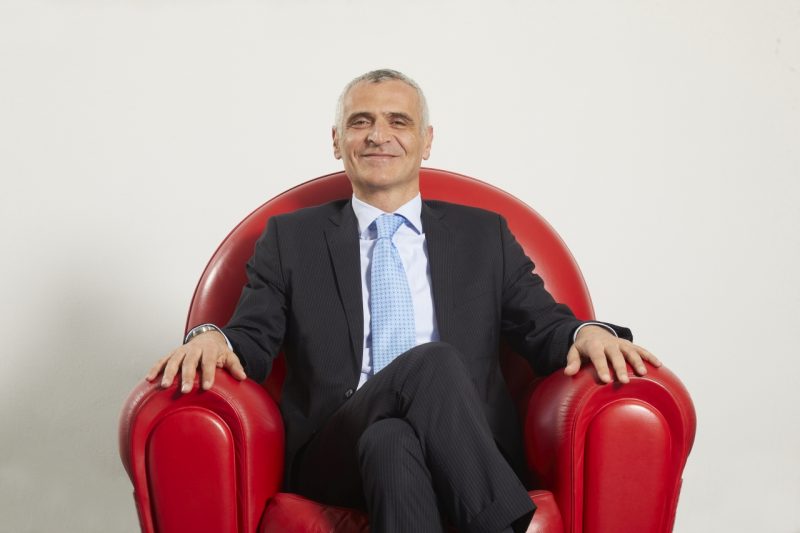
di Edoardo Oldrati
Riccardo Procacci ricopre il ruolo di CEO di Avio Aero, azienda del gruppo GE attiva nella progettazione e produzione di componenti per motori aeronautici. Procacci ha iniziato la sua carriera in GE 22 anni fa, dove ha ricoperto ruoli nelle divisioni Oil & Gas e Aviation in Italia, Asia e India. Procacci si è laureato in Ingegneria Meccanica presso l’Università “La Sapienza” di Roma, dove ha conseguito anche un dottorato di ricerca con specializzazione in Turbomacchine.
Per Avio Aero l’innovazione passa attraverso uno stretto rapporto con le università. Avete un network molto efficace e connesso con i migliori atenei italiani dal nord al sud. Intorno a quali priorità avete costruito questo rapporto?
Con le università lavoriamo insieme sullo studio delle caratteristiche dei materiali, un tema che è fondamentale per permetterci di progettare e realizzare prodotti più performanti. Negli ultimi anni abbiamo cominciato anche a collaborare sul tema dell’additive manufacturing sia per quanto riguarda la produzione sia sul cosiddetto “additive repair”, cioè effettuare riparazioni tramite tecnologia additive. Contemporaneamente proseguiamo nello sviluppo di tecnologie di lavorazione per asportazione, visto che effettuare lavorazioni complesse sui componenti resta un elemento distintivo per la nostra attività. Da questo impegno è nata anche la creazione, insieme a varie università sul territorio, di corsi in “Advanced manufacturing”, dove si affrontano non solo le tematiche dell’additive ma di tutta la manifattura meccanica avanzata. Avio Aero ha bisogno che queste competenze restino elevate, riusciamo a restare competitivi nel mercato per quello che sappiamo fare e non per il costo a cui lo facciamo. Mantenere questo elemento di competitività passa sempre e solo attraverso le nostre università.
Se guardiamo al futuro, stiamo lavorando su due elementi che mirano a migliorare il rapporto tra Avio Aero e il mondo universitario: il primo è incentivare quanto possibile le università alla collaborazione. Su scala mondiale le università italiane tendono a essere piccole, vogliamo incoraggiarle a consorziarsi e a lavorare insieme per avere maggiore impatto dal punto di vista delle competenze e dei finanziamenti alla ricerca da cui attingere. Con questo obiettivo da ormai qualche anno abbiamo lanciato il progetto “Technology Development Community” che stabilisce un network tra università che collaborano sui nostri progetti: si tratta di nove community tecnologiche focalizzate su specifiche tematiche tecnico-scientifiche dove Avio Aero coordina gruppi di lavoro partecipati. Questi ricercatori e tecnici appartengono a più atenei e PMI che collaborano per realizzare un piano scientifico pluriennale condiviso e orientato alla creazione di reali opportunità di sviluppo industriale. Questo approccio a Technology Development Community si sta rivelando molto efficace e lo stiamo espandendo in Europa con altre università.
Il secondo elemento che ritengo importante è che oltre a collaborare con le università sul pensare, si impara molto collaborando sul fare: per questo motivo abbiamo creato laboratori di ricerca congiunti all’interno del Politecnico di Torino e del Politecnico di Bari, insieme a quello con UniPisa sulle trasmissioni meccaniche ed il ComHeatLab sulla combustione a UniFi.
Sono passati poco più di 5 anni dall’inaugurazione dello stabilimento di Cameri: le chiedo un bilancio di quello che, ad oggi, è ancora uno tra i più grandi al mondo interamente dedicati alla produzione additiva. E per il futuro cosa avete in programma per questo sito?
Quella di Cameri è una storia interessante che inizia ben prima di cinque anni fa. Tutto nasce infatti dall’intuizione di un imprenditore locale, un vero innovatore, al quale Avio Aero ha rivolto la sua attenzione: successivamente si è inserito un progetto di collaborazione con il Politecnico di Torino che poi ha dato origine a una start-up, che è diventata una joint venture e ha successivamente portato all’ingresso della società nel gruppo.
È importante ricordare che, quando cinque anni fa abbiamo inaugurato lo stabilimento di Cameri, non avevamo commesse: Avio Aero ha fatto una scommessa usando questo stabilimento come un Innovation Center per far maturare la tecnologia additive. Per questo parlo di una storia di incredibile imprenditorialità tecnologica: avevamo infatti ben intuito le potenzialità della tecnologia additive, ma non sapevamo esattamente dove e come utilizzarla. Negli anni quindi abbiamo testato il mercato realizzando componenti statici e rotanti nel settore aeronautico, componenti automotive per il racing, ma anche componenti medicali. Nel farlo abbiamo sperimentato anche entrambe le tecnologie additive che avevamo a disposizione: la tecnologia di fusione laser (DMLM) e la tecnologia di fusione a fascio di elettroni (EBM). Alla fine di questo processo di esplorazione delle opportunità di mercato abbiamo capito quale poteva essere il futuro per quello stabilimento: la tecnologia a fascio di elettroni utilizzata per la produzione di componenti rotanti in polvere di titanio alluminio che, per le loro caratteristiche, sono scarsamente producibili con tecnologie tradizionali. A quel punto è iniziata la trasformazione di Cameri da Innovation Center a vera fabbrica installando le macchine di stampa che oggi stanno producendo migliaia di palette per il quinto e sesto stadio della turbina di bassa pressione del GE9X.
Cameri nasce quindi da un’intuizione di un innovatore imprenditore locale e poi evolve fino a un centro di produzione industriale di rilevanza mondiale. Per Avio Aero è stato un processo di learning importante, perché ci ha permesso di capire che la tecnologia additive non può e non deve competere con le tecnologie di produzione tradizionale. Quando però la tecnologia tradizionale non ti permette di ottenere il prodotto che vuoi, ad esempio questa lega di titanio alluminio è molto difficile da forgiare, allora l’additive entra in competizione. Una tecnologia che risulta vincente in quanto i costi di produzione dipendono esclusivamente dalla quantità di polveri utilizzate e dal tempo macchina, e non dalla complessità dell’oggetto disegnato. Pertanto questa scissione del rapporto proporzionale tra complessità e costo, che solitamente caratterizza la tecnologia tradizionale, dà la libertà al progettista di disegnare componenti o prodotti più o meno articolati che non potrebbe disegnare con tecnologie standard.
Quali sono le caratteristiche di una Brilliant Factory?
Con Brilliant Factory intendiamo una factory connessa dove tutti gli step della progettazione e della produzione sono tracciati digitalmente, i dati sono raccolti in un unico repository (il data lake) dal quale si accede per analisi di tutti i tipi sui processi di progettazione e produzione, monitorando ad esempio lo stato e le performance di ogni macchina. Lo stabilimento di Cameri e la nuova area dedicata all’additive manufacturing nel nostro stabilimento di Brindisi nascono ovviamente Brilliant Factory, mentre le altre fabbriche le stiamo trasformando attraverso un processo progressivo. Sarebbe bello rendere tutti gli stabilimenti Avio Aero delle Brilliant factory in un solo passaggio, ma non è un’opzione concreta e quindi ci muoviamo per passi successivi. Una delle prime cose che abbiamo fatto è stata connettere le macchine in modo da monitorare in tempo reale il loro stato di efficienza, ora stiamo introducendo software che le rendano macchine smart e quindi in grado di digitalizzare i dati di produzione in modo da poter poi trasmetterli all’ingegneria. Posso dire che stiamo portando avanti in un processo di trasformazione che, tra l’altro, credo e spero non avrà mai un termine: le capacità della brilliant factory si evolveranno infatti a un passo tale che ci troveremo sempre a rincorrere.
L’evoluzione dei processi in Avio Aero (penso all’additive manufacturing o alla digitalizzazione) richiede nuove competenze nelle varie aree. Quali sono le strategie di Avio Aero per la formazione delle nuove competenze?
Sulla formazione agiamo con diverse strategie: la prima è proporre training e corsi di formazione di vario tipo, che tra l’altro fanno parte anche dei nostri obblighi sindacali. Un altro strumento è l’attività dei nostri tecnici che lavorano insieme a ricercatori universitari e che poi riportano in azienda queste nuove competenze trasferendole ai colleghi. Nel learning condiviso che sviluppiamo all’interno delle nostre fabbriche, le attività lean manifacturing hanno poi un ruolo fondamentale visto che offrono l’opportunità a tutti i nostri operatori di condividere le proprie idee e proposte mettendo in pratica le azioni di continuo miglioramento che si sviluppano internamente.
Molto importante per noi è, dal punto di vista della formazione e della crescita professionale, far parte del network GE. Devo dire che non ci vergogniamo nemmeno di “rubare” da altre industrie: in ambito manufacturing e organizzazione del lavoro in fabbrica l’automotive è sicuramente più avanti rispetto all’industria aeronautica, quindi guardiamo con interesse anche a ciò che avviene in altri comparti. Questo è un elemento di umiltà che cerco di mantenere come elemento chiave del nostro Dna: se non pensiamo che il successo che abbiamo oggi sia un diritto garantito, allora ci manteniamo aperti al miglioramento continuo e a imparare da chiunque abbia da insegnarci qualcosa.
I nuovi materiali sono un elemento chiave per l’industria aeronautica: in che direzioni sta procedendo Avio Aero su questo fronte?
La prima direzione è verso materiali che ci diano nuove capabilities (come, ad esempio, maggiore resistenza al calore o maggiore leggerezza) utili rispetto ai prodotti che realizziamo. Una seconda direttiva di ricerca è trovare nuovi materiali per l’additive manufacturing. Oggi l’additive è fortemente limitato da un numero esiguo di materiali che possiamo utilizzare, in termini di polvere, per produrre. Stiamo lavorando quindi per crearne di nuovi, per esempio le cosiddette leghe intermetalliche (come la lega titanio-alluminio) che oggi non esistono in quanto non sono lavorabili con tecnologie tradizionali e che invece potrebbero essere lavorate grazie alle tecnologie additive.
Un’azienda come la vostra ha anche una fitta rete di partner (ho letto oltre mille fornitori in Italia per un volume di fatturato di 321 milioni di euro), ma è anche fortemente innovativa nelle tecnologie e nei processi: come riuscite a trasferire questa innovazione a tutta la filiera?
Considero il coinvolgimento della filiera una priorità perché non si fa innovazione in mezzo al deserto, questo ce lo insegna la storia della Silicon Valley che ha creato un ecosistema tra università e innovatori che si sono influenzati a vicenda generando nuove idee. Quindi è fondamentale la presenza di un network universitario, ma lo è altrettanto avere un network di fornitori capaci e che restino al passo coi tempi. Fino ad oggi abbiamo fatto un buon lavoro nel trainare fornitori, ricordiamo che sul territorio italiano oggi Avio Aero acquista in pratica la metà dei componenti di cui ha necessità, ma dobbiamo cambiare passo, il mio sogno è quello di avere una rete di fornitori che non è a nostro traino, ma che ci spinge. Per realizzare questa visione serve che Avio Aero cambi atteggiamento e sia in grado di offrire ai nostri fornitori in maniera sistematica una visione strategica di dove sta andando. Solo così i nostri fornitori saranno in grado di allinearsi e di precederci nella direzione in cui vogliamo andare. Serve inoltre che le università sappiano offrire anche ad aziende medio piccole opportunità di collaborazione che sostengano l’innovazione tecnologica.
Quali sono le parole chiave per descrivere come sarà il 2019 di Avio Aero?
Output industriale. La sfida principale del 2019 è quella di eseguire i nostri piani di crescita in termini di produzione in modo da rispondere adeguatamente alle richieste dell’industria. È una sfida stimolante, ma decisiva per il futuro dell’azienda.
Condividi l'articolo
Scegli su quale Social Network vuoi condividere