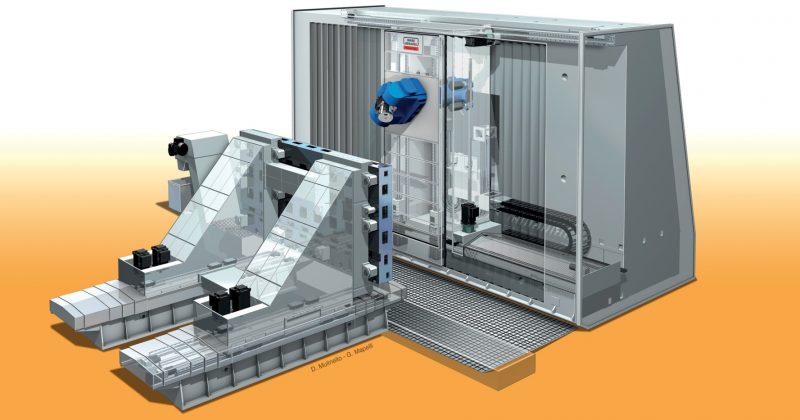
Pensata per lavorare i materiali tipici del settore aeronautico – alluminio e titanio - Zenith Vision Profiler di Innse Berardi presenta una serie di innovazioni capaci di alzare gli standard in fresatura in termini di produttività e costi di gestione
Zenith Vision Profiler è una macchina a cinque assi simultanei che nasce per sopperire alle limitazioni delle fresatrici orizzontali tradizionali nella lavorazione di materiali tipici del settore aeronautico, quali le leghe di alluminio e il titanio.
Di macchine a 5 assi con caratteristiche simili alla Zenith Vision Profiler il mercato è ricco: quello che secondo i tecnici della Innse Berardi mancava, invece, era una soluzione dedicata alla lavorazione dell’alluminio e, soprattutto, del titanio.
I modelli tradizionali presentano infatti una rigidezza differente in funzione della posizione verticale di lavoro e di uscita del ram, costringendo l’utilizzatore a sacrificare i parametri di taglio a causa della necessità di mantenere la massima precisione pur in condizioni gravose.
Una struttura studiata ad hoc
La guida aggiuntiva posta nella parte superiore del montante mobile e il movimento della tavola porta pezzo su struttura esterna assicurano prestazioni dinamiche, di precisione e di accuratezza costanti in tutto il volume di lavoro.
Le caratteristiche e le innovative prestazioni raggiungibili con la Zenith Vision Profiler sono quelle espressamente richieste nel settore aereonautico, in particolare per la lavorazione di parti strutturali i cui materiali sono le leghe resistenti al calore e il classico alluminio.
La macchina è stata perciò progettata attraverso l’impiego di software FEA per assicurare prestazioni costanti in tutto il volume di lavoro in termini di rimozione di truciolo, accuratezza e dinamica.
Questo perché, con le macchine tradizionali, l’utente spesso è costretto a scegliere le condizioni di taglio peggiori e a tarare l’intero processo su quei parametri per avere la certezza di ottenere i risultati voluti. Ciò significa in primo luogo rinunciare a parte del potenziale della macchina utensile, allungando così i tempi ciclo e il ritorno dell’investimento. Inoltre, innesca una serie di criticità legate proprio alla tipologia di materiale lavorato, ovvero le leghe resistenti al calore.
Una questione di frequenze
La dinamica di una macchina utensile è proporzionale alla prima frequenza di risonanza: da questo punto di vista i progettisti della Innse Berardi hanno fatto un lavoro molto accurato, progettando una struttura – basamento in ghisa e colonna in acciaio elettrosaldato – in grado di lavorare al meglio proprio in presenza di materiali difficili come il titanio.
La prima considerazione da fare su una macchina di questo tipo è legata al fatto che i modelli orizzontali classici dotati di ram presentano un calo della rigidezza man mano che la posizione verticale aumenta e che il ram si estende. Questo comporta sia una perdita di rigidezza, sia una perdita di dinamica. Il dettaglio più evidente di questa macchina è dunque la presenza di una guida aggiuntiva posta nella parte alta della colonna, in grado di limitare le vibrazioni e migliorare rigidità e robustezza, indispensabili quando si lavora il titanio.
Le leghe resistenti al calore, come appunto il titanio, innescano poi una serie di problematiche che vanno tenute in attenta considerazione in fase di lavorazione: il titanio viene usato per le note qualità legate al peso, alla resistenza alla corrosione e all’elasticità. Sul fronte dell’asportazione di truciolo, però, è la bassa conducibilità termica a rappresentare la principale criticità: in fase di asportazione, il calore prodotto nel punto di contatto (750-800 °C) si scarica sull’utensile poiché non viene rimosso dal truciolo, né rimane nel pezzo.
Per limitare il passaggio di calore si opera perciò mantenendo una velocità di taglio adeguata, che in sgrossatura sul titanio significa lavorare tra i 40 e i 60 m/min. La frequenza indotta da questi parametri, legata al numero di volte al secondo in cui un dente della fresa va in presa, è dell’ordine di 16-17 Hz. Ogni struttura meccanica, indipendentemente da come è costruita, ha un modo proprio di vibrare e una specifica frequenza di risonanza. La maggior parte delle strutture delle macchine sul mercato presenta una frequenza di risonanza che varia tra i 10 e i 18 Hz circa. Applicando una forzante come quella per la sgrossatura del titanio si rischia di rientrare proprio in questo range, creando una instabilità che ha un impatto negativo sugli inserti che, di conseguenza, possono deteriorarsi precocemente, scheggiarsi o rompersi.
Ci sono due modi per allontanarsi dalla frequenza critica della macchina: il guadagno di posizione e l’accelerazione cubica sono proporzionali alla prima frequenza di risonanza.
Occorre quindi spostarsi verso l’alto con le frequenze. La struttura con vincoli superiori innalza di svariati Hertz la frequenza di risonanza della Zenith Vision Profiler, allontanandola dalla zona di criticità e assicurando prestazioni migliori.
Con l’alluminio una dinamica performante permette di ridurre i tempi di lavorazione grazie a velocità più elevate a parità di accuratezza di interpolazione, mentre con il titanio si ottiene anche una riduzione del costo degli utensili.
Contenere il costo degli utensili
Lavorare in condizioni ottimali significa ottenere il massimo degli utensili: la lavorazione del titanio richiede infatti utensili particolarmente costosi, che beneficiano di un processo “pulito” e con poche vibrazioni.
I terzisti che operano nel mondo aeronautico sanno che i committenti riconoscono loro una cifra per il consumo degli utensili, ma si tratta di un valore molto vicino all’impiego ottimale degli utensili stessi. Utilizzarli “male” significa avere spese aggiuntive in officina.
Quando avviene un’interpolazione nel piano X-Y vi è uno scostamento tra la posizione richiesta dal controllo numerico e quella effettiva in cui gli assi si trovano.
Il CNC effettua perciò degli arrotondamenti al fine di recuperare questi scostamenti: all’utente è sufficiente indicare la massima discordanza ammessa tra la traiettoria ideale e quella effettiva e il controllo numerico interverrà di conseguenza per mantenere i valori entro il range indicato.
Il problema è che il controllo può intervenire solo riducendo la velocità degli assi per rientrare nei valori impostati: questo errore di sfasamento è proporzionale al guadagno, il quale a sua volta è proporzionale alla prima frequenza di risonanza. In definitiva, lavorando con un guadagno doppio è possibile ridurre la velocità della metà.
In presenza di materiali malleabili – come l’alluminio – significa risparmiare sul fronte del tempo ciclo. In presenza invece di leghe resistenti al calore, riducendo troppo la velocità di avanzamento per mantenere le tolleranze volute si rischia di non avere sufficiente interferenza tra utensile e pezzo, innescando un fenomeno di strisciamento e un conseguente aumento del calore. Anche in questo caso, gli utensili lavorano in condizioni non ideali e i costi crescono significativamente.
Il vantaggio di una soluzione come Zenith Vision Profiler è quindi duplice: è possibile lavorare con i parametri più idonei alla produttività e alla precisione, massimizzando l’impiego degli utensili grazie a una vita utile più lunga.
Il problema è tanto più grande se si pensa che con il titanio si parte spesso da forgiati del peso di alcune tonnellate e si asporta il 90% del materiale per giungere al pezzo finito. Maggiore sarà quindi la capacità di asportazione, insieme a un consumo ideale degli utensili, migliore sarà il rendimento dell’impianto.
È così possibile stabilire la vita utensile in base al tempo di contatto o all’assorbimento di potenza al mandrino: in entrambi i casi, sarà l’utilizzatore a decidere quale modalità utilizzare e quali limiti impostare prima di richiamare un nuovo utensile.
In termini numerici, senza queste ottimizzazioni un ciclo di lavoro ipotetico ideale di 500 ore di fresatura rischia di allungarsi fino a 600-650 ore: ciò significa 4-6 giorni aggiuntivi in macchina, con i relativi costi orari e con un maggiore impiego di utensili. Moltiplicando le ore aggiuntive per il costo orario della macchina e degli utensili le cifre in gioco sono notevoli.
Dettagli che contano
Sul fronte delle motorizzazioni, la Zenith Vision Profiler dispone di una doppia vite sull’asse Y per garantire maggiore rigidità e velocità.
In X sono quattro i motori operativi, due nella parte inferiore e due in quella superiore in gantry: pignone e cremagliera con recupero elettronico dei giochi in modalità master & slave consentono al controllo numerico di gestire coppie differenti al fine di ridurre al minimo i possibili giochi.
L’adduzione di refrigerante attraverso l’utensile è garantita da una pompa ad alta pressione che assicura 100 bar e una portata di 130 l/min, valori considerevoli ma fondamentali per lavorare con il titanio.
Lo scopo del refrigerante è infatti asportare il calore dalla zona di lavoro; il liquido viene termostatato entro un range di temperature molto ristretto grazie a un impianto opportunamente dimensionato per evitare che il calore torni in circolo e inneschi una deriva termica. Inoltre, l’alta pressione è fondamentale per tenere pulita la zona di taglio: nel caso l’utensile dovesse “rimacinare” un truciolo già asportato, infatti, la presenza di una piccola percentuale di alluminio nelle leghe di titanio innescherebbe la fusione dell’alluminio stesso, che andrebbe così a incollarsi sul tagliente degenerandone le prestazioni e innescando un processo distruttivo per l’inserto.
Trattandosi di una macchina a mandrino orizzontale, infine, il pallet portapezzo viene posizionato in verticale durante la lavorazione. Posizione ottimale per l’asportazione di truciolo, un po’ meno per lo staffaggio del pezzo: per questo è previsto l’utilizzo di un ribaltatore che gestisce il pallet in orizzontale durante la fase di setup, carico grezzo e scarico pezzo finito, mentre lo ruota in verticale per eseguire l’asportazione in macchina.
La macchina è predisposta per l’utilizzo in modalità stand alone o, insieme ad altre, in configurazione FMS con shuttle pallet.
Personalizzazione della macchina
Sono previste varie versioni della macchina, in base alle necessità degli utilizzatori.
Innanzitutto il campo di lavoro, che può essere pari a 3×6 m o 2×4 m; si tratta del range dimensionale che copre le misure dei pezzi che tipicamente vengono lavorati su macchine di questo tipo.
Il magazzino utensili su catena esterna parte da 40 posti per salire fino a 120, il tutto con attacco a scelta tra Capto, HSK o ISO.
Il controllo numerico, infine, può essere Siemens, Heidenhain o Fanuc a discrezione dell’acquirente. La buona struttura meccanica consente infatti l’impiego di tutti i controlli numerici, anche quelli senza particolari routine di correzione delle traiettorie, proprio perché la macchina è intrinsecamente precisa e quindi non richiede correzioni elettroniche rilevanti. La capacità della Zenith Vision Profiler di gestire spinte elevate riducendo le vibrazioni elimina la necessità di utilizzare componenti attivi: ciò significa semplificare l’intero progetto, togliendo particolari soggetti a usura e manutenzione e riducendo i costi e i tempi di assemblaggio.
Infine, pur trattandosi di una macchina dedicata, la Zenith Vision Profiler può integrare un dispositivo di cambio automatico dell’elettromandrino per passare dall’asportazione del titanio a quella dell’alluminio: due materiali che necessitano di potenze, coppie e regini di rotazione differenti
Condividi l'articolo
Scegli su quale Social Network vuoi condividere