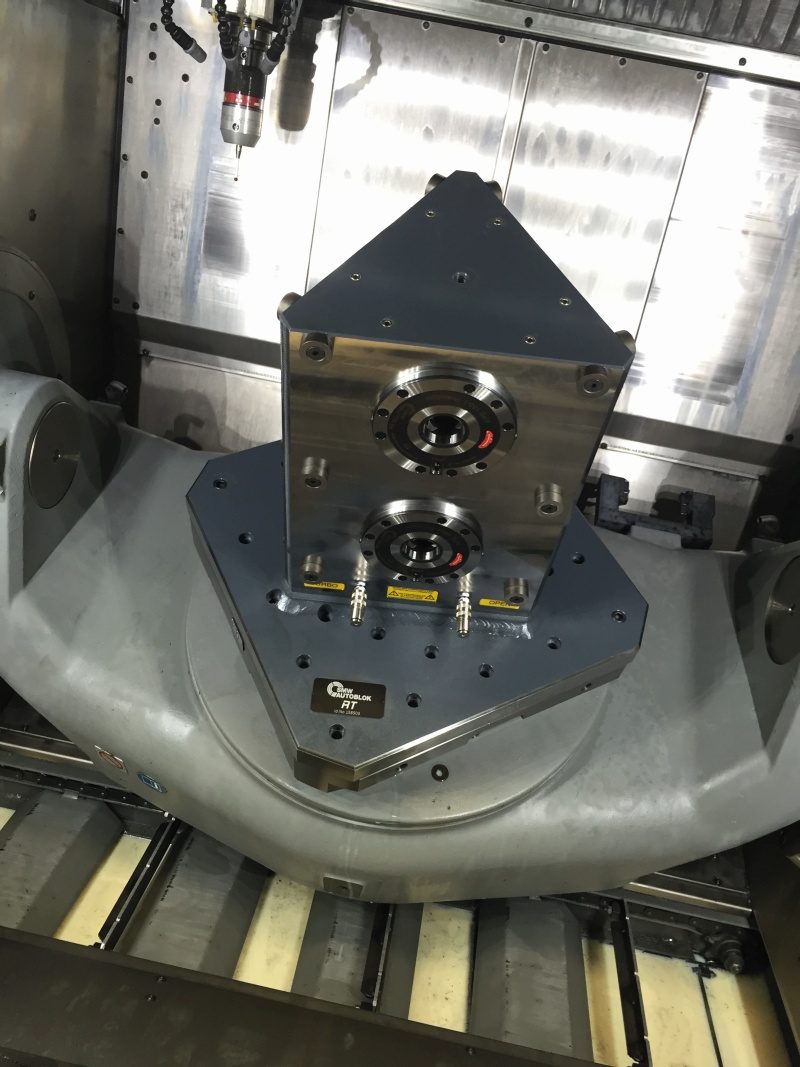
L’utilizzo dei dispositivi APS di OML ha permesso a Chiaravalli Group di approcciare in modo nuovo il lavoro in officina a tutto vantaggio di precisione, ripetibilità e flessibilità operativa
Il mondo delle trasmissioni meccaniche è messo costantemente sotto pressione dalle nuove applicazioni: motociclo, ferroviario, agricolo e movimento terra, energie alternative, oil&gas sono solo alcuni dei mercati nei quali è indispensabile poter contare su componenti e gruppi robusti, efficienti e affidabili.
In questo contesto Chiaravalli Group ed LMC vantano una posizione privilegiata, forte di 65 anni di storia e di sviluppo aziendale, geografico e tecnologico. La concorrenza in questo settore non manca: la qualità resta il driver del gruppo, ma occorre lavorare su soluzioni più complesse, in modo più efficiente e con risultati in officina capaci di ridurre tempi e costi.
«Una soluzione in tal senso è entrata nella nostra officina circa 5 anni fa. – spiega Marco Chiaravalli, Direttore stabilimenti di LMC – Affrontare la lavorazione di nuovi pezzi spesso mette in discussione processi consolidati, costringendoci a ripensare il modo in cui utilizziamo le macchine utensili. Ciò è avvenuto quando abbiamo coinvolto OML nello studio di un sistema di staffaggio e di gestione delle attrezzature che ci consentisse di bloccare i pezzi in maniera rapida e ripetibile, rendendo il processo indipendente dalla singola macchina e mantenendo in ogni caso la precisione richiesta dai nostri committenti».
Chiaravalli fa riferimento allo zero point APS (Automatic Positioning System) di OML, un sistema di interfaccia universale tra la macchina utensile, l’attrezzatura di bloccaggio o persino direttamente il pezzo da lavorare. Il vantaggio principale è la flessibilità del sistema in fase di posizionamento e bloccaggio, eseguibili in un’unica operazione e in brevissimo tempo.
Serraggio del pezzo, il principio di funzionamento di APS
APS usa aria compressa a 6 bar (filtrata e lubrificata) per sbloccare il sistema, mentre il bloccaggio è effettuato attraverso molle: non necessita pertanto di alimentazione in fase di bloccaggio e per mantenere in posizione l’attrezzatura. Una volta che i perni vengono inseriti nell’attrezzatura di bloccaggio o direttamente nel pezzo da lavorare, APS consente di movimentare facilmente il tutto in base alle necessità dell’officina.
Questo si traduce in un bloccaggio e relativo posizionamento estremamente rapidi, nell’ordine di pochi secondi, il tutto con una ripetibilità entro i 5 micron.
APS è inoltre l’unico sistema di bloccaggio zero point a 3 griffe a 120° e, grazie a trattamenti speciali antiattrito e anticorrosione dei perni e delle griffe di bloccaggio (già trattati preliminarmente a 62 HRc), ne migliora ulteriormente le prestazioni e la durata nel tempo.
Il pistone è di tipo monolitico a piani inclinati, mentre le griffe dispongono di doppio piano inclinato che genera un effetto “pull down”: in pratica, una volta inserito e bloccato, il pezzo non può muoversi né essere sfilato.
A richiesta, nelle versioni Premium, è disponibile la funzione Turbo che incrementa ulteriormente la forza di bloccaggio esercitata dalle molle (tipicamente di 12.000 N) sino a 30.000 N. Utile anche la funzione di pulizia automatica, che sfrutta l’aria compressa per eliminare quei corpi estranei che possono interferire con il bloccaggio. Con l’uso degli APS il risparmio sui tempi è evidente, ma probabilmente il vantaggio maggiore deriva dalla possibilità di ripetere lo stesso pezzo, nello stesso modo, bloccandolo nello stesso punto senza sbagliare un colpo.
«Abbiamo bloccato su cubi 16 pezzi di piccole dimensioni così come con un solo pezzo più grande su una piastra. – prosegue Chiaravalli – Possiamo inoltre utilizzare lo stesso cubo con pezzi sia piccoli, sia grandi cambiando semplicemente l’attrezzatura di serraggio: insomma, le possibilità sono illimitate, una volta cominciato a usare, non si torna più indietro. Adesso ogni nuova commessa viene analizzata tenendo conto degli APS, tanto che nel tempo abbiamo adattato le attrezzature presenti in azienda e scegliendo quelle nuove in funzione di questi dispositivi. È come avere un sistema multipallet utilizzabile su tutte le macchine in officina, persino se molto diverse tra loro».
Il risparmio sui tempi risulta evidente già a partire dal secondo piazzamento macchina; inoltre, quando i posizionamenti diventano complessi – come il passaggio da orizzontale a verticale – si vedono le reali potenzialità di APS. Questo perché in alcune occasioni la parte complessa non è il bloccaggio, ma il sollevamento e il riposizionamento in posizioni specifiche: ora è sufficiente sbloccarlo, sollevare tutta la piastra e riposizionarlo. E sempre più spesso non ci sono alternative, poiché il rischio con questi pezzi è staffarli male, realizzarli male o peggio ancora creare un pericolo per l’operatore».
Esperienza positiva
In precedenza, molte delle attrezzature venivano studiate insieme ad alcuni partner specializzati in soluzioni speciali perché, a seconda del settore di riferimento trattato, ciascun sistema di staffaggio deve offrire caratteristiche diverse.
«Ora che usiamo gli APS da diversi anni e che abbiamo lavorato svariate migliaia di pezzi, posso affermare che mantengono ciò che promettono. – aggiunge Chiaravalli – Avevamo la necessità di una precisione di posizionamento entro i due centesimi, e l’attrezzatura ci assicura sempre, anche dopo mesi o anni di utilizzo, una ripetibilità di pochi micron. Una volta montate, abbiamo lavorato per un anno e mezzo con attrezzature che tuttora sono efficienti come il primo giorno, senza mai dare problemi, persino in occasione di lavorazioni gravose. Anzi, le forze di serraggio sul piano sono tali da darci ancora più fiducia in asportazione e ci portano a “spingere” ancora di più, a tutto vantaggio delle tempistiche sul ciclo di lavoro».
«Abbiamo gestito particolari tondi da 800 mm di diametro su pallet da 630 mm che, chiaramente, non sarebbero stati bloccabili direttamente in macchina. Abbiamo costruito una piastra apposita da collegare agli APS: sinceramente all’inizio pensavo che non saremmo riusciti a ottenere la precisione voluta, ma in realtà abbiamo avuto un fissaggio preciso, sicuro e costante nel tempo. Anche per questo oggi utilizziamo questo sistema in tutte le applicazioni in officina, non solo in quelle che tecnicamente possono essere realizzate solo così, ma anche dove possiamo trarre vantaggio dalla versatilità di utilizzo degli APS».
L’importanza del supporto
Le commesse che entrano nel Gruppo Chiaravalli hanno sempre caratteristiche differenti, da qualche piccolo dettaglio a particolari totalmente nuovi. Questo richiede un approccio estremamente flessibile anche da parte di chi fornisce le attrezzature di serraggio.
«OML ci supporta anche nel pensare e nel realizzare l’attrezzatura in base alle nostre necessità. – prosegue Marco Chiaravalli – Per noi è fondamentale questa filosofia di lavoro perché non ci basta un semplice “fornitore” di attrezzature, ma abbiamo necessità di una consulenza a 360° che mostri tutti i modi per serrare, gestire e lavorare un pezzo al fine di ottenere il miglior risultato possibile. L’analisi di fattibilità insieme ai tecnici OML ci permette di esaminare l’applicazione insieme e valutare il modo migliore per ottenere i risultati voluti in maniera efficace ed efficiente: ci suggeriscono come bloccare i pezzi, se prenderne solo uno o multipli, tutti uguali o ottimizzando il volume di lavoro staffando particolari diversi ecc. Poi non sempre è necessario affidarsi a soluzioni speciali: il catalogo dell’azienda è vasto e include un gran numero di morse, staffe, dispositivi antivibranti ecc. ai quali attingere. Questo è ciò che ci aspettiamo da aziende che ci piace definire “partner”, ed è proprio quello che abbiamo ottenuto lavorando con OML».
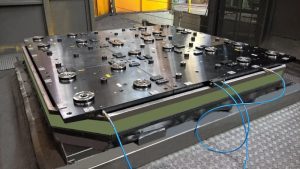
Condividi l'articolo
Scegli su quale Social Network vuoi condividere