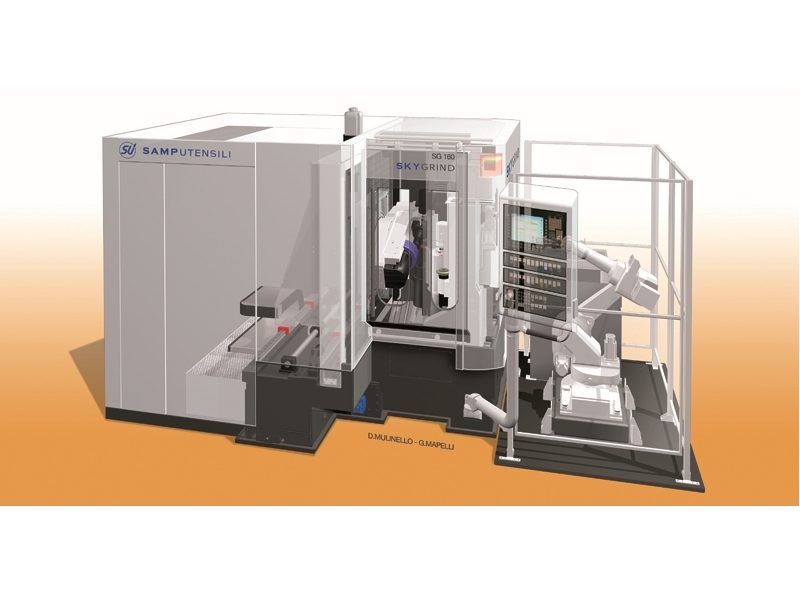
SG 160 SkyGrind è la nuova rettificatrice per ingranaggi cilindrici di Samputensili che non necessita dell’adduzione di oli riducendo del 75% il consumo di energia e con tempi ciclo ancora migliori
Indipendentemente dal campo di applicazione e dai numeri in gioco, disporre di una gamma di macchine completa significa poter offrire la soluzione più idonea a specifiche esigenze.
La SG 160 SkyGrind di Samputensili nasce anche per questo motivo: insieme alla rettificatrice per ingranaggi G 250 (presentata nel 2011) e alla G 450 (nel 2013), infatti, consente di aggiungere una taglia dimensionale più adatta alle altissime produzioni tipiche dei nuovi cambi per l’automotive, come i cambi planetari e quelli dual clutch, nei quali le dimensioni degli ingranaggi – ad eccezione di quello differenziale – difficilmente vanno oltre i 160 mm di diametro e i 300 mm di lunghezza dell’albero.
Un nuovo progetto
I progettisti Samputensili hanno quindi lavorato su una nuova piattaforma compatta, che coprisse in maniera più efficiente questa gamma dimensionale e che migliorasse il rapporto tra i tempi morti e quelli di lavoro (il tempo di cambio pezzo).
Ci sono diverse architetture sul mercato che presentano una tavola girevole con due teste portapezzo, una nella stazione di carico e l’altra in quella di lavoro, entrambe montate su una tavola principale che ne realizza lo scambio. Questi, uniti a quelli dell’allineamento e della fasatura dei denti dell’ingranaggio con la mola, portano il tempo di cambio truciolo-truciolo attorno ai 5 secondi. Il primo obiettivo è stato quindi lo sviluppo di un’architettura con due tavole portapezzo indipendenti tra loro e montate su due slitte lineari, che permettessero il cambio pezzo attraverso tre movimenti simultanei: l’arretramento di una testa, l’avanzamento dell’altra e lo spostamento della mola da una stazione di lavoro all’altra. Tre movimenti simultanei, anziché i consueti tre in sequenza: altre macchine richiedono infatti l’arretramento della mola, seguito dalla rotazione della tavola, per poi procedere all’avanzamento della mola verso il nuovo grezzo. Questo ha permesso di scendere a un tempo di cambio pezzo sotto i 2 secondi senza eccedere con le dinamiche degli assi, con conseguenti potenziali problemi di affidabilità nel medio periodo.
In altre parole, è possibile rettificare l’ingranaggio in minor tempo a parità di ciclo tecnologico: si tratta di un fattore di grande importanza poiché queste produzioni necessitano di elevata precisione nell’esito finale e nelle condizioni del pezzo in termini di qualità e di microstruttura, evitando le cosiddette bruciature.
In termini numerici, un pignone per trasmissione planetaria con 18-24 denti e un modulo compreso tra 1,2 e 1,5 richiede un tempo ciclo di 12-13 secondi inclusivi del tempo di cambio pezzo. A parità di ciclo tecnologico, la sola riduzione dei tempi da truciolo a truciolo consente di scendere sotto i 10 secondi. Ingranaggi più grandi hanno un tempo ciclo più lungo e dunque la riduzione dei tempi morti ha un impatto minore, assestandosi comunque su un buon 5%.
Un altro obiettivo che i tecnici Samputensili si sono posti è stato quello di innovare sotto un punto di vista tecnologico. Si tratta di un trend cominciato anni fa e che sembrava non potesse avanzare ulteriormente: negli anni ’80 la tornitura, la dentatura e la rasatura avvenivano prima del trattamento termico di tempra, e solo successivamente si procedeva con la rettifica utilizzando oli emulsionati o interi.
Negli anni ’90 si è introdotta la tornitura sul temprato, che viene eseguita dopo il trattamento termico e senza lubrorefrigeranti.
Negli anni 2000 le richieste di migliore precisione hanno portato a trasferire anche la rasatura dopo la tempra, sostituendola con la rettifica, che offre una qualità e una precisione migliore dell’ingranaggio, mentre la dentatura è stata trasformata in operazione a secco grazie all’utilizzo di utensili in metallo duro.
Fino a prima dell’avvento della SG 160 SkyGrind nessun olio veniva utilizzato in fase pre-trattamento termico, che invece era necessario per la rettifica dell’ingranaggio.
Il perché di tanto accanimento nei confronti degli oli è presto detto: l’olio porta con sé molti costi: di esercizio, di investimento iniziale, logistici, ecc. L’impianto di filtrazione ha infatti un ingombro pari alla macchina stessa di rettifica; a livello energetico, poi, l’impianto assorbe circa il 75% dei consumi complessivi a causa delle pompe, dei sistemi di raffreddamento ecc.
Rettificare senza oli
Esiste quindi un metodo per rettificare senza utilizzare gli oli?
Innanzitutto il processo di rettifica è divisibile in due fasi distinte: la passata di sgrossatura e quella di finitura. Samputensili ha eseguito alcuni test senza adduzione di fluidi, raccogliendo alcune informazioni ovvie ma altre estremamente significative: il risultato sono chiaramente ingranaggi bruciati, ma il dato più interessante è che, di queste due fasi, è la sgrossatura a creare problemi se effettuata a secco, mentre in finitura il contatto tra mola e pezzo risulta sufficientemente breve per non innescare bruciature. Percentualmente, in termini di volume di materiale asportato complessivamente, la finitura rappresenta circa il 4% del totale.
Il rotolamento della mola sull’evolvente ottenuto con il processo di generazione consente di avere un contatto puntiforme in costante movimento e ad altissima velocità tra la mola e il pezzo, e quindi un tempo non sufficiente a produrre un surriscaldamento locale in presenza delle asportazioni molto leggere tipiche appunto dell’operazione di finitura.
Per eliminare il problema in sgrossatura, quindi, è stata utilizzata una tecnologia già presente sul mercato, lo skiving, che prevede l’utilizzo di un creatore in metallo duro su ingranaggio termicamente trattato.
Oggi con la SG 160 SkyGrind la sgrossatura viene eseguita perciò con un creatore in metallo duro, mentre la finitura avviene di rettifica con mola a vite. La combinazione delle due tecnologie consente di ottenere un tempo ciclo analogo a quello del processo tradizionale di rettifica con la sola mola, dando risultati simili in termini di precisione, a un costo utensili paragonabile perché il costo del creatore in metallo duro viene risparmiato nel rullo diamantato di profilatura. Realizzando solo la finitura, infatti, l’usura della mola risulta ridotta e, di conseguenza, si riduce la frequenza di utilizzo del rullo.
Il vantaggio più consistente è nei cosiddetti “consumabili”, come appunto l’olio e l’energia impiegata nel processo, così come nello spazio occupato dalla macchina. Ci sono poi fattori difficilmente misurabili, come il miglioramento della qualità dell’aria dell’ambiente di lavoro, o l’eliminazione delle macchine per il lavaggio dei pezzi a fine ciclo di lavoro.
Usare un ciclo produttivo completamente oil free significa dunque avere significativi miglioramenti in termini di efficienza complessiva.
Una struttura efficiente
Rinnovare il processo e ridurne i tempi improduttivi è un passo notevole, ma in Samputensili sono andati oltre: le architetture tradizionali delle macchine di rettifica presentano infatti 4 assi di posizionamento: radiale, verticale, quello dell’angolo di elica di rotazione e quello di shifting, che si occupa dello scorrimento della mola lungo il pezzo. Con la nuova configurazione, il movimento lungo l’asse radiale si trova ora sulle due tavole portapezzo. Questo ha portato un significativo irrobustimento della macchina, un tema molto sentito nella trasmissione automobilistica perché la nuova frontiera tecnologica tiene conto anche dell’ondulazione del profilo dell’evolvente, la cui finitura superficiale può generare rumore, vibrazioni, perdite di efficienza, calore e minor densità di coppia. Riuscire a migliorare la qualità del profilo, infatti, consente di trasmettere più potenza sullo stesso ingranaggio, o di ridurre le dimensioni senza ridurre l’affidabilità complessiva della trasmissione; o, ancora, di utilizzare la medesima trasmissione su una gamma più ampia di motorizzazioni (con potenze e coppie differenti) e di beneficiare di economie di scala altrimenti irraggiungibili.
Anche l’asse di shifting posizionato sotto la mola è stato eliminato attraverso l’impiego dell’asse trasversale (che sposta l’intera colonna) e l’interpolazione tra questo e l’asse verticale. La sollecitazione nel processo di rettifica che crea l’ondulazione sull’ingranaggio si scarica proprio lungo questo asse: eliminando guide e viti a ricircolo le forze si scaricano sull’intera colonna, la cui inerzia garantisce evidentemente una maggiore rigidezza dinamica.
La nuova piattaforma è comunque adatta sia per la tecnologia a secco, sia con olio: esiste infatti anche una versione “wet” della macchina, denominata G 160, nella quale i miglioramenti in termini di rigidezza complessiva e di tempi improduttivi possono comunque fare la differenza su lotti estremamente numerosi, come appunto quelli per il settore automotive. In cicli già avviati, infatti, difficilmente il mercato accetta un cambiamento così radicale (come le lavorazioni senza olio), mentre nell’avviamento di nuovi progetti si potrà beneficiare al 100% della nuova tecnologia oil free.
Facile da usare e da manutenere
La macchina è dotata di elettromandrini sia per la rotazione del pezzo, sia per gli utensili.
Si tratta di motori sincroni, che assicurano la precisione di posizionamento necessaria per ottenere il perfetto ingranamento tra l’utensile e l’ingranaggio attraverso l’utilizzo di encoder ad altissima risoluzione.
Il controllo numerico Siemens 840D sl offre le prestazioni multicanale necessarie per permettere il tempo di cambio pezzo in tempo mascherato e con dinamiche importanti. L’interfaccia è sviluppata da Samputensili e consente l’inserimento dei parametri necessari a partire dal disegno, senza che l’utilizzatore debba occuparsi del part program.
Quando i tempi ciclo risultano molto rapidi – generalmente sotto i 15 secondi – Samputensili integra l’automazione di carico/scarico esterno con un sistema aggiuntivo interno che evita qualsiasi collo di bottiglia nel processo. Un singolo manipolatore, infatti, non garantirebbe la velocità necessaria per gestire lo spostamento di grezzi e finiti dalla macchina al magazzino e viceversa.
L’assenza di molta componentistica (l’asse in meno, tutto l’impianto per la gestione degli oli ecc.) consente poi di incrementare l’affidabilità complessiva della macchina e di ridurre gli interventi manutentivi.
I motori sono di tipo a cartuccia, facilmente rimovibili in caso di necessità, mentre il cambio utensili (mola e creatore) risulta agevolato poiché la macchina può posizionare la testa di fronte al portellone e consentire un semplice intervento da parte dell’operatore.
Condividi l'articolo
Scegli su quale Social Network vuoi condividere