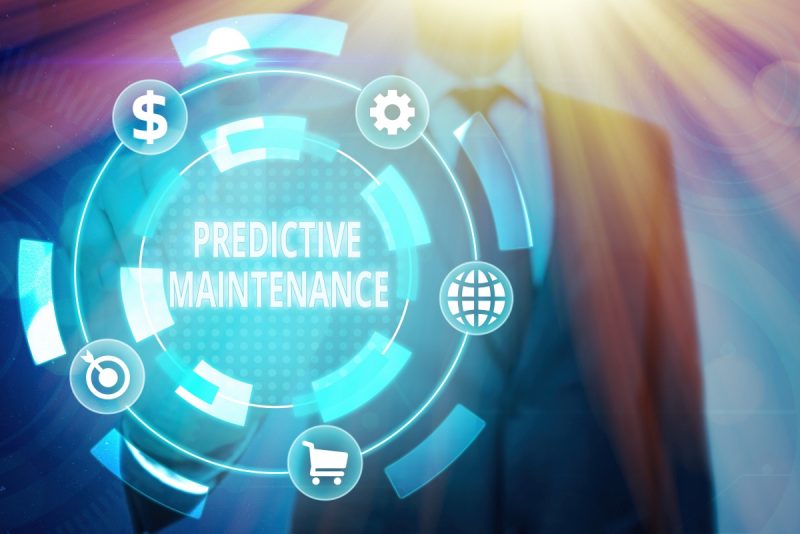
Il contesto competitivo in cui opera l’industria manifatturiera impone un’organizzazione sempre più efficiente, con impianti che funzionano sempre al meglio e senza fermi macchina. Le soluzioni IIoT (Industrial Internet of Things) sono fondamentali per consentire la trasformazione della fabbrica in smart factory: sono ben conosciute dalla quasi totalità delle grandi aziende e messe in pratica dalla maggior parte di queste realtà. Per le PMI va ancora recuperato un certo ritardo, ma la pressione in tal senso è forte: i benefici in termini di efficienza sono indubbi, mentre non vanno sottovalutate le ricadute positive dal punto di vista dell’immagine aziendale.
Manutenzione predittiva e manutenzione preventiva: la chiave del successo
Fra gli aspetti prioritari per l’evoluzione delle realtà produttive in chiave 4.0 rientrano a pieno titolo la manutenzione predittiva e la manutenzione preventiva: permette agli impianti di funzionare sempre al meglio, evitando i lunghi e onerosi fermi macchina che un’azienda competitiva non si può più permettere. Interiorizzare la cultura dell’industria 4.0 e accettare la necessità di effettuare gli investimenti relativi diventano requisiti essenziali per modernizzare l’industria manifatturiera, migliorando l’efficienza e la competitività del comparto.
Dal punto di vista economico le agevolazioni fiscali aiutano, mentre sotto il profilo tecnico un valido supporto viene dalla componentistica intelligente, in grado di monitorare e di comunicare eventuali anomalie nel processo produttivo al loro verificarsi: eccesso di vibrazioni, temperature anomale, aumento dell’assorbimento di energia sono fattori che possono indicare una diminuzione dell’efficienza. Questi dati, raccolti, analizzati e archiviati in grandi quantità dagli impianti moderni, permettono di intervenire tempestivamente, anche da remoto, sui parametri di funzionamento per garantire uno svolgimento sempre ottimale del processo produttivo.
Interconnettere la meccanica con il software, la digitalizzazione e l’intelligenza artificiale è sempre più importante per trasformare gli impianti consentendo il controllo della qualità e le operazioni di manutenzione.
I giunti R+W AIC con sensoristica integrata
R+W, multinazionale tedesca che progetta e produce giunti di precisione e trasmissioni per l’industria, ha sviluppato nuove linee di giunti con sensoristica integrata per contribuire all’evoluzione delle fabbriche verso il modello 4.0.
Fin dal loro debutto sul mercato dei componenti, i giunti AIC (acronimo di Artificial Intelligence Coupling) con sensoristica integrata hanno riscosso un notevole interesse: la possibilità di misurare grandezze rilevanti per l’efficienza del processo direttamente della trasmissione è una novità che porta indiscutibili vantaggi a progettisti e aziende di produzione. Ma come è partito e come si è evoluto il progetto che ha portato a questi giunti?
Lo abbiamo chiesto all’ing. Sascha Markert, che ha sviluppato il prodotto all’interno di R+W.
Quando avete capito per la prima volta che il mercato aveva bisogno di un giunto con sensoristica integrata? Ha ricevuto una richiesta esplicita da parte dei clienti o è stata un’intuizione da parte vostra?
Quando R+W ha avuto per la prima volta una visione sulla misurazione della coppia all’interno di un giunto eravamo nell’ormai lontano 2008. Si è rivelata però un’idea troppo in anticipo rispetto ai tempi, perché i sistemi di comunicazione wireless ad alta efficienza energetica non erano ancora disponibili all’epoca.
C’è sempre stata una domanda indiretta da parte del mercato per la miniaturizzazione dei macchinari, finalizzata al risparmio energetico. Abbiamo pensato che se avessimo potuto integrare la misurazione della coppia e della velocità nei nostri giunti, avremmo potuto risparmiare peso, rendendo superfluo l’uso di collegamenti a vite e cuscinetti di supporto aggiuntivi.
Quando avete iniziato a progettare il nuovo giunto?
All’inizio del 2019 abbiamo fatto i primi progetti. Più tardi nello stesso anno abbiamo costruito i primi prototipi per i test interni. Nel 2020 abbiamo spedito i primi prototipi con una fonte di energia a batteria per i collaudi sul campo, per testare la misurazione della velocità e della coppia e i componenti software e hardware.
A causa della elevata richiesta di prove continue abbiamo sviluppato i prototipi di apparecchiature per la ricarica a induzione nella seconda metà del 2020.
I primi progetti di impianti produttivi che utilizzano giunti con ricarica a induzione diventeranno operativi nel primo trimestre 2021.
Successivamente si verificherà un congelamento del progetto per preparare la produzione in serie.
La tecnologia AIC può essere integrata in qualsiasi giunto, ma qual è stato il primo tipo di giunto in cui avete inserito dei sensori? C’era una ragione specifica per questa scelta?
Il primissimo giunto con sensori è stato un albero di trasmissione di tipo ZAE. Poiché l’albero di trasmissione ZAE presenta un tubo di alluminio come collegamento tra gli elementi elastici, era chiaro per noi che questo era il più semplice da utilizzare: era già disponibile tutto lo spazio necessario all’inserimento della sensoristica.
Esiste una linea di produzione dedicata per i giunti AIC o vengono prodotti utilizzando le stesse linee che producono le versioni non AIC dei giunti?
Nelle fasi iniziali stiamo utilizzando la linea di produzione non-AIC, ma se ci sarà un aumento delle vendite potremmo decidere passare a una linea di produzione dedicata.
Quali sono state le reazioni dei primi clienti a cui vi siete rivolti con questa tecnologia? C’è stata qualche difficoltà a convincerli ad accettare questo nuovo paradigma?
Quasi tutti i nostri clienti sono stati contenti di provare qualcosa di nuovo. Il motivo è che il segmento dei giunti è molto lento ad adattarsi alle nuove tecnologie. Poter utilizzare tablet e smartphone per leggere i dati in diretta dalla trasmissione è diventato istantaneamente lo sviluppo preferito dei nostri clienti.
Ora il compito più grande per noi è quello di convincere il cliente che il nostro prodotto è affidabile nel lavoro quotidiano.
Quale percentuale dei giunti che producete e vendete sarà AIC nel prossimo futuro? Quali tipi di giunti pensate che saranno più richiesti nelle loro versioni AIC?
Da quello che vediamo in questo momento gli alberi di trasmissione sono stati una buona scelta per cominciare. Anche i giunti lamellari con distanziatore in acciaio e sensori integrati sembrano adattarsi alle esigenze dei clienti. La compatibilità con i modelli precedenti è un’opportunità molto conveniente per sostituire gli alberi di trasmissione esistenti con i giunti con allunga AIC: diventa così possibile monitorare al meglio i macchinari, anche nei casi in cui prima non era possibile, senza che sia necessario sostituirli.
Un altro esempio è quello di cambiare i mozzi (per adattarsi alle diverse dimensioni di foratura) e mantenere il distanziatore AIC. Questo offre al cliente la flessibilità di raccogliere dati da diverse macchine con un unico distanziatore AIC. La modularità dei nostri giunti offre al cliente una grande flessibilità per utilizzare il giunto AIC in modo efficiente.
Quali industrie stanno dimostrando, o hanno già dimostrato, il maggior interesse per gli accoppiamenti CA?
I banchi prova sembrano essere i candidati perfetti per i nostri giunti AIC. Il nostro giunto AIC si inserisce come soluzione snella, riducendo la necessità di utilizzare cuscinetti e supporti aggiuntivi.
Uno dei nostri clienti sta costruendo macchine per estrusori dove è installato solo un giunto. Sa quanta potenza entra nella macchina ma non sa cosa succede nel canale dell’estrusore. Vuole sostituire il giunto esistente con un limitatore di coppia collegato ad un giunto a disco con tecnologia AIC. In questo modo avrà la possibilità di osservare il comportamento dell’estrusore nel tempo per ottenere una migliore comprensione del processo.
Condividi l'articolo
Scegli su quale Social Network vuoi condividere