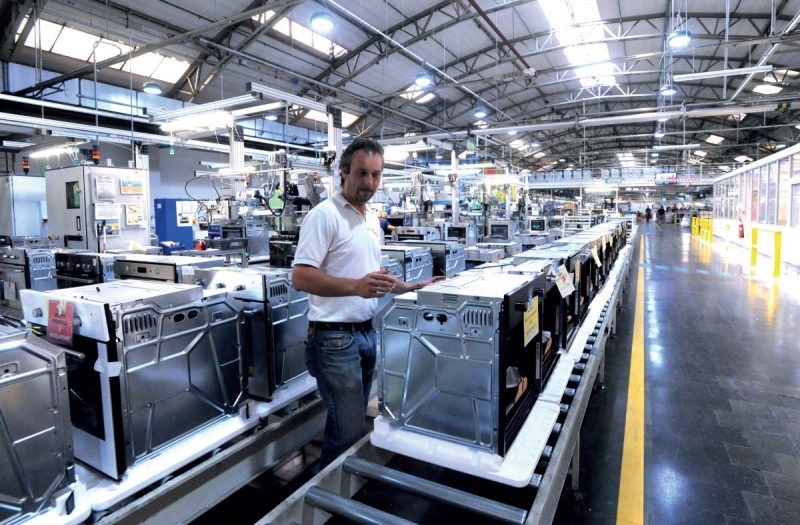
Tra i settori in cui la lavorazione della lamiera è più importante c’è sicuramente l’elettrodomestico. Scopriamo insieme visione, strategie ed esigenze di Whirlpool, uno dei maggiori costruttori mondiali.
Tra i settori in cui la lavorazione della lamiera è più importante c’è sicuramente l’elettrodomestico. Scopriamo insieme visione, strategie ed esigenze di Whirlpool, uno dei maggiori costruttori mondiali.

Quando si parla di Whirlpool Corporation, ci si trova di fronte all’azienda americana leader a livello mondiale nella produzione e commercializzazione di grandi elettrodomestici. La progressione dei fatturati, generati dalla propria capacità d’investimento in sviluppo e innovazione di prodotto, dimostra una costante capacità di crescita che ha reso possibile il lancio sul mercato EMEA di oltre 120 nuovi prodotti negli ultimi due anni. Per capire la rilevanza di questo settore nel mondo della lavorazione della lamiera, ricordiamo come ben il 30% della componentistica utilizzata negli stabilimenti produttivi della Whirlpool per la fabbricazione di un’ampia tipologia di elettrodomestici sia in lamiera (più nel dettaglio, parliamo di materiali Cold Rolled, HDG, EG, alluminati, Galfan, EK, ED, decarburati, Hot rolled o preverniciati, Aluzinc, stainless steel cold rolled BA con differenti finishing).
L’azienda in Italia
Il contributo di Whirlpool all’economia italiana è estremamente rilevante sia a livello nazionale che nei territori dove è presente con i propri impianti. Più di 6 mila dipendenti lavorano infatti in 8 centri collocati su tutto il Paese, stabilimenti destinati alla produzione e alla Ricerca & Sviluppo ma anche uffici amministrativi, centri di logistica o per il ricambio delle parti. I numeri parlano chiaro e testimoniano il ruolo centrale di Whirlpool Italia nell’area EMEA: 6 milioni di unità vendute, 1,2 miliardi di euro di costi annuali di approvvigionamento per sostenere le proprie attività produttive.
Se ci concentriamo sul nostro Paese, nel luglio del 2015 è stato firmato a Palazzo Chigi l’accordo tra Whirlpool, governo, regioni e sindacati per l’attuazione del nuovo piano industriale del Gruppo in Italia e che interesserà tutte le regioni in cui l’azienda è presente. Un impegno che per Whirlpool sta comportando investimenti per oltre 500 milioni di euro nel quadriennio 2015-2018 rivolti al miglioramento e potenziamento delle linee produttive, ma anche alla Ricerca & Sviluppo e alla creazione di nuove piattaforme logistiche internazionali. «Si tratta di un progetto solido e di lungo periodo – dichiara Massimiliano Paolucci, Central Industrial Engineering Senior Manager di Whirlpool EMEA – che accresce la centralità dell’Italia, dove sarà attuato oltre il 70% degli investimenti in Ricerca & Sviluppo previsti nella regione EMEA, oltre a creare le condizioni per offrire occupazione qualificata a centinaia di giovani. Whirlpool ha una presenza multiregionale sul territorio italiano e ha assegnato una specifica missione a ognuno dei suoi stabilimenti. L’utilizzo della capacità in Italia è stato massimizzato, anche attraverso l’insourcing di volumi produttivi dall’estero e il consolidamento di attività distribuite in specifici poli di competenza».
Entrando nel dettaglio dell’organizzazione della produzione Whirlpool in Italia, nel sito di Cassinetta di Biandronno (VA) è concentrata la produzione di tutti gli elettrodomestici da incasso (forni, microonde, frigoriferi Built-In), nello stabilimento di Siena vi è la produzione di congelatori, nello stabilimento di Comunanza (AP) si ha la produzione di lavatrici e di lavasciuga, in quello di Napoli la produzione delle lavatrici ad alta capacità e, infine, la fabbrica marchigiana di Melano (AN) costituisce il polo produttivo di tutti i piani cottura (gas, induzione, ceramica). Lo sviluppo e la sperimentazione delle nuove tecnologie vengono guidati dall’ente centrale Central Industrial Engineering, parte dell’Operations Excellence EMEA, che sperimenta e implementa le nuove tecnologie nei vari siti produttivi a seconda delle esigenze di prodotto/processo e della maturità delle tecnologie stesse. «Per affrontare le nuove sfide del mercato globale – sottolinea Paolucci – abbiamo inglobato nel Whirlpool Production System la metodologia del World Class Manufacturing, con un forte focus sul miglioramento continuo nei nostri processi e con pillars dedicati alla manutenzione e allo sviluppo impianti: Autonomous Maintenance, Professional Maintenance ed Early Equipment Management. Quest’ultimo di fatto è il pillar che ci consente di capitalizzare tutti i dati e le informazioni derivanti dalle attività di continuous improvement, dalle competenze dei nostri team di fabbrica (produzione e manutenzione) e dalle analisi di guasto nelle specifiche dei nuovi impianti, con l’obiettivo di anticipare la fase di individuazione e risoluzione dei problemi di tipo progettuale negli step che precedono l’installazione dell’impianto, di ridurre al minimo la fase di start-up (minimizzando i transition cost della fase di avvio) e di azzerare i costi di modifica impianto a inizio vita dello stesso».
Lamiera, scelte aziendali e processi
«In riferimento ai componenti in lamiera, la strategia decisionale del “make or buy” – prosegue Paolucci – si basa su una serie di driver che tendono a identificare i processi “core”, cioè quelli chiave da un punto di vista qualitativo, tecnologico e di flessibilità produttiva e logistica, i processi “not core” e i processi “swing”, per i quali di volta in volta si valuta la strategia di make or buy da adottare. Rientrano evidentemente nei processi “core” i componenti che costituiscono le parti tecnologicamente fondamentali per la performance del prodotto, come per esempio il cesto della lavatrice, la muffola del forno, la vasca della lavastoviglie e le parti metalliche che necessitano di successivi processi di trasformazioni interne come, per esempio, la smaltatura e la verniciatura. Il fornitore di componenti in lamiera deve ovviamente condividere con noi approccio e obiettivi contemplati dalla nostra metodologia di Lean Manufacturing e deve soddisfare alcuni precisi criteri». L’identikit del fornitore Whirlpool comprende quindi eccellenza nella qualità, nella tecnologia e nella capacità di fare innovazione tecnologica; dimensione internazionale e stabilimenti situati in vicinanza ai siti produttivi Whirlpool (in particolare per i bulky components) ed elevata performance in termini di delivery (Delivery Lead Time e Flexibility on delivery schedule). «Fondamentale – precisa ancora Paolucci – è anche che il fornitore abbia una base costi efficiente e allineata con le nostre richieste e sia solido finanziariamente; importanti anche un parco impianti/presse idoneo e affidabilità produttiva (che comprenda cioè efficaci programmi di manutenzione preventiva ed esperienza di produzione di massa). Valutiamo con grande importanza anche la capacità nel project management di nuovi progetti (new component readiness), una solida struttura di PM per la gestione contemporanea di progetti nelle diverse categorie prodotto e sta assumendo sempre più importanza la capacità di garantire un servizio più ampio, utilizzando tecnologie complementari al metal stamping come per esempio verniciatura, tampografia, marcatura e incisione laser». All’interno dei propri reparti di lavorazione lamiera, Whirlpool esegue l’intero processo di produzione partendo dal coil di lamiera fino al completamento del semilavorato metallico utilizzando tutti i processi di trasformazione necessari: tranciatura, imbutitura, piegatura, profilatura, joining (saldatura laser, saldatura a resistenza e al plasma, clinching, rivettatura), finishing (pretrattamento più coating, ossia smalto o vernice o special coating) e marcatura estetica (serigrafia, tampografia e laser).
Quali tecnologie per lavorare la lamiera?
L’acquisto di un nuovo impianto di lavorazione della lamiera segue un processo molto strutturato, in Whirlpool, che vede coinvolti molti enti aziendali. Per ogni specifica tecnologia vengono definiti i fornitori di riferimento che rientrano nella Suppliers Base list; questi devono rispondere a una serie di specifici requisiti che si possono riassumere in: adeguata struttura organizzativa; assistenza al cliente post installazione; know how specifico su tecnologia, flessibilità nelle scelte tecnologiche, capacità di innovare, capacità e disponibilità a effettuare sperimentazioni e sviluppi tecnici e tecnologici con Whirlpool; provata solidità finanziaria; valido livello di verticalizzazione; disponibilità di risorse e spazi per gestire l’appalto; significativa presenza sul mercato e, in particolar modo, evidenti e consolidate esperienze nel settore del bianco con presenza internazionale. «Nell’acquisto di nuovi impianti di lavorazione – spiega Paolucci – Whirlpool applica un processo cross funzionale ben strutturato che parte dalla definizione delle specifiche tecniche iniziali al processo di selezione processo/fornitore, fino all’implementazione e start up in produzione. La scelta dello specifico impianto da installare negli stabilimenti Whirlpool è infine guidata dai drivers tecnici/tecnologici a partire dal rispetto delle specifiche in termini di reliability, capability, overall equipment effectiveness e al contenuto tecnologico/innovativo dell’impianto stesso. Altri elementi che valutiamo come importanti sono la flessibilità nella gestione, sia dei componenti diversi per geometria, dimensioni e tipi di materiale sia dei lotti di produzioni estesi o estremamente ridotti con basso impatto nel change over, e la modularità intesa come capacità di inserimento, rimozione o by-pass di fasi di processo o moduli, con tempi di fermo impianto estremamente contenuti, per consentire upgrade dell’impianto per l’introduzione di nuovi componenti/estetiche. E poi ancora: riconfigurabilità, quindi possibilità di modificare parti della linea per la produzione di nuovi modelli o per la revisione di alcuni dettagli tecnici nei componenti prodotti, con fermi impianto nulli o estremamente contenuti; capacità di incrementare in modo significativo l’output dell’impianto con un investimento marginale rispetto al costo di acquisto dell’impianto stesso (la cosiddetta scalabilità); utilizzo di principi Lean nelle logiche di realizzazione di impianti o stampi; interfacciabilità con altri impianti/sistemi produttivi; usability degli impianti (specialmente per quanto riguarda le attività manutentive); presenza ed efficacia di sistemi di manutenzione predittiva; tempi di sviluppo/consegna/installazione e, non ultimo, l’impatto economico». A seconda del tipo di lavorazione e dei volumi produttivi in gioco Whirlpool impiega differenti livelli di automazione, che vanno da processi semiautomatici a linee interamente automatiche, che partono da lamiera in coil (a inizio linea) e completano in modo automatico la lavorazione fino allo scarico del semilavorato a fine processo e al controllo automatico dei parametri critici di processo e della conformità estetica del componente stesso. In taluni casi, i sistemi di lavorazione della lamiera sono interconnessi con gli impianti a valle del loro processo produttivo.
È il caso, per esempio, di sistemi di impianti lavorazione lamiera più coating, sistemi che hanno processi di automazione che consentono il trasferimento, in automatico, del semilavorato in lamiera negli impianti di pretrattamento e coating. In tal caso l’automazione parte dal coil e termina nel controllo dei parametri critici di processo e della conformità estetica del componente verniciato o smaltato. Un processo che può essere riassunto in stampaggio, piega, saldatura, controllo dimensionale, pre-trattamento, smaltatura e controllo parametri critici di processo. «Vorrei sottolineare – aggiunge Paolucci – che Whirlpool a livello globale sta lavorando da oltre un anno sul tema Industry 4.0 con un team che è stato appositamente creato con un obiettivo estremamente strategico e ambizioso: incrementare la competitività delle fabbriche attraverso il miglioramento della qualità, dei costi e della velocità di risposta grazie alla trasformazione delle attuali pratiche di gestione degli impianti, delle competenze e delle informazioni in ottica CPS (Cyber Physical System) e quindi interconnettere tra loro impianti produttivi anche geograficamente distanti, processi aziendali cross-funzionali e partner della supply chain estesa. Questo sarà un tema estremamente importante pensando all’evoluzione dei mercati e alle esigenze future degli stessi».
Guardando al futuro: le strategie
Negli ultimi 3 anni, nella regione EMEA Whirlpool ha investito 350 milioni di euro che hanno contribuito alla nascita di molti brevetti. Dal 2014 a oggi, Whirlpool EMEA ha presentato a Bruxelles la richiesta di 330 brevetti, diventando così uno dei principali innovatori tecnologici a livello continentale. Inoltre, sempre negli ultimi 5 anni, ha partecipato a più di dieci progetti di ricerca nel campo del manufacturing in vari programmi europei (FP7, H2020) e nazionali (Industria 2015, Cluster Tecnologici Nazionali). D’altro canto la ricerca puramente tecnica e tecnologica si sta di fatto sovrapponendo/integrando con i principi di produzione Lean e con l’introduzione di principi e progetti di Industry 4.0. «Volendo citare alcune delle aree su cui ci si sta focalizzando – rivela Paolucci – distinguerei tra materiali e processi. Relativamente all’influenza sullo sviluppo dei materiali ci sono importanti trend tecnologici, in cui Whirlpool è fortemente coinvolta partecipando a definire le tendenze dello specifico settore industriale, che sono riconducibili a due aree: superfici pre e post trattate. Per quanto concerne i materiali pretrattati, c’è un chiaro trend di incremento dell’utilizzo di superfici preverniciate e film colaminati (con specifiche finiture: stampati, effetti legno e marmo, decorati, metallizzati inox-look e alluminio) con evidenti implicazioni a livello di processo tecnologico su movimentazione, su taglio/piega e sulla rimozione delle pellicole e con diretto impatto sul design dei prodotti, al fine di rendere le estetiche dei componenti compatibili con le esigenze di processo. Per le superfici post trattate vi è la continua ricerca di rivestimenti tecnologicamente avanzati per aumentare la gamma estetica delle superfici in acciaio inossidabile: nuovi colori, finiture e funzionalità. Whirlpool è leader nell’applicazione di nanotecnologie su superfici in lamiera inossidabile per garantire nuove e importanti funzionalità fruibili dal consumatore (resistenza chimica, al graffio, all’ossidazione); un esempio di successo è rappresentato dai prodotti “iXelium” introdotti sul mercato nel 2009 e in continua evoluzione». Concentrandosi sul processo, in Whirlpool il focus è sullo sviluppo e sulla introduzione graduale di processi agili, cioè flessibili, scalabili, riconfigurabili e modulari. «Un primo esempio è il Robotic Hemming – racconta Paolucci – che è un’aggraffatura robotizzata grazie a una speciale testa che viene montata su un robot antropomorfo; la minore efficienza in termini di tempo ciclo rispetto a un sistema tradizionale è compensata dalla flessibilità nel lavorare su forme di elevata e diversa complessità con un investimento marginale ridotto. Un’ulteriore tecnologia sotto esame è il Flexible Piercing: consiste nella combinazione di lavorazioni meccaniche e laser per personalizzare manufatti intermedi di lamiera (come cavità, pezzi imbutiti eccetera), è tipicamente assistita da robot antropomorfi e permette di gestire complessità di produzione riducendo gli investimenti in tooling dedicati. Un campo sempre importante è quello della giunzione: essenzialmente saldature e relative tecniche di ispezione. Per ciò che riguarda le saldature innovative, siamo in costante ricerca della soluzione ottimale per l’applicazione alla lamiera; ciò ci porta a esplorare e sperimentare tecniche come saldatura ad alta frequenza, nuove sorgenti laser e tecniche di gestione del beam, giunzioni elettromagnetiche. I test non distruttivi o NDT (Non Destructive Test) per la valutazione delle saldature stanno diventando sempre più promettenti: oggi l’utilizzo combinato di laser e rilievi termografici permette di individuare difettosità in brevissimo tempo, permettendo quindi l’adozione delle stesse tecniche in controlli in linea e non più a campione. Non meno importanti sono gli altri sistemi di ispezione e collaudo “in line”, come per esempio i sistemi di visione, che consentono valutazioni estetiche e dimensionali in flusso con le linee produttive e che permettono una completa e integrata gestione dei parametri critici di progettazione (CPM, Critical Parameter Management). In tal modo si è in grado di sostituire, ove ritenuto opportuno, il controllo statistico “near the line” (comunque effettuato su un campione statisticamente significativo e con feedback veloce sul processo) con un test di fatto in linea e con informazioni in tempo reale sul processo produttivo.
Queste e altre attività di ricerca e sperimentazione sono condotte in costante cooperazione con il nostro dipartimento di Global Advanced Manufacturing e facendo leva su partner esterni come università, centri di ricerca e progetti finanziati».
Condividi l'articolo
Scegli su quale Social Network vuoi condividere