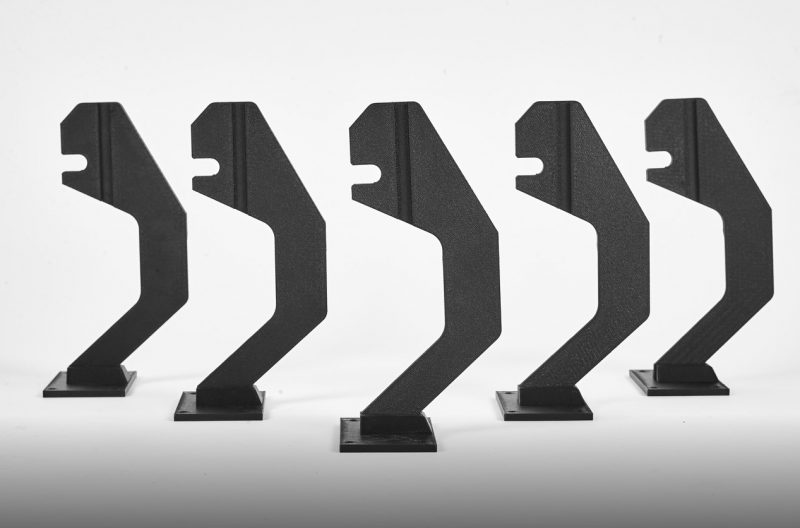
La capacità di stampare in 3D su richiesta le parti di ricambio dei macchinari ha ridotto notevolmente i tempi di inattività delle macchine, garantendo continuità nella linea di produzione.
Stratasys, azienda ai vertici globali nelle soluzioni di tecnologia additiva applicata, ha annunciato che l’agenzia di servizi Dutch 3D, Visual First, utilizza la termoplastica caricata con fibre di carbonio FDM Nylon 12CF per sostituire le parti metalliche della macchina per il suo cliente The Chocolate Factory. L’azienda ha sede a Rotterdam nei Paesi Bassi e utilizza una rete di macchinari per il confezionamento. La produttività dell’azienda dipende dal corretto funzionamento di una parte metallica a forma di gancio, semplice e allo stesso tempo fondamentale, che solleva i fasci di barre sul nastro trasportatore. Quando la parte non funziona correttamente, si verifica un problema, in genere a scadenza regolare, per cui deve essere sostituita tre volte al mese. Dal momento che ogni parte di ricambio viene realizzata a mano, la consegna può richiedere oltre un mese.
«È essenziale che la macchina per il confezionamento sia sempre operativa, specialmente nei periodi movimentati», ha spiegato a ridosso delle recenti ferie natalizie Carl van de Rijzen, titolare d’azienda di Visual First. «Grazie alla fabbricazione additiva di Stratasys possiamo produrre su richiesta parti di ricambio personalizzate caratterizzate dalle stesse prestazioni delle parti metalliche. Siamo in grado di stampare in 3D e fornire le parti di produzione a The Chocolate Factory in meno di una settimana, e questo è fondamentale per garantire la continuità della linea di produzione». L’azienda utilizza il materiale composito FDM Nylon 12CF ad alte prestazioni di Stratasys, un termoplastico caricato in carbonio, contenente il 35% di fibra di carbonio. Prodotta con la stampante Stratasys 3D della serie Production Fortus 450mc, la parte di ricambio della macchina, stampata in 3D, attualmente viene utilizzata in fabbrica. Secondo van de Rijzen, il team di The Chocolate Factory è sorpreso dall’elevato rapporto rigidità/peso della termoplastica FDM Nylon 12CF, che consente di ottenere parti caratterizzate da un’estrema rigidità. «Il successo della parte stampata in 3D è stato subito chiaro dal momento che è impossibile piegare il materiale», ha aggiunto van de Rijzen. «La parte ha superato tutti i test sulla macchina e sono stati completati diversi cicli senza incidenti. Con la sostituzione della parte metallica con la nostra versione stampata in 3D, la fabbrica è riuscita ad aumentare la produttività».
In precedenza, il costante intervento dell’uomo indicava un funzionamento non ottimale della parte metallica, per cui la macchina si danneggiava con frequenza. «Ora, grazie alla capacità di ottimizzare il design della parte con la stampante Fortus 450mc, la situazione è migliorata, in quanto la parte è molto più leggera dell’omologo componente in metallo», ha spiegato van de Rijzen. «The Chocolate Factory ha osservato anche dei vantaggi in termini economici, dal momento che il team ha segnalato una riduzione dei costi relativi alla parte pari al 60%».
Dopo il successo della parte di ricambio stampata in 3D, The Chocolate Factory si rivolge ora a Visual First per risolvere altre sfide legate al design, soprattutto per sviluppare un prototipo di stampo di fusione per testare l’accettazione dei propri prodotti. In genere, questo tipo di stampo è realizzato in plastica, un materiale che richiede molto tempo e costi elevati. «Con gli stampi realizzati in 3D con la stampante Fortus 450mc, l’azienda sarà in grado di accelerare ulteriormente i processi di produzione», conclude van de Rijzen. «Stiamo assistendo alla crescita della domanda di parti di produzione e parti di ricambio stampate in 3D per le macchine industriali, in particolare per le macchine per imballaggio», chiosa infine Nadav Sella, capo della business unit per le nuove soluzioni di Stratasys. «Queste macchine richiedono un livello elevato di personalizzazione, legato alla grande varietà di prodotti che vengono sottoposti al processo di imballaggio. In molti casi, l’uso della fabbricazione additiva consente non solo di risparmiare su tempi e costi durante la fabbricazione di tale macchinario, ma permette anche di rendere queste macchine più efficienti grazie alla riduzione del peso, alla semplificazione del design e alla maggiore funzionalità».
Condividi l'articolo
Scegli su quale Social Network vuoi condividere