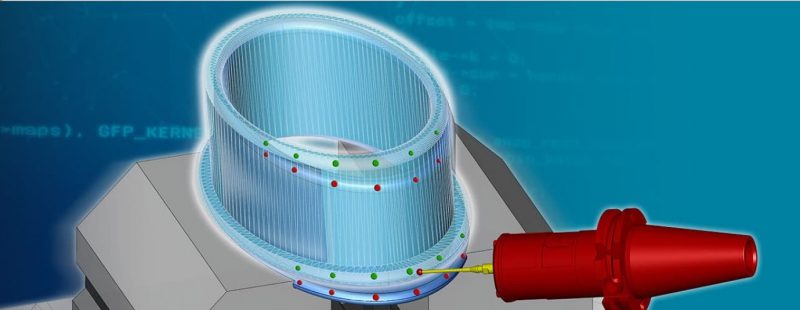
In una produzione del tutto automatizzata e interconnessa, mondo fisico reale e mondo digitale virtuale dialogano e collaborano a creare scenari e ambienti in cui la precisione e la previsione del risultato finale sono sempre più perfetti
È in questo mondo che trova il suo impiego hyperMILL BEST FIT offrendo scenari di posizionamento dei pezzi in macchina controllati e corretti virtualmente prima dell’avvio della produzione.
Perché virtualizzare la messa in macchina si rivela così importante e per certi versi rivoluzionario?
In ambito di produzione attraverso le macchine a Controllo Numerico, virtualizzare la messa in macchina consente di prevenire e correggere situazioni che da anni sono così “normali” da essere ormai date per scontate e non risolvibili.
Con hyperMILL BEST FIT è possibile definire l’orientamento intelligente del componente premendo semplicemente un tasto per far combaciare le parti da stampare e recuperare gli errori con precisione.
In pratica si realizza una integrazione completa tra l’ambiente fisico della macchina e quello virtuale della simulazione: la posizione effettiva della parte da lavorare viene simulata in modo virtuale, corretta attraverso il calcolo del percorso utensile dinamico per sistemare eventuali errori di posizionamento.
hyperMILL BEST FIT riesce, quindi, a calcolare in anticipo la deviazione del pezzo, valore che difficilmente l’utente CAM potrebbe conoscere a priori, e fa una selezione dinamica del percorso utensile, verificandolo con operazioni di tastatura e portando il valore di errore vicino allo zero.
Con il modulo hyperMILL PROBING, infatti, si possono fare analisi sulla macchina CNC
per programmare processi di tastatura e di verifica sulla macchina utensile, riducendo i tempi di lavorazione e garantendo al contempo la qualità dei componenti.
Le funzionalità di hyperMILL BEST FIT
- Orientamento rapido e sicuro del componente in CAM in tempo reale
- Simulazione della posizione effettiva del componente nella macchina virtuale
- Generazione del codice NC in base alla posizione effettiva del componente
- Compensazione automatica dei limiti macchina e delle collisioni
hyperMILL BEST FIT elimina tutte le imprecisioni del componente sulla macchina
Anche voi avete riscontrato questo problema in produzione? Il grezzo o il componente vengono orientati in modo accurato dall’operatore, ma alla fine la posizione non è mai corretta.
In una situazione in cui i clienti richiedono che i pezzi siano fresati in tempi sempre più brevi e con una precisione sempre maggiore con hyperMILL BEST FIT vengono eliminate tutte le imprecisioni relative a questa fase critica.
Grazie ad una tastatura 3D, il componente non orientato viene analizzato sulla macchina e i punti di misura vengono inviati nuovamente al sistema CAM sotto forma di un protocollo di misura. Successivamente, hyperMILL BEST FIT adegua il codice NC esattamente alla posizione reale del componente. È il mondo virtuale (programmazione) che viene quindi allineato al mondo reale (staffaggio). Il codice NC simulato nella macchina virtuale in uno scenario di staffaggio reale risulta automaticamente ottimizzato. Per garantire una lavorazione sicura e precisa, la sonda di misura esegue poi una tastatura di controllo. Successivamente può avviare la lavorazione senza dover pensare a orientare il componente sulla macchina. I vantaggi? Enorme risparmio di tempo, lavorazione in sicurezza e processi pianificabili.
Come utilizzare al meglio hyperMILL BEST FIT
Sicuramente si tratta di una funzionalità molto utile per chi esegue lavorazioni di carpenteria, o per i settori automotive e aeronautica.
Si utilizza principalmente per la forgiatura, la saldatura o per la produzione attraverso l’additive manufacturing, ad esempio nei settori medicale o nel motorsport.
La rilavorazione di componenti fabbricati con processo additivo è un’applicazione importante della nuova funzione hyperMILL BEST FIT.
Da così senza hyperMILL BEST FIT
La procedura standard prevedeva fino ad oggi di adeguare il grezzo e lo staffaggio della macchina alle condizioni del programma NC. Il componente veniva orientato servendosi di comparatore, cicli di controllo e una buona dose di sensibilità manuale. Veniva adattato il piazzamento reale allo scenario virtuale della programmazione. Questo lungo processo doveva essere spesso ripetuto più volte e poteva essere causa di imprecisioni. Con hyperMILL BEST FIT l’orientamento del componente nel CAM avviene in tempo reale. Grazie al ciclo di misura 3D, viene analizzato il componente non orientato sulla macchina, inviando poi il protocollo di misura all’interfaccia CAM. hyperMILL BEST FIT adegua il codice NC alla posizione reale del componente
A nessuna modifica manuale in macchina
Molteplici i vantaggi grazie a hyperMILL BEST FIT
- Lavorazione sicura
- Non sono necessari staffaggi/strumenti di misura complessi
- Tempi di attrezzaggio e processi pianificabili
- Tempi di lavorazione ridotti
- Tecniche di staffaggio non più necessarie
- Progettazione semplificata → Geometrie ausiliarie non necessarie
- Adeguamento al sistema di controllo non più necessario
- Semplicità nel cambio macchina
Come sottolineato da Alberto Basilico, Application Engineer di OPEN MIND Technologies Italia,
“hyperMILL BEST FIT non modifica l’origine nel sistema di controllo e permette di creare percorsi utensile al 100% privi di collisioni.”
Condividi l'articolo
Scegli su quale Social Network vuoi condividere