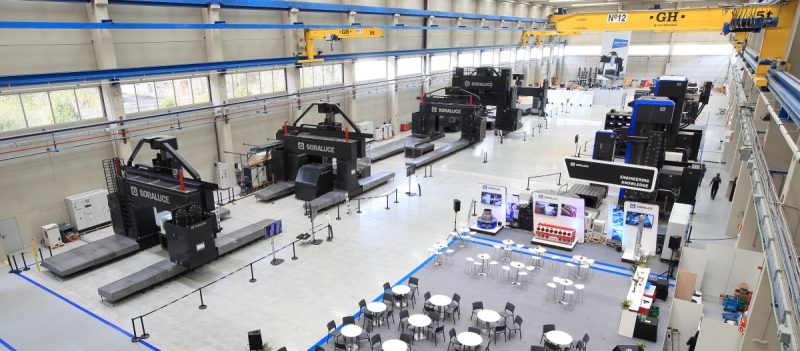
Chi si intende di macchine utensili non si ferma ad ammirare una bella carenatura o lo schermo del controllo numerico: vuole vedere “cosa c’è sotto”, apprezzare una struttura ben dimensionata, scoprire come sia possibile ottenere la precisione senza rinunciare a potenza, velocità e flessibilità operativa.
Quando un costruttore dà la possibilità di visionare le proprie macchine sin dalle prime fasi di assemblaggio dimostra una grande sicurezza nella qualità del proprio lavoro. Non solo: vuole fare breccia proprio nel cuore degli utilizzatori più attenti.
La visita del nuovo stabilimento Portal Factory di Soraluce, all’interno del quale verranno costruite tutte le nuove macchine a portale di medie e grandi dimensioni del gruppo, è stata l’occasione per toccare con mano le soluzioni del costruttore spagnolo.
Soraluce vanta un parco macchine installato nel mondo di 2.800 modelli. In una ideale classifica, l’Italia si piazza al secondo posto dopo la Germania con circa 450 unità, ma ancora più significativo è il dato che vede l’80% dei clienti tornare a comprare le macchine di Soraluce: segno di soddisfazione per la tecnologia e per il servizio.
Tecnologia Soraluce in mostra
Costruire macchine a portale di medie e grandi dimensioni è una sfida logistica. Innanzitutto occorre una attenta progettazione dello stabilimento stesso: nel Soraluce Portal Factory in passato il gruppo effettuava lavorazioni per il settore ferroviario. Per renderlo idoneo alla nuova destinazione d’uso sono stati piazzati oltre 700 pali di fondazione in cemento per stabilizzare la pavimentazione. Chi ha in officina macchine di queste dimensioni, infatti, sa quanto sia importante un buon pavimento industriale.
In occasione dell’inaugurazione lo stabilimento è stato adibito temporaneamente a showroom: qui una decina di macchine gantry configurate in vari modi (a traversa fissa, a traversa mobile, con e senza cambio teste ecc.) erano a disposizione dei visitatori con demo tecnologiche di vario tipo.
Soluzioni consolidate e alcune novità
Che le moderne macchine siano dotate di una sofisticata elettronica è indubbio: riduce gli errori, compensa le dilatazioni termiche e aiuta gli operatori a ottenere sempre le massime prestazioni e in modo ripetibile.
In Soraluce tengono però a precisare che la qualità di una buona macchina inizi a livello meccanico, la struttura delle macchine Soraluce infatti è interamente in ghisa (basamento, montante, carro e slittone): ciò con importanti vantaggi in termini di stabilità geometrica, garantendo maggiore precisione nella lavorazione dei pezzi, e con un eccellente assorbimento delle vibrazioni, ottenendo così un minore stress meccanico della macchina e una conseguente maggior produttività.
Per la dilatazione termica, in particolare, non ci sono scappatoie: alla fisica non si comanda. Per ridurre al minimo gli allungamenti i progettisti Soraluce hanno cercato di eliminare le fonti di calore (ad esempio sostituendo le trasmissioni di potenza con motori a trasmissione diretta) e utilizzando appositi sistemi di raffreddamento e un opportuno isolamento termico così da evitare la propagazione del calore verso altre parti della macchina.
DAS+ è un sistema conosciuto e apprezzato da chi lavora particolari critici per dimensioni, spessori o geometrie. Grazie ad appositi sensori posizionati nel Ram, è in grado di valutare vibrazioni anomale e intervenire di conseguenza attraverso un sistema elettromagnetico con masse che variano le frequenze innescate. La prima conseguenza è un netto miglioramento della qualità superficiale del pezzo, ma si ottiene anche un significativo incremento della vita utile degli utensili e un minore stress meccanico sulla macchina allungando così i tempi tra un intervento di manutenzione e il successivo.
Equivalente del DAS, ma da applicare magneticamente al pezzo, il DWS è un dispositivo sensorizzato che monitora le vibrazioni sul pezzo. Pur non essendo connesso elettronicamente con la macchina, è agganciato al pezzo in lavorazione in un punto critico (tipicamente dove si innescheranno le vibrazioni, come ad esempio in prossimità di pareti sottili) per controbilanciare le vibrazioni in tempo reale. Una dimostrazione pratica durante l’open house ha evidenziato l’efficacia del DWS persino in condizioni limite.
Una delle macchine esposte è stata attrezzata per effettuare anche cicli di rettifica: pur non nascendo specificamente per eseguire queste operazioni, talvolta può essere utile realizzare semplici cicli di rettifica cilindrica. Lo scambio di informazioni sulle rispettive tecnologie è un fattore chiave nel progresso delle diverse realtà del Gruppo Danobat a cui appartiene Soraluce; infatti, gli specialisti di Soraluce hanno attinto dalla competenza di Danobat (l’azienda specialista di rettifica del Gruppo) per ottenere un risultato di qualità.
La possibilità di cambiare le teste di lavorazione (attualmente Soraluce ne ha a catalogo oltre 50 modelli diversi) è un valore aggiunto molto apprezzato dagli utilizzatori.
Alcuni costruttori sacrificano parte del campo di lavoro posizionando il magazzino teste in un punto comodo per il pick-up da parte della macchina, ma che talvolta costituisce un ingombro che rende inutilizzabile la parte terminale della corsa.
Soraluce ha pensato a un magazzino posizionato oltre fine corsa: una volta chiamato il cambio di una testa, questo si apre “porgendo” il magazzino all’interno del campo di lavoro. In questo modo la corsa in X resta tutta disponibile per la lavorazione e si evita di adibirne una parte per il semplice cambio delle teste.
Tutte le macchine sono equipaggiate con l’ultima versione di controlli numerici Heidenhain da 19”, ma il trend è quello di salire ai modelli da 21”. Non si tratta di un vezzo estetico, ma di un vantaggio oggettivo derivante dall’utilizzo della recente interfaccia SmartHMI progettata da Soraluce appositamente per questi CNC. Consente infatti di gestire in modo più flessibile la visualizzazione delle informazioni: una singola schermata può accogliere più applicazioni contemporaneamente, in qualsiasi modalità (schermo intero, finestre affiancate ecc.) e di aggiungere anche in un secondo momento anche altre applicazioni, come il sistema di gestione delle commesse tramite barcode per immettere informazioni senza possibilità di errore.
VSET è un software che consente, applicando appositi marker ai pezzi e fotografandoli fuori macchina, di posizionare il modello 3D all’interno del volume del grezzo. Ciò consente di gestire al meglio i sovrametalli affinché risulti orientato nel miglior modo possibile garantendo un allineamento del pezzo grezzo fuori dalla macchina aumentandone la disponibilità. L’alternativa è rappresentata dai sistemi laser tracker, che però necessitano di personale con competenze specifiche.
Soraluce Data System è infine un pacchetto per il monitoraggio completo delle macchine che permette di tenere sotto controllo un gran numero di parametri e variabili – come consumi, eventi specifici e allarmi – per creare un database storico o segnalare una criticità a un operatore.
Ciascuna tecnologia citata viene immessa sul mercato solo dopo aver superato una serie di prove pratiche anche all’interno di Goimek, quella che può essere considerata l’officina meccanica del gruppo Danobat.
Goimek si occupa infatti della costruzione di gran parte dei pezzi che vengono montati sulle macchine Soraluce e Danobat: constatare in prima persona il comportamento delle soluzioni, eventualmente correggendole dove necessario, consente di portarle sul mercato già con il giusto livello di maturità.
Dove nascono le teste
A poche centinaia di metri dallo stabilimento Portal Factory c’è il capannone nel quale è nata Soraluce nel 1962: qui si occupano dell’assemblaggio dei moduli delle guide degli assi X e della costruzione delle teste. Queste ultime sono tra gli elementi chiave di una moderna macchina utensile e racchiudono buona parte della tecnologia che consente a un’officina meccanica di lavorare con la precisione richiesta.
Per questo i componenti più critici sono fresati su una Yasda posizionata in ambiente climatizzato e opportunamente raffreddata per contenere le dilatazioni termiche. Il tutto viene misurato su una macchina tridimensionale Zeiss e avviato al reparto di assemblaggio, dal quale escono fino a 250 teste all’anno.
Le teste vengono poi collegate ad appositi banchi prova nei quali avviene il “rodaggio” prima dell’installazione in macchina.
Stesso destino è riservato alle teste che necessitano di revisione: qualora fosse necessario intervenire su modelli anche datati, una volta ripristinate dovranno superare gli stessi test di quelle nuove con cicli che ne simulano l’impiego sotto sforzo monitorando temperatura, tenuta del lubrorefrigerante interno ed esterno, geometrie ecc.
Nel cuore delle idee
IK4-Ideko è il centro ricerche e sviluppo del gruppo Danobat. Fondato nel 1986, vede oggi impegnate 120 persone nello studio e nell’industrializzazione di soluzioni per il manifatturiero.
Indicativamente circa il 50% dell’attività è di ricerca pura, mentre l’altra metà serve a rendere applicabili scoperte e invenzioni alle macchine utensili. Qui è nato ad esempio il sistema DAS, sviluppato dapprima per la verifica delle conseguenze delle vibrazioni su pezzi e utensili e, in un secondo momento, reso disponibile sulle macchine Soraluce.
Un’altra attività di ricerca attualmente in corso riguarda un sistema per la calibrazione volumetrica delle macchine.
Utile per verifiche periodiche o per ripristinare la macchina in caso di piccole collisioni, la calibrazione rapida richiede circa 30 minuti, a differenza di una calibrazione completa che può essere eseguita in circa 4 ore.
Condividi l'articolo
Scegli su quale Social Network vuoi condividere