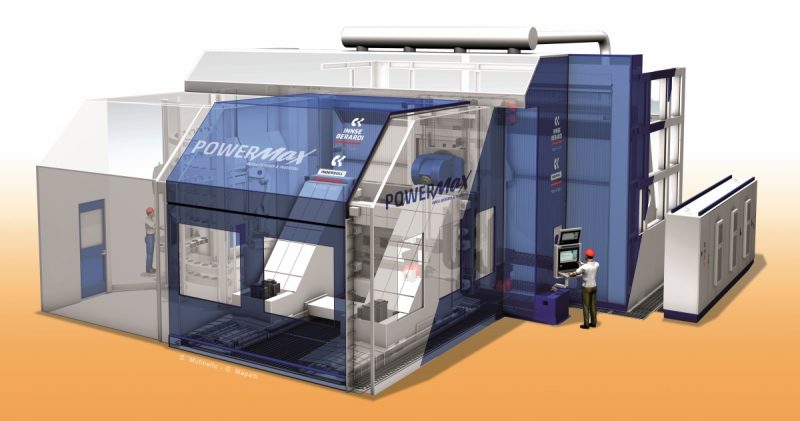
PowerMax è la risposta della divisione Machine Tools del gruppo Camozzi, di cui fanno parte Innse Berardi e Ingersoll, alle esigenze dei clienti che sono alla ricerca della massima produttività nella lavorazione del titanio e delle leghe di alluminio, con conseguente miglior TCO.
di Andrea Pagani
PowerMax è una gamma di centri di lavoro ad asportazione di truciolo specifica per la lavorazione dei componenti strutturali aeronautici, aerospaziali e di meccanica generale, progettata e realizzata da Innse Berardi e Ingersoll. Si tratta di una soluzione predisposta per essere sviluppata in funzione delle necessità del cliente, in base alle dimensioni dei pezzi, ai materiali da lavorare e al livello di automazione necessario.
Macchina innovativa
PowerMax è una vera e propria evoluzione per i settori nei quali vengono lavorati materiali come titanio, leghe resistenti al calore e alluminio. È basata sulla conoscenza di dominio e l’esperienza storica delle due aziende e arricchita dall’innovazione data dalla simulazione digitale, in linea con il concetto di “digital twin”. L’approfondita analisi dei materiali e la partnership con i fornitori sui migliori utensili disponibili hanno permesso di individuare le caratteristiche prestazionali di una soluzione innovativa per ridurre i costi operativi e i tempi dei processi produttivi. Nel settore aeronautico, ogni nuovo progetto introduce nuovi materiali e forme sempre più complesse, al fine di ottimizzare i consumi e ridurre l’emissione di CO2. Tali componenti richiedono specifiche prestazioni nei macchinari che vengono utilizzati per la lavorazione ad asportazione di truciolo: è evidente infatti il costante incremento nell’utilizzo di materiali compositi, titanio e alluminio. PowerMax è la soluzione innovativa che fornisce la massima flessibilità per applicazioni più generiche di particolari in titanio e leghe derivate. Trattandosi di materiali molto diversi tra loro, è richiesto un approccio differente sia a livello strutturale che prestazionale della macchina. PowerMax si distingue quindi tra la versione T (Torque, adatta al titanio), S (Speed, per l’alluminio) e ST (come sistema misto per materiali con caratteristiche diverse tra loro, che prevede un sistema automatico di cambio cartuccia dell’elettromandrino).
Progettata per le massime prestazioni
Le macchine orizzontali tradizionali di grandi dimensioni sono caratterizzate da una struttura con colonna mobile. Su impianti di questo tipo, quando la posizione verticale di lavoro è elevata, si ha una inevitabile riduzione della rigidezza statica e dinamica. La profondità di lavorazione viene gestita da un classico Ram la cui estensione, però, provoca una perdita di rigidezza oltre che problemi di accuratezza dovuti all’effetto della gravità. L’utente finale è perciò costretto a scegliere i parametri di taglio e i settaggi dinamici nella condizione più conservativa, in modo che risultino adeguati in ogni punto del volume di lavoro. Questo comporta una evidente perdita di efficienza complessiva dell’impianto. Per evitare quanto sopra e garantire la massima rigidezza della macchina, PowerMax prevede una colonna mobile, all’interno della quale è alloggiato il carro porta testa, che scorre su quattro guide, due alloggiate nel basamento inferiore e due sulla struttura verticale posteriore. Il classico asse del Ram viene quindi sostituito da una struttura esterna traslante porta pallet oppure da una tavola rototraslante. Una cinematica di questo tipo assicura che le prestazioni in termini di rimozione truciolo, dinamica e accuratezza siano costanti in tutta l’area di lavoro.
Massima flessibilità in più versioni
PowerMax di Innse Berardi / Ingersoll offre una corsa verticale da 2000 mm oppure 3000 mm e una corsa orizzontale da 4000, 5000 o 6000 mm.
PowerMax T (Torque) è pensata per affrontare il titanio e più in generale le leghe resistenti al calore. Può essere configurata con un elettromandrino da 9000 Nm di coppia e 8000 giri/min ad alte prestazioni o con un motore tradizionale da 1500 Nm montati su una testa di produzione Innse Berardi / Ingersoll. Le velocità degli assi lineari sono pari a 30 m/min su X/Y e a 20 m/min in Z (la tavola). Gli assi polari C e A hanno rispettivamente una velocità di rotazione di 30 giri/min e 15 giri/min con elevati valori di coppia su entrambi gli assi polari. Un aspetto molto importante è rappresentato dalla disponibilità di lubrorefrigerante ad alta pressione (80 bar) e portata (150 l/min) attraverso il mandrino.
PowerMax S (Speed) nasce invece per affrontare l’alluminio. Ampia in questo caso la disponibilità di elettromandrini, che arrivano a coppie fino a 100 Nm e 30.000 giri/min. Rispetto alla PowerMax T, la versione S presenta assi lineari decisamente più rapidi con 60 m/min in X/Y e 40 m/min in Z. Elevata dinamica anche sugli assi C e A, capaci rispettivamente di 60 e 30 giri/min. Anche in questo caso la testa è di produzione Innse Berardi / Ingersoll e offre una lubrorefrigerazione a partire dalla minimale fino a quella a 40 bar e 40 l/min di portata.
PowerMax ST (Speed & Torque) è poi una terza versione, che unisce le qualità degli altri modelli per affrontare, in maniera produttiva, flessibile e sullo stesso impianto, materiali che hanno proprietà completamente diverse come appunto l’alluminio, il titanio o acciai speciali. La testa ha le stesse caratteristiche di quella per il titanio, mentre per quanto riguarda la motorizzazione dei mandrini è disponibile una ampia gamma di elettromandrini, per i vari tipi di materiali, intercambiabili tra di loro in maniera automatica.
Alta dinamica per titanio e alluminio
Chi già lavora il titanio sa bene quanto sia complesso gestire al meglio i parametri macchina per massimizzare le prestazioni degli utensili e la produttività complessiva dell’impianto, ne consegue che la dinamica della macchina risulti fondamentale. Se pensiamo a come lavora una fresa e a come viene impegnato il tagliente di un utensile sul materiale, nelle macchine tradizionali il CNC è costretto a rallentare durante un cambio di traiettoria per mantenere costante la precisione di posizionamento, così facendo lo spessore del truciolo diminuisce. Se si scende al di sotto di un certo valore di avanzamento degli assi, l’interferenza non è più sufficiente per ottenere l’azione di taglio e si genera conseguentemente attrito, che si trasforma in calore. Per ovviare a questo problema è necessario imporre al controllo numerico una velocità di riferimento e una tolleranza dinamica. Per questo diventano fondamentali i valori di accelerazione e le spinte di tutti gli assi, supportati da una considerevole rigidezza strutturale. La lavorazione del titanio e in generale la lavorazione delle leghe resistenti al calore richiedono la disponibilità di grandi valori di coppia al mandrino ed elevati valori di rigidezza statica per sopportare le forze in gioco. La conducibilità termica delle leghe resistenti al calore è molto bassa rispetto ai materiali tradizionali come acciai e ghise: questo significa che il calore prodotto durante il taglio si concentra per la maggior parte sull’utensile. Essendo il calore una causa primaria di usura del tagliente diventa indispensabile la disponibilità di un flusso di refrigerante con una portata molto elevata per disperdere il calore.
Per mantenere la zona di lavoro esente dalla presenza di trucioli, soprattutto nella lavorazione delle cavità profonde, presenti ad esempio nei componenti strutturali aereonautici, sono necessari:
– mandrino orizzontale per facilitare l’evacuazione del truciolo;
– l’impianto di refrigerazione interno ad alta pressione dotato di sistema di raffreddamento dei fluidi lubrorefrigeranti per evitare il surriscaldamento della struttura e le possibili derive termiche.
Per ragioni diverse, le stesse problematiche si possono riscontrare per l’alluminio. Si tratta infatti di un materiale che vede nell’elevato volume di truciolo il fattore chiave per la produttività. Sul mercato sono disponibili mandrini che offrono un elevatissimo regime di rotazione e grandi potenze, che però richiedono macchine che abbiano delle velocità di avanzamento sugli assi molto elevate e, soprattutto, che siano in grado di mantenere le velocità programmate anche in corrispondenza di traiettorie con continui cambi di direzione e curvatura. I soli avanzamenti e accelerazioni lineari, tipici criteri di scelta di queste macchine, non sono più sufficienti; per ridurre i tempi di lavorazione occorrono macchine che possano offrire elevate accelerazioni cubiche e cinematismi con elevati valori del guadagno di posizione per ogni singolo asse. Il tutto deve essere integrato in strutture che possano sopportare carichi dinamici molto elevati. Per questo motivo le velocità di taglio adottate durante le operazioni di sgrossatura sono piuttosto basse e conseguentemente la frequenza di taglio risulta essere approssimativamente compresa tra i 13 e i 17 Hz. Per evitare che questa frequenza coincida con la prima frequenza di risonanza della struttura, che potrebbe provocare l’instabilità del sistema, sono stati adottati particolari accorgimenti che hanno permesso di ottenere una prima frequenza di risonanza della macchina, cinematismi degli assi compresi, di gran lunga superiore alle frequenze di taglio. Una frequenza così elevata permette di realizzare una dinamica molto spinta, fondamentale nella lavorazione di ogni materiale perché permette di mantenere la velocità di avanzamento programmata (che nell’alluminio è sinonimo di riduzione dei tempi di lavorazione, mentre nel titanio assicura una migliore durata del tagliente).
Tutta l’automazione che serve
L’asse Z può essere di due tipologie: la soluzione standard, costituita da una struttura porta pallet verticale particolarmente indicata per il settore aeronautico, e una seconda soluzione costituita da una classica tavola rototraslante (come configurata e installata sulla PowerMax presente negli stabilimenti produttivi di Camozzi Advanced Manufacturing di Milano).
Magazzino utensili modulare
Il cambio utensili è di tipo robotizzato e completamente personalizzabile, con capacità che variano da 80 utensili da 200 mm di diametro e 750 mm di lunghezza, sino a 200 posti e più, in base alle dimensioni e alle necessità dei clienti.
Condividi l'articolo
Scegli su quale Social Network vuoi condividere