquistato il beneficio della riduzione dei costi operativi grazie all’introduzione delle sorgenti laser fibra, la tendenza degli ultimi anni è rivolta alla ricerca dell’ottimizzazione delle qualità di taglio che fino a qualche anno fa rimanevano prerogativa delle sorgenti a CO2. Per tale ricerca si sono seguite due strade: aumento delle potenze e introduzione di sistemi di controllo del fascio. Gli sviluppi tecnologici degli ultimi anni relativi al controllo del fascio hanno consentito il raggiungimento di risultati sul fronte della qualità di taglio che sarebbero stati impensabili fino a pochi anni fa. Prima Power ha da sempre perseguito il bilanciamento tra aumento di potenza e introduzione di pacchetti tecnologici o di gestione del fascio, nell’ottica di proporre al cliente il migliore compromesso con attenzione al ritorno dell’investimento. Parlando di prospettive per il futuro, invece, una delle tendenze che a mio avviso caratterizzeranno i prossimi anni è sicuramente quella relativa all’automatizzazione del processo produttivo. Sempre più numerosi sono i clienti alla ricerca di macchine laser dotate di sensoristica avanzata (meglio se basate su concetti di intelligenza artificiale): macchine sempre più autonome in grado di analizzare il processo in tempo reale e di apportare correzioni e modifiche a tutti i parametri e i servizi che ruotano attorno alla produzione, limitando al minimo l’intervento umano e garantendo così una produzione sempre più efficiente e ripetibile».
Pierandrea Bello – Salvagnini
«Le tendenze su cui ci siamo concentrati sono sostanzialmente tre. La prima è quella della semplificazione, dello sviluppo di soluzioni agili e di facile utilizzo, che consentano all’operatore di risolvere senza sforzo alcuni dei problemi che quotidianamente incontra nel suo lavoro. A questa categoria appartengono per esempio i dispositivi per la visione artificiale AVS, SVS e NVS: AVS accelera il centraggio della lamiera e permette il centraggio anche su parti già punzonate; SVS permette di riutilizzare gli spezzoni di lamiera per nestare in modo semplice, veloce e senza errori; NVS verifica il centraggio del fascio laser e lo stato dell’ugello. La seconda tendenza è l’automazione, che consente di recuperare quote rilevanti di efficienza: il nostro magazzino LTWS, per esempio, diventa fattore abilitante per aumentare l’autonomia del sistema di taglio perché permette di avere sempre disponibili materiali e spessori diversi per lavorazioni just in time riducendo i tempi di attesa per l’approvvigionamento della lamiera. In aziende caratterizzate da bassi volumi e rapidi cambi di produzione, combinare magazzino e dispositivi di carico/scarico automatici è una strategia vincente, che può essere ancora più determinante se aggiungiamo un dispositivo di sorting automatico come il nostro MCU. La terza e ultima tendenza è quella del miglioramento delle performance complessive di fabbrica grazie alla digitalizzazione e a OPS, il software modulare per la gestione della produzione. La digitalizzazione rende disponibili soluzioni facili da usare per puntare al controllo, all’ottimizzazione del processo produttivo, all’eliminazione di tutti quei tempi morti, spesso invisibili, che erodono l’efficienza e la competitività delle aziende».
Laura Perini – Trumpf
«Tra proposte diverse e potenze sempre maggiori, Trumpf si pone come consulente a 360° e partner dei propri clienti offrendo, oltre alla potenza, il suo pieno controllo, assistenza costante, macchine facili da utilizzare e in grado di lavorare con elevati livelli di automatismo grazie a sensori intelligenti e funzioni che adattano il taglio senza l’intervento dell’operatore per ottimizzare qualità, efficienza e consentire di ridurre i consumi, gli scarti, le post lavorazioni, i fermi produttivi. Ne è un esempio la funzione Active Speed Control, che osserva attraverso l’ugello la fessura di taglio, monitora il processo e controlla l’avanzamento in modo attivo e automatico attraverso i sensori presenti nella testa. Gli ugelli, originali Trumpf, sono progettati e fabbricati con grande accuratezza. Ogni ugello ha un preciso elemento conico che ne assicura il centraggio all’avvitamento e non richiede ulteriori interventi in situazioni di lavoro normali. Tra le tante funzioni disponibili ControlLine, presente in configurazione standard su tutte le macchine, regola l’altezza della testa e mantiene costante la distanza tra ugello e lamiera durante il taglio anche in presenza di lamiere non perfettamente piane, mentre la testa di taglio è progettata per sganciarsi immediatamente in caso di collisione grazie al giunto magnetico, e può essere poi riportata in posizione velocemente dall’operatore per la ripresa immediata della produzione. Le tabelle tecnologiche, studiate e testate nei reparti produttivi di Trumpf e caricate sul controllo di tutte le macchine, rendono estremamente semplice l’utilizzo degli impianti anche agli operatori meno esperti».
Giovanni Baccolini – Yamazaki Mazak
«Siamo costantemente impegnati nella ricerca, nell’innovazione e nel miglioramento dell’efficienza. Efficienza evidenziata nella creazione di unità produttive intelligenti, flessibili, affidabili e user friendly. Questa è l’esigenza che riscontriamo provenire dal mercato. La spinta del marchio Mazak la si può notare a partire dalla gamma di potenze disponibili abbinate ai modelli e alle tecnologie di taglio, dove Mazak evidenzia tre soluzioni disponibili per ogni esigenza: CO2, fibra e diodo diretto, in grado di definire geometrie accuratissime e lavorare pezzi a costi contenuti su tutti i materiali e spessori grazie alle sorgenti di ultima generazione, alla gestione del fascio e alla Multi Control Torch 2.1, ultimo ritrovato tecnologico in casa Mazak».
Sulla base del vostro feedback, in che modo la situazione che stiamo affrontando ha influenzato le vostre attività di servizio?
Giovanni Baccolini – Yamazaki Mazak
«L’affidabilità raggiunta da queste macchine è altissima. Infatti, non richiedono manutenzione periodica ma si eseguono dei tagliandi manutentivi preventivi, al fine di garantirne la piena efficienza. Si è lavorato tantissimo per ridurre al minimo gli interventi, tutte le macchine possono essere collegate in teleassistenza, un cruscotto gestionale di altissimo livello ci permette di intervenire tempestivamente in caso di guasto e contemporaneamente gestire gli eventuali ricambi entro le 24 ore successive. Grandi investimenti sono stati fatti anche per i servizi: affiancamento al cliente, formazione, assistenza telefonica gratuita, con risultati importantissimi in termini di soddisfazione del cliente, in un clima di esigenze produttive in continua crescita».
Laura Perini – Trumpf
«Oltre a efficienza e qualità, le aziende richiedono la riduzione dei costi di gestione degli impianti e flessibilità, tanto nel funzionamento delle macchine quanto nei servizi di assistenza. Oltre alle funzioni e ai sensori intelligenti per il controllo del taglio, Trumpf propone funzioni in grado di supportare gli operatori anche nel sorting dei pezzi e nella pianificazione delle attività di manutenzione. L’innovativa funzione Sorting Guide combina i dati di programmazione dei fogli con l’elaborazione intelligente delle immagini e supporta la rimozione e l’identificazione delle parti quando la macchina non è dotata di sistemi automatici per il sorting dei pezzi. Il Condition Guide installato sulle macchine Trumpf è un sistema a semafori che supporta l’operatore nell’attività di manutenzione, indicando lo stato degli elementi principali e suggerendo i provvedimenti appropriati, pianificabili secondo le esigenze produttive. Tecnici Trumpf, specializzati per tecnologia, sono a disposizione 12 ore al giorno e forniscono supporto tecnico da remoto attraverso i più moderni sistemi. Le macchine Trumpf comunicano con apparecchi mobili. L’interfaccia permette l’uso di app per essere assistiti con efficienti sistemi di chat, scambio di immagini e suoni».
Pierandrea Bello – Salvagnini
«Da anni la trasformazione digitale ci guida nell’individuare e proporre strumenti innovativi ed efficaci per l’assistenza, con l’obiettivo di migliorare la velocità e la qualità dei nostri interventi, fondamentali per assicurare maggior competitività ai nostri clienti. Anche nell’ultimo anno le attività di service, nonostante il contesto, sono proseguite praticamente senza soluzione di continuità: oltre ai tradizionali interventi in presenza, che hanno giocoforza subito un rallentamento, nello scenario pandemico siamo stati sostenuti da alcuni strumenti – Links e Acty – che già avevamo a disposizione e che hanno dimostrato tutta la loro efficacia. Links è la soluzione IoT Salvagnini che permette di monitorare macchine e sistemi da remoto, consentendo l’accesso in tempo reale a dati di produzione, logbook, KPI di prestazione e telemetria. Links oggi si integra con le nostre proposte di contratto di manutenzione per una gestione ottimale degli impianti dei nostri clienti. Acty è un’applicazione di realtà aumentata che dal 2018 fa parte della nostra offerta e che ha avuto ulteriori, grandi riscontri: riduce i tempi di risoluzione dei guasti e i costi di servizio».
Giulio Amore – Prima Power
«Quasi il 30% dei ricavi 2020 del nostro Gruppo deriva dai servizi post vendita. Questo grazie alla nostra vasta base installata in oltre 80 Paesi del mondo e grazie al fatto che l’attività di service, meno influenzata dal ciclo economico, durante l’emergenza Covid-19 ha mostrato una flessione più contenuta rispetto al mercato delle nuove macchine. La tendenza alla digitalizzazione è un aspetto molto importante nel settore del service, sul quale la situazione contingente ha agito da acceleratore. Non solo le restrizioni agli spostamenti, ma anche la maggiore sensibilità agli aspetti ambientali e sociali hanno dato un forte impulso a tutte le soluzioni smart come IoT, realtà aumentata, intelligenza artificiale. Da decenni proponiamo soluzioni di assistenza remota e i nostri prodotti attuali rispondono ai requisiti 4.0. Le nuove tecnologie a disposizione oggi ci permettono di offrire soluzioni sempre più intelligenti, che permettono di supportare in modo efficace, rapido e sostenibile i nostri clienti anche a distanza. Fra le nuove esigenze dei clienti ci sono sicuramente il monitoraggio delle macchine e la diagnostica avanzata che permettono, grazie alla grande mole di dati provenienti da sistemi intelligenti e iperconnessi, di rilevare possibili problemi prima che si verifichino, minimizzando i periodi di inattività non pianificata e massimizzando l’efficienza produttiva».
Marco Montani – Optoprim
«Già da tempo, in collaborazione con il nostro principale partner nLight, Optoprim sta dedicando una particolare attenzione al service per ridurre al minimo i fermi macchina. Questo è stato possibile anche grazie al fatto che le sorgenti e le teste di processo da noi proposte sono progettate per essere quasi completamente asservite in campo. Inoltre proponiamo ai nostri clienti degli strumenti (microscopi per l’ispezione della fibra, power meter) che facilitano la diagnostica delle problematiche, permettendo una risoluzione delle stesse in tempi brevi. La possibilità poi di potere contare su prodotti dotati di una sensoristica evoluta, che permette di monitorare real time le grandezze fondamentali, ci consente di evitare guasti improvvisi programmando eventuali interventi di manutenzione qualora necessari. Questo è anche possibile grazie ai protocolli di comunicazione industriali presenti ormai su tutti i nostri prodotti, e mediante i quali possiamo accedere da remoto per una prima analisi. In un anno dove la difficoltà degli spostamenti non ha avuto precedenti, è stato evidente come questa avanguardia tecnologica abbia consentito a noi e ai nostri clienti di lavorare con molte meno difficoltà del previsto».
Alessandro Primerano – Messer Griesheim Saldatura
«Il post vendita è una parte importantissima nel rapporto con il cliente finale. Il contratto di acquisto non si esaurisce con la consegna, anzi, la parte delicata inizia proprio dall’istruzione del nuovo sistema. Tanto più tempo si dedica a formare il personale, meno problematiche si presenteranno con il passare del tempo. Questo non esclude le rotture o i malfunzionamenti, ma sicuramente aiuta a individuarli più facilmente e ad avere feedback mirati già dall’operatore sul campo. Con le tecnologie Industria 4.0 si hanno i sistemi collegati in remoto per un check veloce, ma il cliente italiano preferisce ancora la presenza fisica del tecnico per verificare il corretto funzionamento dell’intero sistema e non solo della parte guasta. È questione di mentalità e di utilizzo. Nell’ultimo periodo sono aumentante le richieste di contratti di manutenzione preventiva, aggiornamento dei CNC e altri revamping tecnologici. La situazione è di difficile lettura, si vorrebbe investire per nuovi sistemi ma allo stesso tempo tutelarsi cercando di mantenere in linea anche gli impianti già presenti in azienda. La nostra scelta di avere un tecnico responsabile per singolo cliente ci ha permesso di creare un legame di partnership molto forte e duraturo con i nostri clienti».
Alberto Cavallini – IPG Photonics
«L’attività di assistenza tecnica svolta presso i clienti si è notevolmente complicata negli ultimi tempi a causa della pandemia: spostarsi è diventato più difficile sia per le limitazioni alla mobilità imposte dai Governi, sia per l’espletazione delle pratiche burocratiche connesse. Dove possibile si è sopperito con gli strumenti di diagnosi remota che ci vengono messi a disposizione dalla tecnologia. Più in generale, escludendo le conseguenze della pandemia che sono importanti ma per fortuna temporanee, possiamo dire che la riduzione di prezzo delle sorgenti ha aperto le porte a nuove applicazioni. Il taglio laser rimane tuttora la lavorazione laser maggiormente diffusa, ma sta progressivamente riducendo il proprio peso a favore della saldatura e di altre applicazioni. Questo ha notevoli implicazioni anche per l’assistenza tecnica, poiché si tratta in genere di progetti speciali messi a punto dal nostro laboratorio prove, e il service è chiamato a supportare il cliente sia sugli impianti, sia sul processo. Ai tecnici sono richieste conoscenze e competenze sempre maggiori».
Keiji Kaneda – Fujikura European Engineering Centre di Brescia
«Possiamo asserire che l’intermittenza della produzione durante la pandemia ha sicuramente condizionato prima di tutto l’operatività delle grandi aziende manifatturiere, e di conseguenza la modalità di erogazione del service. Fujikura mira, da sempre, alla creazione di una cultura alla “serviceability” trasparente ed efficiente, che consiste nell’avviare piani di formazione e certificazione mirati all’ottenimento, da parte dei costruttori di macchine e dei system integrator, dell’indipendenza al service. La struttura modulare del design costruttivo dei cabinet Fujikura permette infatti l’operabilità “per moduli principali” e questo dà modo, dopo un percorso di training certificato, di diventare indipendenti nelle attività di service fondamentali. La gestione della produzione per TQM (Total Quality Management) consente di mantenere molto bassa la casistica di intervento durante il ciclo di vita delle sorgenti laser, previo utilizzo corretto. Questo ha consentito storicamente di dividere e approcciare in modo differente i temi di business continuity da quelli di service. Per la business continuity, la struttura modulare e un buffer locale di spares sono rimaste anche durante la pandemia la soluzione preferita nelle produzioni intensive. Per il service, le buone pratiche di training certificati hanno creato una consapevolezza all’intervento che ha consentito di scalare business internazionali e distribuiti su larga scala, creando un ecosistema efficiente e di grande copertura durante le limitazioni logistiche dell’ultimo anno e mezzo».
Christian Mora – Fanuc Italia
«Nonostante la situazione di pandemia mondiale che ha complicato gli scenari produttivi e di contatto con i clienti, le attività di service di Fanuc non hanno registrato ripercussioni particolarmente negative. La caratteristica di Fanuc è sempre stata quella di essere vicino ai propri clienti aprendo filiali in tutto il mondo per essere precisi e puntuali nelle richieste di assistenza (in linea con il motto del Gruppo, “Service First”). A oggi le filiali aperte nel mondo sono oltre 260 e, con le restrizioni imposte dai vari Stati per colpa della pandemia, la mobilità tra Paesi si è praticamente azzerata. L’essere presenti direttamente in loco, con persone della stessa nazionalità del cliente, ci ha permesso di intervenire ove necessario senza nessuna limitazione. Questo anche grazie all’ausilio di un nuovo strumento per il service: Fanuc Assisted Reality, un servizio digitale di teleassistenza che sfrutta la tecnologia della realtà aumentata permettendo agli operatori del Service Fanuc di effettuare la manutenzione e l’avviamento a distanza in modo ancora più efficiente, senza dovere essere necessariamente presenti in loco, con notevole risparmio di tempo e di costi. La sfida di Fanuc per il prossimo futuro sarà quella di essere ancora più vicina al cliente, minimizzando ulteriormente i tempi di attesa intervenendo quanto prima per evitare lunghi fermi macchina che portano a perdite di produzione e denaro».
Federico Campana – Cy-Laser
«I nostri sistemi sono precisi, veloci e affidabili e richiedono una manutenzione minima. Questo grazie a un elevato know how frutto del nostro lavoro che ci posiziona tra i pionieri della tecnologia laser in fibra ottica, e soprattutto grazie a un team di tecnici altamente qualificati. Riteniamo che disporre di personale specializzato e periodicamente formato sia di grandissima importanza e rappresenti un enorme valore aggiunto. Aspetto che in alcuni contesti viene erroneamente trascurato, focalizzando l’attenzione e la discussione più sulla mera operazione economica e causando così un danno al mercato. In questo periodo non abbiamo riscontrato particolari cambiamenti e il nostro servizio di teleassistenza ha continuato ad assistere i clienti con interventi tempestivi. In questo caso la scelta di localizzare il service in più punti strategici, dal Veneto alla Lombardia alla Sicilia al fine di diminuire il tempo di intervento, si è dimostrata vincente. Anche all’estero garantiamo ai nostri clienti interventi risolutivi e tempestivi grazie a tecnici specializzati nelle nostre sedi dedicate (Stati Uniti e India) e al fianco di distributori e agenti di fiducia in tutto il mondo».
Elena Farina – Comaf
«Sicuramente la situazione particolare che stiamo vivendo non ha facilitato i rapporti personali, interventi tecnici inclusi. Le richieste di intervento in presenza sono spesso state sostituite da richieste di intervento in remoto, tecnologia che in ogni caso aveva già preso piede negli anni precedenti. I collegamenti online sono sempre veloci e si può aiutare rapidamente il cliente in qualsiasi situazione. Il particolare momento ha portato all’adozione da parte della clientela di connessioni Internet sempre più efficienti e a un maggior uso in generale degli strumenti informatici, spostando quindi il cliente a una maggiore consapevolezza di quanto questo tipo di tecnologia possa essere utile e veloce in molti casi. Abbiamo anche notato una maggiore richiesta di qualsiasi tipo di strumento informatico che possa rendere il cliente più indipendente non solo nella fase della produzione, ma anche nella manutenzione».
Silvia Bragagnolo – Asaf
«La situazione attuale non ha influenzato tanto il numero di richieste di intervento quanto la modalità di assistenza presso i clienti e un conseguente aumento degli interventi da remoto. La pandemia da Coronavirus ha infatti accelerato la spinta alla digitalizzazione che era già stata avviata negli anni passati e relativamente alla quale Asaf ha già fatto e continuerà a fare ingenti investimenti, sia dal punto di vista di infrastruttura digitale, sia dal punto di vista dell’organizzazione delle proprie attività interne e nella relazione con i clienti. La necessità di distanziamento interpersonale e la difficoltà dei trasferimenti delle persone ha reso ancora più fondamentale investire in tecnologia per rendere possibili, in maniera virtuale, alcuni processi che prima erano eseguiti spostando le persone e le loro competenze. Attraverso sistemi di streaming e di realtà virtuale abbiamo collegato in remoto i nostri tecnici con i clienti, rendendo possibile installare e servire a distanza le nostre macchine. L’impatto delle tecnologie informatiche in questo periodo è diventato talmente forte da avere generato un cambiamento profondo e irreversibile delle nostre normali abitudini».
Pierluigi Vaghini – Amada
«La situazione che stiamo affrontando ha portato tutti i costruttori a dover essere più reattivi, soprattutto quando si parla di service. Da questo punto di vista noi partivamo avvantaggiati poiché abbiamo a disposizione una piattaforma composta da un hardware chiamato VC-Box e dal software My V-Factory, che oltre a permettere l’integrazione delle macchine nella rete aziendale, favoriscono le attività di assistenza da remoto. Questi strumenti consentono alle aziende di tenere sotto controllo, in modo semplice e immediato, il proprio ciclo produttivo, fornendo i KPI istante per istante. In aggiunta permettono al personale tecnico di Amada che si occupa del service, di accedere da remoto all’impianto per effettuare una serie di interventi di diversa natura. Ad esempio, i nostri tecnici possono gestire direttamente i parametri di taglio, oppure possono dare suggerimenti al cliente in merito a come migliorare la produttività dell’intero sistema. Inoltre, attraverso il monitoring continuo reso possibile dai sensori di cui sono dotati gli impianti, c’è la possibilità di capire in anticipo se la macchina ha necessità di determinati interventi, aprendo così la strada alla manutenzione predittiva. Tutto questo permette alle aziende di mantenersi operative e di evitare il più possibile interventi on-site da parte del nostro personale».
Condividi l'articolo
Scegli su quale Social Network vuoi condividere