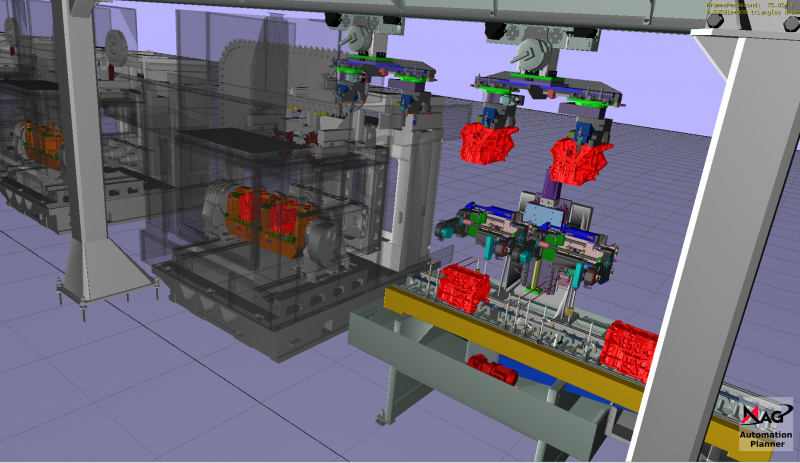
Per rispondere alla crescente domanda di soluzioni personalizzate, i costruttori puntano su sistemi modulari realizzati con nuovi processi di progettazione basati su metodologie fortemente orientate alla simulazione.
Per rispondere alla crescente domanda di soluizioni personalizzate, i costruttori puntano su sistemi modulari realizzati con nuovi processi di progettazione basati su metodologie fortemente orientate alla simulazione.
di Giambattista Gruosso
Una delle sfide più grandi nel panorama industriale è la crescente domanda di prodotti complessi e personalizzati che richiede l’implementazione di nuovi processi di produzione anche essi flessibili. In modo particolare sono le macchine a diventare l’elemento chiave di questa flessibilità: si richiedono, infatti, macchine utensili adattabili e flessibili per prodotti diversi o condizioni di lavoro diverse. Per soddisfare questi requisiti si sta diffondendo sempre di più il concetto di sistemi modulari, facilmente riconfigurabili tanto per i macchinari quanto per i processi.
Tuttavia questa esigenza si scontra con la difficoltà di implementazione di una nuova macchina: durante le prime fasi di progettazione di nuovi processi di produzione né il cliente né il produttore di una nuova macchina utensile conosce l’efficacia risultante della configurazione della macchina utensile scelta. Di conseguenza è necessario implementare nuovi processi di progettazione basati su metodologie fortemente orientate alla simulazione.
Attualmente le ipotesi sono fatte sulla base dell’esperienza maturata o dalla stima attraverso processi simili, ma il futuro è in quello che è riconosciuto come “Virtual Commissioning”. Questa metodologia rappresenta una delle tematiche più sfidanti associata alla Smart Factory, soprattutto se considerato come uno strumento di simulazione avanzata delle macchine e dei processi.
In modo particolare questa metodologia nasce per far fronte a tutti quei contesti i prodotti sono realizzati su commessa, ma può facilmente essere impiegata verso i prodotti di serie. Avere, in tali casi, a disposizione un modello di simulazione della macchina permette al cliente di poter interagire con la progettazione al fine di valutare tutti gli avanzamenti di lavoro e nello stesso tempo poter suggerire modifiche di layout e di funzionalità già in fase di simulazione, senza aver implementato il prodotto.
In quest’ottica la messa in servizio di un macchinario o un processo rappresenta, un passaggio importante della fase di progettazione, in quanto rende evidenti, se ve ne sono, problemi nei sistemi e nei componenti progettati, prodotti ed installati. Ma scoprirlo in questa fase è molto spesso di difficile gestione, pur essendo questa metodologia la pratica comune tra la maggior parte di costruttori di macchinari o processi. Diventa pertanto necessario implementare un nuovo approccio che offra la possibilità di monitorare costantemente la fase di sviluppo prima ancora di giungere alla messa in servizio. I software di simulazione offrono in questo panorama un valido supporto a velocizzare e tracciare tutte le fasi di sviluppo critico del prodotto.
I benefici della simulazione avanzata
Gli obiettivi della simulazione avanzata, nell’ottica di Virtual Commissioning, sono diversi a seconda delle applicazioni e delle strategie di progettazione. Di fatto alla base vi è l’esigenza di una integrazione ottimale della simulazione in quello che è il flusso di lavoro specifico dell’azienda
Volendo sintetizzare alcuni benefici, si possono individuare i seguenti:
– Riduzione del tempo di messa in servizio
– Ottimizzazione dei processi
– Aumento della qualità del software (programmi di PLC e robot)
– Minimizzazione dei rischi
– Validazione delle singole fasi di integrazione
– Controllo dei subappaltatori (meccanici, elettrici e robotica) attraverso la condivisione di modelli
– Delocalizzazione delle attività di costruzione e sviluppo del software in ufficio in modo preventivo.
Ma il Virtual Commissioning non è soltanto una simulazione meccanica o visuale del comportamento del prodotto, della macchina o del processo, è molto di più: permette di simulare anche il controllo meccanico e quello elettronico. Per cui il modello che ne risulta è alter-ego completo della macchina che non solo permette di aiutare in fase di preventivazione e collaudo, ma abilita anche nuove metodologie di sviluppo del software e degli algoritmi. Non si non si tratta altro che costruire un gemello digitale della propria macchina o processo su cui poter fare anche delle analisi e delle considerazioni che sarebbe difficile fare, durante il funzionamento.
L’idea che è alla base di questa visione è quella di connettere un modello digitale del sistema reale direttamente con il controllore reale (e si parta pertanto di Hardware in the loop) oppure con un suo modello di simulazione. Il modello serve a simulare il comportamento del sistema da vari punti di vista e nello stesso tempo permette agli sviluppatori del software di controllo di implementare gli algoritmi prima ancora di avere a disposizione il processo o il macchinario effettivamente assemblato.
Il modello virtuale può essere in questo modo messo in relazione alla macchina reale tenendo conto della geometria, della struttura cinematica e delle sue prestazioni. La specifica simulazione della macchina non riguarda solo il modello virtuale, ma anche la simulazione del sistema di controllo.
Più di una simulazione
Si diceva che questo abilita molto di più che una simulazione: è la creazione dell’era dei Digital Twins o gemelli digitali. In altre parole, i gemelli digitali vengono creati nel stesso software CAD di modellazione che progettisti e ingegneri utilizzano nelle prime fasi di sviluppo del prodotto con la differenza che il gemello digitale viene conservato anche per fasi successive del ciclo di vita del prodotto, ad esempio per verifica e manutenzione.
Il concetto del gemello digitale richiede tre elementi: l’esistenza di un prodotto fisico nello spazio reale, un suo gemello digitale nello spazio virtuale e le informazioni possono essere collegate. I sensori collegati al prodotto fisico sono infatti in grado di raccogliere dati e inviarli al gemello digitale, e la loro interazione può aiutare a ottimizzare le prestazioni del prodotto. Ad esempio, sensori potrebbero rilevare quando l’olio motore di un’auto ha bisogno di essere cambiato, ed il doppio digitale della vettura potrà fare delle analisi sulla base di queste nuove informazioni indica le nuove informazioni, che possono essere visualizzati su uno smartphone o integrati in un sistema PLM del produttore. Ed il concetto di gemello può essere esteso anche alle linee di assemblaggio e altri sistemi di fabbrica.
Il futuro che ci aspetta è quindi molto interessante e ricco di sorprese, ma apre la strada ad una nuova era di approfondimenti e di studi per sfruttare al meglio le potenzialità di quanto la tecnologia può offrirci.
Giambattista Gruosso è professore presso il Dipartimento di Elettronica, Informazione e Bioingegneria del Politecnico di Milano
Condividi l'articolo
Scegli su quale Social Network vuoi condividere