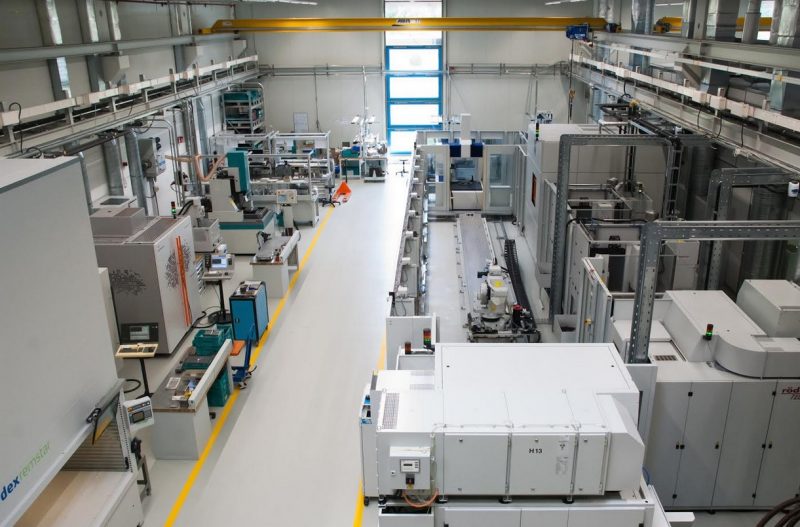
L’officina stampi di Festo Polymer a St. Ingbert è una delle più moderne in Germania e nel 2017 è stata nominata Werkzeugbau des Jahres (“officina stampi dell’anno”). Per l’elettroerosione, la fresatura di elettrodi e le lavorazione complesse, l’azienda del Saarland si affida sistematicamente all’automazione: per migliorare ulteriormente il funzionamento 24 ore su 24 e 7 giorni su 7, i processi di fresatura sono stati analizzati e ottimizzati insieme a MMC Hitachi Tool. Risultato: un minor numero di tipologie di utensili e una maggiore sicurezza del processo.
«Il trasferimento nel 2015 nella nuova sede è stato per noi l’occasione per ripensare i processi esistenti e, laddove sensato, per investire in nuove tecnologie», ha sottolineato Jörg Weber, responsabile di produzione di Festo Polymer. «Nel corso di questo processo, abbiamo sistematicamente automatizzato l’officina utensili e ci siamo concentrati sulle nostre competenze chiave». Per questo motivo, durante la fresatura complessa vengono lavorati solo componenti sagomati, grafite o parti in acciaio ad alta precisione. Nel corso degli anni Festo ha raggiunto uno standard molto elevato nel campo della fresatura. Tuttavia, l’obiettivo non è quello di “vivere sugli allori”, ma di continuare a migliorarci sempre di più, soprattutto per quanto concerne la precisione dimensionale, la durabilità degli utensili e la sicurezza del processo. Si tratta di un processo evolutivo, che presenta svariati gradi di regolazione. Così dovrebbero essere standardizzati i processi di fresatura per l’automazione. Inoltre, a St. Ingbert si era fatto vivo il desiderio di testare le operazioni di lavorazione più frequenti per ottimizzarle e renderle riproducibili in termini di selezione degli utensili, strategie di fresatura e parametri di taglio.
Per questo motivo, nel maggio 2014 è stato deciso di stringere la partnership con MMC Hitachi Tool. Il primo passo è stato quello di ottimizzare le lavorazioni complesse. Insieme al “Process Optimizer” del produttore giapponese di utensili, Stanislav Pupak-Martin, sono stati eseguiti svariati test per un periodo di tempo prolungato con pezzi in lavorazione differenti e con diversi utensili MMC Hitachi, dalla sgrossatura passando per la fresatura a tuffo fino alla finitura, così come anche la filettatura. Sono stati lavorati materiali come l’X38CrMoV5-1 (1.2343), spesso utilizzato da Festo, l’X42Cr13 (1.2083), l’X45NiCrMo4 (1.2767) o acciai Böhler come l’M390, per lo più con durezze fino a 54 HRC, e talvolta persino fino a 64 HRC, come nella filettatura sul Böhler K390.
Durante le varie lavorazioni sono state confrontate tra loro sia strategie di fresatura, sia i parametri di taglio che i differenti tipi di frese MMC Hitachi Tool. Per esempio, nella sgrossatura di un tassello in 1.2343 in Z costante, l’ottimizzatore di processo ha sostituito la fresa torica in metallo duro diam. 20 mm utilizzata inizialmente con la fresa a fissaggio meccanico torica ASRM Pico Maxi (inserti in JS 4060). Con la durata degli inserti di oltre 150 minuti, questa fresa Hitachi ha dato prova di prestazioni notevolmente superiori, nonostante il dimezzamento della profondità di passata a 0,3 mm, necessario per la tipologia di macchina utilizzata. Nel quadro dei lavori di ottimizzazione, anche le frese per filettatura EDT sono state implementate nel processo di produzione di Festo. Persino su acciai superduri questi utensili fresano in maniera diretta (ovvero senza bisogno del pre-foro) i filetti, solitamente realizzati tramite erosione a tuffo.
Incoraggiato dai significativi miglioramenti nelle lavorazioni complesse, un altro progetto è stato quello di dimostrare che le esperienze positive maturate con MMC Hitachi Tool potevano essere trasferite alla fresatura su grafite. Il metodo qui era simile a quello per l’acciaio; il processo è stato innanzitutto esaminato attentamente. Per esempio, come vengono programmati gli elettrodi? Una parte di queste operazioni è stata svolta in uno o due giorni, spesso insieme a numerosi dipendenti. Nel frattempo si sono tenuti con continuità dei piccoli laboratori in cui sono stati spiegati e discussi i nuovi parametri. In questo modo sono state stabilite di comune accordo le strategie di fresatura e i nuovi parametri di taglio, che sono stati, per così dire, studiati su misura per la fresatura automatica su grafite nell’officina stampi di Festo. Ad avere sempre la massima priorità è stata la sicurezza del processo. I nuovi valori sono stati quindi inseriti nella banca dati utensili di VISI CAM.
È stata realizzata poi una applicazione specifica per la lavorazione degli elettrodi, con l’obbiettivo di portare risultati positivi. Sono stati fresati sette elettrodi per realizzare un tassello di un pistone pneumatico, che precedentemente venivano completamente lavorati con una fresa sferica da 1 mm. L’ottimizzatore dei processi ha qui adottato il concetto di ottimizzazione “Production 50”, sviluppato da MMC Hitachi Tool appositamente per il settore della fresatura. Per quanto riguarda la fresa MMC Hitachi Tool utilizzata, si trattava della fresa sferica in metallo duro D-EPDB-2010-5 a due taglienti. Mentre prima venivano utilizzati due utensili uguali, uno per la ripresa di sgrossatura e l’altro per la finitura, la D-EPDB veniva utilizzata per tutte e due le fasi, sia per la sgrossatura e la finitura.
I parametri di taglio erano sostanzialmente gli stessi per tutti gli utensili, fatta eccezione per l’avanzamento. Con la D-EPDB è stata raggiunto un avanzamento di due volte e mezzo superiore a quella dei due candidati concorrenti. La ripresa di sgrossatura non ha apportato alcun vantaggio in termini di tempo, per via di Ap e Ae leggermente diverse. Tuttavia, Festo è adesso più veloce del 30% circa per quanto riguarda la finitura. «Insieme a MMC Hitachi Tool siamo stati in grado di migliorare notevolmente i processi di fresatura e di ridurre i tipi di utensili utilizzati, il che è molto importante per l’automazione e la standardizzazione dei processi assolutamente necessari a questo scopo», ha concluso soddisfatto Jörg Weber. «Quanto all’automazione, è altresì importante l’aver riscontrato ancora una volta degli ottimi progressi in termini di sicurezza del processo».
Condividi l'articolo
Scegli su quale Social Network vuoi condividere