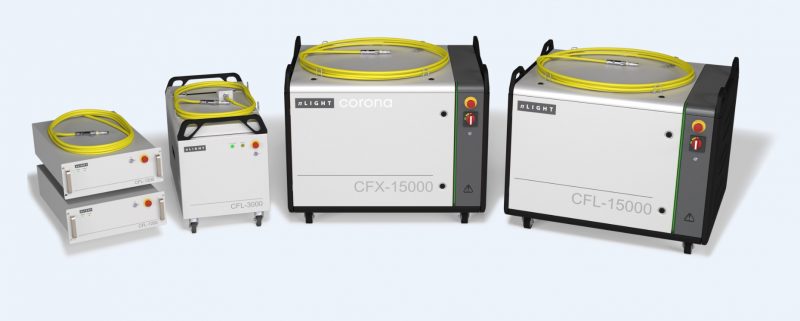
Grazie al beam shaping, la tecnologia che permette di modificare la distribuzione di energia del profilo del fascio laser, le sorgenti laser fibra nLIGHT (di cui Optoprim è distributore ufficiale in Italia) permettono di eseguire saldature ottimali in ogni applicazione.
di Davide Davò
Da diversi anni i propulsori delle automobili vengono saldati con la tecnologia laser, inizialmente con il CO2 e successivamente anche con laser YAG a stato solido, soprattutto da quando quest’ultima tecnologia è diventata più competitiva in termini economici. «Ma non in termini di prestazioni – esordisce Brian Victor, direttore della Divisione Applicazioni Industriali di nLIGHT che ha sede a Vancouver, nello stato di Washington (USA) – perché i laser YAG producono più schizzi (sputter) rispetto ai laser CO2, e questo è uno dei motivi per cui i laser fibra in passato non venivano utilizzati per queste applicazioni di saldatura. Soltanto di recente, con l’avvento del beam shaping, anche questi laser sono entrati a far parte dell’arena della saldatura dei propulsori». L’espressione “beam shaping” è stata utilizzata per descrivere sia il modellamento dello spot del laser attraverso l’uso di ottiche sia per il modellamento della distribuzione di energia (o del modo) del profilo del fascio. Ed è proprio quest’ultima declinazione che ha ampliato le applicazioni dei laser in fibra e in particolare proprio nella saldatura dei propulsori.
Modifica del profilo
In realtà cambiare il profilo della distribuzione di energia di un fascio laser non è una novità in senso stretto. Un modo a ciambella, o ad anello, concentra l’energia verso il perimetro del fascio, mentre nel modo Gaussiano l’energia si concentra nel centro del fascio. Da anni i laser CO2 permettono di ottenere tali profili, e proprio questa la capacità è stata uno dei maggiori vantaggi del laser CO2. «Fare la stessa cosa con i laser fibra è stata una sfida complessa», commenta Victor. Un duro lavoro che ha dato i suoi frutti: oggi con l’approccio di nLIGHT, di cui Optoprim e distributore ufficiale in Italia, si puo variare la distribuzione di energia del fascio all’interno della fibra di delivery del laser.
Confronto tra applicazioni
Quando si tratta di lamiere convenzionali e altre applicazioni industriali, i produttori generalmente usano un laser in fibra per eseguire una saldatura a conduzione termica oppure una saldatura profonda (keyhole). Tradizionalmente la saldatura a conduzione e caratterizzata da una limitata penetrazione e da velocita ridotte. «Si crea un bagno di saldatura ampio e poco profondo senza generare troppa vaporizzazione», precisa Victor. «L’obiettivo di solito e quello di creare una saldatura pulita ed esteticamente accattivante. Le saldature generalmente sono piu larghe che profonde, e le velocita limitate danno il tempo al calore di essere “condotto”. Nella saldatura a conduzione spesso si utilizza il cosiddetto fascio flat-top. La tipica dimensione dello spot e di 600 μm se non piu grande, ma per saldare a conduzione anche 600 μm sono troppo piccoli. Quindi spesso l’ingegnere di processo si mette in una posizione di fuori fuoco per ottenere uno spot piu grande». Il punto di fuoco del laser e centrato nel suo punto di waist, in cui lo spot e il piu piccolo possibile, muovendo il fuoco lontano dal materiale si colpisce la superficie con un fascio piu grande. In questi casi, solo una parte del fascio in realta fa del lavoro sul materiale. Il resto e solo calore sprecato che viene riflesso dal materiale. Nella saldatura profonda invece si utilizza uno spot del laser in fibra piu intenso per creare nel bagno della saldatura una profonda cavita di vaporizzazione, nota come keyhole. Questo spot piccolo e intenso produce delle saldature con una penetrazione profonda e stretta a velocita piu elevate. «In questo caso si possono trovare spot da 100 μm che creano uno stretto keyhole, perfetto per aumentare penetrazione e velocità – sottolinea Victor – ma il keyhole stretto può diventare instabile, generare sputter e irregolarita superficiali, a seconda della lega che si sta saldando». Quando il keyhole diventa instabile, il metallo liquido intorno al bordo della cavita collassa verso l’interno e quasi chiude la cavita stessa prima che l’energia del laser vaporizzi il metallo permettendo al keyhole di formarsi nuovamente. Il metallo liquido che ha quasi chiuso la cavita viene espulso verso l’esterno e questo produce una saldatura instabile con sputter e una penetrazione inconsistente.
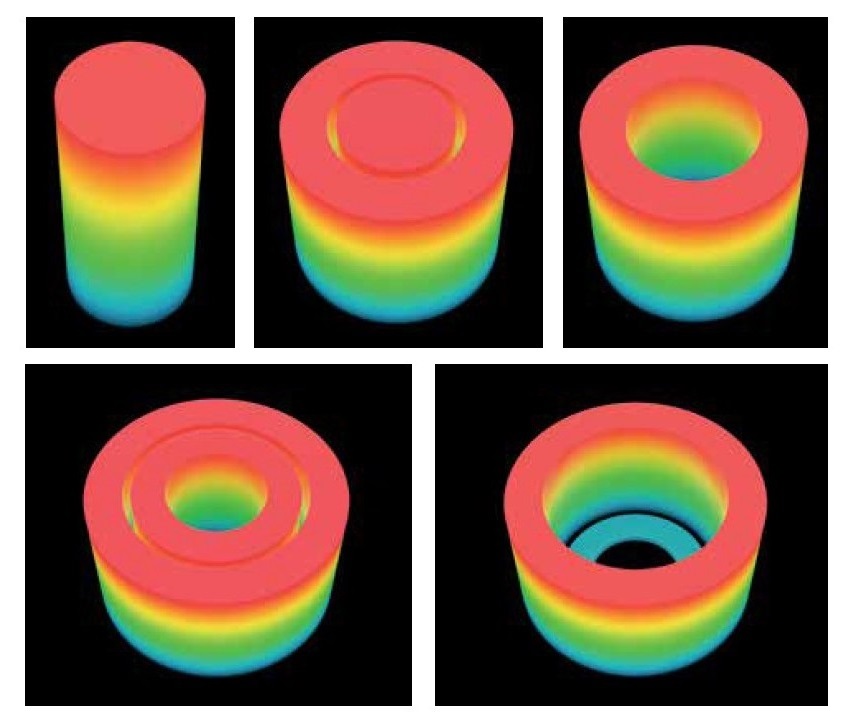
La forma del fascio
Il beam shaping e una tecnologia di estrema importanza, poiché offre un nuovo modo di lavorare agli ingegneri che in passato potevano modificare i parametri di saldatura intervenendo solo sulla velocita, oppure utilizzando varie ottiche. Nell’approccio di nLIGHT, attraverso il suo laser in fibra con tecnologia Corona (a fascio programmabile), la sezione trasversale della fibra di delivery ha tre regioni: un core interno circondato da una sezione intermedia e da una esterna. Il core centrale ha un diametro di 100 μm, mentre le due regioni piu esterne permettono di modificare il diametro del fascio fino a 350 μm. Semplificando, la fibra di delivery ha due “guaine” interne che ridistribuiscono l’energia che emerge dalla sorgente laser. Queste regioni consentono al laser di sintonizzare il suo profilo energetico per soddisfare le esigenze dell’applicazione. Secondo Victor, la possibilità di tale tuning consente di utilizzare laser in fibra per saldature a conduzione senza defocalizzare il fascio. Il diametro del fascio risultante è più piccolo del tipico raggio defocalizzato flat-top, ma potendo usufruire di uno spot a fuoco, la maggior parte dell’energia del fascio viene effettivamente utilizzata per la saldatura. Con l’energia distribuita non solo nel core centrale ma anche nella sezione intermedia e nella sezione esterna del fascio, si possono ottenere dei cordoni di saldatura lisci con penetrazioni superficiali, proprio come richiesto da una saldatura a conduzione. Per la saldatura profonda, diversi profili di energia (o diverse “forme” di fascio) aiutano a stabilizzare il keyhole. La forma più adeguata da dare al profilo dipende dall’applicazione, dalle caratteristiche di fusione del materiale e dalla viscosità del metallo fuso. Con un’alta viscosità infatti si riesce a preservare il muro del keyhole anche con un fascio Gaussiano, ma un metallo che fonde in un materiale più fluido potrebbe formare una parete del keyhole meno stabile a parità di fascio. Ma aumentando l’energia del fascio che viene distribuita alle regioni intermedia ed esterna, avvicinandosi quindi a un profilo ad anello, anche il diametro del keyhole aumenta, e il metallo liquido circostante viene vaporizzato o scorre uniformemente intorno al keykole rendendolo più stabile.
Versatilità d’impiego
Il beam shaping delle sorgenti con tecnologia Corona fornisce decine di diversi profili di fascio, ciascuno dei quali può essere adatto per una particolare applicazione. È dunque possibile adottare un profilo che concentra il 90% della sua energia nel core e solo il 10% negli anelli più esterni per saldare leghe inossidabili che mostrano un keyhole stabile, mantenendo una cavità stretta, una penetrazione profonda ed una maggiore velocità di saldatura, per poi passare subito dopo a un modo con l’80% dell’energia nel core centrale ed il 20% nei ring più esterni per saldare l’alluminio o il rame, entrambi con un materiale fuso molto fluido e capace di compromettere l’integrità del keyhole. Con questa tecnologia, il profilo del fascio può cambiare anche durante il processo tramite un controllo digitale. Quindi l’inizio e la fine di una saldatura potrebbero avere diversi modi del fascio rispetto a quello utilizzato a metà del ciclo di saldatura. Ad esempio, un pezzo potrebbe richiedere sia una saldatura keyhole sia una saldatura a conduzione. In passato questo avrebbe richiesto una configurazione completamente nuova, ora è possibile passare da una tipologia di saldatura all’altra real-time. «Avere un fascio programmabile ci da una capacità maggiore di colmare alcune lacune presenti nella saldatura laser», sostiene Victor. «Ma c’è comunque un limite teorico: quello che ha avuto successo per decenni nella saldatura laser è tutt’ora valido». Come sempre, una migliore “vestibilità” porta a migliori risultati. Anche in questo caso, lo shaping del fascio offre agli ingegneri della saldatura un’altra variabile da controllare, che a sua volta apre a nuove possibilità di processo. «Diciamo che una cella di saldatura può prevedere importanti cambi di applicazione che coinvolgono diversi materiali, geometrie di giunto e requisiti di velocità», prosegue Victor. «Se stai sviluppando un processo con una fibra standard e una testa di saldatura fissa, storicamente le uniche variabili che ti restano da modificare sono la velocità e la potenza. Ma con un fascio programmabile hai un’altra variabile e questo potrebbe evitarti di riprogettare l’intero hardware per modificare la configurazione della cella di saldatura». In generale, il beam shaping è sempre più richiesto da diversi settori della lavorazione dei metalli, anche nel settore del taglio laser. I laser in fibra con fascio programmabile ora possono tagliare con maggior qualità spessori sempre maggiori (utilizzando un modo a ciambella quando si taglia con ossigeno), e spessori più sottili con maggiore velocità rispetto a una sorgente di pari potenza senza possibilità di modificare la forma del fascio. Questa tecnologia è stata utilizzata anche nel trattamento termico e persino nel metal additive manufacturing. «Questo è ciò che rende il beam shaping del laser in fibra così strepitoso», conclude Victor. «Di fatto sta aprendo una serie di applicazioni che solo 10 anni fa non ci saremmo mai sognati di affrontare».
Condividi l'articolo
Scegli su quale Social Network vuoi condividere