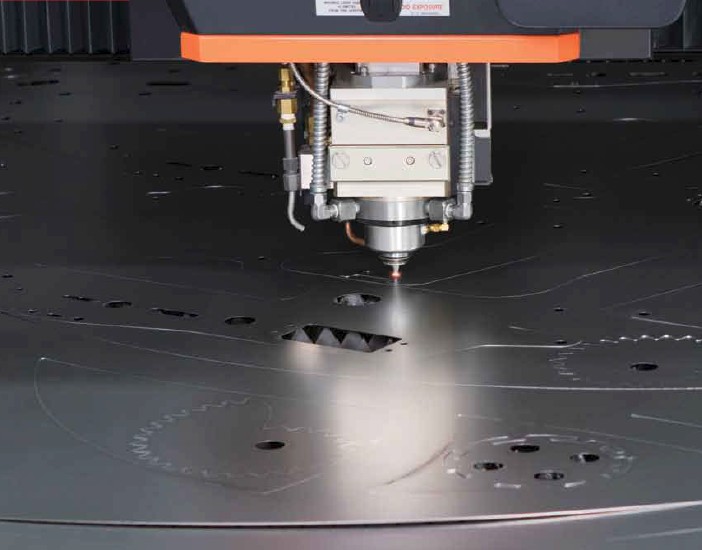
Da piccola realtà contoterzista nel campo del taglio lamiera ad azienda strutturata con processi produttivi automatizzati e flessibili, Metalpunto è cresciuta nel tempo grazie agli impianti laser Yamazaki Mazak
Professionalità, voglia di crescere e di ricavarsi il proprio spazio in un mercato complesso come quello di oggi, oltre a tanta passione nella realizzazione di prodotti dall’alto livello qualitativo. Sulla base di queste premesse è sorta alla fine degli anni Ottant la Metalpunto, che grazie ai suoi fondatori Gianni Casarotto e Rinaldo Cason ha saputo crescere e strutturarsi passando da piccola realtà impegnata nella lavorazione di lamiere sottili, destinate al settore dell’illuminazione, a società in grado di soddisfare le esigenze di qualsiasi campo applicativo, dall’agricolo all’automotive fino al navale, fornendo un servizio completo che va dalla progettazione alla realizzazione dei pezzi finiti destinati ad aziende di tutta Italia e, indirettamente, a società estere.
All’interno dello stabilimento di Castel Goffredo (MN) una ventina di dipendenti si occupa della gestione dell’ufficio tecnico, dove vengono progettate macchine complete o soluzioni di carpenteria in generale, e del reparto di produzione, dotato di quasi tutte le tecnologie per la lavorazione della lamiera: taglio laser, presse, pressopiegatrici, calandre, satinatrici e sistemi di saldatura all’avanguardia.
Crescita continua
Con l’incremento nel tempo dei volumi di produzione a seguito dell’acquisizione d’importanti commesse, Metalpunto ha operato una riorganizzazione dei processi che la porta oggi a porsi sul mercato come una realtà capace di coniugare qualità della lavorazione, flessibilità e capacità di rispondere in tempi rapidi alle richieste dei clienti attivi nei più svariati settori applicativi. La prima vera svolta per l’azienda è avvenuta nel 1992, quando Casarotto e Cason hanno partecipato a una fiera di settore a Milano, avendo l’occasione di vedere personalmente un sistema di taglio laser 2D proposto da Yamazaki Mazak. «Siamo rimasti subito affascinati da una tecnologia così differente da quelle utilizzate al tempo da noi e dai nostri competitor e al rientro dalla manifestazione, dopo una visita nell’allora sede italiana di Yamazaki Mazak a Gallarate (VA), ci siamo convinti che quella del taglio laser era la strada giusta», ha raccontato Casarotto. «Abbiamo quindi acquistato una Super Turbo-X 510 Super Charger PK, che da subito s’è rivelata un prodotto eccezionale e affidabile, permettendoci di portare a compimento molte importanti commesse anche dal comparto dell’agricoltura e della manifattura delle calze (attività principale, per anni, della nostra zona). In breve tempo abbiamo triplicato la produzione, con un livello qualitativo altissimo». Era l’inizio di un percorso intrapreso con l’azienda nipponica che sarebbe proseguito nel tempo fino ad arrivare ai giorni nostri, consolidando un reciproco rapporto di fiducia che ha permesso a Metalpunto di svilupparsi ulteriormente, riuscendo ad approcciare con successo nuovi settori che, diversamente, avrebbe gestito con grande difficoltà. Visti i positivi risultati ottenuti in poco tempo con la Super Turbo-X 510 Super Charger PK, l’anno successivo è stato installato un secondo impianto laser, a cui ha fatto seguito nel 1998 un terzo impianto con cella automatizzata di carico/scarico. In meno di 6 anni, dunque, il parco macchine è cambiato in maniera sostanziale, dando il via a una strategia aziendale che vede ancora oggi un aggiornamento continuo degli impianti, al fine di rimanere sempre al massimo livello tecnologico possibile. Un’importante svolta per Metalpunto però è coincisa con l’apertura nel 2000 di un nuovo capannone a Castel Goffredo e, nello stesso periodo, con l’inserimento del magazzino automatico da 168 pallet nella catena produttiva, che oggi serve due linee di impianti.
Partnership di successo
«In occasione di una visita che ho effettuato nel 1998 presso lo stabilimento giapponese di Yamazaki Mazak, che già all’epoca era organizzata come Smart Factory, ho fatto tesoro di quanto ho potuto osservare, prendendo interessanti spunti per l’organizzazione del sito produttivo che avremmo realizzato due anni più tardi» ha spiegato inoltre Casarotto. «L’evoluzione aziendale è poi proseguita con l’ottimizzazione dei processi produttivi, grazie anche a un sistema di sorting automatico implementato nel 2006 che ci permetteva di fare una separazione del tagliato dallo sfrido in maniera efficiente, garantendo così una movimentazione più performante e una gestione attenta della produttività. Il tutto giustificato da lotti di produzione che diventavano via via più corposi. Si tratta di commesse che abbiamo potuto accettare grazie alla produttività unita alla qualità del taglio offerte da macchine sempre più avanzate dal punto di vista tecnologico. Attualmente disponiamo di due impianti CO2, uno dei quali stand alone mentre l’altro è inserito insieme a un laser fibra a diodo diretto (DDL) all’interno di due diverse linee di produzione, entrambe asservite dal magazzino automatico».
Oggi, dunque, Metalpunto è in grado di gestire lotti importanti così come piccole produzioni grazie alla grande flessibilità garantita dagli impianti Yamazaki Mazak l’ultimo dei quali è l’innovativa Optiplex 3015 DDL con potenza da 4 kW capace di abbinare alta efficienza e qualità del taglio elevata. La decisione di installare questo impianto è legata alla volontà di affrontare le sfide del mercato con una tecnologia di nuova generazione e molto efficiente. Una strada che Metalpunto ha intrapreso basandosi anche sul rapporto di fiducia consolidato negli anni con il costruttore giapponese. La Optiplex 3015 DDL installata di recente ha permesso alla realtà mantovana di ottimizzare i tempi delle lavorazioni e rispondere con grande dinamicità alle diverse richieste del settore.
Prestazioni sotto controllo
Dotato di performance di alto livello in termini di dinamica, con una velocità di rapido in X e Y di 120 m/min, il nuovo impianto a diodo diretto è in grado di mantenere elevate precisioni di posizionamento sugli assi e di ripetizione per ogni singola lavorazione. «L’introduzione nel nostro reparto produttivo della tecnologia DDL ci permette di tagliare i materiali sottili con una velocità del 20% maggiore rispetto alle soluzioni di cui disponevamo in precedenza, e di processare spessori maggiori mantenendo sempre la massima qualità superficiale. All’incremento della velocità di taglio ha contribuito anche il risonatore laser a diodo diretto che genera un raggio con lunghezza d’onda corta, mentre il sistema Multi-Control Torch e un’ampia dotazione di funzioni intelligenti abbinano l’efficienza della macchina alla migliore operatività e semplicità d’uso, a beneficio dei nostri operatori», ha commentato ancora Casarotto. «L’impianto vanta inoltre un sistema di cambio ugelli automatico con integrato un modulo di pulizia dell’ugello stesso, un controllo automatico della lunghezza focale, un sistema di evacuazione sfridi, l’intelligent monitoring del fascio, l’innovativo controllo numerico Preview G e un ampio touch screen da 19” con funzionamento facile e intuitivo, del tutto simile a quello di un normale smartphone o tablet».
Grande soddisfazione dunque da parte di Metalpunto per l’ultima nata del costruttore giapponese, dimostratasi tanto affidabile nel funzionamento in continuo e in non presidiato quanto semplice nell’utilizzo da parte del personale preposto, che comunque ha usufruito anche di una sessione di formazione durante la fase di avviamento e di start-up della macchina al fine di sfruttare al meglio le potenzialità di un sistema dalle alte prestazioni e a elevato contenuto tecnologico.
«Oggi siamo in grado di rivolgerci a un mercato assai ampio e variegato, grazie a una struttura produttiva molto flessibile e automatizzata, coadiuvata da impianti Yamazaki Mazak molto efficienti», ha quindi concluso Casarotto. «Impianti che, al lavoro 24 ore su 24, sono in grado di supportarci nel processo, permettendoci di acquisire una commessa al mattino e consegnare il pezzo finito anche entro sera in base alle necessità o alle urgenze del cliente, mantenendo però invariati gli elevati standard qualitativi che il mercato ci riconosce».
Fondamentale, in questo senso, anche un efficiente servizio di assistenza tecnica post vendita fornito dalla filiale italiana della multinazionale nipponica che, attraverso un primo contatto telefonico e poi eventualmente con l’invio di personale specializzato, è in grado di intervenire in tempi brevi per ripristinare il corretto funzionamento degli impianti, riducendo al minimo i tempi di fermo macchina, sempre più critici per qualsiasi realtà industriale moderna.
Condividi l'articolo
Scegli su quale Social Network vuoi condividere