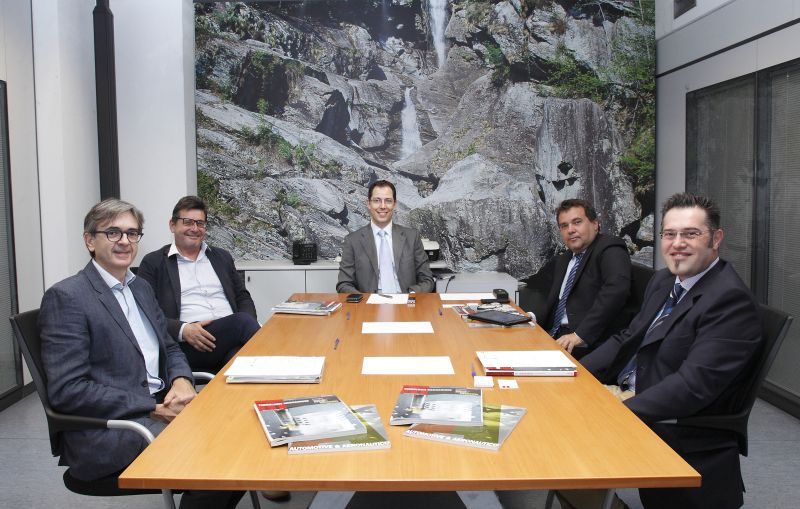
Hanno un enorme potenziale e sono in grado di rivoluzionare le lavorazioni meccaniche: le tecnologie additive presentano molti vantaggi, ma hanno anche delle peculiarità che le rendono complesse da affrontare e da gestire con profitto
Sono una delle idee più promettenti nel mondo del manufacturing: le tecnologie additive hanno un potenziale incredibile, tanto che gli stessi costruttori di macchine e software indicano come “la creatività del progettista” il reale limite di queste tecnologie. Che è un po’ come dire che il limite non esiste! Esiste un “ma”: occorre comprenderle, integrarle nel modo corretto, sfruttarle a dovere e avere il coraggio di ammettere che non sono la soluzione a tutti i problemi manifatturieri. Il maggior lavoro va quindi fatto più sul piano formativo che su quello tecnico; nel frattempo abbiamo incontrato alcuni produttori e distributori di queste macchine, in particolare legate al settore della sinterizzazione selettiva delle polveri metalliche, per avere un quadro più completo.
In che modo le tecnologie additive stanno cambiando il settore manifatturiero? Quanto quest’ultimo è pronto e informato per utilizzarle al meglio e qual è la vostra parte nel processo formativo?
Giuseppe Lazzarini – DMG MORI
«Noi realizziamo una macchina fresatrice a 5 assi molto particolare, ibrida, con in aggiunta un dispositivo di riporto delle polveri con il laser; non sempre viene immediatamente recepita dal cliente italiano, perché di fascia molto alta e quindi non viene considerata inizialmente come vantaggiosa. A tal proposito stiamo proponendo questo sistema in tutte le fiere di settore e alle nostre open house, ma fino ad oggi, specialmente nel nostro paese, non abbiamo ancora una domanda significativa. Al momento, visto il tipo di tecnologia e il costo della macchina, è più rivolta al settore dell’aerospace e dell’energia, ma non è un impianto facile da introdurre in questo mercato proprio perché, per tradizione, si muove con una certa prudenza».
Paolo Capelli – RF Celada
«Celada dispone di un gruppo di persone che analizza le nuove potenzialità di mercato, occupandosi del portafoglio prodotti: parte della nostra attività è proprio quella di valutare quelle che possono essere le nuove tecnologie applicate al mondo della macchina utensile, che continua a essere il nostro core business. Abbiamo iniziato a interessarci di additive manufacturing nel 2013, analizzando quelli che erano i brand che dominavano il mercato così che Sodick, una delle nostre case rappresentate, ha annunciato nel 2014 l’introduzione sul mercato di una macchina innovativa che ha riscosso da subito un grande interesse. Parliamo ai nostri clienti di questa macchina per l’additive manufacturing come di un’opportunità che può essere introdotta principalmente nel mondo della costruzione stampi: Sodick da quarant’anni lavora per questo particolare settore e ha voluto quindi introdurre una nuova tecnologia nel processo di costruzione dello stampo. In questa fase stiamo cercando di fare un’operazione formativa sulla clientela, cercando di spiegare al meglio limiti e vantaggi di questa nuova tecnica di produzione».
Enrico Orsi – Renishaw
«Noi siamo produttori di una macchina che realizza pezzi con il metodo del “letto di polvere”, che si caratterizza quindi per dimensioni ridotte e un dettaglio molto buono. Detto questo, per quanto riguarda la diffusione sul mercato della tecnologia di additive manufacturing c’è ancora molto da fare, anche se l’interesse è altissimo e ci sono buone prospettive all’orizzonte: siamo dunque nella condizione di dover fungere, oltre che da distributori di macchine, anche da persone che seguono i clienti, dalla fase di acquisizione dell’ordine, a quella dell’assistenza e formazione post-vendita. Rispetto ad altre nostre linee di prodotto più tradizionali, quindi, ci troviamo a essere più concentrati sul lato formativo, di analisi prevendita e preparazione del mercato all’accettazione di questo nuovo modo di produrre. Un compito certamente impegnativo, molto importante e che darà i suoi frutti sul lungo termine: al momento, in alcuni ambiti sono state individuate applicazioni verticali di successo, che comportano grandi vantaggi dal punto di vista economico, logistico e della qualità di produzione, che hanno trovato la loro strada. Il punto chiave del passaggio dall’applicazione molto specifica, come potrebbe essere quella della protesi dentale per esempio, ad un ambito più ampio, avverrà sicuramente attraverso differenti metodologie di progettazione».
Vito Chinellato – EOS
«Anche noi siamo attivi nel campo del “letto di polvere” puro e dividerei il mercato in applicazioni orizzontali e verticali: da un punto di vista delle prime, direi che manca una buona informazione diffusa in quanto l’Italia sconta la carenza storica del mondo universitario rispetto ai nostri concorrenti europei, sebbene negli ultimi anni gli atenei si stiano muovendo. Per quanto concerne le applicazioni verticali, invece, esistono dei picchi di assoluta eccellenza a livello mondiale in alcuni settori: come il biomedicale».
Quali sono i settori maggiormente attivi nell’integrare le tecnologie additive nei propri processi produttivi? Come cambia l’approccio (progettuale, costruttivo ecc.) ai manufatti, sulla base delle nuove tecnologie?
Vito Chinellato – EOS
«La progettazione, lo ribadisco, è il punto di partenza per l’utilizzo di questa nuova tecnologia. In tema di settori, oltre medicale ce ne sono diversi che stanno prendendo in considerazione le tecnologie additive: l’oil&gas, che ha già iniziato con l’acquisto di impianti direttamente per la produzione, il comparto dell’energia che inizierà in modo massiccio nel giro di qualche anno, e l’aeronautico che a mio parere offrirà diverse sorprese anche in Italia, oltre che negli Stati Uniti».
Enrico Orsi – Renishaw
«I settori sono quelli appena elencati, ovvero medicale, petrolifero, energetico, aeronautico e, aggiungerei, automobilistico sportivo: vedo che si stanno aprendo applicazioni molto interessanti anche nel settore spaziale, un comparto di non ampie dimensioni come altri, ma che contiene moltissima tecnologia e dove troviamo numerose eccellenze italiane, che collaborano con l'Agenzia Spaziale Italiana. Tutti questi settori sono in ogni caso contraddistinti dall’avere componenti ad alto valore aggiunto e dal fatto che riprogettare e ripensare il processo produttivo è stato un procedimento più semplice: qui, infatti, è più facile prendere in considerazione nuove soluzioni al fine di ottenere i miglioramenti richiesti. Un piccolo vantaggio può portare grandi benefici nell’applicazione, quindi c’è maggiore apertura nell’impiego di queste soluzioni».
Paolo Capelli – RF Celada
«Credo che i settori trainanti in questo momento siano quelli già elencati e che, probabilmente, in futuro non potranno fare a meno dell’additive manufacturing a causa di tutta una serie di vantaggi ottenibili sia dal punto di vista dei manufatti realizzabili, sia per la velocità di lavorazione del processo. Esistono anche altri settori che si stanno avvicinando a questa nuova tecnica: nel mondo degli stampi plastica, ad esempio, lo studio dei raffreddamenti conformali e la conseguente produzione degli stampi garantirà lo stampaggio di oggetti con migliori performance e con risparmi economici non tanto sul singolo componente, ma nel processo completo. Una parte, quest’ultima, da sviluppare con gli utilizzatori perché ancora oggi, quando parliamo di costi, si pensa più frequentemente al singolo oggetto che al costo del processo completo che serve a realizzarlo, il quale determina in realtà il reale costo finale».
Giuseppe Lazzarini – DMG MORI
«Concordo pienamente con i colleghi sui settori d’interesse dell’additive manufacturing, aggiungendo anche il comparto dell’aeronautica militare, all’interno del quale ci stiamo cimentando in alcuni studi e prototipazioni. La cosa fondamentale è quella di pensare e progettare, sin dall’inizio, con la mentalità che questa nuova tecnica produttiva impone perché potremo produrre pezzi che, oggi, non possono essere realizzati. Noi, che ci occupiamo di additive manufacturing con macchine ibride a 5 assi, abbiamo la possibilità di progettare direttamente con un modello matematico; stiamo inoltre lavorando sulla progettazione con un software Cad/Cam ibrido, in grado di pensare sia alla parte di deposito delle polveri, sia a quella di asportazione di truciolo “tradizionale”. L’altro aspetto fondamentale è quello della visione del materiale in senso metallurgico perché, soprattutto nell’automotive e nell’aerospaziale, c’è necessità di avere la certezza che il materiale stesso, una volta depositato, non sia solo conforme alle specifiche e alle tolleranze, ma sia simile, se non del tutto uguale, ai materiali di concezione tradizionale».
In questo settore prevale la ricerca della convenienza produttiva (legata a tempi, costi ecc.) o la possibilità di realizzare pezzi, altrimenti impossibili da ottenere con le tecnologie convenzionali?
Giuseppe Lazzarini – DMG MORI
«Devo dire che, al momento, il 90% delle macchine vendute è andato ad aziende che si occupano di ricoperture e riparazione, quindi utilizzano la macchina per tecnologie convenzionali e trovano più conveniente riparare uno stampo piuttosto che rifarlo. Solo il 10% delle aziende, invece, si occupa di costruzione e progettazione di pezzi con l’additive manufacturing e questi clienti sono anche molto gelosi dei propri processi, per cui hanno acquisito l’impianto e il software per poi proseguire in totale autonomia e con buona soddisfazione: questo ci dà conforto nel poter dire che siamo sulla strada giusta».
Paolo Capelli – RF Celada
«Dobbiamo essere consapevoli che l’uso dell’additive manufacturing spesso offre vantaggi relativi allo specifico settore a cui si applica, con meno evidenti diffusioni trasversali dei potenziali vantaggi. Se guardiamo il settore dell’aeronautica, a parte le caratteristiche tecniche innegabilmente necessarie alla realizzazione del componente, spesso il risparmio di peso è una cosa molto importante e, dunque, la capacità di questa nuova tecnologia di ridurre il peso dei pezzi punta proprio verso questa direzione. Guardando al medicale, poi, la potenzialità dell’additive manufacturing è quella di riuscire a realizzare componenti che abbiano una perfetta compatibilità biologica. Portando il tutto nel campo della meccanica generale, il cliente che adotta questo nuovo metodo di produrre ottiene un risparmio nelle tempistiche di processo: infatti, per particolari di stampi che vengono da subito pensati con questa metodologia, il risparmio arriva anche al 50% del time to market e l’efficienza del suo utilizzo aumenta fino al 30% rispetto ai medesimi ottenuti con metodi produttivi tradizionali».
Enrico Orsi – Renishaw
«Concordo sul fatto che, in questo momento storico, diversi settori hanno ottenuto benefici differenti tra loro nell’adozione della produzione additiva, quindi è difficile fare una valutazione di tipo statistico su una scala di importanza. Quello che è certo è che, tra i vantaggi nell’uso della nuova tecnica produttiva, ce ne sono alcuni ancora completamente inesplorati, che possono andare dall’alleggerimento del peso alla biocompatibilità, fino al risparmio economico (inteso sull’intero processo e non sul singolo componente). Il settore dentale ha fatto invece il contrario, portando risparmi sul pezzo singolo ma, alla fine, il resto del processo è rimasto invariato e i dentisti continuano a preparare le protesi dei pazienti allo stesso modo: il che va a indicare che l’additive manufacturing in questo campo ha vissuto un suo picco e, ora, vive una sua maturità, con difficili sviluppi ulteriori nell’immediato futuro. Futuro che, invece, si vede in altre applicazioni in cui non si ripensa il componente solo nell’ottica del risparmio, ma anche delle prestazioni superiori, rivedendo interamente il sistema in base alle nuove capacità di produzione del componente».
Vito Chinellato – EOS
«Ritengo che il tutto debba essere sempre ripensato in una logica legata ai costi: l’utilizzatore è guidato inevitabilmente da una questione di risparmio economico e, qui, ci sono quelli più evoluti che questo risparmio lo misurano nel ciclo di vita del prodotto, mentre altri nel singolo pezzo. Sarà alla fine il mercato che deciderà chi avrà avuto ragione, anche se una certa lungimiranza, e quindi un approccio di processo sembra la strada più promettente».
Qual è il tasso di crescita relativo all’utilizzo delle tecnologie additive e quali sono i vantaggi più apprezzati dagli utilizzatori?
Vito Chinellato – EOS
«I tassi di crescita in Italia si misurano a due cifre, dal 20 al 40%, e sono assolutamente in linea con quelli a livello mondiale: questo ci fa ritenere che l’additive manufacturing farà decuplicare i fatturati nei prossimi tre o quattro anni. I benefici che ne trarranno gli utilizzatori non sono facili da individuare, perché i clienti che conosciamo sono molto gelosi del loro processo e non diffondono informazioni specifiche in tal senso. Inoltre, se l’azienda pensa sin dalla fase di progettazione a questa nuova metodologia di produzione, le ricadute che questa tecnica avrà sul prodotto saranno estremamente importanti e tutte le società che negli ultimi anni vi hanno investito continueranno a farlo anche perché, a differenza dell’asportazione di truciolo (che fa registrare solo piccoli miglioramenti poiché ormai la tecnologia è matura) la sintesi additiva ha margini di crescita enormi. Noi abbiamo clienti con già oltre 10 macchine installate, a riprova che se si imbocca la strada giusta poi i vantaggi arrivano e giustificano gli investimenti in questa tecnologia».
Enrico Orsi – Renishaw
«I tassi di crescita sono abbondantemente a due cifre e, anche se il numero di aziende, di applicazioni, di macchine e di pezzi è ancora ridotto, riteniamo che crescerà velocemente nei prossimi anni. Oltretutto, anche se pensiamo alle centinaia di migliaia di macchine ad asportazione di truciolo che ci sono in giro e quelle dell’additive manufacturing, che saranno ad oggi qualche centinaio, va detto che le due tecnologie non sono affatto in contrasto tra loro (questa è una credenza da sfatare) ma, anzi, ci saranno sempre più operazioni ibride in futuro. Vediamo dunque una crescita rilevante davanti a noi e i tempi sono limitati solo dalla difficoltà nel raggiungere la testa e il cuore dei progettisti. Per ciò che concerne i vantaggi, anche nel nostro caso le aziende sono molto riservate in tal senso, ma è evidente che ci sono e sono notevoli, visti gli investimenti che hanno operato le società in questi ultimi tempi. Dobbiamo anche dire che questo è il primo cambiamento di tecnologie produttive in decine di anni e il mondo forse non è abituato a simili modifiche nei propri metodi proprio per l’abitudine a pensare le cose in un certo modo e a realizzarle do conseguenza».
Paolo Capelli – RF Celada
«Anche noi vediamo tassi di crescita analoghi a quelli espressi dai miei colleghi e questo ci dà più che altro l’indicazione delle potenzialità di questo mercato che, fino a qualche anno fa, si limitava al concetto di prototipazione 3D mentre oggi punta alla produzione vera e propria. Abbiamo un’infinità di casi di aziende che adottano l’additive manufacturing ormai in maniera stabile e consolidata per la costruzione di particolari anche molto delicati dal punto di vista della sicurezza e dell’affidabilità. Vediamo dunque molto interesse da parte delle grandi aziende, che ovviamente tengono ben nascosti i segreti dei propri processi; anche le piccole e medie imprese italiane, vero e proprio motore del Paese, si stanno attivando in tal senso avvicinandosi con fiducia a questa nuova tecnica di produzione e cercando di sfruttare tutti i benefici di una metodologia capace realmente di cambiare la relazione tra il prodotto e il processo».
Giuseppe Lazzarini – DMG MORI
«La crescita dell’additive manufacturing sta viaggiando sicuramente a due cifre, soprattutto sul lungo periodo. Abbiamo più volte ripetuto il concetto di “pensare in additivo” legato all’utilizzatore finale di un determinato componente ma, ad oggi, tutta la parte di contoterzisti in Italia non ha accesso a questa tecnologia perché da un lato l’investimento economico (in termini di macchinari, ma anche di formazione) è decisamente elevato e, dall’altro, perché al terzista non è richiesto questo tipo di pezzi. Questo è il limite che io vedo, nel breve periodo, per questa tecnologia, mentre nel lungo periodo probabilmente vedremo un 20% di crescita della produzione additiva anche per chi non ha un proprio prodotto, soprattutto quando si comincerà a pensare tutta la costruzione di un particolare in funzione di questa nuova tecnica. Per quanto riguarda la nostra macchina, i vantaggi che le aziende hanno con l’utilizzo delle nuove soluzioni in sintesi additiva sono la velocità di deposito, circa 10 volte maggiore rispetto alla tecnologia concorrente del letto di polveri, oltre che la possibilità di apporre esattamente la quantità di materiale che serve, senza scarti di alcun genere e la lavorazione del particolare in un unico piazzamento».
I materiali di consumo (polveri metalliche, plastiche ecc.) sono fondamentali per un processo ottimale: quali sono le vostre proposte in tal senso (fornitura diretta, specifiche particolari, massima libertà per l’utilizzatore, ecc.)?
Giuseppe Lazzarini – DMG MORI
«Noi abbiamo fatto la scelta di lavorare su materiali e polveri reperibili in commercio per cui, data una certa specifica, lasciamo libero il cliente di approvvigionarsi dove crede. I colleghi della Germania mi dicono che il costo del materiale è circa il doppio dello stesso componente realizzato in fonderia, ma c’è anche da dire che la quantità di materiale asportata è veramente minima. Soprattutto nel settore aeronautico sappiamo che si parte sempre da grandi masselli, per andare poi a sfruttare il cuore del materiale esente da cricche e da tensioni (in un rapporto che può arrivare anche a 1:10), dunque, in questo senso il vantaggio economico per il cliente finale rimane, perché a conti fatti ne usa molto meno».
Paolo Capelli – RF Celada
«La fornitura delle polveri credo sia un argomento abbastanza insidioso e se ne parla spesso in occasione degli eventi dedicati alla manifattura additiva. Parlando di metalli (anche se penso che lo stesso concetto possa essere applicabile alle materie plastiche), l’idea giapponese di Sodick è quella di assicurare la massima garanzia per quello che succede all’interno della macchina, senza fare esperimenti e improvvisazioni, tenendo sempre bene in mente come l’impianto realizzi sia la forma, sia il materiale: le due cose non possono essere tenute separate, pensando magari di fare una forma ben costruita ma generando un materiale scadente. Sodick, quindi, assicura alla clientela un materiale certificato personalmente, con tutte le garanzie necessarie, oppure, nel caso il cliente stesso decida di approvvigionarsi da un fornitore differente, questo dev’essere certificato da Sodick. Ciò non significa blindare il mercato o ridurre le possibilità d’utilizzo della macchina, ma tutelare le aziende sull’affidabilità del funzionamento dell’additive manufacturing e sulla qualità del prodotto che andranno a realizzare».
Enrico Orsi – Renishaw
«Penso che l’argomento delle polveri sia molto delicato, perché sono vere e giustificate le posizioni di chi ritiene che il mercato debba permettere il libero commercio della polvere, tanto quanto quelle di chi ritiene che non possano essere acquistate anche da fornitori differenti da quello certificato. L’approccio di Renishaw è quello di permettere l’adozione di entrambe le possibilità: quando la nostra azienda consegna un impianto al cliente, fornisce i parametri tecnologici per lavorare con tutte le polveri che sono note in quel momento, garantendo però il risultato con l’utilizzo di quelle fornite da noi. Se il cliente desidera provare un materiale differente, perché ha dei vantaggi economici di catena di fornitura o per motivi differenti, è libero di farlo e Renishaw lo aiuterà comunque nella gestione del processo, essendo la nostra società una fornitrice di tecnologia e non di materia prima. C’è un altro aspetto fondamentale da considerare e cioè che quanto stiamo dicendo oggi è destinato a cambiare radicalmente nel giro di pochissimo tempo, perché siamo in un ambito in cui ci sono tre spinte fondamentali: quella di chi vuole realizzare i pezzi in additive manufacturing, quella di chi vuole vendere le macchine e quella di chi vuole fare le polveri. Tre protagonisti che stanno spingendo ciascuno in una direzione specifica ma comunque dipendente l’uno dagli altri con dinamiche assai complesse».
Vito Chinellato – EOS
«Concordo solo in parte con quanto appena affermato perché, parlando di metallo, nel periodo di ammortamento classico dell’attrezzatura il costo della materia prima è comunque una frazione che non supera il 15/20% anche con i materiali più costosi come il titanio, con un’influenza dunque molto limitata sul costo pezzo; inoltre, una buona metallurgia si gioca sulle tolleranze e non sulla stechiometria o sui residui. Ciò che vedo in futuro saranno polveri dedicate a una particolare macchina, seguendo metallurgie che oggi non esistono e che restituiranno vantaggi enormi: stiamo parlando di metalli amorfi, intermetallici di varia natura, che nasceranno sotto forma di polveri destinate a un predeterminato impianto, fornite dunque da un unico soggetto. Ciò non significa che le macchine non possano essere aperte ma, a quel punto, l’utilizzatore sarà responsabile di quello che avviene. L’approccio delle grandi aziende è strategico in questo campo, nel senso che fino a oggi con le tecnologie tradizionali le società tendevano a esternalizzare il più possibile questo tipo di attività, mentre con l’additive manufacturing hanno tutto l’interesse a portarsi in casa la produzione, senza alcuna intenzione di condividere il processo e mantenere così il know how».
Condividi l'articolo
Scegli su quale Social Network vuoi condividere