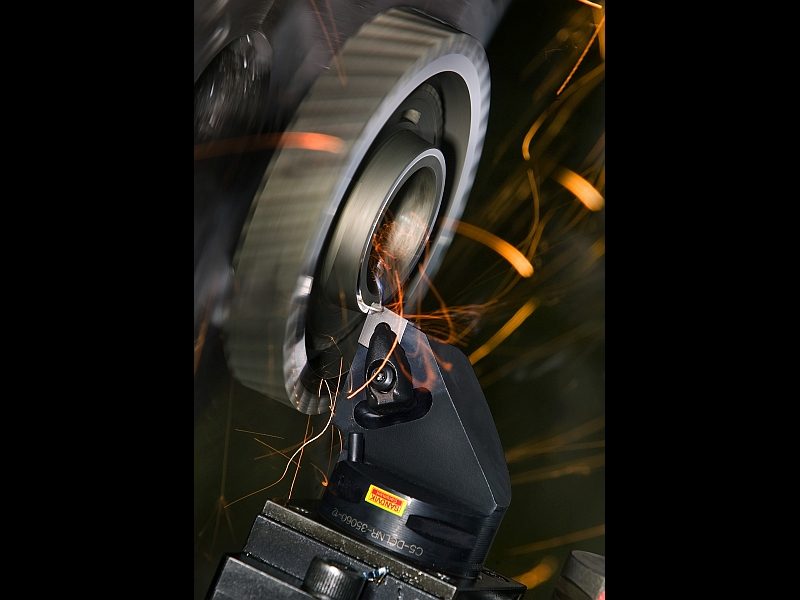
Le difficoltà nella lavorazione di un componente in acciaio sottoposto a trattamento di tempra a induzione hanno portato Denso Manufacturing Italia a rivolgersi a Sandvik Coromant per sviluppare un inserto in CBN su misura
Uno dei principali obiettivi delle Case costruttrici di automobili è quello di realizzare veicoli che consumino sempre meno carburante. Peso, efficienza del motore, aerodinamica, sistemi ausiliari, tutto è ottimizzato per permettere alla vettura di coprire maggiori distanze con quantitativi di carburante inferiori. In quest’ottica una delle soluzioni che negli ultimi anni si è diffusa maggiormente è il sistema stop/start, i cui benefici si fanno apprezzare principalmente nell’utilizzo cittadino dove semafori, attraversamenti pedonali e ostacoli vari obbligano il guidatore ad arrestare continuamente la marcia dell’automobile. In passato durante tali soste il motore restava comunque in funzione, con conseguente consumo di carburante. Il sistema stop/start invece in caso di arresto del veicolo commuta il motore in uno stato di attesa, durante il quale l’alimentazione viene interrotta, per poi riattivarlo rapidamente nel momento in cui il guidatore preme l’acceleratore. Tra i principali produttori di questo sistema figura Denso, società giapponese specializzata nella produzione di componentistica per automobili che vanta partnership di successo con i più importanti marchi automobilistici a livello mondiale.
Presenza globale
«Denso Corporation è un’azienda giapponese fondata nel 1949 con sede a Kariya, nella Prefettura di Aichi – esordisce l’ing. Luigi Bonaventura, Responsabile Parts Process Engineering di Denso Manufacturing Italia – Si tratta di una realtà dinamica, in continua evoluzione e che supporta l’innovazione con investimenti continui per migliorare costantemente prodotti e processi produttivi interni». Una testimonianza di questo approccio è il sistema QR Code, una particolare tipologia di codice a barre sviluppato da Denso nel 1994 per tracciare i componenti all’interno degli stabilimenti e diventato oggi di uso comune per il web mobile. Attualmente la società nipponica produce componenti per i gruppi motopropulsori benzina/ diesel, ibridi ed elettrici, componenti per i sistemi di climatizzazione, componentistica elettronica e sistemi di assistenza alla guida. Grazie alla qualità e all’affidabilità dei propri prodotti Denso è diventata partner dei principali costruttori di automobili a livello mondiale, e vanta quasi 150.000 impiegati operativi in più di 180 società affiliate presenti nei principali mercati d’interesse come quello italiano. «A oggi nel nostro Paese sono presenti diverse strutture affiliate a Denso che operano con obiettivi differenti, dalla produzione di componenti alla distribuzione dei prodotti – prosegue Giacomo Cupido, Parts Process Engineering Specialist di Denso Manufacturing Italia – Tra queste la Denso Manufacturing Italia di San Salvo (Chieti) è specializzata nella produzione massiva di starter, alternatori, piccoli motori e componenti per il sistema stop/start». Lo stabilimento abruzzese nel quale attualmente trovano impiego circa 1.000 dipendenti è nato nel 1972 come sito produttivo della Divisione Macchine Rotanti di Magneti Marelli, ed è diventato Denso Manufacturing Italia quando nel 2001 il Gruppo Denso ha acquisito al 100% le quote azionarie di Magneti Marelli Manufacturing.
Ra 0,6 senza rettifica
La società teatina, dunque, è specializzata nella produzione di massa dei motorini di avviamento del più recente sistema stop/ start progettato dalla Casa nipponica. Grazie a due solenoidi questi motorini sono in grado di sincronizzare la velocità di rotazione del proprio pignone con quella della corona dentata del motore, permettendo così una riaccensione più rapida del propulsore entrato in fase di attesa durante la fermata del veicolo. Uno dei componenti strategici dei motorini di avviamento è un albero lungo e sottile (diametro 11 mm, lunghezza 120 mm) realizzato in acciaio sottoposto a trattamento di tempra a induzione per conferirgli una durezza superficiale di 55 HRC. Un valore decisamente elevato che rappresenta una criticità del processo produttivo, alla quale si aggiungono le necessità di ottenere una rugosità superficiale non superiore a 0,6 μm e di rispettare tolleranze geometriche e dimensionali nell’ordine del centesimo di millimetro. «Per raggiungere il massimo livello di produttività dei nuovi sistemi stop/start abbiamo pensato di finire questi alberi direttamente su torni senza dovere introdurre un processo di rettifica: una strategia che, se implementata con successo, ci avrebbe permesso di abbattere oltre ai costi di gestione del processo anche l’investimento complessivo – spiega l’ing. Bonaventura – L’operazione di rettifica, infatti, richiede tempi di fermo impianto più lunghi per lo svolgimento delle attività periodiche di riattrezzaggio rispetto alla tornitura e un peggiore impatto ambientale. Ci sentivamo pronti per affrontare un processo di produzione diverso, innovativo, consci del fatto che, in fase di avvio produttivo, avrebbe richiesto uno sforzo tecnologico maggiore da parte di tutto il gruppo di lavoro Denso». «Il problema principale per attuare tale strategia però era trovare una soluzione che ci permettesse di lavorare su un tornio un pezzo con durezza superficiale di 55 HRC, che solitamente è lavorabile solo attraverso rettifica – precisa Cupido – Motivo per cui abbiamo attentamente valutato diverse proposte, e al termine dell’analisi abbiamo optato per l’acquisto di circa 20 nuovi torni da utilizzare quasi unicamente per l’applicazione in esame, per le fasi di sgrossatura e di finitura, realizzando anche un’isola robotizzata studiata a hoc per questi alberi».
Supporto in più fasi
Nonostante gli importanti investimenti, Denso Manufacturing Italia si è trovata ad affrontare un imprevisto che ha causato forti ritardi nella produzione del componente. «L’elevata durezza superficiale causava un consumo eccessivo dell’inserto, che nonostante i soli 6 secondi di contatto utensile/ pezzo ci obbligava a sostituire l’inserto dopo soli 30 pezzi con conseguenti ritardi nella produzione giornaliera, il tutto ottenendo alberi di qualità non adatta agli standard Denso – commenta Bonaventura – Per risolvere questo inconveniente che, di fatto, rallentava la produzione, ci siamo rivolti ai nostri fornitori di utensili trovando in Sandvik Coromant il partner ideale per risolvere il problema e potere garantire un eccellente livello qualitativo». «In questo caso non avevamo bisogno di un utensile, ma di una soluzione – aggiunge Cupido – In quest’ottica, Sandvik Coromant si è dimostrata un partner di assoluto livello facendosi carico del nostro problema e lavorando al nostro fianco per trovare un utensile e una strategia di lavorazione che ci permettessero di sbloccare la situazione». L’utensiliere è quindi sceso in prima linea impegnando Stefano Infante, Grade Development & Application Specialist Sandvik Coromant, ed Emanuele Puglia, Tecnico di Vendita area Automotive Sandvik Coromant, per identificare la soluzione più adatta all’applicazione in esame. Data la criticità della situazione che si era venuta a creare, Sandvik Coromant ha deciso di affrontare il problema con una strategia divisa in due fasi, in modo da permettere alla società abruzzese di riprendere l’attività prima possibile. Durante il primo step l’utensiliere ha effettuato numerosi studi di fattibilità per rendere concretamente realizzabile l’operazione di tornitura di materiale temprato sugli impianti acquistati da Denso Manufacturing Italia, consentendole così di sfruttare l’importante investimento portato a termine in precedenza senza dovere ricorrere all’acquisto di nuove macchine utensili. «Questa prima fase è durata molti mesi durante i quali Sandvik Coromant, con Stefano Infante ed Emanuele Puglia, è sempre stata al nostro fianco, lavorando con la massima intensità e condividendo con il team Denso lo spirito di sfida nei confronti di un processo tecnologicamente molto complesso – afferma Bonaventura – Abbiamo testato numerosi tipi di utensili e strategie di lavorazione, con inserti disegnati appositamente per noi, e alla fine siamo riusciti a trovare una soluzione su misura che ci ha permesso finalmente di rendere fattibile la lavorazione dell’acciaio temprato con una produttività e un livello qualitativo del componente finito vicini ai nostri obiettivi iniziali. Per comprendere e valutare tecnicamente questo risultato su una tornitura occorrono alcune precisazioni: un inserto standard garantisce mediamente una durata di circa 500 pezzi, tolleranze dell’ordine del decimo di millimetro e rugosità pari a 1,6, l’aver raggiunto con l’inserto speciale Coromant una durata di 250 pezzi garantendo la tornitura in capability di componenti con tolleranza diametrale inferiore al centesimo, rugosità 0,4 stabile ed usura graduale, ci consente di considerare l’hard turning come una reale alternativa al processo di rettifica convenzionale di norma impiegato su tolleranze così severe». «A questo punto, ha avuto inizio il secondo step durante il quale Denso ha ottimizzato la produzione con il supporto di Sandvik Coromant che ha offerto un pacchetto completo di utensili e strategie in grado di massimizzare l’efficienza del processo, riducendo al minimo i tempi ciclo. Sandvik Coromant ha sviluppato un inserto in CBN dotato delle tecnologie più avanzate in termini di affilatura, rivestimento e geometria che ci hanno permesso di raggiungere i nostri obiettivi di produzione – dichiara Cupido – Grazie al loro impegno oggi siamo in grado di produrre circa 2.000 alberi al giorno per un totale di circa 1,5 milioni di alberi l’anno, con una durata utensile garantita di 250 pezzi. Inoltre, la ripetibilità della qualità di lavorazione in termini di rugosità superficiale e tolleranze dimensionali e geometriche è tale per cui abbiamo eliminato il controllo al 100% dei pezzi». I risultati ottenuti hanno convinto la società teatina a estendere questa soluzione anche a un secondo albero da assemblare all’interno dei motorini di avviamento, anch’esso in acciaio temprato ma più lungo e di maggiore diametro rispetto a quello citato finora, per il quale è stato studiato un inserto su misura con raggio non ISO.
Al fianco dei clienti
Con il caso applicativo di Denso Manufacturing Italia, Sandvik Coromant ha dimostrato ancora una volta la sua capacità di porsi come partner all’interno di un rapporto che non si limita alla questione domanda/offerta. L’utensiliere svedese si fa carico in prima persona delle problematiche dei clienti facendole diventare proprie, e collabora con loro per trovare una soluzione di successo per entrambe le parti in gioco. Mettendo a disposizione personale qualificato, attrezzature tecnologicamente avanzate e strutture all’avanguardia nel campo dell’R&D, Sandvik Coromant si propone come partner di assoluto livello per affrontare le più ardue sfide offerte dal settore dell’asportazione truciolo.
Condividi l'articolo
Scegli su quale Social Network vuoi condividere