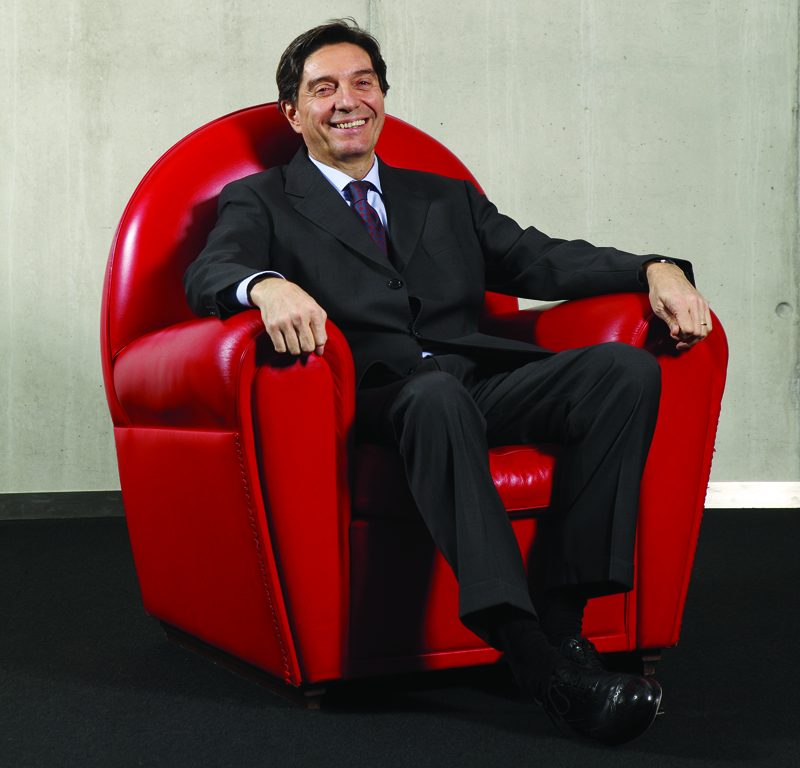
Intervista a Roberto Brembo, Direttore del Business Development & Marketing del Gruppo Brembo e Presidente di CLPA
Sulla poltrona di Tecnologie Meccaniche (i numeri di Tecnologie Meccaniche sono leggibili online previa registrazione gratuita) si è seduto Roberto Vavassori, Direttore del Business Development & Marketing del Gruppo Brembo S.p.A e, dal 2016, Presidente CLEPA l’Associazione europea dei produttori di componenti, con sede a Bruxelles, che è oggi referente stabile della Commissione per l’attività normativa del settore dei trasporti, e che annovera tra i soci tutti i grandi gruppi europei e transplants.
Vavassori oggi è membro del Comitato Esecutivo di Brembo, Amministratore di Petroceramics e Vicepresidente di BSCCB. Fa parte della Commissione Università di Confindustria Bergamo, dal 2012 al 2015 è stato Presidente ANFIA, l’Associazione italiana della Filiera Industria Automobilistica.
Nell’ultimo anno l’automotive è stato tra i settori trainanti della meccanica, pensa che questa tendenza positiva proseguirà anche nel 2016?
Nel 2015 l’automotive è stato uno dei motori trainanti della crescita non entusiasmante del Pil italiano, ma rispetto ad altri Paesi questo incremento va ridimensionato. La produzione in Italia è infatti aumentata a 650mila autovetture e poco meno di 1 milioni di veicoli, includendo i veicoli commerciali leggeri, ma non dobbiamo dimenticare che in Spagna nel 2015 ne sono stati prodotti 2 milioni in più, in Inghilterra 1,5 milioni e in Germania circa 6 milioni. Guardando ai primi mesi del 2016, credo che questa tendenza positiva sarà confermata, anche se forse con risultati meno eclatanti. Nel 2016 c’è anche una tendenza positiva che riguarda la componentistica, un settore che in Italia vale 40-42 miliardi di euro in buona parte esportati.
Il 2015 è stato anche l’anno del diesel-gate. Quali ricadute ha avuto sulla vostra filiera?
Mi piace chiamarlo con il suo nome corretto, cioè Volkswagen-gate, visto che coinvolge un’azienda in particolare. Come associazione dei costruttori di componenti avevamo stimato che non ci sarebbero state ricadute importanti e così è stato, per fortuna. Noi siamo ancora convinti che la motorizzazione diesel sia un fattore imprescindibile, per ottemperare agli obiettivi europei di diminuzione dell’emissione di CO2; i veicoli devono essere però puliti in ogni frangente di utilizzo, cioè con dispositivi a bordo capaci di catturare i NOx. Il problema principale si verificherà quindi sulle motorizzazioni diesel più ridotte di cilindrata che, se dotate di soluzioni che le rendano non inquinanti in termini di NOx, non riusciranno più ad essere economicamente competitive.
Detto questo, i numeri confermano che nel 2016 la motorizzazione diesel rimarrà un elemento importante. Oggi però stiamo giudicando il presente e guardando il futuro con gli occhi del passato. Questo approccio, che ritengo pericoloso, non tiene conto che, ad esempio, nelle nostre città l’inquinamento più grave è rappresentato dalle emissioni di particolato (PM) causate, per quanto riguarda i veicoli, dalla massiccia presenza di veicoli da Euro 0 a Euro 3. Se si convertissero ad Euro 6 tutti i 32 milioni di veicoli italiani il problema sarebbe praticamente risolto.
In termini di sostituzione lineare servono 20 anni per rimuovere l’intero parco circolante italiano, inclusi i mezzi pesanti che sono parte imprescindibile della nostra circolazione. Per questo dovremmo fare di più a livello di politiche comunitarie, per incentivare l’aggiornamento e la sostituzione del circolante europeo e non solo italiano, visto che moltissimi mezzi di altre nazioni utilizzano in transito le nostre autostrade.
Come Associazione lo ripetiamo in ogni sede istituzionale, si è visto qualche segnale per quanto riguarda gli autobus che, in Italia, sono per il 75% precedenti all’Euro 3. Immaginiamo il beneficio per le nostre aree urbane, se solo si aggiornasse all’Euro 6 tutto il circolante degli autobus.
A Bruxelles si prenderanno decisioni importanti sul tema della mobilità, Clepa darà il suo contributo in questo dibattito?
Certamente sì, perché negli anni Clepa è diventata una voce molto ascoltata e ogni volta che c’è da adottare politiche comunitarie su trasporti, circolazione e sostenibilità delle aree urbane, Clepa è coinvolta insieme a costruttori, stakeholder delle città e consumatori. Questa stereofonia di ascolto della Commissione è molto positiva, perché le istanze dei costruttori non sono sempre le medesime dei componentisti. Anche a livello europeo dobbiamo inoltre superare il settarismo di chi vede solo il cittadino, solo il consumatore, o solo le aziende. Chi lavora nel settore della mobilità, 12 milioni solo in Europa, sa che serve un approccio olistico, in cui il cittadino europeo è un cittadino che lavora, che consuma e che ama il proprio ambiente, e che considera la mobilità di dati, persone e mezzi un diritto fondamentale.
Quali istanze ha particolarmente a cuore e vorrebbe portare avanti nel suo nuovo ruolo a Bruxelles?
Clepa sta declinando la sua missione adeguandosi all’evoluzione delle istanze sociali ed economiche europee. Vogliamo rappresentare l’industria della componentistica per la mobilità sostenibile che sia individuale, collettiva, o relativa al trasporto merci. Inoltre, mi piacerebbe che questa filiera fosse uno dei pilastri per tornare a un’Europa in cui il 20% del Pil viene dalla manifattura. È un obiettivo fondamentale, abbiamo visto anche in Italia quali effetti abbia avuto sul Pil nazionale un incremento della produzione di sole 200mila vetture. Un recente studio di Prometeia, che abbiamo presentato insieme alla Commissione Industria del Senato, ha evidenziato come investire nella filiera dell’automotive abbia una ricaduta tripla in termini di valore aggiunto nell’economia e di ricadute occupazionali. Questi dati, superiori per esempio a quelli di altre filiere, confermano come investire in modo intelligente nella mobilità sostenibile sia una delle chiavi per far crescere nuovamente la manifattura europea e raggiungere l’obiettivo del 20% del Pil italiano ed europeo.
Parliamo di Internet of Things, la crescente attenzione sui temi della connettività legati alla mobilità porterà a un crescente peso della componente ICT (Information Comunication Technology) nelle auto. Come vivono questa evoluzione i costruttori di componenti?
Al di là del nome, gli amici tedeschi la chiamano Industrie 4.0, noi Fabbrica Intelligente e gli americani Internet of Things, la sensorizzazione e la digitalizzazione diffuse mi piace intenderle non come una rivoluzione, ma come un’evoluzione accelerata. Per esempio, la sensoristica utilizzata è già a nostra disposizione, ora si tratta di passare da un livello centralizzato di programmazione e manutenzione a un fabbrica che sia capace di autoregolarsi, autoaggiustarsi e autoprogrammarsi.
Non è una missione impossibile, abbiamo già oggi esempi concreti in Italia dove, forse pochi lo sanno, sono attivi 8 cluster di ricerca di cui ben 7 lavorano proprio su questi temi. Se ci concentriamo sulla Fabbrica Intelligente troviamo un cluster composto da 400 aziende, Brembo compresa, che lavorano insieme a centri di ricerca e università. Credo sia un bell’esempio di un’Italia che cerca di fare sistema senza chiedere il sostegno pubblico, capendo che bisogna lavorare insieme prima di tutto per il proprio bene.
Una recente ricerca condotta da Confindustria Bergamo dimostra che sul territorio di questa provincia si producono 10 miliardi di euro di valore aggiunto manifatturiero, in linea quindi con le aree tedesche più sviluppate. La differenza è netta se guardiamo invece al valore aggiunto per addetto: nel nostro territorio è di circa 65mila euro; mentre i colleghi tedeschi lavorano su valori tra i 120 e i 170mila euro ciascuno. Questo punto è fondamentale per me: le aziende italiane devono incrementare la produttività intesa come valore aggiunto dei nostri prodotti, non come numerosità dei prodotti a basso valore aggiunto. Se fino ad ora siamo stati bravissimi ad investire per riuscire a fare sempre più prodotti sempre più economici, oggi dobbiamo prendere esempio dalla Germania e arricchire i nostri prodotti.
In questa sfida la fabbrica intelligente ci potrà aiutare perché l’innovazione di processo e di prodotto è diventata imprescindibile. L’unico modo per aumentare il valore aggiunto della nostra produzione e per migliorare i nostri processi è infatti l’innovazione a tutto campo.
La sicurezza è un altro dei temi chiave nello sviluppo delle nuove vetture: in che modo si riflette sull’industria dei componenti questa sempre maggiore attenzione al tema?
È stato fatto tantissimo, ma c’è ancora tanto da fare. Siamo di fronte a una guerra spaventosa: in Europa ci sono 30mila morti all’anno per sinistrosità stradale, un’ottima riduzione dai 60mila del precedente decennio. Nei prossimi 5 anni l’Unione Europea ci ha chiesto però di dimezzare questo dato che, va detto, risente dell’allargamento europeo a Est, dove regole e comportamenti sono forse meno virtuosi. L’unica strada che vedo, insieme alla manutenzione della rete stradale, che è un fondamentale fattore di sicurezza, è l’elettronica, quindi l’auto connessa e l’auto a guida autonoma. Più del 90% della sinistrosità è ascrivibile ai comportamenti errati degli utenti della strada, è evidente che è qui che bisogna intervenire.
Durante il suo mandato uno dei temi è rappresentato dalle trattative per l’accordo di libero scambio tra Europa e Usa. Per l’industria europea della componentistica automotive quali sono le opportunità e, se presenti, le criticità in questo accordo?
La trattativa per il Partenariato transatlantico per il commercio e gli investimenti (TTIP) è una tela di Penelope. Quando due anni fa avevo partecipato con l’allora viceministro Calenda ad incontri a Washington con senatori e think-tank americani, era emersa l’opinione che non si trattasse di una priorità per gli Stati Uniti, e in tutta franchezza, non lo è ancora adesso. È difficilissimo quindi che si riesca ad approvare la totalità del TTIP oggi.
Dal nostro punto di vista la situazione è molto semplice: noi costruttori consegniamo esattamente gli stessi componenti per esattamente le stesse vetture sulle due sponde dell’Atlantico. L’industria automotive è già globalizzata, anche perché le stesse Case produttrici di auto stanno decidendo di creare poli di produzione da cui esportare, come succede in Messico, piuttosto che replicare la produzione in diversi siti produttivi in giro per il mondo. Il fatto è che non è il componente che ci dice se siamo conformi con il trattato di libero scambio, a stabilirlo è la modalità con cui questi componenti diventano vettura e vengono controllati. È un problema di regole di omologazione. Per fare un esempio, gli airbag negli Usa devono essere più grandi che in Europa, perché le procedure di prova americane prevedono che le cinture possano anche non essere allacciate.
Per questo motivo come Clepa chiediamo un riconoscimento reciproco delle regole vigenti, non un’attesa irrealistica di regole convergenti. È evidente che un regolatore americano ed uno europeo, molto difficilmente si troveranno d’accordo su quale siano le regole migliori per garantire la sicurezza dei propri cittadini. Ci sono però evidenze fattuali che i risultati in termini di sicurezza per i veicoli circolanti non sono dissimili tra Usa ed Europa. Da qui si deve partire per ottenere un mutuo riconoscimento in cui semplicemente l’Europa accetta le vetture americane così come vengono prodotte negli Stati Uniti e viceversa, senza rischi di azioni legali in caso di incidenti. Adesso che si sta pensando alla guida autonoma e alla connettività è ancora più importante non legiferare in maniera separata: se non troviamo oggi i giusti standard di sicurezza, parlo anche di sicurezza nella gestione dei dati, nei prossimi anni avremo una situazione paradossale in cui i sistemi di guida automatici non saranno gli stessi nelle varie regioni del mondo.
Il comparto della componentistica automotive investe ogni anno più di 18 miliardi di euro in R&S. In quali aree si concentrano le ricerche?
Lavoriamo su due fronti, il processo e il prodotto. Sempre di più però il processo condizionerà il prodotto: se i nostri componenti fossero sensorizzati avremmo probabilmente miliardi di informazioni utili per disegnarli e processarli in modo diverso. Parlo dei freni a titolo di esempio, probabilmente stiamo realizzando impianti frenanti largamente sovradimensionati e sovraspecificati rispetto alla missione d’uso tipica di quel componente. È chiaro che più andiamo verso la conoscenza intima di cosa fa un prodotto in esercizio, meglio riusciamo a metterlo in relazione al contorno (il contatto con la strada e con gli altri componenti) e meglio potremo progettarlo. Sto parlando di big data, quindi le nostre aziende avranno bisogno di figure professionali nuove per interpretare queste moli di informazioni come, ad esempio, il data scientist.
Se guardiamo al processo produttivo, il mio sogno è un’azienda leggera e organizzata a rete, dove i diversi reparti possono essere quelli che oggi chiamiamo fornitori. L’obiettivo è realizzare nel distretto un continuum indiviso in cui il prodotto viene processato in maniera molto più funzionale, economica ed efficiente in termini anche di capitale fisso e circolante.
Come stanno cambiando le vostre fabbriche?
Negli stabilimenti Brembo abbiamo attivato un progetto di Fabbrica Intelligente molto pervasivo. Infatti, tanto più riesco a identificare il singolo componente nel suo processo e tanto più riesco a personalizzarlo e dargli le caratteristiche che lo rendono più adatto alle missioni che deve svolgere. Queste priorità, ad esempio la tracciabilità e la gestione della lavorazione singola, invece che a lotti, non si abbinano però alla fabbrica tradizionale. Brembo, in Italia e nel mondo, ha già fatto importanti investimenti di processo in questa direzione, ma ne stiamo facendo ulteriori come una robotizzazione spinta che non vedrà più la distinzione tra robot e l’operatore umano sulla linea di assemblaggio. L’obiettivo rimane, come è sempre stato nella storia dell’umanità per ogni innovazione, rendere ancora meno faticosi i processi di lavorazione.
Quali ricadute hanno queste evoluzioni nel processo produttivo e nelle tecnologie applicate?
Oggi è centrale la flessibilità, un aspetto che come Brembo già decliniamo in modo elevato rispetto ad altri fornitori. Ancora di più però dobbiamo scollegare l’idea che ad una produzione più personalizzata corrisponda un aumento del costo. Oggi il paradigma è che se vuoi un particolare di un certo tipo allora lo devi pagare di più. Lo sforzo che dobbiamo fare tutti, indipendentemente dalle legittime logiche di profitto che ognuno deve perseguire, è quindi migliorare la locazione di capitale fisso, capitale circolante e costo del lavoro, che sono i tre parametri principali che determinano il costo finale. Secondo me abbiamo mezzi già adatti per lavorare in questa direzione. La nostra fabbrica deve diventare sempre più plug and play: arriva una macchina nuova e la fabbrica è già cablata per accoglierla. Servono quindi standard aperti, (nessuno vuole diventare succube di un fornitore solo), e sicuri.
Non è facile, ma la Commissione Europea deve lavorare su questi due fronti.
Inoltre, dove non si può garantire sicurezza, la fabbrica deve tornare a essere un ambiente discreto, servono dei circuit-breakers (degli interruttori di sicurezza informatici quindi), per evitare errori virali, che possono avere conseguenze disastrose propagandosi per tutta l’azienda.
Condividi l'articolo
Scegli su quale Social Network vuoi condividere