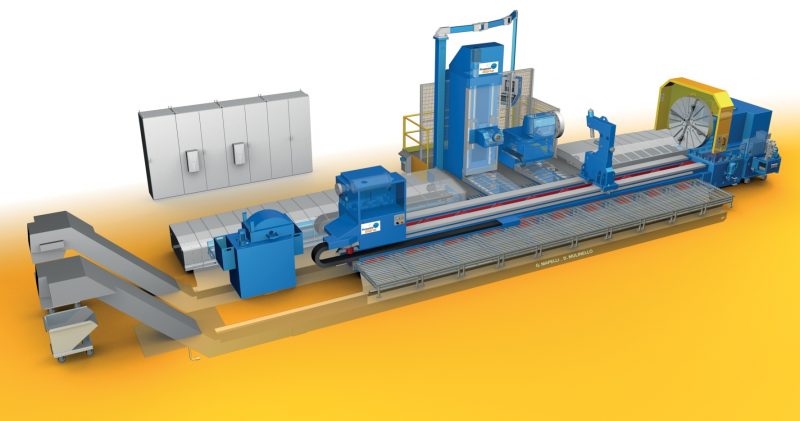
La famiglia GGTRONIC di Giuseppe Giana si amplia con un nuovo modello, sviluppato per rispondere alle molteplici necessità di un terzista e quindi adatto a settori esigenti come la meccanica generale, l’energetico e l’aeronautico.
Il 2004 è stato un anno importante per la Giuseppe Giana: un anno nel quale sono state introdotte in modo sostanziale le macchine multitasking, sviluppando una soluzione modulare in grado di rispondere in modo adeguato a esigenze di diverso tipo.
A seconda dell’applicazione, della dimensione dei pezzi e delle lavorazioni da effettuare, è infatti fondamentale poter contare su uno strumento produttivo “su misura”.
GGTRONIC, questo il nome del progetto, è nato con una specifica taglia (la 3000, con un volteggio massimo di 2.600 mm e 60 tonnellate di portata) per poi declinarsi in più modelli proprio in funzione delle specifiche dei clienti.
L’ultima nata in ordine cronologico è GGTRONIC 2000, destinata a una azienda terzista attiva in più settori, come la meccanica generale, l’energetico e l’aeronautico.
Prodotti unici, un unico progetto
Uno dei punti di forza del GGTRONIC è la polifunzionalità: semplice da usare ed ergonomica, si sposa alla perfezione alla filosofia multitasking perché, semplicemente scegliendo le dimensioni opportune e gli accessori, è possibile “costruire” una macchina ed equipaggiarla con un bareno, le lunette, un montante di fresatura, un dispositivo per il cambio utensile ecc., decidendo inoltre se lasciare la macchina scoperta o se optare per una carenatura completa per eseguire operazioni in ambienti che necessitano di maggiore pulizia e sicurezza.
Una simile configurabilità non deve però andare a discapito di altre qualità, come l’affidabilità di progetto o i costi di acquisto. Per questo i tecnici della Giuseppe Giana sono partiti subito con una progettazione che, basandosi su un numero consistente di moduli standard, fosse in grado di generare molteplici possibili combinazioni.
In questo modo ciascun modello GGTRONIC, indipendentemente dalle caratteristiche finali che presenterà, non sarà una macchina speciale, pur essendo realizzato su misura. Il limite delle soluzioni speciali, infatti, è la loro natura prototipale e il conseguente livello di affidabilità. In questo modo, a seconda delle esigenze richieste, è possibile avere un modello “standard”o impianti che sono solo lontani parenti di quelli presenti a catalogo, ma dai quali ereditano affidabilità e qualità.
Caratteristiche di prim’ordine
Il GGTRONIC 2000 oggetto dell’articolo si presenta con una altezza punte di 960 mm e una distanza massima di 8.500 mm. Questo, unito alla portata massima tra le punte senza lunette di 25 tonnellate, consente di lavorare agevolmente anche con pezzi molto grandi e complessi.
Dispone inoltre di una torretta per tornitura a disco a 12 posizioni con attacco VDI 80 e di un montante di fresatura ISO 50 Big Plus con mandrino e cambio gamma a 2 velocità.
La testa di tornitura offre una buona potenza che si sviluppa fino a 450 giri/min: grazie al cambio gamma a due velocità è possibile ottenere coppie molto elevate (fino a 25 kNm) a ogni regime.
L’avanzamento del carro può arrivare a 10.000 mm/min con una forza di spinta di 30 kN.
Anche in questo caso la macchina presenta una configurazione a doppio bancale: nata da una necessità del primo modello sviluppato nel 2005, si è poi affermata come soluzione ottimale in occasione di lavorazioni particolari, per una migliore evacuazione del truciolo e per avere la possibilità di montare tutti gli accessori di barenatura, tornitura, fresatura ecc. Inoltre, dal punto di vista progettuale consente di definire al meglio la distribuzione degli sforzi, evitando così di sbilanciare l’impianto anche durante le operazioni più gravose.
Disponendo di una intera famiglia di macchine a doppio bancale, con misure differenti del bancale anteriore e di quello posteriore, è possibile predisporre ciascuna macchina in base alle specifiche esigenze tecniche: grande diametro lavorabile con poca asportazione, piccolo diametro ma capace di supportare un grande carico e con grande asportazione ecc. In questo modo il cliente potrà contare su una macchina realmente su misura, senza che sia costretto ad acquistare un modello sovradimensionato o, peggio, senza che debba rinunciare a una funzionalità perché un determinato modello non la prevede.
Gli assi trasversali (X) funzionano grazie a un motore-riduttore che aziona una vite a ricircolo di sfere; il longitudinale (Z) viene mosso da due motori in configurazione master/slave con riduttori a recupero elettronico del gioco; la testa dispone di un motore principale con un cambio a due velocità; infine, l’asse C viene innestato tramite due motori con altrettanti riduttori master/slave che, insieme a un encoder calettato direttamente sul mandrino, offrono la massima precisione.
Con macchine di queste dimensioni è importante garantire la massima ergonomia per l’operatore, che non deve sporgersi eccessivamente sul campo di lavoro per svolgere le varie operazioni alle quali è delegato.
Anche la manutenzione risulta minima e di semplice esecuzione. Le tubazioni elettriche, idrauliche e le catene sono posizionate all’interno delle varie strutture in modo da evitare eventuali rotture dovute a proiezioni di trucioli.
Il GGTRONIC risulta di semplice gestione anche sul fronte dei comandi: dal punto di vista elettronico, il controllo numerico è in grado di gestire tutti gli assi disponibili contemporaneamente o di lavorare come un tornio tradizionale con torretta e utensili motorizzati.
Soluzioni per la qualità
Nonostante le dimensioni, rimane fondamentale la capacità di ottenere precisioni molto spinte nell’intero campo di lavoro. Il cliente ha richiesto tolleranze entro i 2 centesimi:eseguendo la prova NAS, la macchina ha dimostrato di rimanere entro 1 centesimo, meglio anche di alcune alesatrici. Ovviamente simili risultati sono raggiungibili a fronte di una attenta progettazione complessiva: il cliente ha fatto la propria parte realizzando una fondazione particolarmente stabile e robusta, sulla quale Il GGTRONIC 2000 può lavorare al meglio.Dal canto suo, la macchina vanta strutture sovradimensionate e iperstatiche, con guide a rulli che eliminano il problema dell’attrito di primo distacco; gli assi si muovono così con motori di piccole dimensioni permettendo un buon risparmio energetico.
Disponendo inoltre di rettifiche nella propria officina, nelle macchine Giuseppe Giana vengono rettificati tutti i piani, compreso il piano di bloccaggio delle guide a rulli, le geometrie del montante e del carro ecc. Oltre alla precisione negli accoppiamenti, questa procedura consente di costruire la macchina, testarla e di riassemblarla infine presso il cliente con la certezza che le varie parti combaceranno perfettamente e non avranno bisogno di particolari aggiustamenti meccanici. L’unica parte alla quale ad oggi è dedicata una operazione di raschiettatura a mano è la contropunta.
In fase di collaudo, i tecnici della Giuseppe Giana eseguono una doppia verifica tramite Laser Tracker tridimensionale e una bolla elettronica, il tutto sulla base di tabelle di collaudosviluppate internamentepartendo dall’esperienza e dal know how accumulato nel corso degli anni affiancate da test accurati per garantire al cliente la massima qualità.
Pur non essendo una priorità quando si producono pezzi unici, la macchina è in grado di operare senza presidio. Generalmente si predilige una supervisione minima da parte di un operatore, vista la natura dei pezzi: tra le opzioni, la disponibilità di un tastatore pezzo e/o utensile agevola l’operatore nell’eseguire il ciclo di lavoro.
In fase di installazione, poi, i tecnici della Giuseppe Giana presettano gli zeri macchina del montante e della torretta, lasciando all’utilizzatore la possibilità di presettare fuori macchina gli utensili. Così facendo, avendo gli zeri unici, nel momento in cui verranno eseguite in sequenza una operazione con la torretta di tornitura e una con il montante di fresatura, il secondo utensile andrà a posizionarsi esattamente alla quota nella quale quello precedente ha terminato la propria operazione, senza che l’operatore debba eseguire nuovamente l’azzeramento.
L’importanza del software
L’export è una componente chiave per la Giuseppe Giana: le macchine vengono infatti vendute in tutto il mondo e a ogni genere di cliente, da quelli più capaci ai “neofiti” del multitasking. Questo ha reso evidente la necessità di ottimizzare al massimo l’utilizzo delle macchine appoggiandosi alle capacità del controllo numerico, il Siemens 840DE solution line.
Da questo punto di vista i software installati a bordo macchina si comportano egregiamente, perché consentono di gestire un impianto anche complesso in modo molto semplice e intuitivo. Nel pacchetto integrato nei torni GGTRONIC sono presenti un modulo Cam, pagine grafiche per l’autoapprendimento, un help on line, un gestore degli allarmi, la teleassistenza ecc.
È disponibile inoltre un pacchetto di manutenzione programmata che, similmente a quanto avviene sulle automobili, indica quando è necessario eseguire una determinata verifica e quanto manca al prossimo intervento, inclusa una lista dei materiali di consumo (olii e grassi) e la tabella tecnica completa della macchina. Su richiesta del cliente è inoltre possibile aggiungere ulteriori pagine e maschere, al fine di semplificare al massimo l’utilizzo dell’impianto. In alcuni casi, infatti, queste macchine sono state utilizzate da operatori che in precedenza lavoravano su modelli manuali: per semplificare la logica di funzionamento le GGTRONIC quando torniscono si comportano esattamente come un normale tornio con due assi e il mandrino, mentre quando fresano lavorano come una fresatrice con un divisore anteriore.
Poiché l’impiego da parte degli operatori implica un certo livello di imprevedibilità, tutte le macchine sono dotate del pacchettoSafety Integrated di Siemens: una volta dichiarati i punti critici (il diametro della piattaforma in rotazione, la presenza di un bareno ecc.) il controllo numerico si comporterà di conseguenza. In presenza del bareno, ad esempio, il controllo non farà girare la torretta, mentre quando è in funzione il carro di tornitura non sarà possibile comandare il montante di fresatura per evitare una collisione.
Anche gli azionamenti possono essere opportunamente regolati: in presenza di una lavorazione delicata, con utensili o attrezzature costose, è possibile impostare il controllo numerico in modo che la potenza al mandrino o gli avanzamenti degli assi non superino determinati valori, affinché l’intero processo si svolga in piena sicurezza. Trattandosi di macchine che realizzano componenti dall’elevato valore aggiunto, la precedenza viene data all’affidabilità del processo e del pezzo rispetto alla massima velocità possibile di esecuzione.
Condividi l'articolo
Scegli su quale Social Network vuoi condividere