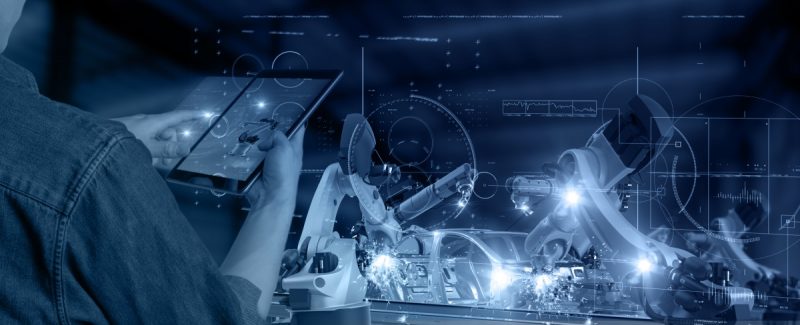
Individuare il potenziale di ottimizzazione nello sviluppo del prodotto e implementarlo nel processo di produzione.
Il tema di Industria 4.0 è stata per oltre un decennio al centro del dibattito pubblico, dettando l’agenda dei vertici di molte aziende. Diventa quindi centrale il processo di trasformazione dalla produzione organizzata in singole fasi controllate dall’uomo alla produzione connessa e digitalizzata.
La divisione Manufacturing Intelligence di Hexagon fornisce soluzioni che utilizzano i dati generati dai reparti di progettazione e ingegneria, produzione e misura per rendere la produzione più intelligente. Questo articolo si concentra sull’area della progettazione e dell’ingegneria, che si occupa dello sviluppo e della validazione del modello virtuale di un componente fino alla sua fattibilità. Inoltre, viene qui trattata l’identificazione e l’implementazione del potenziale di ottimizzazione nello sviluppo del prodotto e nel processo di produzione.
A cosa sono dovuti i costi?
I dipartimenti di sviluppo e pianificazione della produzione sono responsabili fino al 90% dei costi del ciclo di vita di un prodotto, e questo quando un componente nemmeno ancora esiste fisicamente.
È quindi necessario prendere tutte le misure possibili all’inizio del processo per consentire una produzione affidabile, senza errori ed economica.
L’uso di simulazioni numeriche ha un ruolo importante in questa fase: i test fisici di prodotti o processi sono sostituiti o affiancati da test virtuali al computer, il che riduce drasticamente i costi di produzione dei prototipi. Inoltre, si riducono i tempi di sviluppo e consegna del prodotto attraverso analisi e convalide sul modello virtuale, migliorando così la qualità del prodotto stesso.
Per il successo delle aziende manifatturiere, sono decisive l’analisi virtuale di producibilità e le simulazioni del processo di produzione prima della produzione effettiva.
Poiché le modifiche al prodotto o al processo di produzione sono spesso associate a un notevole impegno in termini di test e verifica, i costi possono aumentare rapidamente e smisuratamente.
In pratica, grazie alla simulazione si può ottenere un risparmio di circa il 50 per cento nei costi di processo e sviluppo.
I costi di produzione possono essere ridotti fino al 30 per cento attraverso un migliore uso delle macchine, ottimizzazione della sequenza delle fasi produttive, un uso più sostenibile dei materiali e una messa a punto più agevole.
L’ingegneria del valore
I processi di produzione e lavorazione assorbono oltre il 90% dei costi totali del ciclo di vita di un prodotto; tuttavia, fino al 70% di questi costi sono determinati da decisioni prese all’inizio del processo di creazione del prodotto. Prima di effettuare investimenti significativi (strumenti, sistemi o attrezzature), è possibile prevedere i costi dei materiali, i costi di produzione e la fattibilità in fase di progettazione. Questo processo è noto come ingegneria del valore.
Virtual Lifecycle Manufacturing – il processo di produzione virtuale
Come descritto in precedenza, l’industria 4.0 prevede un ambiente di lavoro connesso in rete lungo l’intera catena del valore.
Per questo motivo, MSC Software è focalizzata sullo sviluppo di una piattaforma di soluzioni strategiche nell’ambito della produzione intelligente: Virtual Lifecycle Manufacturing.
Virtual Lifecycle Manufacturing permette di ottenere ulteriori risparmi sui costi e miglioramenti della qualità attraverso una combinazione di diverse soluzioni software.
L’uso mirato di specifiche soluzioni di simulazione industriale della produzione nelle prime fasi di sviluppo gioca un ruolo centrale.
I dati di misurazione dei processi reali sono di solito disponibili solo per la valutazione e l’analisi della qualità del processo e del prodotto quando i test dei prototipi o la produzione sono iniziati.
Grazie al ciclo di produzione virtuale, i dati di misurazione virtuali sono generati dalla simulazione usando soluzioni software intelligenti, ed elaborati e analizzati con gli stessi metodi e nello stesso sistema di gestione dei dati e della qualità delle misurazioni reali.
Inoltre, è possibile prendere in considerazione i dati di misura reali, in modo da permettere un confronto diretto con i parametri di misura virtuali e i dati CAD nominali con una logica di valutazione uniforme.
Tutti i dati di misura virtuali ottenuti dalla simulazione avanzata e i dati di misurazione fisica possono essere registrati, analizzati e documentati in una piattaforma integrata.
Questa vasta raccolta di dati fornisce la base per sviluppare modelli semplificati con l’intelligenza artificiale o il machine learning per ottenere rapidamente informazioni utili a ottimizzare il processo ed il prodotto.
L’obiettivo di Hexagon è di offrire questa piattaforma come soluzione scalabile per consentire alle aziende industriali di media dimensione di avere un accesso più veloce all’Industria 4.0.
Per maggiori dettagli su questa soluzione è possibile scaricare un whitepaper esteso con casi applicativi sul sito di MSC Software.
Condividi l'articolo
Scegli su quale Social Network vuoi condividere